Что такое ультразвуковая сварка и где она используется?
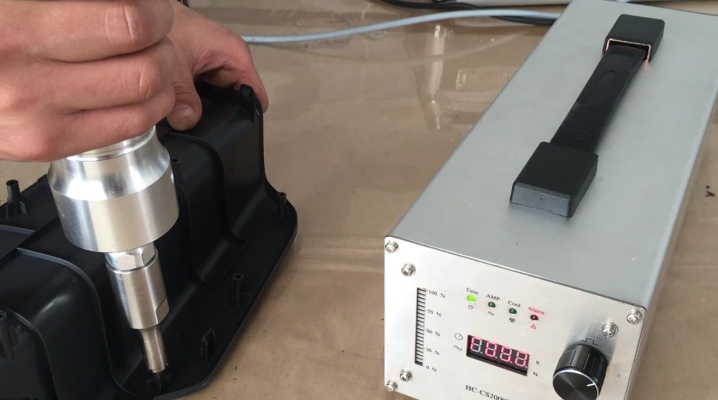
Даже начинающим домашним мастерам очень важно знать, что такое ультразвуковая сварка и где она используется. Эта технология уместна для работы с проводами и пластмассами, с цветными металлами и другими материалами. Критически важен выбор сварочной машины, контроль швов и другие тонкости, о которых и поговорим.
Особенности
Ультразвуковая сварка не является универсальной, однако, может применяться на особо сложных объектах или в личном хозяйстве. Между тем, ей уделяется мало внимания. Главным источником энергии при такой работе выступают высокочастотные звуковые колебания. С их помощью можно сваривать довольно разные материалы. Именно благодаря внедрению сварки ультразвуком еще в далекие 1960-е годы удалось начать выпуск автомашины, полностью сделанной из пластмассы.
Приготовить материал к соединению оказывается достаточно просто. Потребуется лишь обезжиривание поверхностей. Они могут быть довольно грязными и ржавыми, но на результат это не повлияет. Потому существенно понижается общая трудоемкость работы. Немаловажно и то, что разогрев затрагивает лишь локальный участок, и другие части поверхности изделия не будут деформированы.
Ультразвуковая обработка отлично подходит даже для весьма трудных работ, в том числе при манипуляциях в труднодоступных зонах. Сам процесс не занимает существенного времени — прогрев материала происходит примерно за 1 секунду. Еще ультразвук способен сварить детали толщиной порядка тысячных долей миллиметра, что принципиально невозможно при электродуговой, газовой методике или применении холодной сварки. И все же есть обстоятельства, которые не позволяют использовать ультразвуковую сварку повсеместно. Так, для этой работы оптимально подходят только дорогостоящие устройства — генераторы бюджетного класса иногда справляются со своей функцией плохо.
Чтобы ультразвуковая сварка давала приличный результат, требуется подвергать детали определенному давлению. При выполнении такой работы существенно уменьшаются затраты расходных материалов. Также стоит отметить:
отсутствие потребности в изолирующей атмосфере;
пригодность для работы с заготовками произвольной формы;
возможность полной автоматизации и интеграции с прочими технологическими процессами;
экологическую чистоту и сравнительную безопасность;
отсутствие особо высоких температур (то есть уменьшение пожарных рисков);
экономию энергии;
возможность соединять детали не крупнее 25 см;
непригодность для работы с толстостенными материалами;
непригодность для работы с сильно увлажненными материалами.
Сферы использования
Основную роль ультразвуковое сваривание имеет при работе с малогабаритными деталями. Его широко применяют, когда нужно выполнить соединение проводов, прежде всего в радиоэлектронных и приборостроительных производствах. Работа с металлом происходит при заметно более слабом нагреве, чем при использовании классических нагревательных методов. Потому можно не опасаться за сохранность компонентов, восприимчивых к чрезмерной температуре. Кроме того, ультразвук позволит приварить друг к другу изделия из цветных металлов, которые в обычных условиях присоединяются крайне неохотно.
Именно таким путем, к примеру, соединяют изделия из меди и алюминия, алюминий с никелем и другие подобные варианты. Прочность формируемого шва будет примерно 70% от показателей исходного сплава. Ультразвуковая методика подходит еще и для работы с тугоплавкими металлами и сплавами. Немаловажно, что она позволит в произвольных сочетаниях соединять:
композитные материалы;
металлы;
керамические изделия;
пластики;
стекло.
При сварке пластмасс ультразвуком можно добиться повышенной производительности и сократить себестоимость работы. Даже на довольно толстых пластмассовых заготовках удается добиться повышенной герметичности швов. Сами швы будут выглядеть лаконично и практически незаметно. Но необходимо понимать, что из-за ограниченной мощности излучателя придется подводить энергию с двух сторон. Проконтролировать качество шва будет весьма сложно.
При ультразвуковой сварке полимеров можно соединять детали, одна из которых практически не ограничена по величине. В зависимости от распределения энергии такая обработка делится на контактный и передаточный типы. Контактная обработка проводится прежде всего для эластичных конструкций сравнительно малой толщины.
Чаще всего соединения формируются методом «нахлеста». Передаточная методика сварки полимерных материалов предпочтительна главным образом для жестких веществ — в том числе и полиметилакрилата; ультразвуковое сваривание полипропилена и полиэтилена тоже вполне возможно.
Необходимое оборудование
Типичная сварочная машина ультразвукового типа включает:
источник высокочастотных колебаний;
специальный акустический узел;
специальный волновод;
механизм прессового типа;
системы контроля качества.
Стоит учесть, что все аппараты должны быть сделаны на заводе. Кустарно изготовить их нельзя — это потребовало бы слишком сложных математических расчетов и составления продуманных моделей. Достаточно совсем небольшого отклонения, чтобы в контактном месте появился резонанс. Рассчитывать на высокое качество сварных швов в таком случае невозможно. Контактные обрабатывающие системы чаще всего работают с материалами толщиной до 0,5 см. Швейная ультразвуковая машина предназначена для изготовления одноразовых изделий, в том числе и медицинского профиля. Такое оборудование подходит не только для простых полимеров, но и для:
волокнистых материалов;
брезентов полимерного состава;
иглопробивных изделий;
тканых материалов;
термически скрепленных геотекстилей;
различных пленок.
Системы УЗС также различают по методу движения волноводов (в прессовом варианте подразумевается короткое движение элементов, в непрерывном — свариваемый участок подвергается долгому воздействию). По тому, как дозируется прилагаемая механическая энергия, различают:
оборудование с фиксированным временем действия импульсов;
системы с зазором;
системы с осадкой.
Важно: для проверки качества УЗ шва может применяться все тот же высокочастотный излучатель. Но стоит понимать, что в норме само оборудование работает скрупулезно, все рассчитывается до мелочей. Если режим не соблюден, проверять не имеет смысла — качественного стыка все равно не выйдет. Это одинаково верно для:
стационарных станков;
настольных аппаратов;
ручных сваривающих систем.
Хороший станок — к примеру, SportTex EU 1300. Внешне его сложно отличить от простой швейной машинки. Устройство рассчитано на ток с характеристиками 220 В и 50 Гц, потому его можно спокойно применять в любом доме. Общая мощность составляет 1500 Вт, а одновременно обрабатываемая поверхность достигает 5 см. За минуту можно отработать до 10 м шва, при этом создается напор до 7 бар.
Испускаемый ультразвук имеет частоту не более 20 кГц. Линейные параметры устройства — 120х120х55 см. Его масса равна 110 кг. Из-за больших размеров и тяжести агрегат востребован главным образом в промышленных условиях. Платить за EU 1300 придется минимум 200 тысяч рублей.
Более компактны настольные аппараты, которые соединяют тубы для косметики, зубных паст, красок, клеев и так далее. Подобные устройства выполняют работу за 0,3 — 1,5 секунды. Точный показатель определяется шириной шва, которая иногда достигает 7 см. Прочие технические свойства у типичных настольных сварочных машинок:
испускаемые частоты до 35 кГц;
мощность до 1500 Вт;
привод на пневматической тяге;
масса до 30 кг.
Наиболее компактные аппараты предназначены для клепки пластмасс и прикрепления элементов к несущим конструкциям. Хорошим образцом таких изделий является Handy Star. По мощности, частотам импульсов и темпу работы это изделие почти не уступает настольным вариантам. Однако в пользу устройства говорят его сравнительно малые габариты (0,72 по сумме трех измерений) и легкость — 4,5 кг. С помощью Handy Star можно починить изделия из брезента, подготовить ленту для конвейерного транспортера; но допускает только соединение сухих деталей длиной максимум 0,25 м.
Стоит учесть, что ультразвуком варят еще и металлы, и для такой работы применяют оборудование с высокой частотой колебаний. Потому рекомендовано использование магнитострикционного эффекта, то есть перемена размеров отдельных веществ при колебаниях в магнитном поле. Преобразователи в современном ультразвуковом оборудовании часто делают из химически чистого никеля либо сплавов железа с кобальтом. Чтобы нарастить амплитуду смещения и концентрировать энергию, волноводы (концентраторы) обычно делают похожими на усеченный конус.
Регулируемые параметры
Мощность, выдаваемая преобразователем, определяется сообразно толщине и характеристикам свариваемых деталей. В типовом режиме она составляет от 4 до 6 кВт. Колебательная амплитуда чаще всего задается на уровне 10 — 20 мкм. От нее зависит характеристика соединения и степень его крепости. Внимание уделяют и сжимающему усилию.
От него зависит, как будет выдержан физический контакт между деталями. В норме такое усилие варьируется от 100 до 2000 кН. Трение при перемещении детали относительно другой поверхности определяется тем же сжимающим усилием. Наконец, нельзя игнорировать и продолжительность ультразвуковой сварки. Если время очень невелико, то прочность соединения окажется невелика, а при очень сильном затягивании процесса детали покрываются глубокими вмятинами, появляются усталостные разрушения.
Сварка ультразвуком неизбежно сопровождается выбросом тепла из-за контактного трения. Наибольший допустимый прогрев составляет 50 — 70% от температуры, при которой материалы плавятся. Иногда детали могут даже специально прогревать. Это позволяет работать быстрее и добиваться повышенной крепости. Но опять же чрезмерный нагрев будет противопоказан.
Технология
Типичный метод ультразвуковой сварки своими руками подразумевает сначала прикладывание статического давления, а затем уже применение ультразвуковых колебаний. Давление, приложенное до начала сеанса, останется неизменным на протяжении всего рабочего цикла. Убирать его надо через некоторое время, когда успеет сформироваться сварной стык. Материал шва охлаждают еще во время, когда он сжат. До окончания ручной операции подача сигналов производится в формате одного импульса, перерывы недопустимы.
Иногда ультразвук включают прежде, чем будет приложено давление. Такая процедура позволяет эффективно справляться с загрязнениями. Чтобы варить жесткие полимеры, после отключения звука наращивают давление на волновод; интервал времени такого воздействия строго ограничен. Критически важен контроль швов. Для этого применяют:
визуальную проверку;
капиллярный тест;
магнитную дефектоскопию (в случае со свариванием металлов).
В следующем видео показана ультразвуковая сварка многослойных изделий.