Какой бывает фибра и как ее применять?
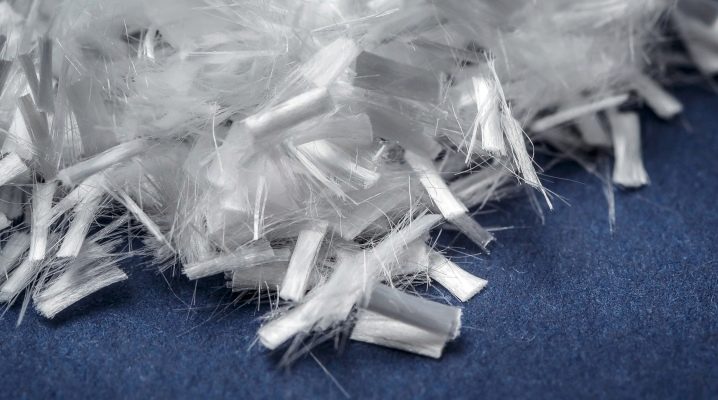
Фибра считается популярным материалом с широким спектром применения. В статье мы расскажем, что она собой представляет, каковы ее разновидности и сферы использования, стоит ли ее делать своими руками из того, что найдется в доме.
Что это такое?
В дословном переводе с латинского языка «фибра» означает «волокно». По сути, это именно армирующие нити, материал которых зависит от назначения. Строительная фибра является добавкой к стройматериалам. Сырье для ее производства бывает минеральным, растительным и синтетическим.
Основные функции в данном случае – придание прочности, повышение физико-механических свойств применяемых стройрастворов.
Материал улучшает сцепление, уменьшает образование трещин при усадке в пределах 60-90%. Он увеличивает прочностные показатели на изгиб, повышает стойкость к истиранию до 20%.
Может выполнять функцию микроарматуры, располагаясь в рабочем растворе под разными углами. Тем самым образуется сеть, исключающая смену положения ЦПС.
Используется в целях улучшения ремонтопригодности готовой плоскости. В зависимости от разновидности способна повышать морозоустойчивость, снижать воздействие температурных колебаний.
Материал поставляется на строительный рынок в мешках массой от 1 до 20 кг. Продукция меньшего объема дополнительно упаковывается в полиэтиленовые гофропаллеты.
Помимо этого, упаковка бывает на бумажной основе. Такая тара удобна тем, что ее не удаляют, а закладывают вместе с волокном в бетономешалку.
Во время размешивания упаковка полностью растворяется.
Виды
Строительный материал классифицируется по типу основного сырья. Каждой разновидности присущи свои особенности.
Стальная
Стальное фиброволокно изготавливается из углеродистой, нержавеющей, классической стали. Оно представляет собой проволоку, толщина которой достигает 1,2 мм при длине 1-1,2 см.
Изготавливается электромеханическим или механическим способом, методом формовки. Длина отдельных волокон доходит до 5 см.
Сечение фибры бывает круглым, треугольным, форма – прямой, дугообразной, в виде скоб.
В целях повышения сцепления с бетоном материал профилируют, благодаря чему он становится волнистым. Поверхность делают шероховатой, покрывают латунью. Помимо волнообразной, бывает прямой (листовой) и анкерной.
Данное фиброволокно добавляют в замес либо итоговый раствор. В первом случае получается более однородный состав. Объем добавляемой фибры связан с нагрузками. Материал сочетается с иными модифицирующими добавками.
Недостатками волокон из стали считаются высокий вес, малая коррозийная стойкость, способность выходить на бетонную поверхность при эрозии. Для предупреждения ржавления волокно подвергают оцинковке либо покрывают иными составами.
Его плотность составляет 7,8 г/см3, сечение – 200-1200 мкм, модуль упругости – 190-210 ГПа. Показатели прочности на растяжение варьируются в пределах 500-1500 МПа. Разрывное удлинение не превышает 3-4%.
Базальтовая
Базальтовое фиброволокно – продукт расплава камня вулканического происхождения. Выглядит как отрезки идентичной длины. Не имеет запаха, обладает устойчивостью к воздействию огня и высоким температурам.
Отличается хорошим взаимодействием с материалами, обладающими пористой структурой. Имеет большие параметры длины и диаметра в сравнении с другими разновидностями.
Имеет массу преимуществ. Является негорючим, нетоксичным материалом, устойчивым к действию агрессивной химии. Отличительной чертой является полное растворение в ходе смешивания с цементной смесью.
За счет своих свойств применяется при создании жароустойчивых бетонных конструкций. Используется в объеме 1,5-2,7 кг на 1 м2 бетона.
Материал отличается экономичностью, предназначен для изготовления гипсовых сооружений.
Плотность базальтовой фибры составляет 2,6 г/см3, сечение – 0,02-04 мкм. Коэффициент упругости ниже стальных аналогов практически в 3 раза (68-70 ГПа). Прочностные значения растяжения больше – 910-3100 МПа. Удлинение практически нулевое (0,6%).
Базальтовая фибра морозоустойчива, инертна к воздействию кислот, солей и щелочей. У нее минимальная гигроскопичность в сравнении с аналогом из стекла. Она упруга, помимо гипса, используется в работе с любыми типами бетона.
Применяется при возведении взрывоопасных объектов военного назначения, в гражданском и сейсмоопасном строительстве.
Полипропиленовая
Продукция из полипропилена – крошечные волокна из пленки, нарезанные и скрученные в жгуты. Их размеры не превышают 0,038х0,5 мм. В ходе размешивания они раскрываются, образуя структуру сетки.
Волокна существенно увеличивают значения усталостной и ударной прочности конструкций. Они повышают морозо- и износоустойчивость, термостойкость.
Использование материала позволяет исключить вероятность образования трещин в бетонных изделиях (например, полах, стенах), продлить срок их службы.
При этом средний расход материала на 1 м2 не превышает 1 кг. Волокно применяется в устройстве изоляции бетонов с ячеистой структурой. Оно улучшает характеристики декоративных изделий (бордюров, тротуарных плит).
Его прочность на растяжение варьируется в пределах 150-600 МПа. Температура плавления составляет 160 градусов, что существенно ниже показателей стального (1550) и базальтового (1450) аналогов.
Коэффициент удлинения полимерного материала колеблется от 20 до 150%. Показатель упругости не превышает 35 ГПа. Материал экономичен, повышает стойкость конструкций к ударам и воздействию влаги. Его плотность составляет 0,9 г/см3.
Примерный расход, в зависимости от типа нагрузки, колеблется в пределах 0,6-2,7 кг/м3. Фибра существенно снижает трудозатраты и общий вес возводимых сооружений.
Другие
Помимо основных разновидностей, существует несколько не столь распространенных видов фиброволокна, используемых для бетона, штукатурки и прочих строительных смесей.
Углеродная фибра – добавка, не подверженная ржавлению. Она устойчива к щелочному воздействию, обладает высоким уровнем сцепления с бетоном, чего нет у полипропиленового аналога.
Производится из углерода путем термообработки при температуре 3200 градусов. Стоит дороже иных аналогов, но это компенсируется показателем прочности, минимальным коэффициентом удлинения, устойчивостью к агрессивным средам.
Углеродное фиброволокно применяется в обустройстве дорог и полос аэродрома. С его помощью возводят инженерные и гидротехнические сооружения, производят железобетонные изделия, устойчивые к истиранию.
Полиамидное фиброволокно из нейлона повышает гидроизоляционные характеристики возводимых конструкций. Оно вводится не только в сухие смеси, но и в растворы с водой.
Отличается низкой стоимостью и небольшим расходом. Его средняя норма на кубический метр составляет 200 г.
Стекловолоконная фибра – продукция, посредством которой рабочий раствор становится более пластичным. Продукт предназначен для отделки и декорирования, поскольку рассчитан на существенные нагрузки.
У него малый вес и скромные объемные размеры. С его помощью реставрируют памятники архитектуры. Материал продается отдельно и включенным в состав строительных смесей. Его область применения ограничена.
При плотности 2,6 г/см3 имеет температуру плавления 860 градусов. Модуль упругости составляет 75 ГПа, коэффициент удлинения – не более 4,5%. Прочность на растяжение колеблется в пределах 1500-3500 МПа.
Асбестовое волокно имеет оптимальные характеристики прочности и долговечности. Оно является натуральной огнеупорной добавкой, отличается высоким значением звукоизоляции.
Применяется для внутренней сцепки слоя бетона либо штукатурки. Характеризуется доступностью, причем не любой вид безопасен. К примеру, хризотиловый продукт безвредный, амфиболовый – канцерогенный.
Устойчивость к действию щелочной среды составляет 9-10,1 pH. У него минимальный порог тепло- и электропроводности. Показатель огнеупорности достигает 1500 градусов.
Полимерная фибра – модифицированный аналог полипропиленовой добавки. У нее более высокие, в сравнении с ней, характеристики. Однако, как и традиционное волокно, она не способна полностью заменить армирование.
ПАН-фибра обладает легкостью и инертностью к химическим реакциям. Она безразлична к ржавлению и полностью безопасна для человеческого здоровья. Проста и удобна в замешивании, придает раствору пластичность.
Целлюлозный аналог – полностью натуральный, с высокой адгезией и образованием плотной армирующей сетки. Он снижает усадку составов после высыхания и риск их растрескивания.
Технические характеристики целлюлозных волокон приближены к полипропиленовым. На 1 м3 бетона расход продукта – всего 0,7-0,9 кг. При этом цена на фиброволокно составляет менее 100 рублей.
Как сделать своими руками?
Сделать фибру можно из подручных материалов. Самый простой вариант – нарезать полипропиленовую веревку либо мешок из-под сахара или муки на полосы одинаковой длины. Однако расход такого армирования не будет соответствовать необходимым значениям.
При отсутствии мешков основным сырьем может стать плотная упаковочная лента (кордовая). Ею обвязывают макулатурные брикеты и отходы пластика. Чтобы превратить в фибру, ее режут на несколько полос и разрезают на одинаковые отрезки.
При желании можно порезать на куски длиной 2 см стальную проволоку. Но с учетом того, что для работы понадобится порезать примерно 20 кг металла, проще всего купить готовое волокно. Особенно это нецелесообразно, если дома нет специального фрезерного оборудования.
Замена оригинальной продукции чревата ухудшением качества и надежности будущих конструкций. Такой подход к строительным работам не даст гарантии долговечности.
Самостоятельное изготовление раствора с фиброй разнится. Общая технология подразумевает подготовку фибромассы, приготовление композита и формовку изделий.
Перед введением полипропилена добавляют наполнитель, щебень либо гравий. После этого сыплют песок и смешивают сухой состав.
Затем в него отправляют нужный объем фиброволокна, после чего в смесь добавляют цемент и воду, в которой растворены пластификаторы. Раствор перемешивают до состояния однородности.
При самостоятельном введении базальтовых волокон изначально в бетоносмеситель сыплют щебень и песок. После этого добавляют фиброволокно с дальнейшим перемешиванием.
Пока оборудование продолжает работать, в него заливают воду, а потом засыпают цемент. Замешивают до получения необходимой консистенции, соблюдая необходимые пропорции.
Особенности применения
Применение материала связано с его разновидностью. Стальное фиброволокно более популярно у покупателей и отличается широкими возможностями в строительной сфере.
Его средний расход на 1 м2 равен 30-40 кг. Фибра из стали делает бетоны высокопрочными и стойкими к внешним факторам. За счет нее они становятся более надежными и долговечными.
Анкерная фибра кладется в бетон в тех случаях, когда необходимо оформление изгибов сооружений. Она расходуется в объеме на 1 м2 до 20-40 кг. Объем воды и цемента уменьшается на 15-20%.
У фибры разное предназначение для различных стройматериалов. Параметры волокнистой присадки для замеса с бетоном, штукатуркой, сыпучими строительными смесями неодинаковы.
- Разновидности длиной 0,6 см предназначаются для добавления в цемент, песок, гипс, пенобетон, штукатурку, затирку.
- Аналоги длиной 1,2 см предназначены для улучшения прочностных характеристик плит перекрытий, пено- и газобетона, наливного пола, свай, полых бетонных конструкций.
- Волокном 1,2-1,8 см упрочняют тяжелые и сверхтяжелые бетоны, замешиваемые с щебенкой, гравийной, крупнопесчаной присадкой.
Оптимальная длина волокон, используемых в кладке и иных облицовочных работах, не превышает 0,6 см. При планировании сооружений монолитов покупают волокнистые отрезки 1,2 см. Полусухую стяжку и гидротехнические сооружения армируют фиброй 1,8 см в длину.
Замешивание производится по определенной технологии с соблюдением пропорций компонентов рабочего раствора. Изначально в бетоносмеситель помещают сухой продукт и волокна фибры, после этого заливают воду.
Нарушение пропорций недопустимо. При слишком густом растворе работа усложнится. Если после замеса его консистенция окажется жидкой, это приведет к существенной усадке, хрупкости, образованию трещин конструкции в ходе эксплуатации.
Для получения однородной смеси достаточно размешивать компоненты не более 5-10 минут. Точное время рассчитывается по формуле: к обычной продолжительности добавляется 15% времени.
Если работа требует увеличения эластичности материала, в состав включается пластификатор. Бывает, что фиброволокно затворяют в самом пластификаторе.
Когда запланирован малый рабочий объем, замес выполняют миксером. Также фибру можно добавлять в цемент после ее соединения с водой. Это способствует равномерному распределению фиброволокон в смеси.
Расход на м3 для бетона напрямую связан с видом перекрытия. Например, для пола надлежит добавлять не более 30 кг на 1 м3. Для стен объем увеличивается до 50-55 кг/м3.
Средний расход микрофибры на мешок цемента марки М200 составляет 0,15 кг. Макрофибра расходуется в объеме до 4 кг/м3 бетона. Чтобы не ошибиться при замесе, следует опираться на рекомендации производителя.
Готовый раствор подается на объект насосом. Это очень удобно при строительстве габаритных конструкций с целью ускорения рабочего процесса.
Если на поверхности застывшей смеси остаются торчащие волокна, а чистовое покрытие не предусмотрено, от них избавляются подпаливанием, используя специальное оборудование.
Когда планируется покраска или иная отделка, волоски оставляют. Они усилят сцепление основания с верхним слоем.
Волокно используют по-разному: его добавляют в напольную стяжку промышленных предприятий, часто применяют в производстве плит, строительных блочных, секционных, трубных изделий.
Волокнистая присадка применяется в изготовлении несъемной опалубки. С ее помощью создают фасадный стеклофибробетонный декор. Она используется в бетонировании дорожных полотен, производстве парапетных плит.
В работе нужно использовать качественный и сертифицированный товар от известного производителя. В ходе эксплуатации он не будет выделять токсических веществ, ухудшающих здоровье. Этот аспект особенно важен при выполнении работ внутри жилых помещений.