Что такое автоматная сталь и как ее обрабатывают?
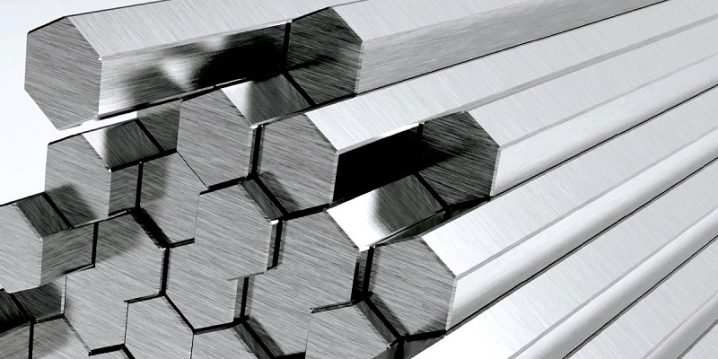
Людям, интересующимся рынком металлической продукции обязательно стоит выяснить, что такое автоматная сталь, какие у нее бывают марки и что показывает маркировка, какие стали называют автоматными и почему. Не меньшего внимания заслуживают структура и ГОСТ, то, какими свойствами она должна обладать. Еще требуется изучить применение стали автоматного типа.
Что это такое?
Разумеется, автоматной сталью называются не те сплавы, которые используются для производства автоматического оружия. Это конструкционный металл, применяемый в получении заготовок на станках-автоматах. Все такие материалы должны обладать свойствами, упрощающими обработку и при этом обеспечивающими экономичность дальнейшей эксплуатации. Очень важно также высокое качество готовой продукции. Во многом оно определяется структурой металла и его химическим составом. Они даже более значимы, чем профессионализм специалистов и совершенство применяемого оборудования. Самым ценным практическим свойством является стабильная обрабатываемость резанием. Именно ее оговаривают в любом договоре о поставке автоматной стали.
ГОСТ на традиционную конструкционную сталь предусматривает стабильную прочность и стойкость к пониженной, повышенной температурам. Там прописывается и отсутствие примесей выше критического порога. Но всего это недостаточно для автоматной стали, более того, для нее подобные свойства могут стать недостатками. Для изготовления сложно устроенных малогабаритных деталей на автоматическом станке не нужно использовать особо прочные материалы. Пластичность существенно упрощает обработку. Автоматную сталь в России выпускают согласно стандарту 1414 от 1975 года. Она должна иметь поверхность с малой шероховатостью, чтобы деталь получила однородное строение.
Еще одним ключевым свойством является небольшой износ режущих приспособлений и станков, пригодность для разрезания на повышенных скоростях.
Плюсы и минусы
Как нетрудно понять, автоматные стали режутся легко и быстро. При манипуляциях с ними стружка отделяется хорошо, а сам материал отличается высокой теплопроводностью. Это сравнительно мягкий материал. При контакте с ним ресурс резца любого станка расходуется медленно.
Такие преимущества гарантируют повышение производительности и рентабельности производства в несколько раз. Однако присутствие заметных серы и фосфора, которые обеспечивают обрабатываемость, ведет и к проблемам: добиться высоких вязких и пластических свойств непросто.
Маркировка и основные марки
Любые автоматные стали маркируют индексами, начинающимися с «А». Эта буква ставится даже перед процентным содержанием углерода. Наряду с углеродом, серой и фосфором могут применяться другие добавки. Присутствие свинца показывают символом «С», а введение кальция — знаком «Ц». Со свинцом поставляют:
- АС14;
- АС40;
- АС35Г2;
- АС45Г2;
- АС30ХМ.
Концентрация углерода в них составляет 0,14%, 0,4%, 0,35%, 0,45% и 0,3%, соответственно. Доля свинца колеблется от 0,15 до 0,3%. Кальцинирование проводится в очень небольших дозах — максимум 0,007%. Речь идет про сплавы АЦ20, АЦ40, АЦ35Г2, АЦ30ХМ. Селен употребляется в количестве максимум десятой доли процента. О нем свидетельствует буква «Е» в конце, например, А35Е, А45Е или А40ХЕ.
Легирование и обработка
Согласно ГОСТу, концентрация серы может быть не меньше 0,08% и не больше 0,2%. В ее присутствии появляются сульфиды марганца. Эти компоненты обеспечивают лучший надлом стружки и уменьшают шероховатость обработанных поверхностей. Дополнительно они как бы смазывают инструмент и повышают его ресурс (вернее, понижают расходование ресурса). Фосфора там содержится от 0,06 до 0,15%, в сочетании с серой он помогает лучше резать металл. Введение свинца гарантирует увеличение стойкости инструментов до 3 раз. Благодаря нему резание проводится быстрее как минимум на 1/4. Концентрация селена варьируется от 0,04 до 0,1%. Кальций в области разреза формирует специальный слой, толщина которого не превышает нескольких микрон. Такой слой является своеобразной внутренней смазкой и ослабляет износ применяемого инструмента.
Также в автоматных сталях присутствуют:
- теллур;
- никель;
- хром;
- висмут (смазывающий участок резки);
- марганец (его доля составляет от 0,7 до 1,7%).
Вхождение серы и фосфора ограничивают очень жестко. Хотя они и позволяют улучшать характеристики автоматной стали, с определенного момента преимущества будут перевешивать. Углеродистые сплавы с доэвтектоидной структурой прокатывают либо куют в горячем состоянии. Дальше их остужают на воздухе, что приводит к появлению пластинчатого перлита и незначительной части феррита.
Если такую обработку применяют к заэвтектоидным сплавам, получается пластинчатый перлит и избыток цементита.
Этот цементит формирует сетчатую структуру (монолитную или прерывающуюся) на периметре изменяющихся аустенитных зерен. Предварительно обрабатывать углеродистый инструментальный сплав надо путем отжига. В этот момент температура составляет от 740 до 760 градусов. В итоге отожженный металл будет состоять из зернистого псевдоперлита. Именно он обеспечивает максимальное единообразие характеристик во всем объеме и легкость механического воздействия. Финальная термообработка тоже важна. Закаливающую процедуру ведут при 780-810 градусах. Критический темп закаливания для автоматного углеродистого сплава очень велик. Из-за этого охлаждение должно идти максимально быстро, чтобы исключить частичное разрушение аустенита и образование размягченных участков. Аустенит распадается максимально скоро, если углеродистую сталь нагревают до 500-550 градусов. Иногда процесс проходит за считанные секунды.
Лишь приспособления с небольшим сечением допускается после закаливания в воде прокаливать насквозь. Но внутри них будут образовываться серьезные внутренние напряжения. Потому вероятность деформации достаточно велика. Большие предметы могут закаливаться не только в воде, но и в водных растворах других веществ (кислот, щелочей, солей).
Такой способ отвода тепла более эффективен. При подобном методе обработки мартенсит будет закален только непосредственно у поверхности. В глубине металла аустенит распадется так же, как он обычно распадается в перлитной температурной зоне. Центр инструмента, обработанного таким образом, менее хрупок, чем при классической мартенситной структуре. Подобное приспособление лучше переживет толчки и ударные воздействия в сравнении с закаленным на мартенсит. Углеродистая сталь должна использоваться для инструментов с сечением не более 0,5 см.
Их закаливают в масле и добивают прокаливанием насквозь. Допускается такой режим обработки для инструментов, чье сечение или минимальная толщина составляют от 1,8 до 2,5 см. В таком случае режущий блок должен находиться лишь на поверхности. Речь идет о зенкерах, напильниках и метчиках. Углеродистая сталь инструментального класса должна быть отпущена максимум при 200 градусах. Этот момент обусловлен необходимостью сохранять твердость. У правильно обработанного термически инструмента твердость составляет от 56 до 64 единиц по шкале HB. Углеродистый автоматный подкласс инструментальной категории ценится за сравнительную дешевизну и обрабатывается (как давлением, так и резанием) без проблем.
Однако такой материал режет сравнительно медленно. Малая эффективность прокаливания накладывает жесткие ограничения на размер вырабатываемого инструмента. При водной закалке деформации будут крайне сильны.
Применение
Сфера использования автоматных сталей невелика. В основном их отгружают на производство крепежа (метизов). Допускается выпуск и других изделий, к которым не предъявляются повышенные требования. Речь идет про некоторые детали автомобилей и мелкие объекты с малой нагрузкой. Автоматные стали заказывают производители:
- болтов;
- шурупов;
- гаек;
- валиков;
- участков цепей и тому подобных малонагруженных предметов.
На основе таких сплавов можно выпускать еще детали машин, имеющие усложненную геометрическую форму и конфигурацию. Речь идет про:
- передающие механизмы зубчатого типа;
- валики насосов, качающих масла;
- кольца на полуосях автомобилей.