Каким бывает азотирование стали и как его делают?
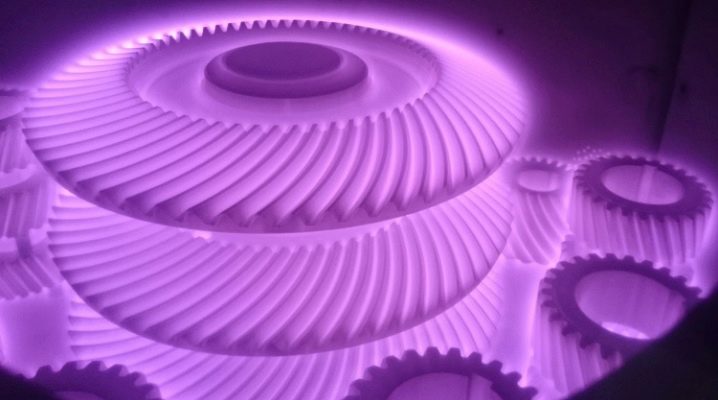
Азотирование стали – процесс изменения химических свойств металла. Его методы разнятся, отличаются и виды сред, в которых оно выполняется. Предлагаем рассмотреть основные нюансы его выполнения и узнать, для каких металлов оно подходит.
Что это такое и зачем нужно?
Азотирование сталей – промышленная термо-химическая технология. Ее сущность заключается в насыщении поверхностного стального слоя азотом. Ключевые цели – повышение твердости, износостойкости, инертности к ржавлению. Наряду с этим, азотирование снижает коэффициент трения поверхностей. В промышленных масштабах оно стало использоваться недавно. Несмотря на схожесть с цементацией, она в 2 раза эффективней.
Она выполняется с щадящим нагреванием стальных изделий. Их параметры остаются неизменными. Благодаря этому методика применяется для продукции, прошедшей закалку и шлифовку до предельно точной геометрии. В дальнейшем азотированную сталь полируют либо подвергают иным способам финишной отделки. Суть азотации заключается в нагревании стали до насыщенной аммиачной среды. Наряду с улучшением износоустойчивости повышается прочностная характеристика заготовок. Они приобретают иммунитет к воздействию воды, влажной и паровоздушной среды. Азотация стабилизирует показатели твердости стали.
После процедуры нагретая до предельно температуры деталь не меняет своих свойств. Азотные атомы преобразуются в кристаллическую решетку.
Как происходит процесс?
Процесс насыщения поверхностного слоя проходит в специальных герметичных камерах. Используемые муфельные печи имеют герметично закрывающиеся дверцы. Внутри можно создавать температуру от 500 до 600 градусов С. По достижении нужного показателя оно поддерживается в течение некоторого времени. Изначально осуществляется закалка металла с последующим отпуском. Он становится удобным для нарезки, механической обработки, выверки геометрии. После этого детали подвергаются следующему виду термообработки. В камеру оборудования под давлением подается аммиак. Из-за высокой температуры аммиак распадается на 2N и 6H.
После высвобождения атомов происходит процесс диффузии и образование нитридов. В ходе покрытия металла происходит его усиление. Для закрепления результата прибегают к постепенному охлаждению камеры. Это требуется для того, чтобы в дальнейшем исключить окисление металла. Полученная азотированная сталь может иметь глубину нитридного слоя от 0,3 до 0,6 мм. Данные значения являются нормой, поэтому дальнейших обработок не нужно.
В редких случаях азотация занимает несколько суток. Для нее необходимо специализированное оборудование, поэтому упрочнить сталь в домашних условиях не получится. Негативным моментом является высокая стоимость изделий. Для процедуры применяют дорогостоящие марки металла. Стоимость таких изделий существенно выше обычных. В ходе обработки некоторые участки деталей закрывают защитным слоем. Это делается для частей оснований, не нуждающихся в обрабатывании. В защитных целях их закрывают оловянной либо жидкостекольной пленкой. Под такую пленку азот не проникает. Затем выполняют насыщение и упрочнение стали и ее конечную обработку (шлифовку).
Виды
Существует 3 типа азотирования. Они разнятся методом выделения азота, рабочим режимом температуры и средой. Однако все они протекают по закону диффузии. Появление разных методик сопряжено с желанием ускорения процесса, улучшения характеристик и качества изделий. Например, с развитием технологий сегодня используют принцип плазменного (ионно-плазменного) азотирования и прием с использованием электролитного раствора.
Суть последнего заключается в анодном электролитном нагревании. Скоростная техника подразумевает подачу на деталь электрических импульсных зарядов, проходящих через все изделие. Плазменное азотирование востребовано ввиду неиспользования аммиака. Кроме того, технология проходит при сниженной температуре. Это исключает вероятность даже малейшего изменения изначальной геометрии деталей.
Благодаря этому в обработке используют детали с обработкой в размер, которым не нужна финишная отделка. Такая особенность позволяет удешевить процесс насыщения металла.
Газовое
Каталитическая газовая азотация происходит с созданием атмосферы, при которой аммиак обрабатывают на каталитическом элементе. Методика предполагает использование сложного оборудования (шахтных, ретортных, камерных печей). За счет выхода большого объема ионизированных радикалов происходит увеличение твердорастворной диффузии. Таким образом, создается ускоренное проникновение азота в структуру стали.
В сравнении с другими технологиями производства, данный процесс более затратный. Однако подобное насыщение позволяет добиться максимальной износоустойчивости изделий. Азотация газового типа проходит в рабочей среде, в которой аммиак смешан с пропаном либо эндогазом. Диффузия занимает порядка 3 ч, в ходе нее создается тончайшая защита. Процесс протекает при разных температурах. Для смены структуры применяется воздух, разбавляется диссоциированный аммиак и водород.
Термохимическое
Химико-термическая обработка металла предполагает использование лишь газообразного аммиака. Он подается из баллона внутрь надежно закрытого бокса, где уложены заготовки, нуждающиеся в азотировании. Бокс располагают в печи, где проводят нагрев при заданной температуре. Под воздействием горячего воздуха аммиак распадается на азот и иные элементы.
Азот проникает в поверхностный слой стали. Глубина проникновения зависит от времени технологического процесса: чем дольше, тем глубже. Благодаря данной технологии удается получить укрепленный слой 0,6 мм. Методика считается модифицированной, более щадящей в сравнении с газовой технологией. Эффект зависит от предварительной подготовки и термических операций.
Температура подбирается с учетом химического состава металла, параметров твердости основания, конструктивной жесткости, допуска величины деформации.
Факторы, влияющие на азотацию
Ключевыми критериями считаются:
- значения температуры в ходе насыщения стали;
- давление газа в герметично закрытом бункере;
- продолжительность периода остывания.
Важна и аммиачная диссоциация, оптимальные параметры которой составляют 15-45%. При большем нагревании происходит ускорение диффузии с одновременным уменьшением прочности. Для сокращения продолжительности процесса и обеспечения твердости азотации сталь насыщают на оборудовании, оснащенном 2-мя термическими режимами работы. Температура первичной обработки достигает 525 градусов. Так задается базовая твердость без вероятности перекалки заготовки. Позже она поднимется до 600 градусов.
Благодаря этому аммиак проникает до необходимой глубины. Снижение давления газа не увеличивает предел текучести. Деформация протекает однородно по всей поверхности. Однако аммиак хуже меняет пластичность и механические свойства деталей. Что касается продолжительности выдержки в печи, то длительное ожидание в условиях промышленного производства не всегда целесообразно. Это решается технологией двухступенчатого нагревания.
Типы сред
Для максимально эффективного усвоения нитридов каждому сплаву нужны свои условия. От этого зависит качество насыщенной азотом структуры и специфика организации технологии. Особо популярный вариант – аммиачно-пропановая среда. При этом для обработки используется смесь из компонентов в равном соотношении. Оптимальные показатели температуры составляют 570 градусов, выдерживаются обработанные изделия не более 3 ч. В итоге удается добиться особо износоустойчивого покрытия.
При минимальной толщине его твердость может варьироваться в диапазоне 600-1100 HB. Технология подходит для работы с деталями из легированной стали, к которой предъявляют требования максимально допустимой выносливости. Помимо этого, для упрочнения стали прибегают к принципу тлеющего разряда с подключением металла к катоду. В данной среде деталь является отрицательным электродом. Муфель – с положительным зарядом. Содержащая азот разреженная среда существенно сокращает срок азотации. При возбуждении разряда газовые ионы подаются на катод, разогревая его до заданной температуры. Изначально осуществляется катодное распыление, в дальнейшем – очищение и насыщение поверхности металла. Длительность первого этапа составляет от 5 до 20-60 мин под напряжением 1400 В. 2-й этап азотации длится от 1 ч до суток. Азотирование проходит и в жидкой среде. Карбонитрирование осуществляется в расплаве солей. Технология занимает меньше времени, считается гибким методом.
Он выгоден тогда, когда на 1-е место ставится получение максимальной твердости и прочности, инертности к ржавлению обрабатываемых материалов. Однако технология не подходит для изменения структуры габаритных предметов. В жидкостной среде компоненты цианистых солей проникают в поверхностную структуру.
Сама методика дорогостоящая и вредная для человеческого здоровья. Вдыхание паров опасно, хотя метод и производителен.
Какие металлы подвергаются процедуре?
Для азотистого обогащения могут использоваться легированные, углеродистые марки сталей. Варианты 1-го вида протекают с большей эффективностью. Азотирование в аммиаке, согласно ГОСТ 6221-75, выполняется для среднеуглеродистых сталей, работающих на износ в условиях знакопеременных нагрузок. Идеально, когда в сплав включены легирующие вещества, формирующие термоустойчивые нитриды (алюминий, хром, молибден). Данные металлы не имеют хрупкости. По окончании обработки они становятся максимально твердыми.
Твердость сплавов после обработки составляет: углеродистых – не более 250 HV, легированных – 800 HV, нитролои – 1200 HV. Выбирая металл, отталкиваются от маркировки стали и предназначение самого изделия. Легирующие компоненты стали сказываются на толщине слоя. Вольфрам, молибден, никель, хром делают структуру тоньше. Влияние иных элементов менее значительное.
- 38Х2МЮА – разновидность стали с алюминием. После обработки она становится не только твердой и износоустойчивой, но и стойкой к деформации. Исключение алюминия позволяет изготавливать детали со сложной конфигурацией.
- 40Х и 40ХФА – металлы, применяемые в станкостроении. Азотирование придает им особую прочность и стойкость к высоким нагрузкам.
- 38ХНМФА, 38ХН3МА – марки стали, из которой в дальнейшем планируется производить изделия с постоянной нагрузкой на изгибание.
- 30Х3МФ1 – сталь для выпуска продукции с особо точной геометрией. В целях повышения прочности в нее нередко добавляется кремний. Из нее производят топливное оборудование.
Кроме того, азотированием упрочняют инструментальные, коррозионно-стойкие, жаропрочные, конструкционные металлы.