Химический состав сталей
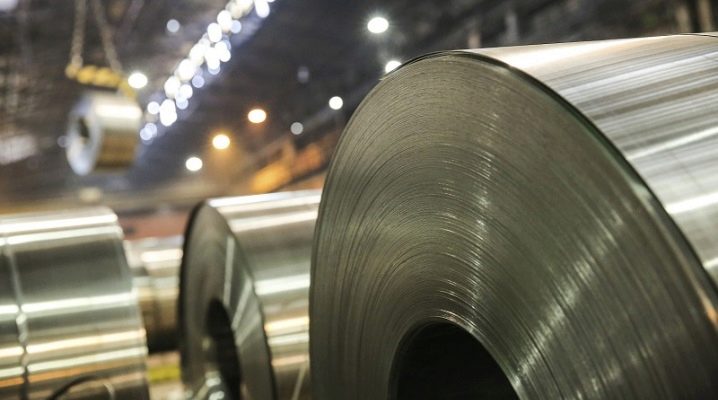
Химический состав сталей — тема практически неисчерпаемая, но оттого ее важность не становится меньшей. Любой потребитель обязан четко представлять себе классификацию сталей по составу. Особенно актуально обратить внимание на состав стали 3 и 45, 20Х и 20ХНЗА, 45Х и 35, 40ХНМА и У9А.
Как влияет на свойства?
Ценность изучения химического состава сталей в том и состоит, что каждое вводимое в них вещество воздействует определенным образом. Совершенно обязательный углерод обеспечивает во многом твердость и упругость. Отвечает он также за прочность материала. Однако тот же карбоновый компонент делает сталь менее вязкой, затрудняет ее сварку и механическую обработку. Польза кремния для металлургов несомненна. Они используют его как раскислитель. По умолчанию этот элемент содержится в незначительном количестве. Существенного воздействия на параметры сплава он не оказывает. Но если кремния будет свыше 2%, хрупкость стали заметно возрастет. Ковать ее нельзя, потому что она будет разрушаться.
Сера и фосфор — однозначно вредные компоненты. Только в автоматных сталях допускается относительно высокое их содержание, но и там оно жестко нормируется. Значительная концентрация серы приводит к красноломкости. При попытке ковать подобный металл в разогретом состоянии он будет трескаться. Фосфор ведет к появлению эффекта хладноломкости. Но надо понимать, что фосфористые стали чуть лучше обрабатываются (отделение стружки улучшается).
Марганец по умолчанию присутствует в объеме 0,3-0,8%. Этот элемент не оказывает серьезного воздействия на свойства. Он отчасти компенсирует вредные воздействия серы и кислорода. Легируя сплав марганцем, металлурги добиваются лучшей твердости. Немного вырастает пригодность его для режущих инструментов, сокращается риск появления красноломкости, улучшается и прокаливаемость. Однако сопротивляемость ударной нагрузке понизится.
Хромированный продукт менее вязок и имеет низкую теплопроводность. Но все же такие сплавы весьма популярны. Введение хрома улучшает способность стали закаливаться.
Металл:
- станет прочнее;
- приобретет большую жаростойкость;
- улучшит пригодность для режущих инструментов;
- не будет преждевременно истираться.
В простых сортах стали доля хрома составляет не более 2%. В специальных марках его может быть до 1/4. Такие добавки точно исключат коррозию. Полезен в антикоррозийном плане и титан. Его применяют, чтобы сделать сталь прочнее и плотнее. При введении титановых добавок растет ее пластичность и упрощается производство готовых изделий на станках. Молибден увеличивает прочность и твердость одновременно. Благодаря нему сокращается вероятность поломки при горячей ковке. Молибденовые стали мало подвержены коррозии. Они достаточно теплоустойчивы, чтобы подходить для конструкций в сфере энергетического машиностроения. Такой металл имеет высокую несущую способность даже под воздействием ударных нагрузок и значительных температур. Правда, его сварка встречает затруднения.
Ниобий вводят, чтобы повысить стойкость к кислотам. Косвенно он помогает сократить коррозию сварного шва. От никеля зависят вязкие свойства и упругость, однако он немного понижает теплопроводность. Вольфрам, реагируя с углеродом, наращивает твердость и понижает красноломкость сплава. Его примесь способствует росту работоспособности сталей, оптимизирует их способность к прокаливанию. Стоит вкратце охарактеризовать и влияние других базовых элементов. Ванадий способствует образованию мелких зерен. Пригодность для сваривания повышается. Раскисляющий эффект позволяет добиться большей плотности.
Кобальт помогает увеличить жаропрочность. Кобальтовые стали имеют более высокие магнитные характеристики. Алюминий используют в производстве стали в качестве раскислителя. Он способствует выработке мелкозернистой структуры. После добавления такого компонента штамповая обработка будет идти проще.
Медь не сказывается на пригодности для сваривания, но благодаря ней растет стойкость к коррозии и улучшается текучесть.
Классификация сталей по составу
Сплавы могут быть разными по своему составу.
Углеродистые
Стали подразделяются не только по тем свойствам, которые определяют элементы по отдельности. Углеродистые стали имеют низкую концентрацию добавок. Свыше 70% всего проката в мире относится именно к такому типу. Решающее значение имеет концентрация углерода. За счет ее варьирования технологи научились влиять на:
- текучесть;
- общую твердость;
- плотность материала;
- уровень его пластичности.
Среди углеродистых сталей бывают частные виды:
- феррит и перлит образуются при количестве карбонового компонента меньше 0,8%;
- при точном содержании в 0,8% типична перлитная структура;
- если концентрация вырастает более 0,8%, там появляется цементит.
Конструкционную углеродистую продукцию, сообразно названию, используют для получения арматуры и иных частей строительных конструкций. Доля углерода при этом составляет не более 0,65%. Принято делить такой металл уже по степени качества: на обыкновенный, качественный и специальный разряды. Для строительства применима сталь всех групп по качеству, с учетом требований. Инструментальная продукция существенно отличается и к ней предъявляют иные запросы.
Легированные
В них, в отличие от углеродистых, содержится больше марганца и кремния. Добавляется также как минимум один легирующий (улучшающий) компонент. Такие сплавы классифицируются именно по концентрации оптимизирующих добавок. Низколегированный продукт подходит для инструмента с низкими практическими характеристиками.
Высоколегированная сталь ценится за улучшенные технологические параметры, привлекательную закаливаемость и способность прокаливаться, за то, что она меньше коробится. Еще больше легирующих элементов в быстрорежущих сталях.
Маркировка и обзор марок
Уже традиционно стоит напомнить, что в большинстве случаев первые 2 цифры в марке стали — это десятые доли процента углерода. При отсутствии таких цифр можно считать его концентрацию равной или большей 1%. Прочие элементы обозначаются уже цифрами перед буквенным символом. Сталь 3 вообще никаких букв не содержит. В ней есть от 0,14 до 0,22% углерода, на долю марганца приходится от 0,4 до 0,6%. Качественная углеродистая сталь 45 более богата углеродом. Его концентрация может достичь 0,5%. Для марганца это минимальная планка, максимально же его бывает 0,8%. У сплава 45Х доля углеродного компонента может достичь 0,41-0,49%, при этом туда вводят еще не менее 0,8% хрома и не более 0,8% марганца. Не менее любопытной может оказаться сталь №5.
Это классический углеродистый металл обыкновенного качества. При содержании того самого углерода от 0,28 до 0,37% в нем присутствует еще:
- минимум 0,5% марганца;
- 0,15-0,3% кремния;
- до 0,3% меди.
Сталь 20Х — это хромистый сплав с содержанием не более 0,3% никеля. Концентрация меди в нем ограничена той же планкой, а вот углерода не менее 0,17%. Среди конструкционных углеродистых сплавов выделяется еще и сталь 35. Разброс содержания углерода — от 0,32 до 0,4%. Сопротивление разрыву в краткосрочной перспективе составляет 530 МПа. Вариант 25Г2С оптимально подходит для сварных конструкций. Хрома там содержится максимум 0,3%, а вот марганца может быть в 5 раз больше. Содержание кремния втрое выше, чем хрома.
Среди легированных сталей стоит упомянуть 40ХНМА. При концентрации углеродной добавки от 0,37 до 0,44% присутствует заметно больше никеля (допускается свыше 1,4%).
Хорошим легированием отличается также сплав 20Г, однако в нем явно меньше углерода (строго максимум 0,24%), а тем более никеля. Основной упор делается на марганец, которого может оказаться до 1%. Если нужно выбрать богатый никелем сплав, то это будет 18Х2Н4МА (4,4%) при содержании углерода максимум 1/5 процента и марганца не более 0,55%. В составе 20ХН содержится от 1 до 1,4% никеля и до 3/4 процента хрома. А закаливаемый при 860 градусах в масле металл 38Х2Н2МФА включает около 95% железа. Допустимый разброс никеля – от 1,3 до 1,7%, молибдена будет максимум 0,3%.
Марка У9А красноречиво говорит про углеродистость на уровне 0,9%. Концентрация главного улучшителя (марганца) при этом достигает 0,28%. В случае 20ХГСА нормировано строгое вхождение кальция (максимум 3/1000 процента). При этом марганца может быть до 1,1, а кремния – даже до 1,2%. Что касается других марок:
- 2ХНЗА улучшается никелем и хромом (до 3,15 и до 0,9%, соответственно);
- в составе 7ХФ не допускается присутствие менее 97,3% железа, более 0,6% марганца и свыше 0,7% хрома;
- для сплава 09Г2 официальный норматив устанавливает довольно большую (до 1,8%) концентрацию марганца, долю никеля задает максимум 0,3%, а углерода можно включать не более 0,12%.