Все о стали ХВ5
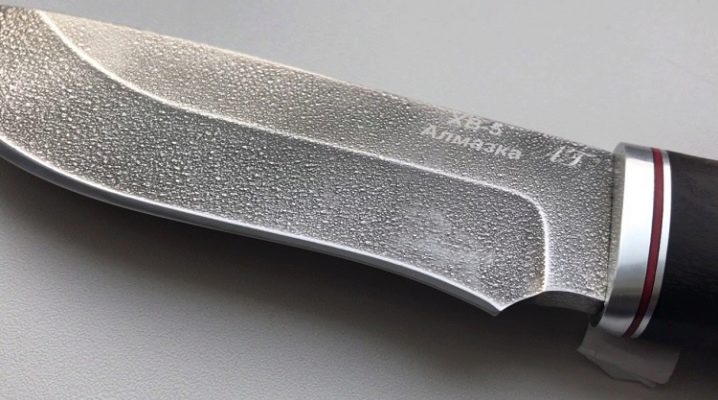
Всем известно о свойствах алмаза, но далеко не все наслышаны о существовании алмазной стали. Так называют сплав ХВ5 — он востребован при изготовлении клинков исключительной прочности. Эти ножи пользуются высоким спросом, именно поэтому об особенностях такого материала стоит узнать подробнее.
Состав и расшифровка
Список ножевых сталей включает свыше десятка позиций. При этом далеко не каждая может применяться для изготовления и бытовых, и охотничьих, и рыболовных ножей. Однако инструментальная сталь марки ХВ5 относится к категории универсальных. Из неё создают ножи, а также штампы, резцы и сверла. Главным преимуществом такого материала является его стойкость к износу. Этот сплав известен давно. Во времена СССР его использовали для производства инструментов, предназначенных для огранки драгоценных алмазов. Это и неудивительно, поскольку по шкале твёрдости Мооса он занимает место рядом с этим камнем — 9,5 баллов против 10.
Впервые такая сталь была получена в Японии. О ее производстве стало известно почти два века назад. В 1825 году в популярном «Горном журнале» вышла статья, в которой подробно описывалась технология создания материала.
Конечно, маркировки ХВ5 на тот момент не существовало, поскольку аббревиатура «ХВ» означает «хромовольфрамовая», а вольфрам в то время ещё не был известен. Вместо него в сплав добавляли платину.
Расшифровка маркировки указывает на следующие характеристики состава:
- Х – наличие в составе стали хрома;
- В – наличие в составе стали вольфрама;
- 5 – доля вольфрама, 5%.
Сплав содержит высокую концентрацию углерода — 1,5%. Также в нем содержатся легирующие примеси, которые оказывают положительное воздействие на технико-эксплуатационные свойства материала. Добавление хрома и вольфрама в тандеме с другими компонентами обеспечивает повышение параметров пластичности и ударной вязкости, при этом без ущерба для прочностных показателей.
Хром отвечает за стойкость к окислению и, соответственно, снижает коррозию. Однако его процентное содержание в этом сплаве невелико — всего 0,5-0,7%. Этой дозировки недостаточно, чтобы обеспечивать высокую устойчивость к ржавчине. Поэтому поверхность металлов при продолжительном контакте с влагой может подвергаться коррозийным процессам. На долю вольфрама приходится 4,5-5%. Этот элемент отвечает за повышение прочностных параметров при термическом воздействии свыше 200-250 градусов. Присутствие вольфрама способствует образованию высокопрочных карбидов, проявляющих стойкость к любым колебаниям рабочей среды. В незначительных концентрациях в сплаве присутствуют марганец и кремний. Их содержание не превышает 0,3-0,4% в равных объемах. Это полезные примеси, которые связывают свободный кислород и препятствуют активному окислению.
Плюсы и минусы
Сталь марки ХВ5 практически недоступна для деформации. Её отличает повышенная теплостойкость. Именно поэтому из материала чаще всего делают резьбовой инструмент, а также тонкостенные изделия с завышенными требованиями по части твёрдости и стойкости к износу.
К основным достоинствам алмазной стали относят:
- прочность;
- упругость;
- высокую технологичность;
- хорошую прокаливаемость;
- легкость штамповки и резки;
- обрабатываемость;
- возможность применения для серийного производства;
- доступную цену.
В то же время при механической обработке такой стали на её поверхности могут появляться прожоги и растрескивания. В сочетании с низкой стойкостью к окислению это ограничивает сферу ее применения. Такие ножи нежелательно использовать как рыболовную и охотничью оснастку.
Из других минусов можно обозначить:
- недопустимость любых касательных напряжений в металле;
- трудоемкость заточки, необходимость использования специализированных инструментов и станков.
Характеристики
Эксплуатационные параметры алмазной стали напрямую зависят от её физико-химического состава, структуры и типа взаимодействия отдельных компонентов друг с другом. Так, наличие углерода в структуре вызывает синтез карбида. Эти соединения считаются базовыми для определения рабочих параметров алмазного сплава в процессе термообработки. При этом важную роль играют их конфигурация, величина и месторасположение. В качестве легирующего компонента вводится хром. В стальном сплаве ему отведена роль уплотнителя кристаллической решетки. Он отвечает за её стабилизацию и позволяет карбидам принимать такой же размер, как и атом. В концентрации ниже 10,5% улучшает прокаливаемость.
Ещё одним важным легирующим элементом является вольфрам. Он обеспечивает повышенную прочность сплавов при прогреве до 250 градусов и больше. Оказавшись в сплаве, вольфрам также формирует карбиды, которые более крепки и устойчивы к внешним факторам, нежели карбид железа. Температура плавления подобных карбидов превышает 3000 градусов, поэтому получить их можно только путем запуска сложных химических взаимодействий и дальнейшего дробления. Кстати, этот способ начали использовать еще в XIX столетии.
Молибден в качестве дополнительного компонента увеличивает толщину закаливаемого материала и параллельно вызывает уменьшение величины зерен. Снижение размера зерновой структуры обуславливает повышение пластичности с сохранением твёрдости, а еще обеспечивает высокую обрабатываемость. Карбидные соединения молибдена отличаются повышенной прочностью и многократно повышают тугоплавкость расплава. Кремний и марганец вводят для стабилизации состояния металла. Все это в целом способствует улучшению качественного состава металла.
Подобная структура обеспечивает следующие технико-физические характеристики стали марки ХВ5:
- вязкостный параметр — 455 кДж/кв. м;
- свариваемость металла – без ограничений;
- твёрдость по Роквеллу — 62-65, отдельные изготовители доводят данный параметр до 69-70 единиц;
- плотность — 7940 кг/м3;
- температура плавления — 1390 градусов.
Сталь ХВ5 востребована преимущественно при изготовлении режущего материала. Аналогичными свойствами обладают следующие импортные сплавы:
- N690 (Швеция);
- X105CrCoMo18-2 (Германия);
- ZA-18 и VG-10 (Япония).
Кстати, последний вид металла используется исключительно для производства ножей. Его состав и структура разрабатывались специально под выпуск холодного оружия.
Обращаем внимание на то, что эти виды стали обладают схожими характеристиками, но их состав, структура и, конечно же, цена не являются идентичными.
Применение
Стоимость ножей из алмазной стали составляет несколько тысяч рублей. Конечно, это высокая цена, но она в полной мере обусловлена исключительным качеством изделий. Главным плюсом таких ножей можно назвать продолжительный эксплуатационный ресурс: пользователь может не переживать, что нож сломается и затупится вскоре после покупки. Его изготавливают из чрезвычайно прочного и износостойкого материала, поэтому он будет служить верой и правдой много лет. Если говорить о ноже, как об инструменте для резки, то алмазная сталь подходит для этих операций как нельзя лучше: её отличает максимальный параметр прочности. Под эти требования попадают разновидности ножей, используемые для работы с дублеными шкурами и прочими скорняжными материалами с аналогичной жесткостью и текстурой. Такие ножи востребованы в меховом и сапожном деле. Ими допускается стругать древесину, но ни в коем случае не рубить.
Ножи с длиной клинка в 15-30 см часто используют в мясных цехах для обработки туш. Если использовать более мягкие лезвия, то придется править их после обработки каждой единицы продукции. При соблюдении номинальных стандартов заточки ножи из алмазного сплава сохранят функциональность на несколько лет. Ножи из стали ХВ5 подвержены гравировке. Именно поэтому их часто украшают высококачественными рукоятями из древесины дорогих сортов. Такие изделия популярны в качестве подарка, они вызывают интерес у коллекционеров. Будьте уверены — клинок из алмазной стали, украшенный гравировкой, непременно станет центром коллекции холодного оружия.
Однако у этого сплава имеются и недостатки. В первую очередь, это трудоемкость обработки лезвия. Присутствия вольфрама наделяет сталь исключительной твердостью. Чтобы наточить такой нож, приходится прилагать значительные физические усилия и даже использовать специализированные инструменты.
К тому же ХВ5 не годится для применения в походных условиях, поскольку в случае динамических нагрузок может сослужить своим владельцам плохую службу.
Таким ножом нельзя выполнять рубку, наносить удары по глине, металлу и другим твердым материалам. Не допускается его использование в качестве рычага для открытия консервных банок и других ёмкостей. При сильной динамической нагрузке клинок изгибается, ощущается повышение упругости. Но пользователь обычно не может поймать ту грань, при которой происходит внезапное разрушение материала. В таких случаях на кончике ножа или режущей кромки образуются изломы. Что касается стойкости к коррозийным процессам, то этот сплав не обладает данным свойством в полном объёме, поскольку материал ржавеет. При отсутствии частого контакта с водой нож будет сохраняться длительное время. Однако продукты после резки приобретают малоприятный привкус железа. А при реакции с кислотами, в том числе растительного происхождения, на лезвии возникает заметная ржавчина.
Поэтому использовать подобные ножи туристам, а также рыболовам и охотникам не просто нежелательно, но и крайне опасно. У них всегда имеется риск остаться без инструмента в лесу, тайге или какой-либо экстремальной ситуации, к примеру, при необходимости быстро обрезать верёвку, при нападении хищного зверя или других неприятных неожиданностях. К тому же такие ножи вне дома трудно заточить, даже имея в своём арсенале шлифмашинку. ХВ5 сталь с течением времени набирает прочность, что приводит к растрескиванию даже при легких ударах. А применение при температурах менее -25 градусов ситуация только усугубляется. Поэтому такой вариант предпочтителен для домашнего использования, но никак не полевых условий. Небольшой лайфхак: чтобы свести к минимуму риск появления коррозии на лезвии из алмазной стали, периодически нужно натирать его животным жиром.
Обработка и заточка
Механическая и термическая обработка ножей из алмазных сплавов производится в строгой последовательности. Тем самым обеспечивается повышение её технических и эксплуатационных свойств.
- Ковка при нагреве в 1100-870 градусов.
- Отжиг при нагреве до 800-600 градусов на протяжении 4 часов. Это размягчает алмазную сталь и обеспечивает высокую скорость выполнения механической обработки. Такой вариант температурного воздействия часто используют при организации предварительной холодной прокатки.
- Закалка при 800 градусах с дальнейшим охлаждением в масляной ванне до 250, а затем на открытом воздухе.
- Отпуск для снятия накопившихся внутренних напряжений выполняется при 180 градусах с дальнейшим охлаждением на свежем воздухе.
Обычно закалка выполняется сразу же после проведения механической обработки, не предусматривающей шлифования. При этом производится нагрев до 830 градусов и последующее охлаждение. Подобная обработка обеспечивает плавный переход металла в мягкий, но при этом прочный мартенсит. В ходе отпуска запускается коагуляция мартенсита с образованием сорбита и троостита.
Если точно выдерживать рекомендованную технологию термоупрочнения стали марки ХВ5, ножи и лезвия нее будут исключительно прочными и практичными. Именно поэтому любителей ценных подарков и коллекционных экземпляров вряд ли испугает стоимость в 300 долларов и более.