Все о термической обработке стали
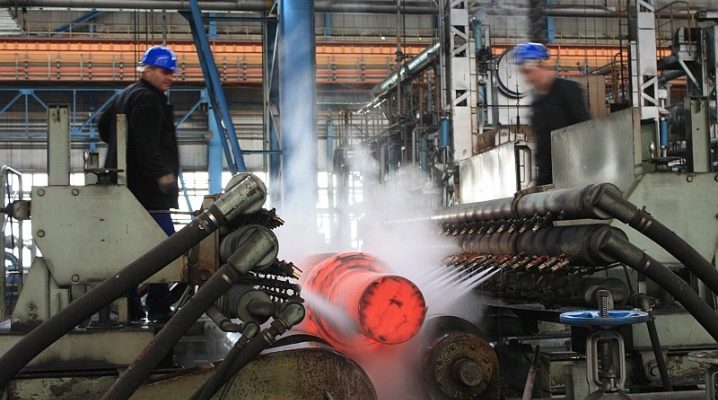
Термическая обработка металлов, наряду с легированием и обогащением углеродом стального сплава, – один из способов поднять механические параметры стали и других сплавов на новый уровень. Этот метод требует чёткого соблюдения всех предписаний.
Что это такое?
Термическая обработка сталей – нагревание, выдерживание при определённых температурах некоторое время и охлаждение стальных заготовок. Термообработка основана на изменении их фазового состава, улучшении кристаллической решётки сплава. При этом структура молекул располагается иным, отличным от первоначального их взаимного расположения образом.
Термообработка сталей применяется как промежуточная и заключительная мера, направленная на улучшение и облегчение обработки заготовок в ходе выделки из них деталей нужного построения. Например, улучшаются показатели разрезания и обточки заготовок, в результате чего изделие обретает заданные свойства.
Время нагрева и выдержки материала имеет критически важное значение. Если металл слишком быстро раскалить, а затем так же быстро охладить, то вместо упрочнения может произойти смягчение. И хотя у мягких металлов лучше пластичность, прочностные и общевесовые по нагрузке показатели пострадают. Улучшение прочностных и упругостных свойств показано на графике изменений образцов стали, взятых для проведения этой процедуры. Каждая сталь (или семейство сплавов) обладает собственными кривыми (корреляция, или взаимозависимость), показывающими, где лучше расположить рабочую точку процесса, чтобы металл или сплав дал максимальную отдачу по всем параметрам. Для улучшения процессов термообработки используется печь с высокотемпературным конвейером, исключающим ручной труд повышенной опасности у рабочих цеха.
Нагревание сплава приводит к обеднению содержания углерода (по массе) на поверхности заготовки. Дело в том, что часть углерода можно выжечь, если прокалить стальную или чугунную заготовку, при этом поверхность её станет несколько более умягчённой, чем глубже лежащие слои, расположенные близко от сердцевины. При нагревании и охлаждении стальных сплавов состав претерпевает фазовые переходы. Они сопровождаются наличием температурных критических отметок. Согласно одной из них перлитная сталь превращается при 727°С в аустенитную. При 768°С происходит переход в состояние феррита. Далее феррит и цементит переходят вновь в состояние аустенита.
Для критических точек характерно поведение стали при нагреве и постепенном остывании. Оксидирование (покрытие окисной плёнкой) важно при этом максимально исключить.
Виды и особенности отпуска
Отпуск по своему виду преподносится как низко-, средне- или высокотемпературный процесс. Его проводят на воздухе, в воде или в масле, а также при медленной скорости охлаждения, вместе с остывающей печью. Формально классификация отпускания как процесса представлена низким, средним и высоким отпуском.
Низкий
Низкий отпуск осуществляется при температуре 150-250°С. Сталь теряет свои внутренние напряжения, мартенситное закаливание переходит в отпущенную мартенситную сталь, возрастает прочность и несколько улучшается вязкость без особого снижения твёрдости. Закалённый сплав с содержанием до 1,3% углерода (по массе) сохраняет твёрдость в рамках 58-63 единиц по Роквеллу. Низкотемпературный отпуск характерен для быстрорежущей стали и сортов сплава для измерительных инструментов.
Детали, подвергнутые поверхностному закаливанию, цементированию, цианированию или азотоцементации, выдерживают примерно 2 часа, а для заготовок больших сечений назначается более длительный сеанс отпускания.
Средний
Среднему отпусканию подвергается сталь при температурах порядка 400°С. Она используется в основном для пружинно-рессорных деталей и комплектующих, изготовления штампованных заготовок. Такое отпускание позволяет достичь повышенной упругости, выносливости и стойкости к ослаблению ответного усилия при сжатии/растяжении. После отпуска сталь превращается в троостомартенситную или трооститную со средним показателем твёрдости в 45 единиц по Роквеллу. Неверно выбранная отпускная температура вызывает необратимое охрупчивание стального сплава.
После отпускания сталь с температурой примерно в 425°С погружается в воду, это ведёт к появлению на поверхности остаточных сжимающих напряжений. Это позволяет пружинам легко держать форму после длительного воздействия на них.
Высокий
Высокотемпературное отпускание осуществляется в среднем при 590°С. Сталь становится сорбитной. При этом виде отпускания сталь обретает хорошую прочность и вязкость. Закаливание стали перед проведением высокотемпературного отпуска позволяет поднять на новый уровень текучесть и прочность. Состав относительно сужается, более интенсивно поглощает удары и гасит вибрацию. Недостаток – такая сталь сложна в обработке.
Процедура улучшения (высокого отпускания) характерна для среднеуглеродистых составов, массовое содержание углерода в которых остаётся на отметке в 3-5 промилле. Область применения таких составов – несущие конструкции особенно ответственной нагруженности. Устойчивость к трещинам (хладноломкость) также у таких сплавов снижены. Остаточные напряжения уходят, но длительность сеанса может достигать 6 часов.
Отжиг
Основная схема отжига – нагрев заготовок до высоких температурных значений с постепенным замедленным охлаждением. Структура становится однородной, лишние механические напряжения уходят.
- Диффузионный отжиг – когда деталь накаляют до 1200°С. На остывание уходят сутки и более. Задача процесса – устранить неоднородности.
- Полный – нагрев до аустенитной температуры в 727°С с замедленным охлаждением. Твёрдость стального сплава понижается, пластичность, напротив, возрастает. Полному отжигу подвергается преимущественно конструкционная сталь. Зернистость кристаллов и твёрдость сплава падают, пластичность – повышается, внутренние напряжения полностью уходят. Неполное отжигание производят при температуре примерно в 755°С. Кристаллическая структура не изменяется так же, как и при полном отжигании, однако остальные изменения такие же, как и после полного отжига. Процедура короче по времени, затраты – меньше, образования окалины почти не происходит.
- Изотермический – заготовку раскаляют так же, как и при неполном отжиге, затем изделия выдерживаются при температуре в 650°С. Выдержка – по ситуации, пока не произойдёт рекристаллизация.
- Рекристаллизационный – устраняет нагартованность сплава после протягивания, волочения или штампования. Нагревание осуществляется до температуры ниже 727°С, заготовка выдерживается до этой температуры, а затем медленно остывает.
- Сфероидизирующий – производят в основном с высокоуглеродистой сталью, в результате перлитные стали меняют структуру кристаллов с пластиночной на зернистую (круглые гранулы). Состав содержит 0,8% углерода по массе.
Отжиг применяется для восстановления структуры стали после неудачного закаливания.
Закалка
Закалённая сталь применяется, к примеру, для изготовления зубьев болторезов, придания свёрлам свойств быстрорежущей стали. Охотничьи ножи и медицинские скальпели также проходят процедуру закалки. В процессе закаливания стальной сплав накаляется выше 727°С, выдерживается при этой температуре до обретения изделием нужных свойств и быстро охлаждается. Именно быстрое, а не медленное, охлаждение закрепляет полученный результат. Чем ниже углеродистость стали, тем больше греют заготовку. Для инструментальных сталей закалка осуществляется приближённо до 750°С.
Скорость прокаливания определяется массой изделия, сложностью исполнения (рельефность). Особое внимание уделяют вязкости и текучести определённого сорта стали.
Другие способы термообработки
Нормализация стали – нагревание до температуры в 750°С, выдержка и последующее охлаждение стали на открытом воздухе в условиях цеха. Сущность её в том, что охлаждение не затягивают по времени, как при отжиге или отпуске, и не ускоряют, как при закалке, а ожидают, пока сталь сама остынет под влиянием обычных условий. Кроме нормализации и улучшения, применяют следующие типовые режимы термообработки: криогенную, химико-термическую и термомеханическую.
Химико-термическая
Суть химико-термической обработки – приповерхностное обогащение металлов примесями, улучшающими твёрдость и стойкость к изнашиванию изделий. Так, цементация проводится при 925°С дополнительным углеродом. Нитроцементация – азотноуглеродной смесью из газа при 875°С. Цианирование – обогащение сталей цианидами (солями синильной кислоты). Азотирование – нагревание стальной заготовки в азоте до 600°С.
Борирование, хромирование, титанирование, алюминирование производятся при нагретом газе, а обогащение кремнием – из порошка, расплава, суспензии или пастообразного реагента.
Термомеханическая
Обработка при повышенных температуре и давлении даёт гартованную сталь. Обязательными стадиями являются горячий прокат, а также волочение или технология штампования с ускоренной закалкой. При быстром охлаждении гартованной стали твёрдость повышается при закалке. Затем производится низкотемпературное отпускание. Термомеханическая закалка повышает твёрдость в среднем на 35%, пластичность сплава при этом возрастает.
Криогенная
Криогенная обработка – погружение заготовки в жидкий азот, при этом процесс сходен с закалкой на мартенситную фазу. При криогенировании сталь по окончании выдержки в жидком азоте естественно нагревается до комнатной температуры, затем подвергается низкотемпературному отпуску. Результат – замедление процессов старения до очень низкой скорости состаривания стали, и за свой срок службы габариты заготовки практически не меняются: сталь не «течёт» спустя десятилетия, как это постепенно происходит при штатных нагрузках на деталь, не трескается и не гнётся при воздействии гораздо меньшем, чем максимальные рабочие усилия, которые она бы испытывала, например, в составе работающего станка или автомобиля.
Нюансы обработки разных марок
Легированные стали типа 20Х, 15ХГН2ТА, 4Х5МФС, 20Х2Н4А, 50ХГФА, 6ХВ2С, 18ХГ, У9, 45Г2, 20ХГР, 38ХН3МА, 7Х3, 20ХН3А, не являющиеся нержавеющими, обрабатывают на основе общих правил для перлитных, мартенситных и аустенитных сталей. Чтобы получить перлит, аустенит, феррит или мартенсит, существуют свои критические точки на графике, некоторые из которых оговорены выше. Термообрабатывают такие стали путём затяжного прогрева до нужных температур, выдержки положенное время – и с таким же медленным остыванием. Исключение – закалка: остужение заготовок производят быстро. Медленные нагрев и охлаждение обусловлены простыми законами физики: чем ниже теплопроводность, тем больше вероятность повредить сталь при такой спешке. Нагревание производят постепенное – по всей площади детали.
Нержавейки – 07Х16Н6, 20Х13, 20Х14, 20Х16, 20Х18Н9Т и похожие составы (маркер «Х-число» в маркировке обозначает целые проценты хрома по массе), под которые подпадают и похожие сорта стали, содержащие 13% и более хромовой присадки по весу заготовки, после отжига оставляются в медленно остывающей печи. Иногда для отложенного раскаливания в составе печи используется специальное электронагревательное оборудование, включающее подогрев по специальному алгоритму – в целях соблюдения технологии производства на 100%.
После отжигания производится отпуск – это позволяет нержавеющим заготовкам набрать прочность, ударную вязкость (нержавейка относительно сложна в резке и сверлении). Быстро охлаждать нержавейку нельзя – это приведёт к возникновению дополнительных дефектов.
Аустенитные стали подвергаются временному разогреву в печи до 1150°С. Чтобы получить устойчивую внутреннюю структуру, раскалённые и выдержанные положенное время заготовки погружаются в масло по специальному алгоритму или до полного охлаждения. Улучшенная таким образом сталь обретает все присущие ей положительные свойства. Быстрорежущая сталь закаливается в печи с максимально точным термодатчиком. Она не подлежит быстрому разогреванию или охлаждению. Правильно достигнутый результат – потеря первоначальной твёрдости лишь при температуре порядка 650-700°С.
Простые углеродистые стали марки 3, 4, 5, 6, 8, 10, 15, 20, 25, 30, 35, 40, 45, 50, 55, 60, 75 (подписаны как «Ст» с соответствующим номером), содержащие в себе соответствующее количество сотых долей процента углерода по весу заготовки, нормализуются и отпускаются, отжигаются по общей методике «мартенсит – перлит – аустенит – феррит» в зависимости от того, какой род стального состава вы хотите получить. Цель – сделать связи в кристаллической решётке между молекулами устойчивыми, добиться уменьшения хрупкости.