Описание рельсовых сталей
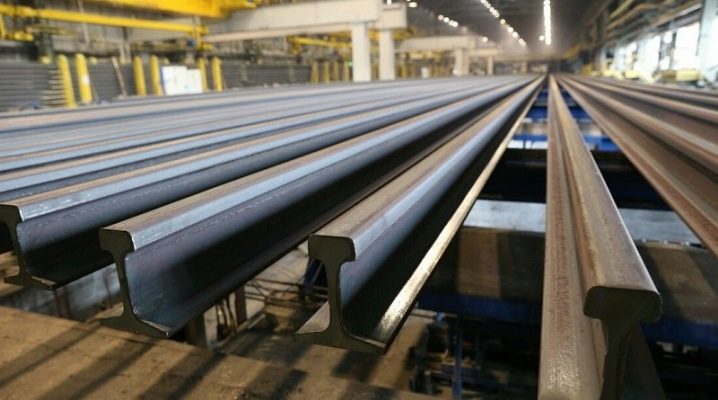
Описание рельсовых сталей и их марок весьма поучительно не только для людей, интересующихся рельсовым транспортом, но и для торгующих металлургической продукцией либо производящих ее. Важно разобраться, из каких сталей делают железнодорожные рельсы Р65 и Р43.
Также весьма актуальны характеристики и состав, коэффициент температурного расширения и другие практические параметры.
Состав
Железнодорожные пути существенно изменились по сравнению с теми, что были даже 50 лет назад, не говоря уже о вековой давности. Заметно выросли и скорость движения поездов, и нагрузка от них. Потому и к рельсовой стали на ЖД предъявляют куда более высокие требования. Необходимые параметры выдерживаются во многом благодаря тщательно подобранному химическому составу. Надо понимать, что рельсовый сплав — это не одна сталь, а целая группа, и их изготовление проводится различными путями. В любом случае фазовая структура вещества основана на перлите с мелкоигольчатым строением.
Производство этого материала для путевого хозяйства делится на 2 варианта сообразно применяемому металлургами раскислителю. Один вариант — использование ферромарганца либо ферросилиция. Но иногда необходимый продукт изготавливают при помощи алюминиевых окислителей. Именно сталь такого типа берут гораздо охотнее. Она ценится за меньшее количество неметаллических веществ в составе.
Как бы то ни было, рельсы должны полностью отвечать положениям ГОСТ 2013 года. Важно понимать, что конкретно делают добавки того или иного вещества. Базовым компонентом без всяких колебаний стоит назвать углерод. В составе рельсовых сталей его доля варьируется от 0,71 до 0,82%. Этот элемент связывает железные молекулы и повышает общую прочность. Мало того, в присутствии углерода металл при повышенной температуре становится крепче.
Доля марганца варьируется в гораздо более широких пределах – от 0,25 до 1,05%. Его задача — улучшить ударную вязкость (она может быть повышена на 20 или даже на 30%). За счет марганца растут также твердость и сопротивляемость износу. Но преимущество его перед углеродом состоит в том, что этот эффект достигается без потери пластических качеств. А подобное обстоятельство крайне важно именно для путевого хозяйства. Концентрация кремния варьируется от 0,18 до 0,4%. При реакциях с ним устраняется кислород, что позволяет оптимизировать кристаллическую решетку.
Введение кремния позволяет сократить химическую неоднородность разных участков рельса. В итоге срок эксплуатации магистрали повышается как минимум на 30%. Доля ванадия невелика — от 0,08 до 0,012%. Но все же этот компонент весьма важен — он позволяет добиться контактной прочности изделия. Ванадий немедленно вступает в реакцию с углеродом и образует с ним прочную химическую связь (профессионалы выделяют различные карбиды ванадия). Классификация этих карбидов — целая отдельная тема. Куда важнее то, что они обеспечивают оптимальные показатели износостойкости и плотности. Как следствие, минимальная выносливость сплава возрастает. В составе рельсовых сталей иногда присутствует 0,03 — 0,07% азота. Это уже не сознательно вводимый компонент, а вредная примесь.
В присутствии азота ванадий не может качественно легировать сталь. Вместо этого образуются вещества с низкими механическими свойствами. Термическое упрочнение оказывается невозможно. Фосфора в составе рельсовой стали может быть не более 0,035%. Этот неметалл понижает хрупкость готового изделия, что грозит растрескиванием и даже последующим разрушением рельсовых путей. Концентрация серы не может превышать 0,045%. Ее присутствие грозит падением технологических характеристик материала. При горячей обработке сернистой стали она оказывается неподатлива, растет и опасность появления трещин.
Почти все рельсы такого происхождения бракуются при сколько-либо тщательном техническом контроле. На самые загруженные пути отпускают рельсы с наименьшей концентрацией фосфора и серы.
Основные свойства
Среди ключевых характеристик марок стали для железной дороги обязательно стоит назвать особенную стойкость к циклически прилагаемым нагрузкам. Абсолютный предел прочности у разных типов металла варьируется от 800 МПа до 1 ГПа. Но первые признаки разрушения материала обнаруживаются уже в диапазоне от 600 до 810 МПа. Конкретные показатели зависят от вводимых улучшающих добавок и усталости конкретного образца. Структура рельсового сплава идеально отвечает требованиям защиты от ударных нагрузок. Вязкость при соударении с другими телами будет равна 2,5 кг на 1 кв. см. Показатель твердости по Роквеллу в значительной мере зависит от уровня термообработки. Если выполнить объемную закалку как следует, можно поднять этот показатель до 60 базовых единиц.
Длина железнодорожных путей достигает десятков и даже сотен километров. Потому особое значение для их использования приобретает коэффициент температурного расширения. У качественного продукта, соответствующего нормам ГОСТ, такой показатель принимается равным 0,00001118. В отношении материала могут действовать разные стандарты, выбираемые с учетом химического состава сплава.
При разборе механических свойств надо обязательно упомянуть умеренную пластичность.
Так как относительное сужение металла не превышает 1/4, вполне можно прокатывать разогретые рельсы. Температура обработки (отправки на прокатный стан) составляет от 900 до 1000 градусов. Модуль упругости качественного изделия принимается равным 210 ГПА. Нормируются также:
- временное сопротивление;
- предел по текучести;
- удлинение и сокращение длины в относительном исчислении.
Все эти свойства определяются целевой категорией рельсов. В основном ключевые параметры задаются ГОСТ 2013 года. В 2020-м началось обсуждение проекта более продвинутого стандарта. Он позволит применять металлы ряда новых марок и улучшить качество продукции. Однако перспективы введения актуальной редакции документа пока туманны. Единого ответа на вопрос о температуре плавления железнодорожных рельсов нет. Имеет значение химический состав конкретного сплава. Это обстоятельство придется учитывать не только металлургам, но и тем, кто собирается выполнять сварку. Уровень свариваемости зависит уже не только от металла. Его определяют с учетом применяемых электродов.
Стыки высокоуглеродистых конструкций (а именно таковы рельсы) при превышении допустимой температуры накапливают избыточные напряжения внутри. Это со временем может привести к образованию трещин и иных деформаций, способных даже привести к аварии. Нормальная сварка выполнима лишь на качественном оборудовании с использованием флюсов. После завершения сварочных работ шов должен быть дополнительно обработан.
Группы
Речь идет о градации рельсового металла по способам получения и применяемому исходному сырью. Первая категория вырабатывается из спокойной стали, обрабатываемой внутри ковша комплексными раскислителями. Такие составы не содержат алюминия либо иных веществ, провоцирующих появление опасных включений. Вторая категория продуктов также представляет собой заготовки из спокойной стали. Она раскисляется алюминием либо сплавом алюминия с марганцем.
Дополнительно стоит упомянуть деление на сорта. В первый сорт записывают лишь то, что полностью отвечает технологическим нормативам. При незначительных отклонениях с химической и физической точек зрения продукт относят ко второму сорту. Необходимо учитывать также повышенные требования к рельсовому материалу, используемому к востоку от Урала. Там допускается применять только первоклассный объемно-закаливаемый металл, в состав которого входят ниобий, ванадий и бор; улучшение свойств (легирование) производится при помощи азотированных ферросплавов.
Если сталь плавили в электрических печах, то даже при температуре ниже — 60 градусов она будет иметь вдвое большую ударную стойкость, чем полученная мартеновским способом. Маркировка продукции очень важна для правильной отгрузки. В ходе обработки на прокатном стане металл получает основную маркировку. Ее наносят посредством клеймения. Дополнительные обозначения создаются при помощи краски.
Эти виды обозначений показывают, соответственно, исполняемые стандарты и специфику каждого отдельного рельса.
Марки и их применение
Наиболее часто на отечественных железных дорогах используется рельс из сплава 76. На его основе делают профильную продукцию из линейки Р50 и для рельсов Р65. На эти две категории приходится не менее 75% всех опор ширококолейных магистралей. Довольно частым вариантом сейчас выступает и сплав 76Ф. Это улучшенный вариант, который за счет ванадия приобрел увеличенный ресурс.
Именно прокат 76Ф оптимален для высокоскоростных и тяжелогруженых поездов. Рельсы с маркировкой Р43 в основном делают из СТ76. Иногда в ход идут улучшенные сплавы 76Ф и 76Ц. Продукция категории К63 легируется никелем в количестве до 0,3%. Такой материал тверд и стоек к коррозии, позволяет создавать крановые рельсы.
Также могут использоваться:
- К63Ф (включающий вольфрам);
- М54 (материал, улучшенный марганцем и отличающийся превосходной вязкостью);
- М68 (марка, подходящая для отдельных конструкций верхнего строения пути).
Обработка
Термическая закалка — не единственный возможный вариант. Для улучшения продукта применяют:
- изотермический режим охлаждения;
- закаливание по краям через подачу высокочастотного тока;
- нормализацию;
- закаливание за счет нагрева при прокатке.
Именно применение некоторой части тепла прокатного подогрева считается наиболее перспективным решением. Прокатанный металл сразу прогревают в индукторе. После этого его форсированно остужают. Следующей стадией работы оказывается самоотпуск на охладительном элементе. Объемная закалка рельсовой продукции в масле, применяемая еще на ряде предприятий, имеет серьезные недочеты:
- большие затраты времени;
- токсичность процесса;
- расходование дорогого масла;
- недостижимость дифференцированной твердости.