Особенности стали 5ХНМ
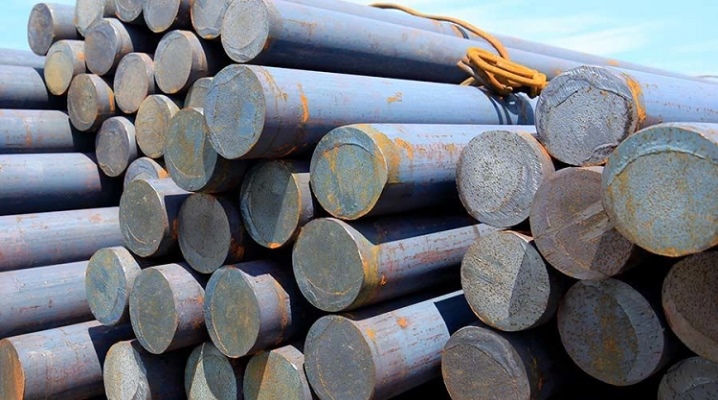
Особенности стали 5ХНМ могут оказаться весьма интересными для всех, кому нужно знать расшифровку названий металлов и их характеристики. Придется изучить особенности применения стали и ее термообработки, режимы закалки этой марки стали. Также надо обратить внимание на ее состав и уровень твердости.
Состав и расшифровка
Сталь 5ХНМ — довольно часто используемый металлургический продукт. Его принято относить к числу инструментальных штамповых сплавов. В химическом составе этой марки предсказуемо преобладает железо. Наряду с ним важную роль играют и другие элементы, оказывающие прямое воздействие на свойства готового продукта. Примерный состав таков:
- доля углерода колеблется от 0,5 до 0,6%;
- концентрация никеля – минимум 1,4, максимум 1,8%;
- молибдена в сплаве может быть от 0,15 до 0,3%;
- вхождение кремния должно быть не менее 0,1 и не выше 0,4%;
- доля марганца варьируется от 0,5 до 0,8%;
- присутствие серы более 0,03% не допускается;
- при производстве могут добавлять 0,5-0,8% хрома;
- допустимая концентрация меди – не выше 0,3%.
Расшифровать значение этой марки не так сложно. Цифра в начале условного обозначения говорит о присутствии не менее 0,5% углерода. Идущие за цифрой буквы соответствуют хрому, никелю и марганцу. Буквенное обозначение говорит и то, что их там не более 1,5%.
Потому вывод прост — это качественный легированный вид стали, а не отдельная категория сплавов.
Характеристики и свойства
Основные параметры стали 5ХНМ заданы по ГОСТ. Там внимание уделено не только механическим, но и термическим, и химическим моментам. Сразу стоит оговориться, что свариваемость крайне мала или вовсе отсутствует. Этот материал не допускается использовать в сварных конструкциях, так как сварка неэффективна либо дает плохой результат. Ковкость довольно высока. Начинают ковку при температуре 1240 градусов. Завершают ее при 750 градусах. Твердость этого сплава составляет 241 МПа. По другой шкале этот показатель равен НВ 10-1. Отмечается повышенная флокеночувствительность, а вот отпускная хрупкость не проявляется.
Возможности обработки 5ХНМ резанием довольно велики. Критические температурные позиции:
- Ac1 – 730;
- Ac3 (Acm) — 780;
- Ar3 (Arcm) — 640;
- Ar1 — 610.
Для такой стали характерны как солидная вязкость, так и хорошая прокаливаемость. Первое свойство обусловлено добавкой никеля, а второе связано с хромом и марганцем. Коэффициент линейного расширения при 200 и при 400 градусах составляет 12,6. Значение при 600 и 800 градусах достигает 14,2. Испытания различных свойств проводятся при температурах от 100 до 800 градусов, не более. Коэффициент теплопроводности для сплава 5ХНМ может составлять 46 Вт/ (м×°С). Но такой показатель достигается только при определенной температуре. В большинстве случаев он существенно меньше. В среднем плотность такого сплава равна 7800 кг на 1 куб. м.
С ростом температуры удельное электрическое сопротивление будет понижаться, и минимальное его значение равно 160 МОм×м.
Сортамент
Набор выпускаемой продукции строго задан по ГОСТ 1133, принятому в 1971 году. Предельное отклонение, в зависимости от позиции, может составлять:
- 2;
- 2,5;
- 3;
- 3,5;
- 4;
- 4,5;
- 5;
- 6;
- 7;
- 8 мм.
Если сечение круглого или сторона квадратного изделия составляют от 40 до 50 мм, погрешность свыше 2 мм не допускается. Для такого продукта установлены следующие обычные нормы: диаметр в поперечнике – от 12,57 до 19,64 кв. см, а тяжесть участка длиной 1 м — от 9,86 до 15,42 кг. В случае с квадратными заготовками сечение в поперечнике варьируется от 16 до 25 кв. см. Масса метрового участка составляет от 12,56 до 19,62 кг. Площади исчисляются по номинальным размерам, а плотность стального сплава принимается равной 0,00785 кг на 1 куб. см. Овальность, ромбичность и длина прутков также нормируются по стандарту.
Аналоги и заменители
В России вместо 5ХНМ можно использовать 5ХГМ либо ХНВ. Также допускается применение 4ХМФС, 5ХНВС, 4Х5В2ФС. За границей этому металлу соответствуют:
- 55NiCrMoV6 (согласно стандарту DIN) в Германии;
- 1.2711, 1.2713 — также в Германии;
- 55NCDV7 либо 55NiCrMoV7 – во Франции;
- в английской металлургии — BH224/5;
- по нормативам ЕС — 1.2714 или 55NiCrMoV7;
- в китайской сталелитейной отрасли — 5CrNiMo;
- в Японии – SKT3/SKT4;
- в американской практике – L6.
Применение
Принято считать, что 5ХНМ — штамповая полутеплостойкая продукция. Это один из самых распространенных в повседневной практике сплавов. Он выгоднее многих других деформируемых в горячем состоянии видов металлургической продукции. Добиться твердости на уровне 45 HRC можно при прогреве 350-375 градусов. При тех же условиях достигается предел текучести 1000 МПа. В основном сплав 5ХНМ приобретают для максимально больших горячих штампов, одна из сторон которых составляет 80-90 см. Также его используют и в тех молотовых штампах, которые подвергаются динамическому воздействию. Возможно и применение в выпуске контейнеров либо технических матриц. Очень важным нюансом является сохранение высокой вязкости в крупном сечении. Эта вязкость поддерживается и в продольной плоскости, и в поперечнике.
Присутствие молибдена дает возможность понизить чувствительность к хрупкости второго типа. Это обстоятельство очень важно при выпуске штампов, твердость которых варьируется от 40 до 60 единиц по шкале HRC. Такой металл можно использовать для штампов в молотовом исполнении, входящих в состав работающих на паровоздушной смеси или чисто пневматических молотов с тяжестью обрушиваемого блока не более 3000 кг. Дополнительно его заказывают для:
- штампов пресс-формата;
- оборудования высокоскоростной механической обработки цветного металла штамповкой;
- матричных элементов ковочных машин горизонтального типа;
- промышленных ножей для резки разогретого металла.
Термообработка
График термической обработки для каждой партии стальных сплавов составляется индивидуально. Учитывают химический состав вещества и его целевые практические характеристики. Большую роль при составлении графиков играет подбор оптимального характера мартенситных и аустенитных преобразований. Разработаны специфические режимы в зависимости от конкретной цели, которыми в первом приближении может воспользоваться любой технолог-термист. Важную роль играет предварительная термообработка с целью улучшения разрезаемости. В этом случае отжиг производится до температуры нагрева. Изотермическую выдержку ведут при 760-790 градусах. Гарантируется максимальная твердость по шкале HB от 197 до 241 единицы. В режиме смягчающего отпуска металл прогревают до 500-580 градусов. В этом случае уровень твердости будет колебаться от 325 до 446 единиц.
Иначе поступают, если требуется отжечь металл и подвергнуть его высокому отпуску. Подобный подход практикуется, когда делают штампы горячего деформирования. Отжиг производится так же, как и в предыдущем случае. Однако все меняется, когда наступает время высокого отпуска. При такой процедуре должна быть температура от 650 до 690 градусов, а достигаемая твердость ограничена 241 единицей. Интересны и режимы финишной термообработки частей штампов. В этом случае обязательно практикуется закалка при 600-650 градусах. Наибольшая достигаемая температура — в диапазоне от 830 до 860 градусов. Первоначальной стадией остужения оказывается погружение в масло. На этой стадии сталь 5ХНМ должна остыть до 200-230 градусов.
Дальнейшее снижение температуры должно происходить в воздушной среде. Итоговая твердость по HRC – от 56 до 60 единиц. Такой небольшой разброс позволяет гарантировать предсказуемые свойства готового продукта. Во время отпуска металл нагревается до 380-420 градусов. Величина отпечатка может составлять от 0,27 до 0,285 см; твердость по HB равна 461-514, а по HRC 48-52. Иногда штампы из 5ХНМ приходится азотировать. Лучшей операционной средой для такой манипуляции считают аммиак. Оптимальная температура азотирования – не ниже 480 и не выше 500 градусов. Длится обработка от 25 часов, иногда занимает вдвое больше времени. Диффузия происходит на глубину 0,02-0,04 см; при этом обязательно нормирована и микротвердость. В некоторых случаях инструмент на основе этого сплава цианируют. Длительность подобной обработки не превышает 120 минут. Ведется она при 560 градусах. Слой диффузии составляет 0,02-0,025 см. Окончательная микротвердость также нормирована.