Особенности высокоуглеродистой стали
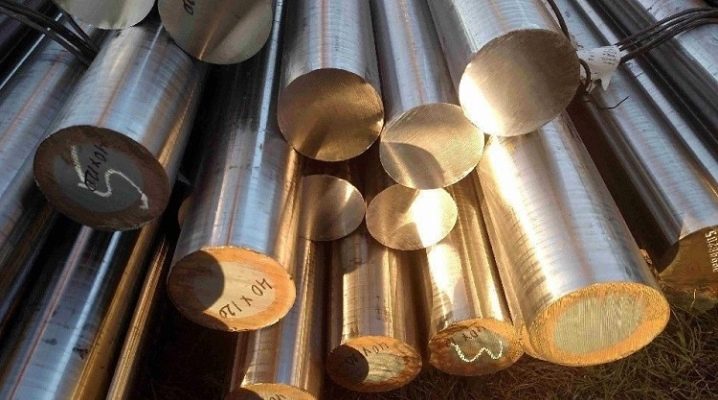
Высокоуглеродистая сталь широко востребована во многих сферах. Ее отличают неоспоримые преимущества перед другими сплавами. Тем не менее использование материалов подобной группы отнюдь не всегда допустимо, потому нужно хорошо разбираться в его основных физико-эксплуатационных характеристиках.
Что это такое?
Высокоуглеродистая сталь является сплавом железа и углерода, объём последнего в котором исключительно высок — от 0,6 до 2%. Для сравнения: в низкоуглеродистых составах этот параметр не поднимается выше 0,5-0,6%. С целью придания необходимых механических свойств подобная сталь в ходе производства проходит через термическую обработку. Это приводит к появлению растрескиваний и снижает прочность материала. Чтобы предотвратить подобное нежелательное явление и увеличить эффективность сварки, а также свести к минимуму риск образования закаленных зон, используется предварительный нагрев металлической детали до 200-250 градусов. После этого стальной сплав хорошо варится, и может создавать прочные соединения.
Производство стали нормируется ГОСТ 380-2005. В соответствии со стандартами качество сплава напрямую зависит от доли вредных примесей фосфора и серы. Чем меньше их содержится в сплаве, тем лучше качество материала. Зачастую для придания тех или иных эксплуатационных характеристик в состав вводят легирующие элементы. К примеру, присутствие марганца повышает степень прокаливаемости и улучшает прочностные характеристики материала.
Кроме того, этот компонент имеет свойство нивелировать нежелательное воздействие серы.
Характеристики и свойства
Параметры высокоуглеродистой стали обусловлены тем, что с возрастанием концентрации углерода увеличивается доля цементита, а объем феррита, наоборот, сокращается. В результате материал утрачивает свою ударную вязкость, становится малопластичным. Однако он в полной мере сохраняет свою высокую твёрдость и прочность. Выделяют ряд основных особенностей высокоуглеродистых составов. Процентное содержание микроэлементов: углерод (от 0,55 до 1,7%), марганец (от 0,3 до 0,9%). Малая вязкость становится причиной, по которой из стали этого типа не производят никакие конструкционные детали. Высокая стойкость к износу и повышенная прочность. Однако это правило верно только в том случае, когда на долю углерода приходится не более 0,8-0,9%.
Если содержание карбидов будет выше, то физико-технические характеристики начнут ухудшаться. Низкая подверженность сварке — в этом заключается основное различие высоко- и низкоуглеродистых сплавов. При повышенном температурном воздействии интенсивно выгорает углерод — это ведет к появлению закаленных сегментов, пор и растрескиваний в металле. Поэтому при работе необходимо производить предварительный прогрев рабочей зоны до 200-250 градусов. Материал практически не применяют в сложных сварных металлоконструкциях. Такой тип обработки целесообразен исключительно при проведении ремонтных работ.
При этом сплавы имеют довольно солидную себестоимость. Именно высокая цена существенно ограничивает сферу использования подобных металлов.
Марки
Высокоуглеродистый сплав маркируется при помощи буквенно-числовых обозначений. Первым символом является символ У — она означает углеродистую инструментальную сталь. После неё идёт цифра, указывающая на долю углерода. Так, маркировка У7 будет указывать на то, что перед вами сталь, содержание карбидов в которой составляет 0,65-0,74%. В сплаве У13 на его долю приходится 1,25-1,35%.
На особые функциональные характеристики сплава может указать присутствие марганца. В этом случае после числовых символов будет указана буква Г, к примеру, лист 65Г. Если маркировка включает букву Ш и Х (ШХ4, ШХ20, ШХ15СГ) — значит, в составе сплава имеется хром. Такой материал востребован при производстве подшипников. Если сталь относится к группе высококачественных, то после буквенно-числового обозначения указывается ещё одна буква А.
Применение
Сфера использования высокоуглеродистой стали напрямую зависит от марки сплава. В материалах У7 и У13 присутствует кремний в концентрации от 0,15 до 0,35%, а содержание серы не поднимается выше 0,03%. Такой материал используется для создания матриц с дальнейшей закалкой. Из сплава У8 и У10 производят магниты обыкновенного качества небольшого размера. Высокоуглеродистая сталь с маркировкой 55, 60 и 70 характеризуется повышенной прочностью, плотностью и жёсткостью. Такой материал применяют для производства валов прокатных станков, штоков, тросов, а также проволоки и прочих изделий, которые в ходе работы претерпевают существенные нагрузки.
Конструкционная углеродистая сталь 15, 35, 45 и 50 востребована при производстве деталей под цементацию. Это позволяет повысить параметры твердости, плотности, стойкости к износу. Её используют при создании осей, валов, зубчатых колёс, гаек, болтов и других элементов, которые испытывают значительное трение. Высокоуглеродистые стали нашли своё применение при изготовлении всевозможных металлических изделий в технике литья. Из них изготавливают проволоку, обрабатывают этот материал при помощи штамповки. Помимо этого, из высоколегированных сплавов создают стальную дробь, предназначенную для абразивной обработки материалов. Она может быть дробленой, колотой или рубленой. Высоколегированный состав востребован при создании пружин и напильников разных типов. Инструментальный сплав повсеместно используют при создании резцов, сверл, зенковок и других инструментов особой твёрдости для металлообработки.
Высокоуглеродистые составы актуальны при изготовлении бурильных, деревообрабатывающих и прочих инструментов, а также изделий, которые отличаются повышенной прочностью и не ржавеют. Если соединить нержавеющую высокоуглеродистую сталь с нержавейкой, то получится углеродистая нержавеющая сталь. Такой сплав будет брать самое лучшее от каждой своей составляющей. Подобные материалы характеризуются твёрдостью, устойчивостью к ржавчине и окрашиванию. Материал обладает четким краем при заточке, поэтому его часто используют для производства ножей.
Режущие основания из высокоуглеродистой нержавеющей стали долго сохраняют свою остроту, не темнеют со временем и не впитывают запахи от обрабатываемых продуктов.
Сварка
Повышенная концентрация углерода в высоколегированных сталях делает их непригодными для производства сварных металлоконструкций. Этот материал имеет ограниченное применение в силу низкой пластичности и слабой свариваемости. Тем не менее в ходе эксплуатации стальных изделий из высокоуглеродистой стали может возникнуть необходимость в проведении ремонтных работ. В этом случае нужно правильно подготовить материал — тщательно зачистить рабочую поверхность от ржавчины, механических неровностей, загрязнений любых типов и окалины. В противном случае в ходе сварки могут появиться поры. Конструкцию из высокоуглеродистого материала перед работой нужно нагреть до 400 градусов. Это позволит добиться оптимальных параметров прочности.
При сварке стали с высоким содержанием углерода можно использовать несколько техник. Оптимальным вариантом сварочного процесса считается дуговая ручная сварка при помощи электродов. Такая работа выполняется за счет тока обратной полярности. А за саму сварку отвечают специально разработанные для этого электроды, такие как НР-70. Сварка под флюсом — покрыть рабочую зону флюсом в ручном режиме довольно проблематично. Поэтому в подавляющем большинстве случаев для работы прибегают к автоматической технологии. Флюс расплавляют и покрывают поверхность трубы. Он формирует на стальном изделии плотную герметичную оболочку и тем самым предотвращает неблагоприятное воздействие внешних атмосферных факторов на сварочную ванну.
Для проведения сварки под флюсом применяют трансформаторы, которые беспрерывно выдают переменный ток. Эти аппараты создают между собой устойчивую дугу. Основное достоинство подобной техники — это минимальное разбрызгивание металла и, как следствие, снижение его потерь. Газовая сварка — этот метод для высоколегированных сплавов не рекомендован. В этом случае значительный объём углерода выгорает, на поверхности формируются закалочные участки и изменяется структура кристаллической решетки. Это самым неблагоприятным образом сказывается на прочности и качестве шва. Однако, если сваривание производят на рядовых конструкциях, то этот способ может быть результативным. В этом случае соединение производится на незначительном пламени с мощностью не более 900 кубометров ацетилена в час, при этом изделие следует прогреть до 300 градусов.