Особенности конструкционных сталей и их классификация
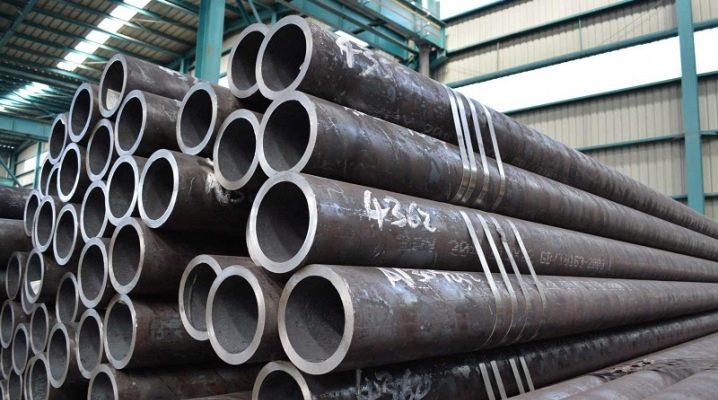
Разбираясь с особенностями конструкционных сталей и с их классификацией, надо точно знать сначала, что это такое, по сути. После этого придется изучать отличия от инструментальных сталей. А также потребуется ознакомиться с марками углеродистых качественных сталей и других видов металла, с положениями ГОСТа.
Что это такое?
Главным моментом, характерным для конструкционных сталей, является их целевая область применения. Такие металлические сплавы активно используются в создании строительных конструкций и составных элементов транспорта, различных машин. Это один из самых распространенных материалов в промышленной сфере. Он хорошо поддается штамповке и другим методам механической обработки. Важно обратить внимание и на отличия от инструментальных сплавов.
Другой вариант металла находит применение в выпуске твердых и стойких к износу приспособлений. В такой продукции нормативное содержание углерода составляет минимум 0,7%. В основном для нее типична:
- ледебуритная;
- доэвтектоидная;
- заэвтектоидная структура.
Независимо от конкретной структуры, металл включает карбиды. Они возникают при эвтектоидной модификации. Но иногда карбиды появляются при распаде мартенсита. Спрос на конструкционные стали довольно велик и непрерывно возрастает.
Встречается большое количество сплавов такой категории, имеющих самые разные практические характеристики.
Основные свойства
Главные механические характеристики металла определяются содержанием углерода. По химическому составу высокосортная конструкционная сталь отвечает требованиям ГОСТ 1050 от 1988 года. Этот стандарт предусматривает нормальное либо увеличенное содержание марганца. Правильный микроструктурный анализ очень важен, поскольку позволяет убедиться в безопасности использования материала при пожаре. Значимость концентрации углерода определяется тем, что она влияет на хладноломкость и возможность переносить серьезные температурные нагрузки.
Диапазон текучести — это наибольший уровень сжатия (то есть сжимающей деформации), в случае которого образец не разрушается. Только при высоком диапазоне текучести и получается классифицировать сплав как конструкционный материал. Важную роль играет и концентрация дополнительных примесей в составе сплава. Они влияют на характеристики материала и определяют, насколько прочным и качественным оказывается производимый продукт.
Плотность конструкционного металла отличается в разных случаях весьма сильно. Надо помнить, что подобно другим сталям, этот продукт может менять свою удельную массу при разной температуре. Важно обратить внимание и на усталостное разрушение. Так называют подверженность разрушению при повторяющихся, часто циклических, нагрузках. Во многом оно связано с неоднородностью структуры на микроуровне.
Это не только различие зерен по размеру и их свойств, но и разница в их ориентации, посторонние включения, присутствие шлаков. Важны и дефекты кристаллической решетки. Трещины обычно развиваются на микроуровне в зависимости от того, какие напряжения присутствуют в материале.
Твердость конструкционной стали, как и у других видов металла, определяется по глубине вдавливания специальной иглы в ходе профессионального теста.
Виды и марки
Обыкновенного качества
Примером таких углеродистых сталей в общепринятой классификации является сплав ВСт3сп. Этот металл сваривают без всякого риска и проблем. Заблаговременный прогрев конструкций не требуется. Однако иногда, если толщина металла превышает 3,5 см, это будет нужно. Рабочий диапазон температур варьируется от –40 до +425 градусов.
Прочие особенности ВСт3сп:
- отсутствие флокеночувствительности;
- отсутствие хрупкости при отпуске;
- высокоэффективная обработка резанием;
- содержание железа не ниже 97,8%;
- концентрация марганца от 0,4 до 0,65%.
Качественные
Стоит обратить внимание, что стали делятся по признакам совершенства на уже упомянутые обыкновенные и высокого качества. В разряд улучшаемых металлов входят углеродистые и содержащие легирующие компоненты сплавы, которые закаливают на мартенсит и подвергают затем высокому отпуску. Концентрация углерода колеблется от 0,3 до 0,55%. Хорошим примером является сталь марки 10. Обозначение ее говорит про концентрацию углерода на уровне 0,1%. Поставляют качественные конструкционные сплавы в виде:
- сортового проката;
- тонких и толстых листов;
- полос;
- труб;
- проволоки;
- ленты (производимой согласно ГОСТ 6009 от 1974 года).
Сталь 10 работает уверенно при температуре от –40 до +450 градусов. Легирующие компоненты при ее изготовлении почти не применяются, потому это считается нелегированный металл. Отмечают повышенные пластические качества такого металлургического продукта. Для лучшей обрабатываемости сталь 10 подвергают нормализации при 930-950 градусах. Появление флокенов нехарактерно.
Автоматные
Такое название носят отнюдь не те сплавы, которые отпускают на производство автоматических винтовок. Зато они находят применение в производстве метизов для строительных нужд и для машиностроения. Чтобы очень тонко и скрупулезно обработать поверхность такой стали, она должна иметь особые свойства. Добиться их можно только за счет повышенного содержания серы и фосфора. В этом смысле автоматная сталь — единственный случай, когда концентрацию таких элементов технологи стремятся не уменьшить, а нарастить до определенного предела.
Подобный материал в отличие от сплавов общего назначения гораздо легче подвергается воздействию металлообрабатывающих станков. При работе с таким сырьем резцы мало изнашиваются, что радует любого инженера и станочника. Готовые метизы будут по умолчанию иметь низкую шероховатость, и их поверхности почти не требуется дорабатывать. Автоматными бывают как обычные углеродистые, так и подвергнутые легированию материалы.
Помимо метизов, из них получают еще шестеренки и валы.
Легированные
Разобрать этот тип очень важно уже в силу того, что строительные сварные конструкции делаются из него очень часто. Ничего удивительного в том нет, причиной является высокая коррозионная стойкость. Но сводить только к ней достоинства легированного металла будет не слишком правильно. Лишь после появления серьезной металлургии в XIX столетии стало возможно получать такой продукт в заметном количестве. Добавка кремния не отражается на вязкостных характеристиках; зато она увеличивает предел прочности, магнитную проницаемость и электропроводность.
Введение алюминия повышает устойчивость к старению. Этот элемент наращивает еще и пластичность металла. Благодаря хрому повышается прочность и твердость. Кислотостойкие конструкционные стали имеют большое количество хромистых добавок. Добавление никеля приводит к появлению значительного объема аустенита, в основном этот компонент требуется для жаропрочных и быстрорежущих сталей.
Наряду с такими легирующими веществами часто применяют:
- молибден;
- вольфрам;
- ванадий;
- медь;
- кобальт;
- редкоземельные металлы.
Теплоустойчивые
Это подвид легированных сталей. Он рассчитан на эксплуатацию при температуре до 600 градусов. Однако теплоустойчивые сплавы экономически нецелесообразно применять при температурах ниже 300 градусов. В основном их производят для энергетического машиностроения. Металл может иметь перлитную и мартенситную структуру.
Теплоустойчивую сталь часто заказывают производители:
- котлов;
- паропроводов;
- печей бытовых (вернее, их второстепенных элементов);
- деталей для топливной и химической индустрии.
Подшипниковые
Такой материал должен быть высокопрочным и отличаться приличной износостойкостью. Он еще и стойко переносит контактную устойчивость. Усиливать прокаливаемость помогает введение марганца и кремния. Они нужны для подшипников с толщиной стенки от 1 см и более. Подшипниковую сталь поставляют в виде проволоки либо прутков. Термическая обработка включает закалку и последующий низкотемпературный отпуск. Твердость варьируется у разных слоев. Доля углерода составляет от 0,95 до 1,15%.
Важной чертой подшипникового металла является легкость закаливания. Это зависит от добавления хрома, придающего металлу заэвтектоидную структуру.
Рессорно-пружинные
Ее важнейшая характеристика — высокий уровень текучести. Отпуск проводится при 350-500 градусах. В основном эта категория представлена кремнистыми сталями, содержащими до 2% легирующего вещества. Упругость обеспечивается во многом путем масляной закалки. Дальше отпуск проводится при среднем уровне температур.
Характеристика рессорно-пружинной стали — ограниченность упругой деструкции. Материал делают согласно ГОСТ 14959 от 1979 года. Хорошими примерами являются:
- 3К7;
- 50ХГА;
- 50ХФА;
- 55С2А.
Конструкционная сталь при грамотной обработке отлично сопротивляется пластической деформации. При одинаковом количестве углерода она выигрывает у лучших углеродистых материалов. Прокаливание идет гораздо интенсивнее, чем обычно. Термообработка проводится при помощи мягких охладительных масел. Недостатками такого продукта выступают:
- обратимая отпускная хрупкость;
- подверженность усталости после теплового воздействия;
- при легировании никелем — образование флокенов;
- строчечная структура после ковки и прокатной обработки.
Очень важно изучить правила маркировки — что позволяет прочитать любое обозначение. Легированные металлы маркируют прежде всего двузначным числом, равным концентрации углерода (измеряемой в сотых долях процента). Следующие буквы в марке показывают улучшающие вещества. Если после буквы не пишутся цифры, значит, концентрация улучшителей не превышает 1%.
Обработка и сварка
Конструкционную сталь для получения трубных заготовок часто подвергают холодной радиальной ковке. Перед этой процедурой, однако, требуется термическое улучшение. Важной чертой продукта является наличие особо мелкозернистой и нанокристаллической структуры. Такие состояния вещества позволяют добиться превосходных механических характеристик. Добиться подобного диспергирования структуры стали помогает механико-термическая обработка (та самая радиальная ковка) в холодном состоянии и дальнейший отжиг.
Ковочная обработка по радиусной схеме гарантирует повышенную деформацию особо точных длинномерных поковок. Такой подход приводит к возникновению особенно дробной деформации. Очаги деформирования многократно перекрываются, и накапливается в итоге повышенная степень деформации. Отжигая металл, провоцируют рекристаллизацию и получают дисперсную структуру.
Контроль микроскопической структуры проводится на микрошлифах с помощью сертифицированных оптических микроскопов.
Термическое улучшение (по крайней мере для сплава 09Г2С) приводит к возникновению сорбитной структуры. Имеется также избыточная ферритная фаза. При грамотной рекристаллизации получается однородная структура. Она будет совершенно монолитна по всему сечению стенки заготовки. Обнаружить при наблюдении через оптический микроскоп структурно свободный феррит почти не удается — он практически отсутствует.
Отжигая сталь 09Г2С при 500 градусах, провоцируют ее разупрочнение. Уровень прочности сокращается на 15% в сравнении с холоднодеформированным состоянием. Однако предел прочности почти не изменяется. Относительное удлинение немного увеличивается, но оно окажется примерно вдвое меньше, чем в термоулучшенном виде. Последеформационный прогрев до 300 градусов почти не влияет на прочность, но чуть уменьшает надежность.
Сварочные работы с низкоуглеродистыми конструкционными сталями наиболее просты. Часто применяют ручную сварку при помощи обмазочных электродов. Особенно важен подбор самой марки электродов. Подготовка соединяемых деталей должна идти тщательно. Газовая сварка тоже возможна — и для нее не требуют дополнительные флюсы; идеальной присадкой считается металлическая проволока с небольшой долей углерода, которая уменьшает возникновение пор.
Ответственные изделия из конструкционной стали варят в атмосфере аргона. Подготовленное изделие необходимо нормализовать. Для этой цели прогревают вещь до 400 градусов, потом выдерживают и остужают в воздушной среде. Структура металла после такой обработки становится равномернее. Низкоуглеродистый конструкционный металл можно варить ручным способом при помощи покрытых электродов, лучше всего в низком пространственном размещении.
Для электрошлаковой сварки конструкционных сталей рекомендуется применять флюсы. Электроды могут быть проволочного или пластинчатого типа. Их выбирают с поправкой на химический состав сплава. Автоматический и полуавтоматический режимы обработки проводят в среде чистого аргона либо гелия. Уменьшить расходы во многих случаях помогает применение высококачественной углекислоты.
Среднеуглеродистые сплавы можно ковать. Сварка происходит труднее, чем в случае низкоуглеродистого металла. Необходимо помнить про то, что основной и наплавляемый металл будут иметь разную прочность. А также проблемой является значительная опасность крупных трещин и непластичных участков рядом со швом. Кристаллизационные дефекты также весьма вероятны.
До начала сварки конструкцию очищают от засорений и ржавых участков. Недопустимо появление любой окалины. Детали под сварочную обработку составляют с зазором, который определяется толщиной предмета. Точный выбор режима обработки проверяют по степени твердости наплавляемого металла. В идеале она должна быть максимум 350 HV; самые ответственные части варят в 2 прохода и более.
Высокоуглеродистые стали варить очень сложно. Эту работу проводят при предварительном прогреве до 150-400 градусов. Во время сварки значительный нагрев должен сохраняться. Дополнительно важна термообработка после окончания работы. Рекомендовано сваривание узкими валиками, и каждый наплавленный слой последовательно остужают. Сварка под флюсом в основном идет автоматически. Этим занимаются при выдаче переменного тока. Газосварочная обработка высокоуглеродистой конструкционной стали нецелесообразна. Это провоцируется выгоранием заметного объема углерода.
Газовая сварка такого металла проводится только в отношении рядовых конструкций, при расходовании до 90 куб. м ацетилена за 60 минут.