Способы и техника сварки трением
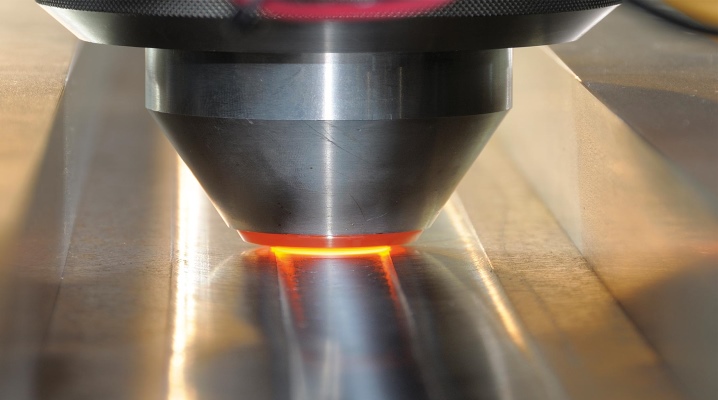
Изобретённая сравнительно недавно сварка трением, быстро заняла достойное место среди множества иных методов сварки. Сегодня благодаря минимальной энергозатратности, высокому качеству сварочных швов, отсутствию расходных материалов и значительной экономии времени фрикционный метод распространён в атомной энергетике, кораблестроении и машиностроении.
Что это такое?
Технологии и понятийный аппарат метода регламентируются ГОСТ 260184. Указанный процесс стоит несколько особняком от прочих способов сварки, что обусловлено технологическими особенностями способа. Для нагрева соединяемых элементов используется тепловая энергия, выделяемая в ходе трения заготовленных элементов.
Наиболее актуальным и распространённым здесь является трение вращения, при котором вращается один из свариваемых элементов. В ходе процесса элементы с усилием прижимаются друг к другу, с постепенным ростом силы прижатия. Одновременно с нагревом подвергаются разрушению поверхностные окисные пленки, а также остатки различных загрязнений. Поверхности элементов постепенно плотно притираются между собой, удаляются выступы и неровности, а атомы свариваемых материалов получают доступ к тесному взаимодействию.
При этом контакты на уровне кристаллических структур быстротечны и скоро разрушаются за счет энергичного вращения элементов.
Обсуждаемый способ в значительной мере проще, чем, например, газовый.
Среди особенностей технологии отмечают ряд факторов.
- Возможность качественного соединения неоднородных материалов. При этом нет необходимости применять присадки и более сложное оборудование.
- Возможность создать качественное и плотное соединение элементов из меди, свинца, титана, избегая деформаций деталей.
- Наибольшая продуктивность метода фиксируется при обработке заготовок диаметром 6-100 мм.
- Возможность соединять плохо свариваемые металлы. Например, детали из алюминия и стали.
Метод широко применяется и для соединения предметов из термопластика.
Преимущества и недостатки
У этой уникальной технологии множество преимуществ.
- Высокий уровень производительности. Сварочный цикл длится несколько секунд, иногда минут. Значительно меньше времени уходит и на подготовку операций. Таким образом, обсуждаемая технология выгоднее контактной электросварки.
- Экономия энергии. Нагрев обрабатываемых областей проявляется крайне скоро и в весьма локализованных районах, поэтому энергозатраты в десятки раз меньше, чем в иных технологиях.
- Высококачественные сварные швы. При оптимально выбранном режиме исполнения зона шва и его близлежащие края остаются абсолютно идентичными базовому материалу. Более того, в теле шва не остаётся дефектов (трещинок, инородных проявлений и прочего).
- Качественные и стабильные характеристики швов в партиях финишной продукции сохраняются – окончательные параметры изделий в них отличаются минимально, что предоставляет возможность реализации выборочного контроля, экономя время и средства.
- Не требуется предварительных механических зачисток шовной зоны и около неё, выполняемых в начальной фазе процесса.
- Возможность сваривания неоднородных материалов.
- Экологичность.
- Метод прекрасно поддается автоматизации, что актуально при крупных производственных сериях.
Стоит сказать и о недостатках.
- Применимость способа лежит в небольшой области форм деталей-заготовок. Метод не применяется для соединения удлиненных швов (прямых и кривых), непростых конфигураций, при монтаже стройконструкций, крупных корпусных элементов.
- Громоздкость агрегатов. Агрегаты требуют стационарной установки и электропитания.
- Ограничения в габаритах деталей, длина которых соизмерима с вылетом бабки агрегата, а диаметр — с выносом кулачков патрона.
- Появление возможных радиальных нарушений текстуры в зонах швов и около них. При значительных динамических нагрузках появляются места усталостных напряжений, возникают микротрещины и иные дефекты. Снижается и уровень антикоррозионной устойчивости. Во избежание таких последствий на деталях оставляют грат, на снятие которого уходит некоторое время.
Фазы
Основными фазами процесса являются:
- удаление оксидных пленок;
- разогрев соединяемых поверхностей до температуры создания и разрушения элементов кристаллических решеток (температура пластичности);
- прекращение вращательного движения, кристаллизация области контакта, формирование сварочного шва.
Обзор видов
На сегодняшний день разработаны и активно реализуются несколько специализированных (по области применения) методов фрикционной сварки, которая бывает:
- перемешивающая;
- радиальная;
- штифтовая;
- линейная;
- ротационная (для сварки тонкого листового металла);
- точечная;
- орбитальная и другие.
Перемешивающий способ
Технология с перемешиванием изобретена и применяется с конца прошедшего века. Суть способа состоит в применении особого штыря с заплечиками, изготовленного из высокопрочного сплава. Нагревая при вращении материал, штырь проходит в него по назначенной траектории. Благодаря его вращению в процесс вовлечены размякшие слои металла, которые перемешиваются. Таким образом достигается однородность структуры и параметров шва.
Радиальная
Этот способ используется при монтаже труб. В местах стыковки на них с малым зазором надевают кольцевую конструкцию из металла, которой придают ускоренное вращение. За счет возникающих фрикций появляется интенсивный нагрев торцов свариваемых труб. Кольца производятся из аналогичного трубам сплава.
Штифтовая
Технология штифтового способа используется для осуществления ремонтных работ. В детали для ремонта просверливают отверстие, в которое вводится штифт из подобного сплава. В процессе его вращения возникает значительное количество тепла, которое и обеспечивает процесс соединения. Это уникальный и мобильный способ фрикционной сварки.
Линейная
Этот вид сварки производится без вращения – свариваемые элементы, совершая встречные возвратно-поступательные движения, нагреваются. В критический момент движение прекращается, и детали сильно прижимаются друг к другу. Металлические излишки (грат), ставшие пластичными, выдавливаются из сварочной зоны, образуя шов.
Есть технологии, когда оба соединяемых предмета неподвижны, а в зоне шва о них трется особый инструмент.
Оборудование
Комплект сварочного оборудования может состоять из сварочной машины, мини-компьютера с программами заданных режимов, станка для устранения грата, погрузочно-разгрузочных манипуляторов и транспортировочных устройств.
Машины комплектуются рядом рабочих узлов (как на токарном станке): вращающийся привод, фрикционная муфта, шпиндель с ременной передачей, тормоз.
Фрикционный метод сварки предполагает использование и иных конструкций. Например, агрегатов для микро- и прецизионной сварки. В небольших агрегатах шпиндель развивает частоту вращения 80-650 с-1, которая является одним из главных параметров установки. При её повышении сварочный шов становится более однородным, а его прочность увеличивается. Оптимальная скорость вращения подбирается под конкретный металл.
Технология
Основной технологической операцией фрикционной сварки является нагрев соединяемых деталей за счёт сил трения, возникающий главным образом при вращательном движении заготовок.
Эта продуктивная технология широко применяется в машиностроении и прежде всего в инструментальной его сфере. Нередко её применяют и при сборочных работах в атомной энергетике. Популярен метод и при сварке алюминиево-магниевых сплавов в электротехнике и аэрокосмической области, в машиностроении.
Относительно недавно получил он своё развитие в судостроении. Тенденции развития способа тяготеют к вытеснению иных методов сварки в операциях по замене:
- пайки и клепки;
- электросварки;
- восстановительных операций узлов и сложного инструментария;
- в приваривании заготовок к различным, заранее обработанным элементам.
Технология полностью себя оправдывает там, где предъявляются высокие требования к экологичности сварочного цикла. Повышенный уровень энергоэффективности, отсутствие брызг раскалённого металла, неприятных выделений и результатов сгорания, ультрафиолета и низкий уровень пожарной опасности делают метод очень целесообразным.
Подготовка
В ходе проектирования заготовок для последующей сварки важно учитывать ряд факторов:
- возможности сварочного оборудования;
- степень свариваемости материалов;
- закрепление заготовок в сварочной машине;
- стоимость подготовительных мероприятий к сварке заготовок и последующей обработки сварных швов;
- соблюдение необходимой степени соосности и углового размещения заготовок;
- формирование равномерного температурного режима и одинаковых условий деформации;
- правильный выбор припусков по длине и диаметрам заготовок.
Обеспечение требуемой соосности зависит от степени надёжности закрепления деталей в зажимных устройствах агрегата. В этом контексте актуальным параметром становится уровень жёсткости свариваемых элементов по длине их выхода из зажимов. Если длина выхода меньше необходимого размера, то это приводит к температурному отпуску зажимных устройств.
При фрикционной сварке состояние соединяемых поверхностей в наименьшей степени влияет на качество сварных соединений, чем при иных методах сварки давлением. Поверхности для соединения могут быть получены в процессе резки на гильотине, дисковой пилой. Неровности можно устранить, используя притирку, или увеличением времени нагрева.
Небольшие коррозийные участки, остатки покраски, масла и других загрязнений на поверхностях устраняются в ходе нагрева.
Процесс
Начальная фаза процесса включает разрушение и устранение окисных плёнок, что достигается трением. Во второй фазе процесса рабочие кромки разогреваются до пластичного состояния, появления временного контакта. По достижении температуры плавления вращение прекращают, затем увеличивают силу прижатия поверхностей. Далее происходит выдавливание из стыковочного пространства пластичных объёмов металла.
К третьей фазе относят прекращение вращения и формирование сварочного соединения в целом.
Наглядная инструкция сварки трением в видео ниже.