Особенности стали 65Г
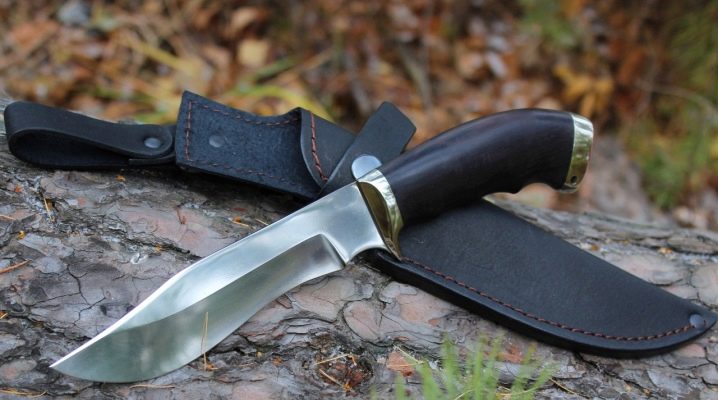
Сталь 65Г – одна из самых востребованных российских марок рессорно-пружинной стали, которая подходит как для создания ответственных промышленных деталей, так и для изготовления холодного оружия. Из этого обзора вы узнаете ее основные характеристики и особенности обработки.
Состав и расшифровка
Этот сплав – специальная конструкционная низколегированная высокоуглеродная сталь, которая относится к семейству рессорно-пружинных. Ее характеристики определяет ГОСТ 14959-2016.
Символы обозначения несут для специалиста информацию о типе, составе и ключевых свойствах материала. Их расшифровка следующая.
-
Маркировка начинается с цифрового индекса, что указывает на принадлежность к категории конструкционных сталей. Сам индекс соответствует доле углерода в сплаве в долях процента. То есть в данном случае цифра «65» говорит о том, что углерода в марке содержится от 0,65%. Точные рамки для элемента задает ГОСТ: не менее 0,65%, но не более 0,70%.
-
Символ «Г» в обозначении качественных конструкционных сталей сообщает о повышенном содержании марганца по сравнению с типовым: стандартно такие сплавы содержат до 0,80% этого элемента, тогда как маркируемые буквой «Г» – от 0,80% до 1,2%. Для сплава 65Г установленный нормативом диапазон: от 0,9% до 1,2%. Введение в состав марганца в такой пропорции позволяет повысить (по сравнению с нелегированными углеродистыми сталями) важнейшие для пружинного сплава характеристики – твердость, упругость, вязкость, улучшить прокаливаемость.
Кроме главной добавки – марганца – в состав стали 65Г входят и другие компоненты. Они выступают в качестве дополнительных и содержатся в небольшом количестве (суммарно не более 2,5%), поэтому в маркировке их не перечисляют.
Но без них сплав не обретет нужные свойства. Точный химический состав сплава 65Г регламентирован ГОСТом, он следующий:
-
железо (Fe) – около 97%;
-
углерод (C) – 0,65-0,7%;
-
марганец (Mn) – 0,9-1,2%;
-
кремний (Si) – 0,17-0,37%;
-
никель (Ni) – до 0,25%;
-
хром (Cr) – до 0,25%;
-
медь (Cu) – до 0,2%;
-
сера (S) – не более 0,035%;
-
фосфор (P) – не более 0,035%.
Плюсы и минусы
Сплав 65Г является пружинным, то есть предназначен для производства элементов с повышенной упругостью (пружин, рессор) и работы в таких условиях, для которых большинство других сталей являются слишком жесткими: переменные, повторяющиеся нагрузки, многократные циклы сжатия-растяжения, изгибы, трение. Поэтому от обычных углеродных сталей этот материал отличается рядом свойств:
-
высокий для стали предел упругости и текучести;
-
хорошая для своего класса поверхностная твердость;
-
пластичность;
-
высокая вязкость;
-
релаксационная стойкость;
-
устойчивость к хрупкому разрушению;
-
стойкость к истиранию;
-
однородность структуры;
-
хорошая для низколегированных сталей коррозионная стойкость;
-
хорошая ковкость;
-
сравнительно невысокая стоимость производства в сравнении со сложнолегированными сталями.
Благодаря такому соотношению характеристик сталь 65Г отлично подходит для создания ответственных упругих деталей (например, рессор заднего моста грузовых автомобилей, промышленных пружин), а также холодного оружия: она упругая, твердая, с хорошей ковкостью и возможностью получения острой режущей кромки, которая долго не тупится.
При выборе следует учитывать, что сталь 65Г:
-
не предназначена для сварных конструкций, трудно режется (как все рессорно-пружинные стали);
-
имеет более низкую ударную стойкость, чем многие другие пружинные стали;
-
по коррозионной стойкости хороша для своей группы, но существенно уступает нержавеющим сталям.
Поэтому сплав 65Г не подходит для производства элементов двигателей, испытывающих ударные нагрузки или трубопроводов для агрессивных сред, жестких промышленных конструкций. А также, хотя эта марка хороша для создания холодного оружия, для медицинских изделий и кухонных ножей ее коррозионная стойкость недостаточна.
Но то, что материал имеет ограниченную область применения, это не его недостатки или достоинства, а нюансы, которые должен знать технолог, выбирая материал для конкретного изделия и условий эксплуатации (ведь универсальных сталей не существует).
Характеристики и свойства
Для правильного выбора материала и расчета конструкций, изделий необходимо знать точные физические, механические, технологические характеристики сплава. Приведем ключевые характеристики, которыми по ГОСТу должна обладать сталь 65Г.
Механические свойства
При 20 градусах Цельсия сталь 65Г обладает такими механическими свойствами:
-
твердость в термообработанном состоянии (способность не разрушаться при воздействии твердых тел) по Бринеллю (HB) – 241, по Роквеллу (HRC) – 40-50 единиц;
-
модуль нормальной упругости – 215 ГПа;
-
предел текучести – 850-1790 МПа;
-
максимальная прочность на растяжение – 700 МПа;
-
максимальная прочность на кручение – 400 МПа;
-
сопротивление разрыву – 880-2200 МПа;
-
ударная вязкость 5-76 Дж/см2.
Физические свойства
Физические свойства при 20 градусах Цельсия:
-
плотность – 7850 кг/м3;
-
удельная теплоемкость – 490 Дж/ (кг*К);
-
теплопроводность – 37 Вт/ (м*К);
-
примерное удлинение при отрыве – 8%;
-
относительное сужение – 30%.
Сталь 65Г также отличается определенными технологическими свойствами.
-
Свариваемость. Как и все пружинные стали, сплав 65Г не предназначен для сварных конструкций (из-за особенностей своей поверхности, которые приобретает при термообработке), но допускает контактную сварку без ограничений.
-
Отличается хорошей ковкостью.
-
Доступна всем видам резки. Разумеется, твердая и упругая высокоуглеродистая сталь режется несколько сложнее, чем низкоуглеродистая (коэффициент обрабатываемости резанием составляет 0,80-0,85 в закаленном и отпущенном состоянии).
-
Мало подвержена возникновению флокенов (опасных внутренних дефектов в виде транскристаллитных трещин со светлыми краями).
-
Имеет хорошую прокаливаемость (благодаря марганцу).
-
Может быть склонна к отпускной хрупкости при содержании марганца менее 1%.
-
Изделия из этой стали предназначены для эксплуатации при температурах от -50 до 200 градусов Цельсия, без постоянного контакта с водой и агрессивными веществами.
Аналоги
Для большинства задач допускается заменять сталь 65Г близкими по свойствам аналогами. Среди российских марок такими могут являться:
-
55С;
-
60Г;
-
60С2;
-
70Г;
-
65ГА;
-
9ХС.
В других странах существуют свои стандарты сталей, среди которых также можно найти довольно близкие по свойствам к 65Г марки. Например:
-
США (стандарт AISI) – 1566, 1066;
-
Германия (стандарт DIN) – 66Mn4, Ck67;
-
Великобритания – 080А67;
-
Япония (стандарт JIS) – SUP 6;
-
Китай – 65Mn.
Сортамент
Российские производители осуществляют поставку стали 65Г в следующих видах:
-
сортовой прокат (включая фасонный);
-
калиброванный пруток разных сечений – круг, квадрат, прямоугольник, шестигранник;
-
шлифованный пруток и серебрянка;
-
лист;
-
лента;
-
полоса;
-
проволока;
-
поковка.
На основе этих заготовок создаются изделия более сложных форм. Так, плоские пружины делают из ленты, полос или листовой стали, круглые пружины – из прутков или проволоки.
Для производства рессор автомобилей используют специальные полосы (ГОСТ 33556-2015). Типовая ширина таких листов: 55, 65, 75, 90, 100 и 120 мм, толщина – от 4,5 до 14 мм. Форма профиля, кроме обычной, может быть специальной: Т-образной, трапециевидной, трапециевидно-ступенчатой, желобчатой.
Холоднокатаная лента из пружинной стали 65Г выпускается толщиной от 0,1 до 4 мм, шириной – от 4 до 465 мм (по ГОСТ 2283-79), горячекатаная – толщиной до 14 мм и шириной до 630 мм (ГОСТ 14959-2016). Пружинные ленты используют не только для создания пружин, но и для многих других изделий. Так, для создания ножей в качестве основы используют полосы или ленты из стали 65Г.
Обработка
Чтобы сплав 65Г обрел заданные ГОСТом качества, он должен на этапе производства любых изделий обязательно пройти термическую обработку, схема которой зависит от специфики детали.
Основная технология для упрочнения многих изделий – закалка с последующим отпуском.
Закалка – это нагрев сплава до температуры выше критических температурных отметок и последующее быстрое охлаждение. В результате в материале происходит изменение типа кристаллической решетки, благодаря которым заметно повышается прочность и твердость, улучшаются эксплуатационные характеристики. Сталь 65Г закаливают при температуре от 800 до 830 градусов в камерных печах разных типов (нефтяных, пламенных, электрических, газовых и других) или соляных ваннах.
Чтобы термическое воздействие было оптимальным (равномерным по всему сечению, с нужной интенсивностью), для закалки этой стали часто применяют двухступенчатую схему:
-
в первой печи изделие постепенно (от 10 минут до нескольких часов) нагревается при температуре 500-700 градусов Цельсия;
-
после этого для финальной закалки во второй печи будет достаточно нескольких минут при температуре выше критических точек (при 800-830 градусов Цельсия).
За счет этого минимизируется нахождение заготовки в печи при экстремальных температурах, что позволяет предотвратить испарение углерода из верхнего слоя (по нормативу обезуглероживание не должно превышать 1,5-2%, чтобы не возникло дефектов).
Правда, есть и такие детали из сплава 65Г (например, некоторые виды пружин и проволоки), технология создания которых для получения нужных эксплуатационных свойств (увеличение предела упругости, пластичности) предусматривает изотермическую закалку (то есть при постоянной температуре, в одной печи).
Общее время нагрева в печи составляет от 20 до 180 минут в зависимости от закалочного оборудования и конфигурации детали: более толстые изделия требуется нагревать дольше.
Чтобы стальные изделия со сложной геометрией не коробились при высоких температурах, при их помещении в нагревательное устройство иногда требуются особые поддерживающие приспособления:
-
пружины большого диаметра закаливают на специальных оправках круглого сечения (например, на трубах);
-
небольшие пружины помещают в печь на прогретом поддоне (благодаря этому можно уменьшить время пребывания в печи, а значит, избежать деформации и снизить обезуглероживание поверхности, что особенно критично для небольших деталей).
После закалки детали из сплава 65Г охлаждают в минеральном масле: риск растрескивания деталей и возникновения дефектов в таком охладителе меньше, чем в воде.
В результате закалки этот материал приобретает мартенситную структуру. У такой стали высокая прочность, но низкая упругость, кроме того, она содержит внутренние напряжения, появившиеся при формировании мартенситной фракции, и могущие привести к дефектам, ломкости. Чтобы микроструктура материала перешла в устойчивое состояние, повысились упругость и текучесть до требуемых по ГОСТу значений, нужно провести еще один этап термообработки – отпуск. Это нагрев до определенной температуры, когда происходит распад пересыщенного твердого раствора мартенсита, и несколько меняется структура материала.
Для стали 65Г применяют следующие варианты отпуска:
-
низкий – при температуре до 250 градусов, в результате чего получается сталь с внутренней структурой отпущенного мартенсита;
-
средний – от 350 до 500 градусов, получаемая структура – тростит;
-
высокий – от 500 до 600 градусов, получаемая структура – сорбит.
Таким образом в зависимости от температуры отпуска получают сталь 65Г с нужными характеристиками. Максимальные показатели упругости удается получить при высоком отпуске.
Поэтому изделия, которые будут работать в условиях динамических нагрузок, где особенно важны пружинящие свойства (пружины и подобные элементы), отпускают обычно этим способом.
Кроме закалки с последующим отпуском, для упрочнения стали применяют и другие схемы термообработки (в зависимости от особенностей детали, требуемых свойств, экономической целесообразности). Например, используются:
-
патентирование (нагрев выше критических температур и охлаждение в расплаве свинца) с последующим отпуском;
-
нормализация, затем холодная пластическая деформация и отпуск/или низкотемпературный отжиг;
-
закалка, холодная пластическая деформация и старение/или отпуск.
Для улучшения антикоррозионных свойств в качестве финального этапа обработки может применяться специальное покрытие поверхности изделий из стали 65Г: оксидирование (воронение) или оцинковка.
Что касается механической обработки стали 65Г, то это материал, хорошо поддающийся ковке. Температурный режим: 1250 градусов в начале, 780-760 – в конце с последующим охлаждением на воздухе.
Сварка при необходимости осуществляется контактным способом без ограничений, но другие виды сварки для 65Г не подходят.
Если говорить об изготовлении изделий (ножей, клинков) из этой стали не на производстве, а в домашних условиях, то для достижения оптимальной твердости также требуется закалка и отпуск. Сделать это довольно сложно, так как требуются высокие температуры (800-830 градусов), но все-таки возможно. Для этого могут использоваться:
-
газовая горелка;
-
костер;
-
самодельная закалочная печь из кирпича.
Температуру контролируют по цвету стали: она должна быть практически белой («белого каления»). Охлаждают изделия в техническом масле (например, трансформаторном) или мыльном растворе. Отпуск можно осуществлять даже в обычной духовке.
Применение
Пружинный сплав 65Г разработан и применяется в первую очередь для нужд промышленности и машиностроения. Из этой стали производят самые разные ответственные упругие элементы и детали:
-
плоские и круглые пружины;
-
пружинные кольца и шайбы;
-
автомобильные рессоры;
-
упорные шайбы;
-
фланцы;
-
подшипники;
-
тормозные барабаны и ленты;
-
фрикционные диски;
-
шестеренки;
-
зажимные и подающие цанги;
-
ходовые колёса мостовых кранов, катков;
-
пластины для станков трикотажной промышленности;
-
специальные стальные ленты для фиксации особо тяжелых и ответственных грузов при транспортировке.
Другая сфера, кроме промышленности, – изготовление холодного оружия:
-
реконструкции исторического оружия (мечи, палаши, шашки, сабли);
-
метательные ножи;
-
спортивные клинки.