Все, что нужно знать о станках
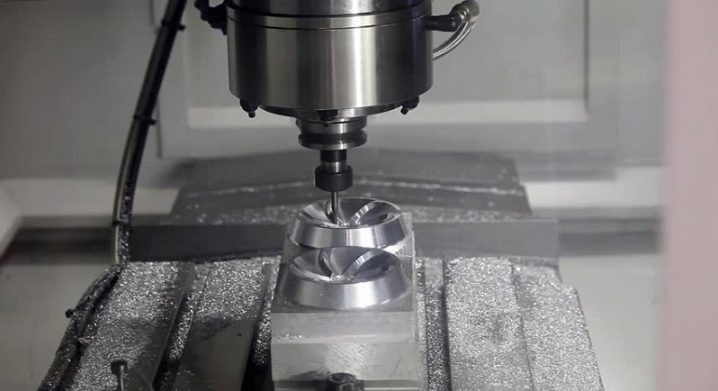
Без станков не может обойтись ни одно производство. В том или ином виде обрабатывающее оборудование задействуется и на крупных заводах, и в небольших частных фирмах любой направленности. При этом существует великое множество классификаций таких агрегатов, каждый из них имеет свой функционал, опциональное наполнение, технико-эксплуатационные характеристики.
Что это такое?
Станки относятся к группе промышленных агрегатов. От всех остальных типов технологического оборудования их отличает присутствие станины, на которую устанавливается основной функциональный орган или система рабочих блоков. В качестве обрабатывающего элемента может выступать алмазная коронка, абразивный круг или сверло — это напрямую зависит от типов выполняемых операций. В большинстве случаев станки используются на крупных промышленных предприятиях.
Они представляют собой массивную конструкцию, которая предусматривает платформу, фиксаторы, мотор и многие другие элементы. В мелкосерийных цехах и бытовых мастерских востребовано более компактное оборудование. В последние годы среди станков появились не только стационарные, но также и мобильные устройства. При этом грань между мини-станком и ручным инструментом порой не определяется даже производителям. Тем не менее именно станина, наличие силовой установки и обрабатывающий орган относят агрегаты к группе станков. А каких именно, рассмотрим далее.
Описание видов
В наши дни уровень автоматизации промышленных предприятий неуклонно повышается, поэтому количество станков на механическом управлении становится всё меньше. Именно поэтому все машины можно условно разделить на ручные, полуавтоматы, а также автоматические модели. Самые современные установки предусматривают числовое программное управление. Такой тип контроля обеспечивает повышенную точность настройки, а сама обработка выполняется с минимальной погрешностью. Основным преимуществом станков с ЧПУ является отсутствие потребности в постоянном наблюдении за ходом производства, так как все основные рабочие параметры задаются оператором до начала обработки.
Технические характеристики станков варьируются в зависимости от типа обрабатываемого материала. Большинство видов агрегатов используются для работы с деревом и металлическими изделиями. При этом для древесины допустимо применение менее мощных агрегатов, но с исключительной точностью настройки. Для обработки металлических заготовок мощность должна быть максимальной. Станки бывают разными — зиговочными, фальцепрокатными, рельсорезными, брусовальными, окорочными, для фальцевой кровли, лущильными, прецизионными, а также копировальными и лазерными.
Наиболее востребованными являются фрезерные, сверлильные и токарные машины.
Металлорежущие
Для работы с металлом используются слесарные металлорежущие, листоправильные станки, рубочные для арматуры и установки для сетки-рабицы. Все типы станочного оборудования для металлообработки разделяют на несколько категорий.
- Токарные — производят обработку постоянно вращающихся внутренних и внешних поверхностей заготовки. При этом в процессе обработки деталь вращается вокруг своей оси.
- Сверлильные — сюда относят также расточные установки, они незаменимы при необходимости формирования глухих и сквозных отверстий. В процессе обработки инструмент вращается одновременно с подачей заготовки, в расточных механизмах подача производится за счёт перемещения рабочего основания.
- Шлифовальные — включают несколько разновидностей станков. Всех их объединяет наличие абразивного шлифовального круга в качестве базового рабочего инструмента.
- Доводочные и полировальные — здесь также используется абразивный круг. Вместе с полировальной пастой он делает поверхность гладкой.
- Зубообрабатывающие — предназначаются для оформления зубьев шестерёнок, сюда же можно отнести и шлифовальные станки.
- Фрезерные — в этой категории в качестве функционального органа используется многолезвийная фреза.
- Строгальные — принцип действия этих агрегатных устройств основан на возвратно-поступательном перемещении заготовки. Разрезные — служат для разделения уголка, швеллера, прутка и других типов металлопроката при помощи разрезания.
- Протяжные — в качестве функционального инструмента здесь установлены многолезвийные протяжки.
- Резьбообрабатывающие — к этой группе относят агрегаты, предназначенные для оформления резьбы. Токарные станки сюда не входят.
- Вспомогательные — в эту категорию включают дополнительные установки, позволяющие выполнять вспомогательные технологические операции.
Деревообрабатывающие
Современные деревообрабатывающие станки делят на несколько групп.
- Строгальные — также известны как рейсмусо-фуговальные или, проще, рейсмус. Это оборудование осуществляет два вида манипуляций. Первая — строгание вагонки и деревянных заготовок до определённых размеров, то есть рейсмусование. Вторая — придание деревянной поверхности гладкости за счёт строгания.
- Циркуляционные пилы — такой тип станков востребован при необходимости проведения распила заготовок. Его отличает максимальная точность по сравнению с аналогами.
- Форматно-раскроечные — позволяют выполнять поперечную и продольную, а также угловую раскройку фанеры, пиломатериалов и древесных заготовок, облицованных шпоном либо пластмассой.
- Распиловочные — сюда относят продольно-распиловочные станки, станки дисковой распиловки и рамные пилорамы. Они используются для деления массивных заготовок на несколько более мелких.
Выбор конкретного типа оборудования зависит от параметров твердости древесины.
- Долбежные — такое деревообрабатывающее оборудование отличается высокой мощностью. Поэтому при формировании перфорации или выпиливании пазов в заготовках зачастую возникают повышенные нагрузки на двигатель станка.
- Токарные — универсальные модели, используются для проведения работ в широком спектре (сверление, нарезка резьбы, выпиливание пазов, обточка).
- Фрезерные — как и в случае с металлом, это оборудование позволяет выполнять обработку внутренних и наружных поверхностей и плоскостей разных форм. Инструмент востребован для выдалбливания зубьев, также используется при создании проточки канавок.
- Сверлильные — как и следует из названия, инструмент востребован при необходимости создавать отверстия в деревянных заготовках.
- Комбинированные — производят комплексную обработку столярных изделий. К примеру, распиловку, фрезеровку и рейсмусование.
- Ленточные пилы — такие станки востребованы при распиловке деревянных заготовок разной твердости и высоты. Они же позволяют осуществлять фигурное выпиливание. Это экономически выгодное оборудование, поскольку его использование снижает количество отходов.
- Кромкооблицовочные — такие агрегаты позволяют выполнить декоративную обработку кромок мебели и других изделий из дерева.
- Шлифовальные — высокоточное оборудование, используемое на финишных этапах создания продукции. Зачищает любые неровности и дефекты поверхности, придавая изделию эстетичный вид.
Камнерезные
Конструкция камнерезных станков включает станину, а также зафиксированный на ней режущий инструмент. Последний приводится в движение бензиновым либо электрическим двигателем, благодаря чему обеспечивается качественный распил бетона, керамогранита, натурального камня и других видов сверхтвердых плит. Электрическое оборудование требует подключения к сети переменного тока, но при этом не дает токсичных выбросов отработанных газов. Бензиновые агрегаты автономны, но используются редко, обязательным условием его эксплуатации является хорошо вентилируемое рабочее помещение.
В зависимости от типа управления машины могут быть ручными и автоматизированными. Автоматизированные делятся на две группы — предназначенные для прямой резки и резки под углом 45 градусов, а также для фигурной резки.
К первой категории относятся:
- камнекольные установки — востребованы при производстве брусчатки и декоративных осколков, которые используют при мощении улиц и садовых дорожек;
- отрезные — отвечают за распил массивных каменных глыб на фрагменты необходимого размера;
- калибровочные — производят выравнивание поверхности из камня и придают ему эстетичный декоративный вид.
Предусмотренная функция обработки под углом 45 градусов существенно облегчает трудовые затраты и намного сокращает время обработки каждой заготовки. Фигурную резку производят на специализированном оборудовании с целью придания изделиям узорной формы.
Принцип работы такого устройства базируется на гидроабразивной технологии.
Другие
Особняком стоят линии по переработке пластика в гранулы и станки для производства пеллет. Они включают в себя оборудование, предназначенное для измельчения, очистки от сторонних включений, подсушивания, сепарации, гранулирования и заключительной упаковки пластмассы.
Одна линия станков включает все вышеперечисленные механизмы. В ряде случаев требуется сепаратор, сортировочные столы, транспортеры и конвейеры.
Классы точности
Каждый вид станкового оборудования подлежит обязательной проверке на соответствие нормативам точности. Итоги проведенных испытаний фиксируются в специальных актах и вкладываются в паспорт агрегата. Все виды оборудования имеют свой ГОСТ, который регламентирует максимальное отклонение по каждой проверке. В зависимости от типа станков количество и частота проверок могут различаться. К примеру, некоторые модели широкоуниверсальных фрезерных станков с ЧПУ могут включать несколько десятков испытаний.
По результатам тестов все станковое оборудование делится на классы с учётом точности работы.
- Н — установки нормальной точности, на них производится обработка деталей из металлопроката и литья.
- П — повышенная точность. Такие агрегаты изготавливаются на базе оборудования с нормальной точностью, но их монтаж производится с максимальной тщательностью. Эти станки обрабатывают те же заготовки, но все работы выполняются точнее.
- В/А — оборудование высокой и особо высокой точности. Здесь предполагается использование особых конструктивных элементов, более тщательная проработка узлов и специфические условия эксплуатации.
- С — особо точные станки, позволяют добиться максимальной точности обработки заготовок. Востребованы при изготовлении измерительного инструмента, зубчатых колес и прочих вариантов обработки.
Отклонения по испытаниям соседствующих классов точности агрегата отличаются между собой в пределах 1,6 раза.
В соответствии с ГОСТ 8-82 для всех видов станков, включая версии с ЧПУ, внедрен единый стандарт тестов на точность. В соответствии с ним принадлежность к категории определяется по трём параметрам:
- геометрическая точность самого оборудования;
- точность обработки тестовых заготовок;
- дополнительные параметры.
На основании этого стандарта категориям агрегатов присваиваются классы точности. При этом оборудование, принадлежащее к одинаковой группе, должно обеспечивать равную точность обработки образцов идентичной величины и формы.
Лучшие производители
Надёжные, функциональные и долговечные станки изготавливаются в разных странах. Наиболее качественное импортное оборудование производится в США, Европе, а также в ряде азиатских государств. В топ крупнейших производителей входят несколько известных брендов.
- TOYODA (Япония). Эта фирма была открыта в 1941 г. в качестве дочернего подразделения Toyota Motor Corporation. Изначально предприятие специализировалась на выпуске цилиндрических шлифмашин, но начиная с 70-х гг. ХХ столетия производитель наладил выпуск обрабатывающих центров высокой точности для массового производства. В наши дни компания признана лидером по изготовлению агрегатов с ЧПУ.
- SMTCL (Китай). Станкостроительный комбинат признан самым крупным на территории Китая, выпуск продукции превышает 100 тысяч единиц станков в год. Производственную деятельность предприятие начало в 1964 г. К 2020 г. в концерн вошло 15 станкостроительных производств, а также научно-исследовательский центр, занимающийся созданием высокотехнологичных агрегатов. Произведённые станки продаются свыше чем в 70 странах мира, в том числе в России, Италии, Германии, Англии, Канаде, США, а также Турции, Южной Корее, Японии и ЮАР.
- HAAS (США). Американское предприятие работает с 1983 г., на сегодняшний день считается самым крупным станкостроительном комбинатом в США. Ассортиментный портфель включает токарные агрегаты, обрабатывающие модули с ЧПУ и крупногабаритные пятиосевые специализированные установки. При этом 75% цехового оснащения составляют станки собственного же изготовления, подобный подход позволяет существенно снизить себестоимость изделий.
- ANCA (Австралия). Производитель изготавливает шлифстанки с ЧПУ с середины 80-х гг. ХХ столетия. Цеха располагаются в Мельбурне, ещё два завода работает на Тайване и в Таиланде. Компания производит инструментальные режущие, а также заточные станки, установки для выпуска метчиков, изготавливает фрезерные и шлифовальные агрегаты.
- HEDELIUS (Германия). Старт работы немецкой компании пришелся на 1967 г. Изначально производитель ограничивал ассортимент деревообрабатывающими станками. Но уже спустя десятилетие была открыта линия по созданию обрабатывающих устройств для нужд металлообрабатывающей промышленности.
- Biglia (Италия). Итальянский изготовитель признан одним из лидеров по изготовлению производительных обрабатывающих токарных агрегатов. Свою производственную деятельность ведёт с 1958 г. Компания предлагает токарно-фрезерные центры, а также вертикальные станки, установки для обработки круглых прутков и обрабатывающие установки.
Качество продукции подтверждено международными сертификатами ISO 9001 и CE Mark.
Комплектующие и приспособления
Все комплектующие, используемые в станках, условно можно поделить на 3 категории.
- Механические — это направляющие, а также подшипники для них. Сюда же входят зубчатые рейки, приводные ремешки для передач, муфты, рольганги, редукторы и другие.
- Электромеханические — включают всевозможные движки, шпиндель и приводы осей. К этой группе относят вспомогательные моторы, к примеру, для подачи смазочно-охлаждающей жидкости. В категорию входят и силовые агрегаты для управления ими (блоки питания, преобразователи частот, электромагнитное реле, концевые датчики).
- Электронные — эту группу расходников составляют платы, коммуникации, драйверы и многое иное.
Нужно иметь в виду, что некоторые расходники образуют друг с другом единую функциональную связку. Примером является: шаговый двигатель, драйвер, а также блок питания для привода. Все комплектующие этой связки должны в точности соответствовать друг другу. То же самое относится к группе: шпиндель, частотный преобразователь, винты и гайки, зубчатая рейка и шестерня.
При необходимости замены одной из запчастей в подобной связке выбор необходимо делать с учетом технико-эксплуатационных параметров всех остальных комплектующих. При выборе одной определённой запчасти такой группы необходимо предоставить продавцу основную документацию на прочие компоненты связки. Как минимум у них должен быть один производитель.
Нюансы ремонта
Ремонт станков — процесс непростой. Выполнить его своими руками могут люди, имеющие специализированные навыки работы с подобным оборудованием. Приведём пример на основе токарного станка. Далеко не секрет, что желание оборудовать мастерскую токарным станком зачастую расходится с возможностями бюджета. Именно поэтому некоторые приобретают модели, бывшие в употреблении, порой в довольно плачевном состоянии.
Продлить эксплуатационный ресурс подобной техники позволяет ремонт. Одним из самых распространенных дефектов таких станков становится выработка режущих поверхностей металлообрабатывающего станка, приводящая к износу. В таком случае ремонт должен обязательно включать процедуру шабрения, в результате которого все поврежденные слои фрикционных поверхностей снимаются.
Чаще всего шабрению в токарных станках подлежат суппорт, каретки и направляющие станины. Выработка направляющих связана с частым попаданием металлической стружки либо грубым нарушением условий эксплуатации. К поломке приводят резкая смена рабочих режимов, недостаточное количество смазки и другие факторы. Шабрение может быть черновым — оно производится с целью устранения выраженных дефектов, в этом случае снимается 0,001-0,03 мм металла.
Сразу после черновой обработки производится чистовое шабрение, оно позволяет нейтрализовать все мелкие неровности, выявленные при помощи краски. Оставшиеся на поверхности после шабрения нанесённой краски пятна становятся ориентиром для мастера— чем меньше будет их число и диаметр, тем ровнее получится поверхность. На финишной стадии работ производят отделочное шабрение, его целью является обеспечение равномерного распределения пятен.
Конечно же, ремонт не ограничивается проведением шабрения. Однако, именно эта мера позволяет обеспечить максимальную точность точения и плавность передвижения рабочих механизмов оборудования.
Однако, нужно понимать, что любой ремонт станков своими руками целесообразен лишь в том случае, если речь идет об облегчённой малофункциональной бытовой технике. При необходимости реставрировать установки среднего или тяжелого класса весом в несколько тонн лучше передать технику в руки специалистов. Они не только вернут ей работоспособность, но и увеличат производительность.