Какие бывают режимы резания при фрезеровании?
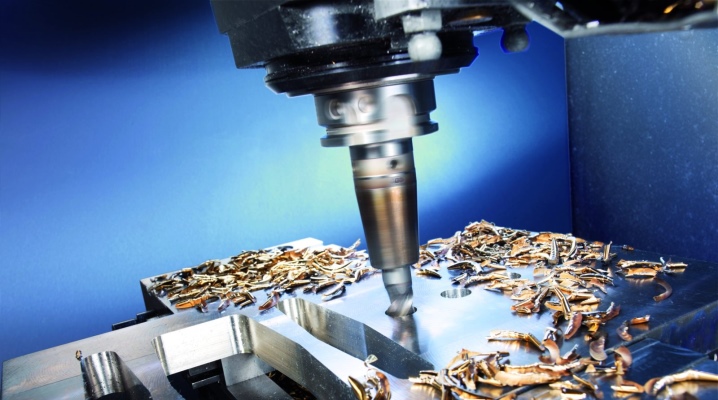
Фрезерование — это способ обработки различных поверхностей фрезой. Во время работы станка режущий инструмент с зубьями совершает вращение вокруг своей оси, в то время как материал заготовки поступает на него. В результате происходит отделение слоя металла, сплава или древесины в виде стружки и обработка поверхности. Сегодня большинство станков для фрезерной обработки снабжены числовым программным управлением, что позволяет работать оборудованию бесперебойно в автоматическом режиме. Рассмотрим основные характеристики, влияющие на работу фрезерного станка.
Скорость резания
Основной тип движения при фрезеровании — вращение режущего элемента. Оно оценивается показателем скорости. Для фрезы это путь в метрах (м), который преодолевают по окружности режущие кромки её зубьев за 1 минуту. Параметр характеризует быстроту работы фрезерного станка, а также скорость снятия слоя материала с обрабатываемой поверхности, измеряется в м/мин.
На практике скорость фрезеровки вычисляется по справочным таблицам или с помощью специально разработанных калькуляторов. Технически фрезеровщик не может управлять этим параметром, он может регулировать другой показатель, от которого зависит скорость — частоту вращения шпинделя.
Сегодня среднестатистическое оборудование рассчитано на работу от 12 до 24 тыс. об/мин, что, к примеру, соответствует скорости резания 100-400 м/мин для пятимиллиметровой фрезы.
Перед работой на станке мастер составляет схему, где учитывает все параметры рабочего оборудования. Скорость резания выбирается с учётом эксплуатационных характеристик станка, глубины резания, вида обрабатываемого материала и скорости его подачи на станок. Отличия в скорости обработки различных материалов определяются степенью их прочности, упругости и пластичности.
- Нержавеющая сталь. Оптимальная скорость резания — 45-100 м/мин. Добавление в состав различных элементов повышает твёрдость сплава, что может отрицательно сказаться на состоянии высокоскоростного оборудования. В таком случае придётся пожертвовать качеством обрабатываемой поверхности взамен за сохранность фрезы.
- Бронза и латунь. Оптимальная скорость обработки — 90-170 м/мин и 130-320 м/мин соответственно. Это относительно мягкие сплавы, состав которых позволяет обрабатывать их быстрее, получая гладкую поверхность. При нагревании они частично размягчаются, что рекомендуется учитывать при обработке бронзовых и латунных заготовок.
- Алюминий. Оптимальная скорость резания — 200-430 м/мин. Это очень мягкий металл, который обладает низкой температурой плавления. Обработка его не составляет трудностей, однако, на высоких скоростях из-за повышенного размягчения металла можно случайно повредить заготовку.
- Полимерные материалы. Оптимальная скорость резания — 100-200 м/мин. Акрил и другие пластмассы обладают средними показателями твёрдости. Температура их плавления ещё ниже, чем у металлов и сплавов, поэтому не стоит злоупотреблять высокими скоростями вращения при их обработке.
- Древесина. Оптимальная скорость резания — 230-310 м/мин. Материал по свойствам абсолютно не похож на предыдущие. Дерево обладает хорошими параметрами упругости и пластичности, но даже самые твёрдые породы, такие как лиственница и дуб, имеют свойства растрескиваться от механических воздействий. При обработке древесины выбирается высокая скорость, а слои удаляются постепенно. При этом стоит учитывать возможность её самовоспламенения из-за сильного нагрева, что усложняет процесс обработки.
Скорость резания всегда требует точных расчётов. Незначительные отклонения как от минимальной, так и максимально допустимой величины могут привести к поломке фрезы, изнашиванию частей станка и, соответственно, к порче обрабатываемой заготовки. Специалисты рекомендуют занижать фактическую скорость на 10-15% от максимально допустимой. Это позволит сохранить качество обрабатываемой поверхности, а также производительность труда без механического износа оборудования.
При работе с любым материалом рекомендуется учитывать обязательный нагрев фрезы вследствие длительной работы оборудования. Это явление отрицательно сказывается на состоянии режущего инструмента и обрабатываемого материала, поэтому сегодня большинство фрезерных станков оборудуются системой подачи смазочно-охлаждающей жидкости.
Глубина резания
В процессе обработки детали на фрезерном станке режущий инструмент, сталкиваясь с поверхностью заготовки, снимает с неё слой материала в виде стружки. Величина снятого слоя за один проход фрезы и есть глубина резания. Параметр измеряется в мм и рассчитывается как разность между исходной и снятой в ходе фрезерования поверхностью.
Рабочий процесс фрезерной обработки обычно включает несколько проходов по заготовке и проводится в два этапа: черновой и чистовой. Первый предполагает максимальное снятие припуска детали, т. е. утилизируемой части материала, и проводится в 2-3 прохода. При этом выбираются наиболее допустимые значения глубины фрезерования при как можно меньшей скорости. Такой режим позволяет снять достаточное количество материала при незначительных нагрузках на оборудование.
Поверхностный слой заготовки получается негладким, шероховатым, поэтому далее следует чистовой этап, который обычно проводится в 1 проход. В ходе него фреза работает на максимально возможной скорости при незначительной глубине резания и как бы шлифует обрабатываемую поверхность, снимая незначительный слой материала.
На заметку! Если величина припуска детали минимальная и составляет несколько миллиметров, достаточно всего одного чистового прохода.
Стоит отметить, что глубина фрезерования выбирается по используемому материалу заготовки. К тому же параметр зависит от производительности станка и ограничивается его конструктивными особенностями. При использовании маломощного оборудования с небольшим режущим элементом требуется несколько проходов по заготовке, т. к. силы такого устройства иногда недостаточно, чтобы снять весь припуск сразу.
Регулировку фрезы по металлу можно сравнить с таковой у мотоблока. Плуг вспашет землю на такой глубине, которую вы заранее ему обеспечите, приложив собственные усилия. В противном случае культивировать он будет неглубоко, а без усилий вообще останется рыть землю на месте.
Виды подачи
Заготовка при обработке перемещается относительно оси станка, т. е. фрезы, по одной из трёх осей: продольной (x), поперечной (y) или вертикальной (z). Величина проходимого деталью расстояния называется подачей. Теоретически выделяют 3 вида подачи заготовки.
- На зуб, Sz — это величина перемещения детали при вращении режущего элемента на расстояние между кромками двух зубьев. Единицы измерения: мм/зуб.
- На оборот, So — это величина перемещения заготовки при одном полном обороте фрезы. Рассчитывается по формуле: So = Sz • z, где z — число зубьев режущего элемента. Единицы измерения: мм/об.
- Минутная, Sm — это расстояние, на которое перемещается обрабатываемая заготовка относительно фрезы за одну минуту. Рассчитывается по формуле: Sm = So • n = Sz • n • z, где n — частота вращения режущего элемента (об/мин); z — число зубьев режущего элемента. Единицы измерения: мм/мин.
На практике используется только минутная подача, которая является важной характеристикой режима резания при обработке деталей на фрезерном станке. Она регулируется в зависимости от материала заготовки, вида фрезы, режима резания и мощности оборудования. Параметр обратно пропорционален скорости резания. Так, высокая скорость требует уменьшения величины подачи. В противном случае будет возрастать осевая нагрузка на станок и степень сопротивления фрезы заготовке, что приведёт к быстрому механическому износу или поломке режущего элемента, шпинделя и других деталей установки.
При снижении величины подачи допускается увеличение скорости фрезерования, что в сочетании с небольшой глубиной резания используется для чистовой обработки поверхностей.
Ширина
Фрезерный станок, как правило, технически не способен обработать всю деталь сразу. Фрезеровке подвергается определённая поверхность, которая и является шириной фрезерования. Показатель измеряется в мм и определяет ширину снимаемого слоя материала, которая перпендикулярна его подаче. Фактически это расстояние, на котором кромки зубьев режущего элемента соприкасаются с поверхностью заготовки. Параметр указывается в технологической схеме перед началом обработки детали. Зная значение ширины фрезерования, а также величину заготовки, мастер может заранее определить необходимое количество проходов.
Параметр варьируется в широком диапазоне и зависит от диаметра фрезы. Для каждого режущего элемента ширина фрезерования является константой, так как изменить геометрические показатели невозможно. При большом количестве обрабатываемого материала рекомендуется использовать режущие элементы соответствующих размеров. Это необходимо для того, чтобы снизить время работы на станке, затраты на эксплуатацию оборудования, а также уменьшить показатели нагрузки.
Рекомендации по выбору режима
Выбор правильного режима работы фрезеровочного станка играет важную роль в процессе обработки материалов и изготовления деталей. Точное соотношение рекомендуемых параметров позволит мастеру добиться лучшей производительности при тех же рабочих затратах, уменьшит износ деталей станка и сохранит заготовку в хорошем состоянии. Сегодня специалисты-фрезеровщики разработали большое количество таблиц и технологических карт. Их можно использовать в качестве примера при выборе оптимального режима.
Если готовые схемы для работы отсутствуют, специальные онлайн-калькуляторы или компьютерные программы помогут с расчётом параметров процесса. В них заранее внесены все формулы, мастеру необходимо лишь указать базовые характеристики станка и фрезы.
При выборе технологического режима мастера руководствуются следующими критериями.
- Параметры станка. Технические характеристики оборудования оказывают наиболее значимое влияние на процесс. При работе следует принимать во внимание его возраст. На современных станках с ЧПУ результаты работы будут лучше, чем на оборудовании возрастом 10-15 лет. Связано это и с меняющимися технологиями разработки, и с механическим износом отдельных частей. Именно поэтому следует периодически проверять техническое состояние оборудования, вовремя ремонтировать неисправности и утилизировать брак.
- Также от возраста системы зависит её прочность. Новое оборудование без особых усилий выдержит высокие нагрузки и качественно обработает любые твёрдые сплавы. Более старые модели, в свою очередь, чаще подвержены поломке, поэтому непригодны для работы с такими материалами.
- Другая часть результатов процесса зависит от предустановленных параметров в зависимости от используемого материала. Это касается скорости, которая варьируется в пределах 50-400 м/мин. Рекомендуется начинать работу со средним значением, а в процессе фрезеровки менять его в необходимую сторону. В противном случае высокая частота вращения шпинделя может привести к его поломке, а низкая — испортить материал.
- Станок не должен испытывать сопротивление при работе, поэтому необходимо постоянно регулировать величину нагрузки на ось. Для этого можно менять параметры глубины резания и подачи. Оптимальное значение последнего в начале работы составляет 0,15 мм/зуб.
- Последней особенностью работы фрезеровочного станка является необходимость в его постоянном охлаждении. Для этого современные устройства оборудованы системой подачи смазочно-охлаждающей жидкости в зону обработки. Это существенно снижает нагревание режущих кромок зубьев, что лучше сказывается на состоянии заготовки. Также СОЖ удаляет с материала постоянно образующуюся стружку и пыль.
- Особенности режущей части. Свойства фрезы оказывают существенное влияние на качество процесса. При выборе инструмента обратите внимание на его состав. Для обработки большинства металлов, пластмасс, древесины достаточно обычной фрезы из быстрорежущей нержавейки. При работе с твёрдыми сплавами рекомендуется использовать режущие элементы с тугоплавкими напайками на зубьях. Так инструмент не сломается после нескольких минут работы и не испортит заготовку.
- Имеет значение также диаметр режущего элемента, с увеличением которого пропорционально снижаются скорость фрезерования и подачи, при этом увеличивается ширина резания. Рекомендуется выбирать диаметр, соответствующий глубине обработки и виду используемого материала. Тогда для работы достаточно будет всего нескольких проходов. Качество фрезерованной поверхности зависит от длины режущего элемента, количества зубьев и угла заточки их режущей кромки. Большинство фрез изготавливается с 4-мя зубьями, что позволяет добиться лучшего соотношения между скоростью процесса и состоянием заготовки.
- Особенности материала – самый важный критерий во всем процессе. Именно от свойств заготовки зависит большинство настраиваемых параметров. Среди особенностей материала важны степень твёрдости, пластичности и упругости. Первый параметр прямо влияет на прочности детали и её износостойкость. С другой стороны, обработка таких материалов существенно усложняется. Всегда есть риск износа или поломки оборудования. Иногда это приводит к порче заготовки.
Поэтому для обработки твёрдых металлов и их сплавов, например, калёной стали или титана, следует снижать глубину и скорость резания станка, а также использовать фрезы с тугоплавкими напайками. Показатели пластичности и упругости существенно зависят от величины нагрева материала. При работе с такими сплавами, как бронза или латунь, эти свойства могут оказаться полезными, в то время как для других металлов они окажутся причиной порчи заготовки.
Для алюминия
Среди всех использующихся металлов при изготовлении деталей этот самый мягкий. В сочетании с высокой степенью пластичности алюминий легко подвергается обработке. В то же время стоит учесть его относительно низкую температуру плавления — 660 C, что может привести к размягчению заготовки при сильном нагревании фрезы.
Обработку алюминия рекомендуется начинать со скорости 250-300 м/мин и постепенно повышать её до 400-420, если станок оборудован системой подачи СОЖ. Глубина резания при этом должна быть минимальной. В таком режиме фреза будет быстро снимать несколько миллиметров слоя поверхности, что позволит сохранить структуру и свойства металла.
Для дерева
Древесина, в зависимости от породы, характеризуется различными параметрами твёрдости. Большинство видов при этом обладает хорошей упругостью и пластичностью, которые, к сожалению, пропадают при полном высушивании. Такой материал необходимо обрабатывать на высоких скоростях, чтобы избежать появления трещин и дефектов. Оптимальный режим — 250 м/мин при небольшой глубине.
Независимо от материала, любой режим резания считается оптимальным, если все параметры сочетаются между собой разумно, обеспечивают максимальную производительность и точность работы. Сегодня практически любой человек, воспользовавшись справочными пособиями и калькуляторами, способен за несколько дней овладеть навыками фрезерования. Однако одних таблиц для выбора правильного режима недостаточно: необходимы многолетний опыт и знания всех особенностей работы.