Все о прочности болтов
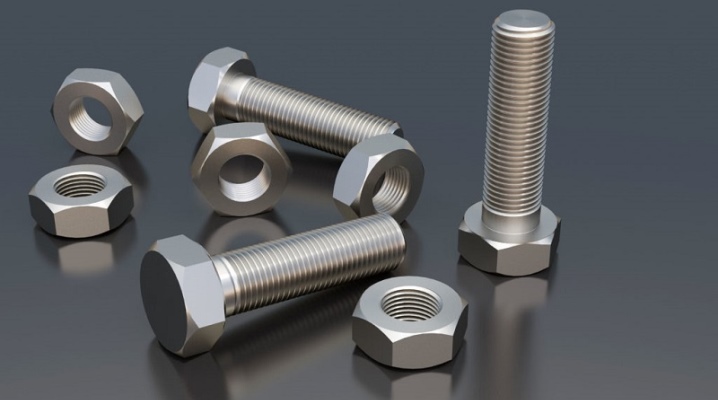
Большой ассортимент на рынке представляют крепежные составляющие. Они могут применяться как для обычного соединения различных частей конструкций, так и для того, чтобы система выдерживала увеличенные нагрузки, была более надежна.
Выбор категории прочности болтов напрямую зависит от того, с какими целями будет использована конструкция.
Основные классы
Болт представляет собой крепежный элемент цилиндрической формы с резьбой снаружи. Обычно имеет шестигранную головку, сделанную под гаечный ключ. Соединение происходит при помощи гайки либо другого отверстия с резьбой. До создания винтовых крепежей болтами называли любые изделия в форме стержня.
Конструктивное устройство болта выглядит следующим образом.
Головка
С ее помощью остальной части крепежа передается крутящий момент. Она может иметь шестигранную, полукруглую, полукруглую с винтом, цилиндрическую, цилиндрическую с шестигранным углублением, потайную и потайную с винтом формы.
Стержень цилиндрической формы
Делится на несколько видов:
- стандартный;
- для установки в отверстие, имеющее зазор;
- для монтажа в отверстие, обработанное разверткой;
- со стержнем уменьшенного диаметра без резьбы.
Гайка
Может быть следующих форм:
- круглая;
- гайка-барашек;
- шестигранная (с фасками низкими/высокими/нормальными, корончатая и прорезная).
Существует множество типов болтов, все зависит от того, какими качествами при эксплуатации должна обладать изготавливаемая конструкция. Класс прочности болтов описывает их механические свойства.
Опираясь на самые популярные таблицы, можно понять, что данный класс является основным.
Прочность — это свойство изделия, характеризующееся сопротивлением к разрушению со стороны внешних факторов. Любой производитель обязательно указывает прочность изделия для того, чтобы при монтаже или сборке было понятно, подходят ли крепежи для тех или иных случаев. Измеряется прочность двумя цифрами, разделенными точкой, либо двузначным и однозначным числом, также разделенными точкой:
- 3.6 — соединительные элементы, изготовленные из нелегированной стали, дополнительная закалка не применяется;
- 4.6 — для производства использована углеродистая сталь;
- 5.6 — изготавливаются из стали без заключительного отпуска;
- 6.6, 6.8 — метизы из углеродистой стали, без примесей;
- 8.8 — в сталь добавляются такие компоненты, как хром, марганец или бор, дополнительно происходит отпуск готового металла при температуре выше 400°С;
- 9.8 — имеет минимум отличий от предыдущего класса и более высокую прочность;
- 10.9 — для производства таких болтов берется сталь с дополнительными добавками и отпуском 340-425°С;
- 12.9 — применяется нержавеющая или легированная сталь.
Первое число означает предел прочности (1/100 Н/мм2 или 1/10 кг/мм2), то есть 1 миллиметр квадратный болта 3.6 выдержит на разрыв 30 килограмм. Второе число — это соотношение предела текучести к пределу прочности в процентах. То есть болт 3.6 не будет деформироваться до усилия 180 Н/мм2 или 18 кг/мм2 (60% от предела прочности).
Исходя из значений прочности, соединяющие болты делятся на следующие варианты.
- Функционирующие на растяжение-разрыв по внутреннему диаметру болта. Чем выше прочность крепежа, тем больше вероятность, что болт деформируется при нагрузке, то есть растянется.
- Функционирующие на срез болта по двум плоскостям. Чем меньше прочность, тем выше вероятность, что крепление разрушится.
- Функционирующие на растяжение и срез — происходит срез головки болта.
- Фрикционные — тут происходит смятие материала под крепежом, то есть функционирующие на срез, но с большим натяжением крепежей.
Предел текучести — это наибольшая нагрузка, при увеличении которой происходит деформация, в дальнейшем не подлежащая восстановлению, то есть винтовое соединение увеличится в длину после определенных действий. Чем большую тяжесть выдерживает конструкция, тем выше показатель текучести. Рассчитывая нагрузку, обычно берут 1/2 или 1/3 от предела текучести. В качестве примера можно рассмотреть кухонную ложку — если согнуть ее в одну сторону, получится другой предмет. Текучесть нарушилась — это привело к деформации, но сам материал не сломался. Можно сделать вывод, что упругость стали выше ее текучести.
Другой предмет — нож, при сгибании сломается. Следовательно, сила прочности и текучести одинакова. Изделия с такими характеристиками еще называют хрупкими. Предел на растяжение — изменение размера и формы материала под действием внешних факторов, изделие при этом не разрушается. Иными словами, это процент удлинения материала по сравнению с изначальным образцом. Данная характеристика показывает длину болта до поломки. Классификация по размерам – чем больше площадь, тем больше сопротивление скручиванию.
Длина болта выбирается в соответствии с толщиной соединяемых частей.
Крепежи делятся и по такому показателю, как точность. В производстве используются разные способы нарезки резьбы и обрабатывания поверхности. Она может быть повышенной, нормальной и грубой.
- С – грубая точность. Данные крепежи подходят для отверстий на 2-3 миллиметра больше самого стержня. При такой разности диаметров соединения могут сдвигаться.
- В – нормальная точность. Соединительные элементы устанавливаются в отверстия на 1-1.5 миллиметра шире стержня. Поддаются меньшей деформации по сравнению с предыдущим классом.
- А – высокая точность. Отверстия для данной группы болтов могут быть шире на 0.25-0.3 миллиметра. Крепежи имеют достаточно высокую стоимость, так как производят их методом точения.
Для крепежей, изготовленных из нержавеющей стали, указывают не класс, а предел прочности на разрыв, обозначение у них другое — А2 и А4, где:
- А — это аустенитная структура стали (высокотемпературное железо с кристаллической ГКЦ-решеткой);
- числа 2 и 4 — это обозначение химического состава материала.
Нержавеющие болты имеют 3 показателя прочности — 50, 70, 80. При производстве высокопрочных болтов используют сплавы с большей твердостью и прочностью. Такие материалы стоят дороже углеродистой стали. Класс прочности варьируется – 6.6, 8.8, 9.8, 10.9, 12.9. Также для повышения показателей проводится этап термической обработки, которая изменяет химический состав и строение материала. Возможная эксплуатация в условиях температур ниже 40°С — имеет обозначение У. 40-65°С маркируется как ХЛ.
Твердость болтов — это способность материала сопротивляться проникновению в его поверхность другого тела. Характеристика твердости болтов измеряется по Бринеллю, Роквеллу и Виккерсу. Испытания твердости по Бринеллю проводятся на твердомере, индетором (вдавливаемый предмет) служит закаленный шарик, диаметр которого равен 2.5, 5 или 10 миллиметров. Размер зависит от толщины проверяемого материала. Вдавливание происходит в течение 10-30 секунд, время также зависит от испытуемого материала. Затем полученный отпечаток при помощи лупы Бринелля измеряют в двух направлениях. Соотношение приложенной нагрузки к поверхности отпечатка и есть определение твердости.
Метод Роквелла также основан на вдавливании. В качестве индетора для твердых сплавов выступает алмазный конус, для более мягких — шарик из стали диаметром 1.6 миллиметров. В данном методе испытание проводится в две фазы. Сначала прикладывается предварительная нагрузка для плотного соприкосновения материала и наконечника. Затем в течение небольшого времени идет основная нагрузка. После того как рабочую нагрузку убирают, измеряется твердость. То есть расчеты будут происходить по глубине, на которой остался индетор, с приложенной предварительной нагрузкой. В данном методе выделяется 3 группы твердости:
- HRA — для особо твердых металлов;
- HRB — для относительно мягких металлов;
- HRC — для относительно твердых металлов.
Твердость Виккерса определяется по ширине отпечатка. Вдавливаемым наконечником служит алмазная пирамида с четырьмя гранями. Измеряется расчетом соотношения нагрузки к площади полученной отметки. Замеры производятся под микроскопом, установленным на оборудовании. Данный метод отличается повышенной точностью и сверхчувствительностью. Применяемые способы измерения по ГОСТ в советские времена не позволяли определять все максимально допустимые нагрузки на крепежи, поэтому изготавливаемые материалы были низкого качества.
Основные виды болтов
- Лемешный. С его помощью крепятся подвесные тяжелые сооружения. Чаще всего применяется для сельского хозяйства.
- Мебельный. Главное отличие – резьба наносится не по всему стержню. Головка гладкая – делается это для того, чтобы болт не выступал над плоскостью. Помимо производства мебели, данный крепеж нашел свое применение в строительстве.
- Дорожный. Используется при установке ограждений. Его отличает головка полукруглой формы, под которой находится подголовок в виде квадрата. Благодаря такой конструкции элементы прочно фиксируются.
- Машиностроительный. Самый популярный вид, применяемый в производстве автомобилей.
Колесные болты отличаются высокой прочностью и устойчивостью к воздействию неблагоприятных факторов.
- Путевой. Используется при строительстве железных дорог, обычно с его помощью соединяют части рельс. Резьба наносится меньше, чем на половину стержня.
Маркировка
Все крепежные элементы маркируются согласно стандартам:
- ГОСТ;
- ISO — система, введенная в большинстве государств с 1964 года;
- DIN — система, созданная в Германии.
С учетом всех требований и стандартов на головку болта наносят следующие обозначения:
- класс прочности сырья, из которого был изготовлен крепеж;
- знак завода производителя;
- направление резьбы (обычно обозначается только левое направление, правое не маркируется).
Нанесенные знаки могут быть как углубленными, так и выпуклыми. Их размер определят сам завод-изготовитель.
В соответствии со стандартами ГОСТ, на болты наносятся следующие обозначения.
- Болт — наименование крепежа.
- Точность болта. Она имеет буквенную расшифровку А, В, С.
- Третьей идет цифра, обозначающая исполнение. Оно может быть 1, 2, 3 или 4. Первое исполнение не всегда указывается.
- Буквенное обозначение вида резьбы. Метрическая — М, коническая — К, трапецеидальная — Тр.
- Размер диаметра резьбы, обычно указывается в миллиметрах.
- Размер шага резьбы в миллиметрах. Он может быть крупный или основной (1,75 миллиметров) и мелкий (1,25 миллиметров).
- Направление резьбы LH — это левое направление, правосторонняя резьба никак не обозначается.
- Точность резьбы. Она может быть точной — 4, средней — 6, грубой — 8.
- Длина крепежа.
- Класс прочности — 3.6; 4.6; 4.8; 5.6; 5.8; 6.6; 6.8; 8.8; 9.8; 10.9; 12.9.
- Буквенное обозначение С или А, то есть применение спокойной или автоматной стали. Данное обозначение подходит только для болтов прочностью до 6.8. Если прочность выше 8.8, то вместо данной маркировки будет наноситься марка стали.
- Номер от 01 до 13 — этими числами обозначается вид покрытия.
- Последним идет также цифровое обозначение толщины покрытия.
Как узнать?
Главные параметры для измерения размеров креплений — это длина, толщина и высота. Чтобы определить данные параметры, нужно сначала визуально понять, какой тип болта имеется. Диаметр крепежа можно измерить с помощью штангенциркуля или шаблонной линейки. Измерение точности проводится комплектом калибровки ПР-НЕ — проход-не проход, то есть одна составляющая навинчивается на анкер, вторая – нет. Длина также измеряется штангенциркулем или линейкой.
Измерения винтов имеют обозначения:
- М — резьба;
- D — размер диаметра резьбы;
- P — шаг резьбы;
- L —размер болта (длина).
Диаметр резьбы измеряется аналогично измерению параметров болта. Диаметр резьбы гаек определить сложнее. Обычно маркировка характеризует наружный диаметр болта, который будет ввинчиваться в гайку, то есть отверстие гайки будет меньше. Точность диаметра можно измерить также с помощью набора ПР-НЕ. Здесь стоит помнить о том, что размер гайки может быть уменьшенным, нормальным и увеличенным.
Во время стройки соединение конструкций в основном происходит при помощи болтовых соединений. Главное их преимущество — это несложный монтаж, особенно если брать для сравнения сварочные соединения. Формулы, применяющиеся для подсчета соединения на разрыв, зависят от материала основания (бетон, сталь, растворы и комбинации материалов).
Расчет анкерных крепежей на разрыв происходит уже на объекте, в соответствии с прилагаемыми документами.
Главное условие установки крепежей — это выдержка болтами общей конструкции. Самая высокая несущая способность у анкеров из легирующей стали повешенного качества. Сила дополнительных воздействий может быть динамической, статической и максимальной. Масса дополнительной нагрузки не превышает 25% от силы разрыва стержня болта.
Способ крепления болтами стал очень популярным в современном мире. Опираясь на все характеристики, можно выделить моменты, на которые стоит обратить особое внимание при выборе:
- сфера деятельности, где будет применяться крепление;
- конструкция головки;
- используемый материал;
- прочность;
- есть ли дополнительное защитное покрытие;
- маркировка по ГОСТ.
В следующем видео вас ждет дополнительная информация о классах прочности в маркировке болтов.