Особенности инструментальных сталей и их марки
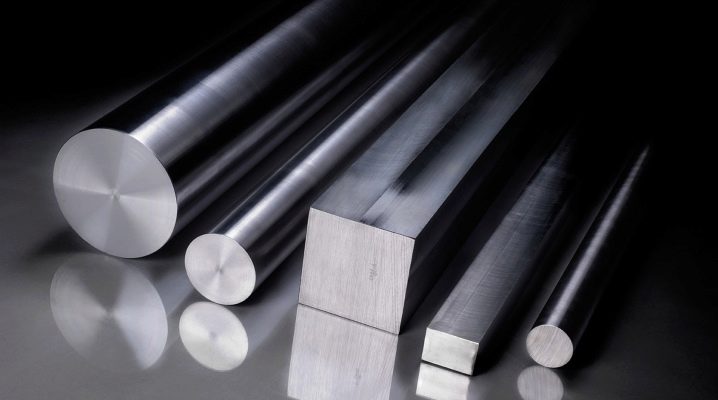
Инструментальная сталь представляет собой углеродистый или легированный сплав, предназначенный для изготовления штампов холодного или горячего деформирования, режущих инструментов, а также элементов машин, работающих в условиях повышенного износа. Обо всех особенностях такого металла мы расскажем в нашей статье.
Общее описание
К группе инструментальных относится сталь, в которой массовая доля углерода превышает 0,7%. Базу такого сплава составляет мартенсит, в исключительных ситуациях — ледебурит. С учетом того, в какой сфере будет использоваться этот металл, к нему предъявляются вариативные требования. Однако выделяют ряд общих критериев ко всем типам инструментальных сплавов вне зависимости от их марок:
- твердость;
- повышенная прочность;
- стойкость к износу;
- сниженная чувствительность к нагреву;
- малая степень прилипания и приваривания к обрабатываемым заготовкам;
- легкость резки материала;
- стойкость к растрескиванию;
- высокая пластичность в нагретом состоянии;
- подверженность шлифовке;
- восприимчивость к прокалке;
- противостояние обезуглероживанию.
К тому же инструментальные сплавы должны иметь отличную вязкость.
Особенно это актуально при производстве элементов, которые в процессе использования часто подвергаются механическим воздействиям.
Конечно, это далеко не весь перечень требований. К примеру, марки, которые востребованы при создании деталей, работающих в среде холодной деформации, должны обязательно иметь идеально ровную конфигурацию, проявлять повышенный уровень упругости и хорошую текучесть. Важно, чтобы они удерживали форму и габариты при внешних воздействиях. Те металлы, которые обрабатывают техникой горячей деформации, должны демонстрировать повышенную теплопроводность, стойкость к тепловым колебаниям и не допускать даже малейших отпусков.
В сравнении с классическими конструкционными сплавами инструментальный материал обладает рядом весомых преимуществ. К ним относят:
- твёрдость на уровне 60–70 единиц по Роквеллу;
- повышенную прочность — уровень сопротивления разрыву держится на отметке от 900 МПА и более;
- стойкость к абразивному истиранию;
- способность сплава к прокаливаемости.
Для инструментальных сплавов характерна так называемая красностойкость. Это свойство определяет способность металла в полном объёме сохранять свои прочностные качества при повышении температурного воздействия.
Впрочем, не обошлось и без недостатков. Данный материал отличается сниженной стойкостью к износу.
Поэтому для деталей машин и оборудования, которые в ходе эксплуатации подвержены интенсивным нагрузкам, инструментальные составы не применяют.
Виды
В зависимости от качественной структуры и технико-механических характеристик материала выделяют несколько разновидностей инструментальной стали. Познакомимся поближе с их классификацией.
Углеродистые стандартного типа
Углеродистый сплав характеризуется повышенной твердостью при комнатной температуре. При этом стойкость к тепловому воздействию невелика, поэтому даже при сравнительно невысоких терморежимах (в пределе от 200 до 250 градусов) твердость многократно уменьшается.
Легированные
Основное отличие таких сплавов от углеродистых заключается в повышенной концентрации легирующих компонентов. Они могут включать:
- хром — придает материалу стойкость к коррозии, повышает прочность и плотность с одновременным снижением пластичности;
- никель — улучшает параметры прокаливаемости, прочности и пластичности материала, способствует росту ударной вязкости;
- вольфрам — обеспечивает теплостойкость расплава и придает ему высокую твёрдость;
- ванадий — формирует мелкозернистую структуру, улучшает прочностные и твёрдосплавные характеристики;
- кобальт — увеличивает жаростойкость материала и его вязкость;
- молибден — способствует росту прочности, упругости и стойкости стали к тепловым воздействиям.
В зависимости от марки в состав может вводиться один или несколько легирующих компонентов в различной концентрации. В результате этого материал получает все необходимые характеристики.
Так, для создания режущих инструментов по традиции используют низколегированные составы: 9ХФ, 11ХФ, 13Х, ХВ4, ХВСГ, а также ХВГ и некоторые другие. Эти сплавы проявляют исключительно высокие физико-технологические характеристики, их отличают лучшая прокаливаемость и закаливаемость, меньшая подверженность короблению. При этом их теплостойкость практически идентична соответствующему показателю для углеродистых сталей и держится на отметке 350–400 градусов.
Быстрорежущие
Основным легирующим компонентом для такой стали считается вольфрам. Кроме него, в структуру быстрорежущих сплавов могут вводиться ванадий и кобальт. На долю хрома в таких составах приходится не больше 3–4% — это настолько мало, что данный элемент даже не указывается в маркировке.
Валковые
Валковые стали относят к категории сложнолегированных сплавов. Они востребованы в производстве опорных и рабочих валков, материал нашел повсеместное применение при выпуске шестерён, обрезных матриц, ножей для резки металлов, пил и многих других изделий, связанных с интенсивной нагрузкой. Инструменты из такой стали отличаются стойкостью к повышенным температурам, механическим повреждениям и истиранию.
Для валковой стали характерна хорошая прокаливаемость, она не подвержена деформации, обладает достаточным уровнем шлифуемости.
Штамповые
Подобные стали, в зависимости от особенностей использования, бывают штампованными методом холодной или горячей деформации. В холодном состоянии сплав проявляет повышенную твердость, благодаря чему обеспечивает стойкость металлов к истиранию. Для горячих штампов характерна сниженная чувствительность. Штамповой стали свойственны повышенная прокаливаемость и слабая деформируемость в процессе закалки.
Маркировка
В состав инструментальной стали обычно вводятся легирующие компоненты, призванные улучшить физико-химические и механические характеристики материала. В соответствии с ГОСТ в маркировке эти добавки указываются буквенными символами, благодаря чему можно установить, какие элементы составляют основу инструментального материала. При этом каждая буква дополнена цифровым обозначением — оно указывает на долю того или иного элемента.
Если цифра отсутствует — следовательно, концентрация примесей не превышает 1%. На первом месте в маркировке любых сталей указано количество углерода. К примеру, расшифровка марки с обозначением 6ХС говорит о том, что сплав содержит 0,6% углерода и менее 1% кремния и хрома.
Быстрорежущие сплавы маркируют с указанием буквы «Р» впереди, а также числа, которое обозначает долю вольфрама в структуре. После них идут буквенные элементы, указывающие на легирующие компоненты с указанием их концентраций.
Если в маркировке содержится буква «Ш», это означает, что изделие представляет собой электрошлаковый переплав. Долю хрома и молибдена в маркировке быстрорежущих составах не указывают из-за ее малой величины.
Марки и категории
Все группы инструментальных металлов условно разделяются на следующие категории.
Теплостойкие и вязкие — это хромистые сплавы, содержащие вольфрам и молибден. Объем углерода в подобных металлах держится на средних и пониженных отметках.
Высокотвёрдые и мягкие, а также теплостойкие материалы — в этих сталях присутствует минимум легирующих компонентов, количество углерода на среднем уровне. Такой материал отличается низкой прокаливаемостью.
Высокотвердые и температуростойкие — обычно это быстрорежущие сплавы с повышенной долей легирующих добавок. Сюда же относятся материалы с ледебуритной микроструктурой, на долю углерода в них приходится свыше 3%.
Высокотвердые, стойкие к износу, с усредненным параметром теплостойкости — особенностью таких сплавов является включение 15% хрома и 23% углерода.
Сплавы и стали обыкновенного качества — данные виды отличаются между собой по наличию в них серы и фосфора. Соответственно, чем выше категория — тем ниже доля вредных добавок.
Высокотвердые и нетеплостойкие — такие инструментальные составы вообще не содержат никаких легирующих компонентов либо их массовая доля минимальна. Твёрдость нелегированных и низколегированных металлов обусловлена высокой концентрацией углерода.
Выделяют множество марок инструментальных сталей. Наибольшее распространение в промышленности получили У7А, У8, а также У8А и У9 — их отличают стойкость к износу, повышенная твёрдость и плотность. При механических ударах они не разрушаются и не деформируются. Марки У10 и больше также проявляют повышенную неплохую пластичность, но при интенсивных термических воздействиях становятся более пластичными, что существенно ограничивает сферу их использования.
Применение
Высококачественная сталь инструментального типа получила повсеместное распространение в промышленности. Главными областями её применения является создание:
- режущих инструментов;
- приборов для измерений;
- пресс-форм, эксплуатирующихся под высоким давлением;
- рабочих элементов штампов, работающих по принципу холодного либо горячего деформирования;
- металлоизделий высокой точности.
Сталь У7 обладает достойной коррозионной стойкостью и пониженной электропроводностью. Этот металл оптимален для изготовления топоров, стамесок и прочих деревообрабатывающих инструментов. Может использоваться для создания молотков, пассатижей, пил, а также крючков, иголок и зубил.
У10 и У11 — эти сплавы справляются с деформационным воздействием, им не страшен локальный нагрев. Кроме того, они устойчивы к ржавлению. Введение легирующих добавок существенно улучшает физические характеристики марок и придает им эластичность. Такой материал востребован для изготовления напильников, ленточных пил, сверл и роликов.
У8 и У9 — такие марки также обладают хорошей прочностью, но нагрев выдерживают намного хуже. Они нашли своё применение при создании торгового оборудования, пил, роликов, топоров и стамесок. Из них делают запчасти для часов, гвозди, заклёпки, шурупы и болты.
У12 — сталь высокой прочности без каких-либо легирующих компонентов. Актуальна для создания топоров, ручных пил, напильников, резцов или других запчастей высокой прочности, которые не нагреваются до средних и высоких температур.
У13 — металл из категории грубых сплавов, пластичным он становится только при термическом воздействии. Назначением таких материалов является выпуск обрабатывающих инструментов, надфилей, медицинского оборудования и приспособлений для выполнения гравировки.
Закалка и отжиг
Большинство разновидностей инструментальных металлов с целью улучшения их физико-технических характеристик подвергаются закалке и отжигу. Для проведения обработки готовые стальные изделия прогреваются в растворах соли, в результате тепло максимально ровно перераспределяется по металлической поверхности. Для быстрорежущих составов нагрев производится поступательно, со сменой 3 ванн:
- температура начального воздействия соответствует 400–500 гр., в этом резервуаре сплав выдерживается около 40–60 минут;
- после первого прогрева изделие помещают в следующую стальную ванну, в ней температура уже на 250–350 гр выше;
- на заключительном этапе деталь вновь перекладывают — в последней емкости содержится соль, нагретая уже до 1200–1300 гр, здесь производится финишная закалка сплава.
Такая ступенчатая процедура обеспечивает равномерное распределение аустенитов по всей структуре материала. Это самым благоприятным образом сказывается на технических и физических характеристиках металла. Для того чтобы окончательно расплавить аустенитную часть, следует провести отпуск в ванной при температуре 500–550 гр, при этом желательно повторить отпуск трижды. В результате доля аустенитов снижается ниже уровня критической отметки.
Для проведения дополнительной обработки используют метод воздействия низкими температурами.
Для этого первично закаленный материал размещают в резервуаре с жидкими солями при температурном режиме от -100 до – 50 гр. Такую закалку производят в одну стадию, повторная обработка не нужна.