Все о твердосплавных фрезах
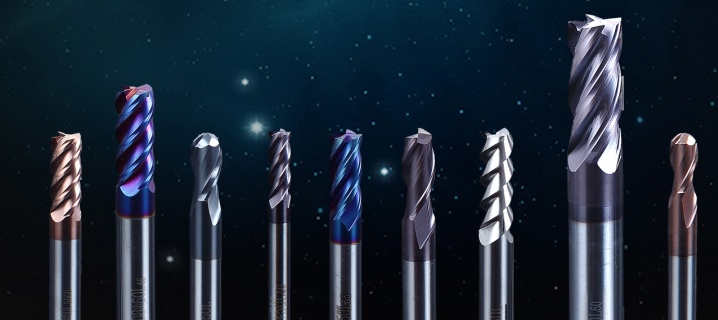
Зная всё о твёрдосплавных фрезах, можно исключить множество ошибок в организации производства. Существуют различные виды такого инструмента: по металлу и дереву, концевые и «кукуруза», отрезные с твёрдосплавными пластинами и другие типы. Помимо их заточки и требований ГОСТ, необходимо учесть особенности использования.
Описание и сферы применения
Твёрдосплавные фрезы могут пригодиться даже в самых сложных и тяжёлых случаях.
Обработка на высоких скоростях неизбежно приводит к сильному нагреву инструмента. Традиционные быстрорежущие сплавы в таких случаях резко теряют свои свойства.
Хорошая твёрдосплавная фреза может работать на скоростях в 5-10 раз больше, чем простое стальное изделие. Система отлично работает по металлу, даже если накалится до 700-800 градусов.
Немаловажно, что при этом обеспечивается ещё и очень высокая производительность. Срок службы весьма велик, даже при активном использовании. И наконец, такие модели отлично проявляют себя при работах с особо твёрдыми заготовками. Ни один быстрорежущий инструмент на такое заведомо не способен.
Но стоит отметить, что фреза из твёрдого сплава сильно страдает от вибраций и в зоне их воздействия может быстро выйти из строя; частично проблема решается за счёт напыления карбида титана и других веществ.
Такой инструмент может пригодиться:
- для чистовой обработки;
- для чистовых и получистовых манипуляций;
- под выборку;
- под раскрой;
- для контурной обработки различных изделий;
- для фрезерования металла и пластика на высоких скоростях;
- для обработки предварительно термообработанных материалов.
Твёрдосплавные фрезы с пластинами позволяют фрезеровать:
- пазы серьёзной глубины;
- полностью открытые пазы;
- уступы различной сложности.
Дисковые изделия такого рода могут быть отрегулированы по ширине.
Но закрытые пазы обрабатывать нельзя. Отвод стружки серьёзно затруднён.
Твёрдосплавные фрезы могут неплохо использоваться и по дереву. Обычно такие изделия имеют сборное исполнение; стандартная для иностранной продукции маркировка — HSS.
Разумеется, на инструмент из твёрдого сплава разработан специализированный ГОСТ 18372. Он действует с 1973 года, но в целом не потерял своей актуальности. По стандарту предусматривается использование как цельных конструкций, так и изделий со сборным хвостовиком. Различаются праворежущие и леворежущие фрезы такого рода; нормируются и линейные показатели, и общее число зубьев.
Обзор видов
Важную роль играет специфика материала. Есть три основные группы:
- вольфрам-кобальт;
- титан-вольфрам;
- вольфрам-титан-тантал.
Сплав вольфрама и кобальта всегда прочен. Однако всё же он имеет самую малую крепость среди всех твёрдосплавных вариантов. Стойкость к нагреву составляет всего лишь 800 градусов.
Чаще всего такие сплавы применяют в обработке хрупких металлов и ряда неметаллических веществ.
Сочетание титана и вольфрама прогревается как минимум до 1000 градусов без потери качества и имеет отличную прочность; его можно применять, чтобы быстро фрезеровать распространённые сорта чугуна и стали.
Есть и ещё более прочные сплавы. Объединение танталового, титанового и вольфрамового карбидов позволяет заметно сократить подверженность крошению. Восприимчивость к вибрациям тоже уменьшается. Подобные модели пригодны для черновых манипуляций:
- с отливками;
- поковками из стали;
- сплавами (в том числе сталями), которые трудно обработать другими методами.
Концевые твёрдосплавные фрезы обычно изготавливаются из сталей категории ВК. Строго нормируется не только степень износа зуба, но и значение конуса инструмента в целом (показатель конусности, как его часто называют в документации и в описаниях). Отвод стружки может иметь верхнее и нижнее направление — оба варианта соответствуют технической норме. Варьируется изначальная величина зуба.
Довольно широко применяется отрезная фреза 2х10х50 и других размеров. Она нужна, чтобы работать именно со сталями средней плотности и с чугунами. Допускается использование как на простом станочном оборудовании, так и на системах ЧПУ. С помощью подобных изделий можно:
- нарезать заготовки на части;
- дорабатывать их;
- прокладывать канавки.
Солидная часть ассортимента представлена всегда цельными (монолитными) фрезами. С их помощью обрабатываются заготовки из разнородных материалов и в самой разной геометрической конфигурации. Но и шпоночная разновидность тоже находит широкое применение. Основная сфера их использования — формирование различных технологических выемок. Можно добиться самых разных режимов резания без лишних проблем.
Шпоночные фрезы активно использует машиностроение во всех своих отраслях. Трудно назвать тот вид специализированной металлообработки, где без них можно обойтись. Но и производство бытовой аппаратуры, коммунальной техники тоже часто подразумевает использование шпоночных инструментов. Их, разумеется, применяют и в частных, домашних мастерских, а не только на крупных заводах.
Обычно частные заказчики выбирают недорогие изделия массового класса, которые служат недолго, но зато вполне доступны.
Корончатая группа инструментов также, безусловно, заслуживает внимания.
К сведению: в ряде источников их ещё называют кольцевыми фрезами.
Достаточно нескольких секунд, чтобы с их помощью получить в металлической заготовке отверстие существенного диаметра и притом большой глубины. Что немаловажно, многократно понижается расход энергии, что сразу положительно отразится на экономических показателях при работе.
Основные достоинства:
- прорез отверстия идёт точно по контуру, что и позволяет экономить драгоценную энергию;
- можно добиться отличной шероховатости внутреннего объёма в канале;
- пригодность для работы на токарном станке;
- высокая площадь соприкосновения с обрабатываемым материалом;
- отличный уровень производительности;
- повышенная точность манипуляций;
- сравнительно малая шумность;
- сочетаемость со многими другими инструментами в формате многоинструментальной обработки.
Довольно часто продаются фрезы с механическим креплением пластин из твёрдого сплава. Обычно они имеют кольцевое исполнение. Присоединение пластинки через намеченное отверстие производится как винтами, так и штифтами. Но могут встречаться и торцевые варианты инструмента. Весомая разница между ними часто заключается в количестве граней у используемых пластин; альтернативное название — фреза со вставляемыми ножами.
В завершение стоит рассмотреть конусные фрезы формата «кукуруза». Отличие от предыдущего варианта состоит в том, что рабочие пластины ставятся в несколько рядов. Разумеется, это позволяет обрабатывать материал сразу на существенную глубину.
Подобное решение становится идеальным для высокопроизводительных черновых проходов, минимизирующих потребность в чистовой обработке.
Корпусные «кукурузы» находят широкое применение в тяжёлых механических операциях для нужд:
- авиа и ракетостроения;
- судостроения;
- производства локомотивов и вагонов;
- получения штампов, пресс-форм.
Сравнение с другими типами
В промышленных работах твёрдые сплавы демонстрируют существенное отличие от других видов, в том числе от быстрорежущих марок. Разумеется, у тех есть свои области применения, но даже в специфических сферах «твёрдосплав» вполне выгоден. Карбид вольфрама, который настолько распространён, что уже стал неформальным синонимом термина «твёрдый сплав», позволяет:
- исключить налипание стружки в процессе работы;
- выполнять манипуляции достаточно точно;
- справляться с самыми грубыми и трудными материалами.
Но совсем вытеснить другие варианты твёрдосплавный инструмент вряд ли сумеет. Все его технологические преимущества изрядно обесцениваются высокой стоимостью. При диаметре 15 мм и выше быстрорежущие соединения оказываются экономически эффективнее.
Стоит отметить, что есть и другие примеры, когда твёрдый сплав проигрывает. Так, для ногтевого сервиса однозначно лучше керамическая фреза.
Особенности эксплуатации
Среди режимов резания очень большое значение имеет его скорость. Термопласты, а также различные виды древесины обрабатываются с темпом от 300 до 500 м за минуту. Для прочих материалов ситуация такая:
- бронза – 90-150;
- латунь – 130-320;
- поливинилхлорид – от 100 до 250;
- алюминиевые сплавы – от 200 до 450 м.
Но знать, как быстро работать — это ещё далеко не всё. Крайне нежелательно работать с максимально высокими темпами кручения инструмента и шпинделя (если только это не предписано напрямую технологией). Иначе гарантировать безопасность никак не получится.
Чтобы ослабить потерю 10-15% скорости от максимума, можно иногда ставить фрезу чуть большего по сравнению с расчётным диаметра. Но подобные эксперименты могут проводить лишь профессионалы, изучившие как следует использование конкретного инструмента и станочного парка.
Оптимальные значения подачи на каждый зуб нормируются производителем. Если вынужденно используется инструмент сомнительного происхождения, без документации, то лучше ограничиться значениями от 0,1 до 0,25 мм. В крайнем случае прямо по ходу прореза станет ясно, что нужно скорректировать настройки. Обязательно следует иметь в мастерской или при цехе станок для заточки твёрдосплавных фрез. На нём используют круги с алмазным напылением или на основе зелёного карбида кремния – все прочие варианты не справятся с такой задачей.
Вот ещё несколько рекомендаций:
- брать для мягких материалов инструмент с крупнозернистым составом;
- по возможности разделять операции черновой и чистовой проходки для лучшего контроля результата;
- выбор инструмента диктуется ещё и соображениями максимальной сохранности обрабатываемой поверхности;
- положительное направление спирали подходит лишь для заготовок с надёжной фиксацией;
- по возможности следует организовывать отвод тепла от применяемого инструмента;
- наиболее перспективной технологией охлаждения является так называемый промышленный туман.
Подробнее о других видах твердосплавных фрез вы сможете узнать из видео ниже.