Особенности суппортов токарного станка
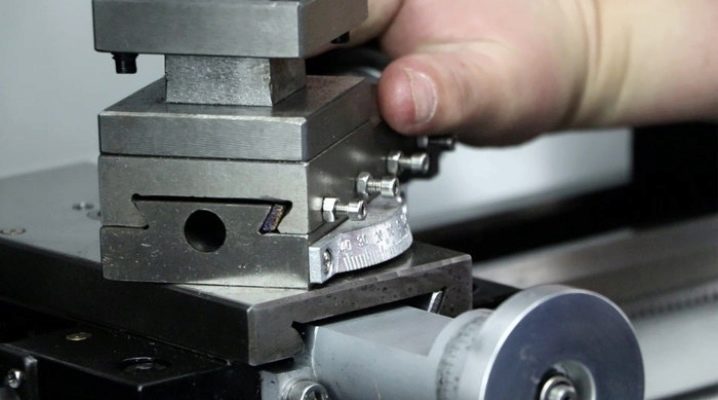
Особенности суппортов токарного станка должны быть изучены всеми, кто решает работать на таком оборудовании. Помимо назначения суппорта, стоит выяснить, кто первый его создал. Важно также узнать, из каких частей он состоит. Дополнительно понадобится разобраться с поперечными и продольными суппортами, с вертикальными и другими видами.
История создания
Развитие машиностроения сдерживалось долгое время не только отсутствием механического двигателя. Выдающимся успехом стало появление металлорежущего станка с суппортом, или иначе — держателем резца. Именно его изобретение легло в основу всех успехов токарного дела в XIX-XX столетиях, существенно удешевило технику и упростило работу с ней.
Прежде, еще с глубокой древности, токарные станки менялись очень мало, и резец всегда держал оператор.
В XVIII веке появились ранние копировальные аппараты с суппортами. Но это было уникальное оборудование, существовавшее в единственном экземпляре. Приобрести такую технику могли только особо обеспеченные люди. Первый создал практичный суппорт, применимый на массовом промышленном оборудовании, механик из Великобритании Генри Модсли. Это имя заслуживает не меньше почтения, чем Уатт или Фултон. Модсли заметно усовершенствовал более раннюю разработку того же рода, ставившуюся на токарный станок 1785 года.
Крестовой суппорт появился в середине 1790-х годов. Целью изобретения было повышение количества выпускаемых деталей, поскольку традиционная ручная техника достигла потолка своего развития. Более продвинутую конструкцию Модсли представил к 1798 году. Она позволяла уже делать винты значительной длины; важная особенность заключалась в неподвижности заготовки, по отношению к которой перемещался сам суппорт. Нельзя считать Г. Модсли единственным создателем держателя, но именно его разработка оказалась наиболее своевременна.
В 1800 году он представил еще более совершенный станок. Теперь стало возможно формировать резьбу с недостижимым прежде качеством и точностью. Концепция станка с суппортом оказалась настолько продуктивной, что была подхвачена другими изобретателями. Они в течение нескольких десятилетий использовали её в создании ряда типов машин, которые и сегодня встречаются на многих производствах. Так скромный вроде бы держатель оказался у истоков всей современной промышленности.
Принцип работы
Этот принцип как раз и состоит в точном передвижении фиксируемого режущего приспособления либо иного узла, используемого для обработки. В некоторых случаях фиксируется и заготовка. Основным импульсом является крутящий момент. Он отбирается от ходового винта, если надо сделать нарезы или произвести подачу в продольной плоскости.
Подавая режущий инструмент, отбирают энергию у специального вала.
Изредка в ход идет ручной привод. Его применяют, если как вал, так и винт задействовать непрактично. Речь идет о таких операциях, как:
- снятие фаски;
- торцевание;
- сверлильная обработка;
- отрезка приготавливаемой детали от более крупной заготовки.
Устройство и назначение
Роль суппорта токарного станка понятна уже по его названию, которое с латинского языка буквально переводится как «поддерживаю». Такое приспособление координирует действие режущего блока. Благодаря ему подача совершается на строго определенную величину, в рамках заданных допусков. Типичный суппорт состоит из частей различного типа:
- салазок (расположенных внизу у продольных и выставленных в поперечной плоскости у поперечных держателей);
- плиты, обеспечивающей поворот, на которую монтируют верхний тип инструмента;
- станочного фартука.
В продольном варианте салазки служат опорой и полем движения для всех прочих механизмов. Внутри фартучного узла скрываются приспособления, позволяющие передавать механический импульс. При работе перемещается весь агрегат в сборе. Поперечный тип подразумевает отбор механической энергии от винта каретки (хотя возможна и работа в ручном режиме).
Устройство предопределяет ход поворачиваемой плиты.
Вертикальный суппорт движется по направляющим, устанавливаемым на поперечный элемент. Конструкторы предусмотрели возможность его падения. Эта опасность устраняется благодаря планкам. Облегчение перемещения достигается за счет упора поперечными роликами, на которые ставят дополнительно пружины. Горизонтальное движение происходит благодаря ходовому винту и специальной гайке; обычно вертикальные суппорты могут еще и разворачиваться по отношению к салазкам.
Какими бывают?
О некоторых из видов суппортов уже сказано, но на этом останавливаться не стоит. Важную роль играет способ работы. Механический и автоматизированный аппарат хорошо подойдет для оснащения промышленных станков. Ручной держатель используют преимущественно в личных мастерских, где работа не предполагает серьезных усилий при управлении техникой.
Продольный суппортный узел обычно получает импульс от дискового кулачка посредством рычага. В нем также используется реечная пара и втулка для регулировки.
Кривошипный валик монтируется в корпусные подшипники. Поперечный суппорт может относиться и к горизонтальному, и к вертикальному типу; для приведения в движение используются кулачки, передающие импульс через комплекс рычагов с зубчатыми секторами и реечной системой. Верхние салазки могут встречаться в резцедержателях как обычных токарных, так и токарно-винторезных станков.
Регулировки
Нормальная работа оборудования возможна только при высокой точности его эксплуатации. В частности, направляющие держателей эффективно действуют лишь при определенном уровне зазора. Даже незначительные отклонения от этого показателя действуют пагубно. Если такая величина превышена, жесткость сопряжений утрачивается, растут ошибки. Для управления зазором используют винтовой зажим и фиксатор.
Иногда силы, которую дает фиксирующий узел, оказывается недостаточно. В этом случае есть риск фатальной деформации под действием осевой или приходящейся по радиусу нагрузки. Изнашиваются трущиеся части неоднородно, что не позволяет задать идентичные зазоры на каждой рабочей поверхности. Отмечается выраженная неравномерность износа также на приводных винтах.
Потому нормальный функциональный ход поддерживается за счет выставления каретки в точку с наименьшей степенью износа.
Если не регулировать суппорт, поддержать равномерное движение салазок не получится. Они станут локально заедать и прекратят покачиваться, когда к ним прилагают усилие сбоку. Проблема решается путем использования клиньев. Они принудительно ставят направляющие так, как положено, и убирают избыточный зазор. Те же клинья позволят поджать каретку к направляющим.
Очень важно контролировать люфт. Его появление в винтовой передаче недопустимо. Проблема решается за счет манипуляций с фиксирующей гайкой. При долгой эксплуатации токарного станка неизбежно засоряются и сальники каретки, что проявляется в образовании грязевых полос при сдвигах станины. Неполадка устраняется путем мытья войлочной набивки и пропитки ее маслом; при тотальном износе правильнее не возиться с этим, а заменить модуль на новый блок.