Все о выплавке стали
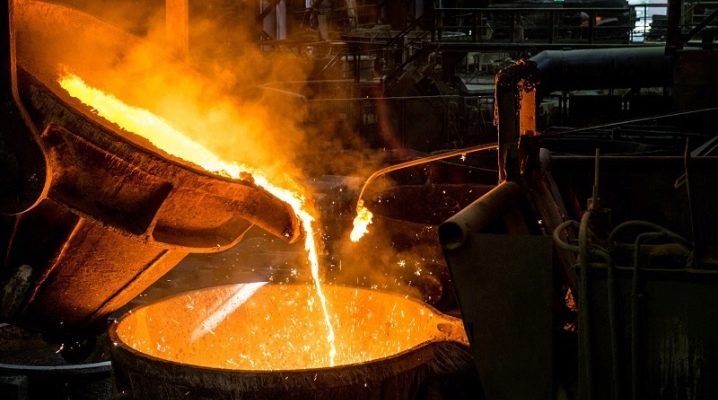
Знать все о выплавке стали, о способах ее получения необходимо даже просто для общего развития. Надо разобраться с описанием сырья, из чего ее выплавляют. Внимания заслуживает также процесс выплавки в электропечах (электродуговых) и в конвертере, другими способами.
История
Человеческая история — это не только и даже не столько войны, хитрые интриги придворных и чиновников, религиозные обряды и роскошные балы аристократии. Гораздо более важным измерением ее является повседневная практическая деятельность. И в том числе выплавка стали, которая сопровождала человечество с древности, а по ее развитию можно судить об уровне той или иной страны и в наши дни. Впервые сталь выплавили в I тысячелетии до нашей эры на территории современной Турции. Позднее эстафету подхватили на Балканах и в Центральной Европе, где между 900 и 400 годами до нашей эры впервые массово распространились железные мечи. Распространение самой плавки стали происходило стремительно. Очень скоро ею начали заниматься и в Китае, и в Юго-Восточной Азии. А в Африке обособленно ото всех начали производство металла с помощью цилиндрического горна, неизвестного в других регионах. В древние времена и в течение большей части Средневековья сталь плавили в сыродутных печах. Изобретенные в Индии еще до нашей эры штукофены распространялись не так уж быстро.
Так, в западноевропейских государствах они начали использоваться не раньше XIII-XIV столетия. Штукофенный процесс сразу дал ощутимый прирост производительности. Проблемой было то, что качественный металл таким образом получать не удавалось — единственный способ очистки от примесей (ковка), который был тогда доступен, не годился для этого продукта. Тем не менее именно усовершенствование штукофенов (создание блауофенов) позволило в конце Средневековья начать выпуск уже более близкой к современным образцам стали. В XV-XVI столетия европейская металлургия впервые вырывается на лидирующие позиции. Именно в ней освоили так называемый передельный процесс, и начали строить крупные доменные печи. Интенсивность насыщения углеродом была очень велика. Естественным ограничителем выступала только трудность получения древесного угля в необходимых количествах.
Вплоть до XVIII столетия использовать каменный уголь в плавке стали нигде не умели. И именно введение его в практику металлургии завершает примитивный этап ее развития и создает условия для внедрения более или менее современных методов.
Бурно растущая промышленность, появление железных дорог и пароходов были бы немыслимы без качественного рывка в черной металлургии. В 1864 году появляется мартеновская технология. Она позволяла получать много марок стали с недостижимым прежде качеством, что и дало возможность выпускать мощные станки, паровые двигатели, невообразимое прежде количество оружия. К середине ХХ века из мартеновских печей выходило не менее 50% всей стали, и не будет большим преувеличением сказать, что именно в них был «выплавлен» современный мир. Бессемеровский процесс, открытый на 8 лет раньше мартеновского, долгое время оставался в тени. Он не позволял получать столь же качественный металл.
Только в 1930-е годы начинается выпуск достаточных количеств чистого технического кислорода, и проходят первые эксперименты по его применению в массовой плавке. Правда, в условиях военного времени приоритет был отдан проверенным технологиям. И только с 1950-х годов кислородные конвертеры начинают вытеснять мартеновские печи. В те же 1930-е годы появляются впервые и достаточно мощные электростанции. Их создание позволило начать плавку металла электрическим током. Дуговые сталеплавильные печи оказались серьезным соперником кислородных конвертеров и не позволили тем занять весь пьедестал. Постепенно конвертерный и электродуговой процесс вытеснили мартеновскую методику практически полностью. Они существенно усовершенствованы и сами за последнее время.
Из чего выплавляют сталь?
Сырье для первичной плавки стали принято называть шихтой. Любой процесс обработки подразумевает раскисление и избавление от посторонних примесей, прежде всего фосфора и серы. Позднее в сплав добавляют улучшающие добавки, такие как:
- хром;
- ванадий;
- титан;
- марганец.
Изначально необходимо добыть железную руду. Даже мощным машинам тяжело разбить ее огромные участки на необходимые фрагменты. Потому дробление часто выполняют при помощи взрывчатки. Только выходящую на поверхность руду дробят механически, без взрывов. Иногда привезенную на металлургический завод руду дополнительно дробят и отделяют от пустой породы при помощи магнитной сепарации.
Среди горных пород, подходящих для переработки в сталь, выделяют:
- гематит;
- магнетит;
- сидерит (руда среднего качества);
- марказит.
Такие породы, как миспикель и леллингит, содержат незначительное количество железа. Их применяют только при отсутствии других, более подходящих, руд. Бедное металлургическое сырье используют только при концентрации железа не менее 26%, и его обязательно подвергают обогащению. Нет необходимости в обогатительном процессе только при концентрации железа минимум 57%. При этом дополнительно требуется, чтобы доля серы и фосфора была ниже 0,15%.
Освобождение от пустой породы достигается не только посредством магнитной сепарации. Для этой цели могут применять и агломерационную технологию. В таком случае подготовка подразумевает спекание руды. В ходе его сера и прочие примеси выгорают. Полуфабрикат дополнительно остужают водой и продувают воздушной струей.
Современная металлургия использует для выпуска стали руду с содержанием не менее 14-16% железа. Это очень внушительный результат, если учесть, что на технологиях XVIII столетия требовалась доля не ниже 65%. Кроме руды (шихты) сталь могут получать и из чугуна. Немалое количество ее сегодня получают за счет плавления вторичного сырья (металлолома). А также бывают нужны:
- ферросплавы;
- чугунный лом;
- флюсы.
Основные способы
Охарактеризовать виды процесса по получению стали необходимо более подробно. Начать стоит с плавки в конвертере. Самой первой стадией работы является продувка чугунной массы очищенным кислородом. Какого-либо топлива такой процесс не требует. Переработка 1000 кг чугуна до качественного стального сплава подразумевает зато расход 350 м3 воздуха. Аппарат может быть выполнен с верхним, нижним и комбинированным поступлением кислорода. Последний вариант отличается повышенной универсальностью. При окислении чугуна выделяется тепло. Это позволяет сократить количество примесей. Завершающим этапом оказывается раскисление.
Мартеновская технология предусматривает использование отражательных печей. Чтобы выплавить в них металл, необходима подача дополнительного тепла при помощи регенераторов. Тепловая энергия в них поступает за счет горения топлива в воздушной струе. Мартеновские методы подразумевают также окислительную атмосферу в печи. Это условие достигается завышением количества кислорода; время обработки в мартеновской печи составляет обычно 4-6 часов. Нижние насадки (регенераторы) работают при температуре от 1000 до 2000 градусов. Для их получения используют прочный шамотный кирпич.
Направления перехода потоков вещества периодически изменяются. Это достигается за счет перекидных клапанов. В современной металлургии их переключение автоматизировали. Отличные высококачественные стали получают в электропечах. В продвинутых электродуговых аппаратах может быть выработано 100 тонн металла и более. Ванна в таких устройствах имеет форму сферы. Электроды фиксируются в держащих приспособлениях, которые за счет особого механизма могут двигаться вверх и вниз.
В больших печах закладка шихты механизирована — поскольку делать это вручную и непроизводительно, и попросту опасно.
На окислительной фазе плавильного процесса сокращается количество фосфора. Одновременно уменьшается вхождение водорода и азота. Углерод тоже окисляется до необходимой степени. В ходе восстановительной обработки:
- металл раскисляется;
- сталь освобождается от серы;
- состав продукта доводят до заданных норм;
- исправляется температура.
Часть стали выплавляется в индукционных печах. Они делятся на работающие по кислому и основному процессам. Кислая методика позволяет исключить появление серного и фосфорного шлака. Однако окисление углерода в этом случае происходит не слишком эффективно. Его доля в шихте должна быть на 0,1% выше, чем в готовом сплаве.
Преимуществами индукционной плавки оказываются:
- малый угар металла;
- возможность работы в широком температурном диапазоне;
- возможность использования шихты в виде стружки (без дополнительного превращения в брикеты);
- равномерность температуры расплава и его состава во всем объеме печи;
- высокий уровень производительности;
- достаточное качество даже при перерывах в плавке;
- отсутствие громких звуков;
- экологичность процесса.