Обзор марок подшипниковых сталей и их применение
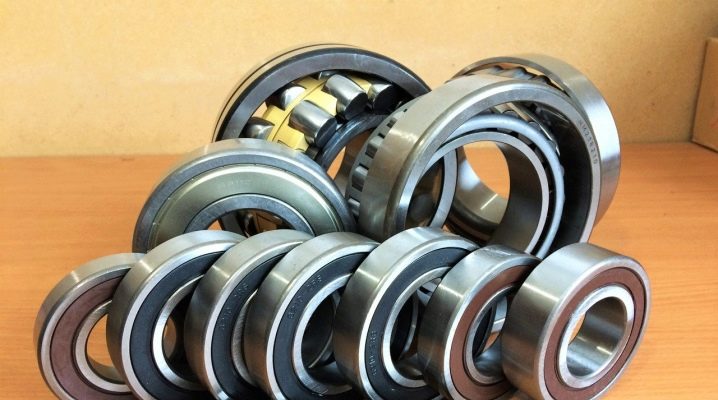
Ознакомиться с обзором марок подшипниковых сталей и их применением будет очень полезно для практиков. Стоит изучить маркировку шарикоподшипниковых сталей и узнать, из какой конкретно стали обычно делают обойму подшипников. Необходимо также изучить твердость сталей и их состав, особенности применения и конкретные свойства.
Общее описание
Само по себе название «подшипниковая сталь» говорит о том, что соответствующий сплав применяется преимущественно в составе подшипников (для их основных частей). При эксплуатации элементы подшипников подвергаются серьезным знакопеременным напряжениям. Потому приходится создавать конструкцию с расчетом на многократные нагрузки даже в течение короткого цикла эксплуатации.
Вывод прост: настоящая подшипниковая сталь должна быть минимально восприимчива к образованию усталостных трещин и к крошению поверхности.
Интенсивность истирания во многом определяется точностью изготовления и качеством сборки подшипников. Обязательно нужно учитывать условия, в которых он подвергается нагрузке, использование смазки. В присутствии абразивных частиц и активных веществ изменение будет идти быстрее. Приходится учитывать и вероятность ударных нагрузок, и иные факторы. Все вместе это резко поднимает планку требований к конструкционным материалам.
Качественная подшипниковая сталь обязательно должна быть максимально однородна по своей структуре. Не допускается значительного вхождения неметаллических частиц и иных посторонних фрагментов. Еще с начала ХХ века активно применяют в подшипниках высокоуглеродистый хромистый сплав. В некоторых случаях куда лучшим выбором оказывается сталь с повышенным содержанием марганца. Состав и практические свойства позволяют сближать такой металл с инструментальными продуктами, но используют его как конструкционный сплав специального назначения.
Свойства
В сталь для подшипников обязательно вводят значительное количество углерода. Этот компонент гарантирует превосходную прочность и предотвращает истирание. Именно по насыщенности мартенсита углеродом можно судить о твердости готовой поверхности. В норме этот показатель идентичен для всех подшипниковых сплавов – как обычных, так и применяемых в особых условиях. Твердость расположенных глубоко слоев определяется уровнем прокаливаемости, а на него, в свою очередь, влияет прежде всего концентрация хрома.
Чем больше этого легирующего элемента добавляют, тем медленнее аустенит будет преобразовываться в перлит. Особенно много его должно быть при изготовлении крупных частей. Карбиды хрома тверды и обеспечивают отличную износостойкость. Они же гарантируют, что мартенсит сможет перенести отпуск очень хорошо и уменьшит восприимчивость металла к перегреву.
Последний момент позволяет проводить термическую обработку практически безбоязненно.
Однако и это свойство, и мелкозернистость не позволяют игнорировать тот факт, что при избытке хрома однородность стали нарушается. Практически всегда поэтому его вводят не более 1,65%. Исключения связаны с совершенно особыми случаями, когда негативным эффектом вполне можно пренебречь. Роль марганца — наращивание твердости и стойкости к истиранию. Правда, этот компонент активизирует рост прогреваемых зерен, что повышает опасность перегрева.
Кремний плох тем, что из-за него неоправданно снижается вязкость. Все же надо понимать, что кремний и марганец — раскислители. Увеличивая их содержание до определенного уровня, добиваются максимального раскисления стали. Однозначно вредны медь, фосфор и никель — от них стараются избавляться всеми средствами. Под влиянием фосфора повышается опасность возникновения крупных зерен, хрупкость металла растет, а сопротивляемость изгибающей нагрузке падает.
А вот роль серы не может быть оценена однозначно, как в случае с иными сталями. При ее отсутствии или очень низком содержании обработка поверхности усложняется. В некоторых случаях вовсе не удается получить высококачественные изделия. Мнения части специалистов о сокращении срока эксплуатации подшипников из сернистой стали и их высоком усталостном разрушении все чаще критикуются. И все же концентрацию серы стремятся ограничить.
Медь, несмотря на повышение твердости сплава и улучшение его прокаливаемости, признана нежелательным компонентом. Не меняет дела и рост предела прочности. Это связано с высоким риском возникновения трещин и надрывов на поверхности при горячей механообработке. Никеля также не должно быть много, потому что он не позволяет добиться твердости металла. Интенсивность крошения зависит от присутствия свинца, олова и мышьяка.
Негативный эффект еще бывает связан с:
-
водородом;
-
кислородом;
-
азотом.
Планка требований к подшипниковой стали высока и по другим критериям. Очень важна строго выдержанная макроструктура. Недопустимы любые включения шлаков и газов. Под запрет попадают все карбидные ликвации, а также полосчатость. При значительном количестве углерода велика опасность возникновения усадочных дефектов, таких как раковины и пористость.
Особенно критичны осевая и суммарная виды пористости. Борьба с этими проблемами ведется за счет отливки некрупных (не более 3000 кг слитков). Их конусность увеличивают как минимум на 5%. Иногда прибегают к утеплению верхушек слитков. Из-за обширного кристаллизационного интервала ликвация примесей развивается очень интенсивно — особенно это характерно для хрома и углерода.
Такие элементы превращаются в карбиды. В ходе прокатки проблемные участки тянутся в том же направлении. Как результат — появляются неоднородные полосы. Разница между ними касается и подверженности травлению.
Избежать подобной ситуации помогает долгая выдержка заготовок при сильном нагреве, она же гомогенизация.
Значительная карбидная ликвация считается абсолютно недопустимым нарушением из-за твердости и хрупкости образующих ее веществ. В итоге сложный участок склонен крошиться. Предотвращение карбидной ликвации достигается при долгой выдержке металла на 1150-1160 градусах. Такой режим гарантирует исчезновение эвтектических карбидов. Без этой процедуры нельзя нагревать металл перед дальнейшей прокаткой.
Шарикоподшипниковые стали делят на 2 основательные группы. Одна из них выпускается для задействования при сильном разогреве и в разъедающей среде. Такие сплавы дополнительно подразделяют на теплостойкую и нержавеющую (вернее, коррозионностойкую) подгруппы. Иной разряд специализирован для применения в типовых условиях. Обычно подразумевается легирование кремнием и молибденом.
Выплавка
В РФ и других странах постсоветского пространства подшипниковые стали плавят в электродуговых печах. На долю кислых мартеновских печей приходится лишь 10% вырабатываемого сплава. Во втором случае речь может идти как об активной плавке, так и о восстановлении кремния. Обе эти металлургические технологии оказываются весьма хороши. Активный метод означает введение известняка, руды и других необходимых веществ напрямую во время работы.
В описываемой практике потенциал кремния при окислении весьма высок. Восстановительная способность его уменьшается. Понижается мобильность жидкого шлака. Восстановительная методика позволяет исключить добавление посторонних веществ в процессе плавки.
Кремнезем имеет важную роль — благодаря ему шлаковый расплав при повышении температуры насыщается очень эффективно.
Электродуговые печи могут вести обработку руды синтетическим шлаком, в котором содержится много глинозема. Сам шлак перед подачей в ковш обрабатывают по особой технологии в другом аппарате. Металл может быть обработан также и за счет шлака, появившегося в самой печи. Оба эти варианта допускают как переплав, так и введение свежей шихты.
Раскисление производится за счет присадки кускового алюминия. Дорабатывать подшипниковые стали после плавки можно за счет:
-
электрошлаковой концепции;
-
вакуумной методики;
-
плазменного рафинирующего переплава.
Из-за суровых ограничений по концентрации вредных примесей наиболее практично производство со свежей шихтой. Отходы применяют при плавке сталей с большим количеством легирующих компонентов. При большом объеме отходов выбирают переплавную методику. Емкость используемых печей преимущественно колеблется от 10 до 200 тонн. Сами печи требуется основательно футеровать. После плавки стали с вредными для подшипников компонентами понадобится несколько промывных плавок.
Качественная шихта должна быть сделана из отходов углеродистой стали. В ней не допускается наличие чугуна. Добавить углерод можно в виде кокса либо боя электродов. Его концентрация в шихте может достигать 1,2-1,3%. Окислительный шлак позволяет еще в момент плавления быстро окислять фосфор.
Примеси окисляют как железной рудой, так и кислородом (в газообразной форме). Так как подшипниковые стали флокеночувствительны, надо минимизировать присутствие водорода. Когда окислительный шлак скачан, а металл науглеродили, ванну раскисляют. Для этой цели применяют металлические раскислители.
Практикуется еще и вакуумная обработка, которую на передовых предприятиях сочетают со шлаковой методикой.
Маркировка и марки
Обычно шарикоподшипниковые стальные сплавы подразделяют на:
-
соединения общего назначения:
-
ШХ15 и ЩХ20СГ;
-
металл для химически агрессивной среды (например, 9Х18);
-
материал для подшипников, действующих при динамически меняющейся нагрузке (20Х18Н4А, 18ХГТ, 20Х18Н4ВА).
В последнем случае может практиковаться дополнительная цементация. Ее глубина составляет 0,08-0,35 см. В некоторых случаях дополнительно наклепывают поверхность. Это позволяет повысить стойкость к усталостным воздействиям. Стали 20Х18Н4А и 18ХГТ, а также 95Х18 маркируются так же, как и все конструкционные сплавы, вообще.
Стали категории «ШХ» обозначаются иначе. Литера «Ш» говорит о шарикоподшипниковой категории. Символ «Х» свидетельствует о наличии хрома. Цифры после нее показывают концентрацию хрома (в десятых долях процента). В любом случае концентрация углерода составляет примерно 1%.
В ряде случаев маркировка включает указания на концентрацию кремния и марганца. Ее расписывают в точном соответствии с государственными стандартами.
При использовании специализированных вариантов выплавки маркировка включает дополнительные символы после дефиса. Буква «Ш» там значит получение путем электрошлакового переплава (если есть буква «Д» — то она говорит о двойном переплаве). Символ «В» пишут для металла, который вакуумировали вне печи, а «ПВ» показывает использование методики прямого восстановления.
Применение
В основном подшипниковые стали используются для изготовления подшипников качения и других подшипниковых изделий — шариковых, радиально-упорных, самоустанавливающихся и прочих типов. Помимо основных частей подшипников, из них делают еще и обоймы. Такие обоймы довольно надежны, весьма стойко переносят износ и имеют вполне приличное качество. Но на этом сферы применения подшипниковых сталей не заканчиваются.
Из них изготавливают и многие другие изделия. В основном речь идет про выработку ножей и прочих бытовых товаров. Чаще всего для ножевого производства отпускают хромистую сталь ШХ15, отличающуюся низким уровнем легирования. Подобный сплав хорошо переносит коррозионные воздействия и мало подвержен износу, к тому же он довольно твердый.
Грамотная термическая обработка позволит нарастить твердость материала без потери его пластичности и вязкости.
Еще могут быть сделаны:
-
шарики и ролики;
-
плунжерные втулки;
-
клапаны для нагнетания;
-
толкающие ролики;
-
цельнокатаные кольца.