Сталь 40ХН2МА
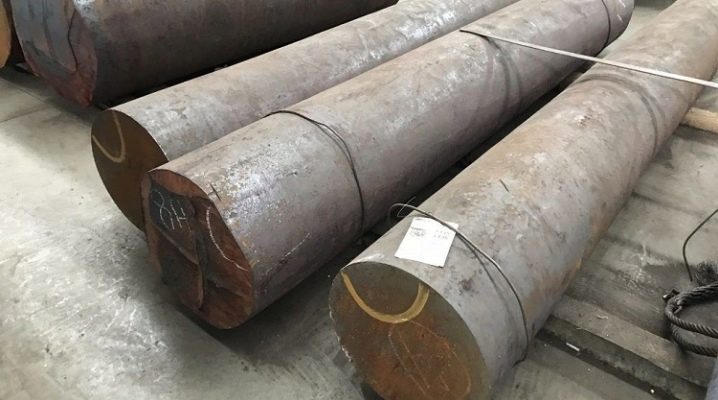
Сталь 40ХН2МА не относится к нержавеющим. Из маркировки состава очевидно, что за ней обязательно требуется уход, особенно во влажной среде. Но как конструкционный и инструментальный материал она вполне сгодится.
Состав и расшифровка
На основании ГОСТ 4543-2016 стальные сплавы, включая и состав 40ХН2МА, распознаются по буквенно-цифровым обозначениям. Число 40 – отсылка к 4 промилле углерода в составе данного сплава: закономерность такова, что опережающее число перед буквенными обозначениями указывает именно сотые доли процента углерода. Данный сплав относится к среднеуглеродистым – низкоуглеродистыми считаются сплавы до 30-х, содержащих менее 0,3% углерода.
Хрома в стали содержится менее 2%, так как после «Х» число 2 (или другое) отсутствует. Для примера, 20Х18Н9Т указывает на легирование 18% хрома; массовое число примесей после соответствующего буквенного маркера указывает на целое количество процентов по общему весу сплава (единицы изделия).
«Н» – отсылка к никелю, 2 – сведения о двух процентах данного металла в составе сплава. «М» – отсылка к молибдену, содержание его не превышает 1%. Маркер «А» – не алюминий (или иной металл), как кажется на первый взгляд, а отметка о высококачественности сплава. Высокое качество сплава предполагает почти полное удаление из его химического состава серы и фосфора – вплоть до процентного количества, стремящегося к следовому. Полностью удалить всю серу и фосфор из сплава крайне сложно. Дело в том, что сера портит сталь, делая её ломкой, на производстве её стремятся оставлять в сплавах как можно меньше.
По сравнению со своим ближайшим отечественным аналогом – 40ХНМА – сталь 40ХН2МА отличается не только по химическому составу, но и по свойствам. Содержание углерода прямо влияет на твёрдость стали: чем его больше, тем прочнее сплав. Однако прочность и надёжность конкретного состава определяется ударной вязкостью и упругостью. Недостаточная упругость стали 40ХН2МА привела бы к меньшей вибрационно-ударной устойчивости. Допуски содержания углерода по массе – 3,7-4,4 промилле.
Легирование этого состава осуществляется в основном при помощи молибдена и хрома. Хром вводится в количестве порядка 1% по массе, но его не хватило бы, чтобы полностью защитить спав от коррозии. В составе стали 40ХН2МА молибдена содержится не более четверти процента, кремний включён в этот сплав в количестве 0,27%, марганец – в массовой доле 0,65%.
Остальные присадки, включая фосфор и серу, представлены в составе 40ХН2МА в сравнительно небольшом количестве – от сотых долей процента и менее.
Характеристики
Согласно нормативам ГОСТ стальной сплав 40ХН2МА относится к хроммолибденовым составам с добавлением никеля. Применяется такая сталь в качестве конструкционной легированной основы. Производится она с применением электрических печей открытого типа. Для выработки используется способ электрошлакового плавления. Сталь 40ХН2МА почти нечувствительна к отпускной хрупкости.
Деформационная способность в разогретом состоянии у 40ХН2МА выражена хорошо. Это означает, что детали можно ковать при температуре 1180 градусов. Плотность стали 40ХН2МА – 7,86 г/см3. При температуре в минус 196 градусов сталь 40ХН2МА не теряет своих параметров, отчего возможно её использование в криогенной промышленности.
Сортамент и аналоги
Стальной сплав 40ХН2МА представлен сортовым прокатным продуктом, включая и фасонные изделия. Калиброванные и шлифовальные пруты, серебряночная продукция, кованые заготовки, полосовая сталь и валковая (стержень, или круг) изготавливаются не только из состава 40ХН2МА, но и из заменителей, к примеру, 40ХГТ, 40ХГР, 30Х3МФ, 45ХН2МФА.
В России именно эти сплавы, наряду с общеевропейским 40NiCrMo4KD, немецким E36CrNiMo4, американским G-3400/4340, британским 36CrNiMo4 (или его заменителем 817M307), японским SNCM439 (либо его заменителем SNCM8) и французским 36CrNiMo4, пользуются особым спросом при производстве всех вышеперечисленных типов деталей.
Применение
Применение данный сплав нашёл при получении из него ряда видов и разновидностей комплектующих: коленвалы, клапаны, шатуны и их крышки, болты с повышенными требованиями к прочности, шестерёнки, кулачковые детали, муфты, диски, валы для холодного проката металлов и сплавов. Все эти детали применяются в станкостроительной отрасли. Для химиков и нефтяников, работников газопереработки ценными комплектующими также являются замки и переходные детали для буровых вышек, оси блоков и кронштейнов, стволы и траверсы плоских крюков, переходных комплектующих карабинов, шайбовые прокладки в шарошечных долотах, шатунные болты, цельнопрокатные кольца и ряд иных составляющих.
Нагрузочная оценка получаемых из состава 40ХН2МА комплектующих – и собираемых из них конструкций – относительно высокая.
Обработка
Обрабатывающие методы для сплава 40ХН2МА характеризуются в основном технологическими параметрами, тщательно отслеживаемыми по целому ряду ГОСТов. Для данной стали характерно образование флокенов (неоднородностей) при выплавке и нагревании в процессе сварки деталей, сработанных из марки 40ХН2МА. Если технология выплавки оказалась нарушена, то зачастую возникают дефектные точки, распределённые по объёму будущей заготовки. После ковки одним из заключительных этапов является отжиг, в ходе которого изменяется кристаллическая решётка затвердевшего до этого в процессе остывания сплава. После двух сеансов охлаждения заготовки должны подвергнуться отпуску. Отпускное охрупчивание при соблюдении технологии почти полностью исключено. В результате становится возможным получить детали, которые не теряют своих основных параметров даже при нагреве до 500 градусов по Цельсию. Термообработка в режиме закалки-отпуска заключается в следующем.
Поскольку данный сплав относят к сталям перлитного рода, критические точки фазовых переходов отмечены на уровне 730 и 820 градусов. Доэвтектоидный состав, по технологии выделки, пропускают через стадию полной закалки, при этом температурный перепад составит всего 40 градусов. В результате формируется аустенитный состав, обладающий мелкозернистой консистенцией. После охлаждения аустенит трансформируется в мартенсит с аналогичным диаметром зерна. Аустенитные частицы формируются при переходе из фаз феррита и цементита – они разделяются от того и другого отчётливой пограничной линией.
Кроме проникновения цементита в аустенит, альфа-фаза сплава переходит в гамма-фазу. Так как растворение цементита происходит более медленно, чем формирование частиц аустенита, получаемому составу в итоге потребуется определённое термическое выдерживание на отметке, соответствующей полной закалке.
Охлаждая сплав 40ХН2МА в воде, при превышении скорости охлаждения темпа перекристаллизации, образуется мартенситный состав с мелкозернистой консистенцией. В результате образуется перенасыщенный твёрдый раствор углерода в альфа-фазе железа. Сам по себе мартенситный состав – достаточно затвердевший материал. В приповерхностных слоях деталей, подвергшихся закалке, формируются немалые механические перенапряжения. Чтобы их снять, детали подвергают отпуску при 550 градусах. Повышая температуру при дальнейшем разогреве, добиваются проникновения углерода в более заглубленные слои, в результате мартенсит постепенно становится перлитной сталью. Однако миграция атомов углерода происходит из исходных их позиций на сравнительно небольшие дистанции. От этого ферритный и цементитный составы перемешиваются.
Отпуск 20ХН2МА проходит в три этапа. Сначала из мартенситного сплава выделится часть углерода в форме метастабилизированного эпсилон-карбида. Эта стадия протекает с небольшой скоростью, без нагревания. Затем мартенсит и аустенит полностью исчезают, одновременно происходит карбидирование состава. Мартенсит распадается по всему объёмному пространству обрабатываемой заготовки, при этом эпсилон-карбид становится цементитной составляющей. Наконец, остатки мартенсита полностью трансформируются в ферритный состав. При дальнейшем раскаливании феррит и карбид претерпевают изменение габаритов элементарных ячеек. Проникновение углерода осуществляется быстрее, чем при среднем отпускании – атомы углерода преодолевают более длинные дистанции. При этом растёт размер каждой частицы ферритного и цементитного сплавов – образуется сорбитный состав.
Интервал, в течение которого производят отпуск, рассчитываются таким образом, чтобы стальной сплав в итоге стал высокостабильным. Заготовки с небольшим поперечным разрезом подвергают одно-двухчасовому высокотемпературному отпусканию. После термообработки свариваемость состава 40ХН2МА ограничена – детали зачищаются и в обязательном порядке подвергаются отжиганию. При необходимости производят нормализацию при температуре, примерно на 100 градусов выше закалочной.