Заточка резцов для токарного станка
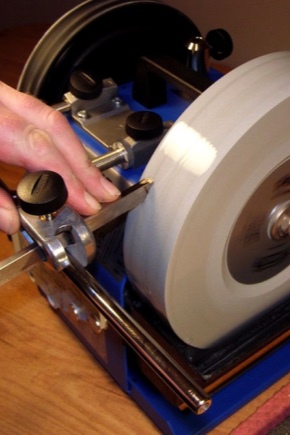
Заточка резцов для токарного станка – естественная и необходимая стадия работ, когда из-за периодической и интенсивной нагрузки они затупились. Затупленные лезвия режут во много раз хуже, скорость и эффективность работы стремительно падает, и настаёт момент, когда она останавливается.
Когда нужна?
Трение стружки о режущие грани резака – неотъемлемый процесс. Идеального разрезания и спиливания, стачивания рабочей детали не бывает. В процессе любой токарной работы обрабатываемый материал медленно, но верно воздействует на инструменты. Трение всегда сопровождается выделением тепла – часть механической энергии превращается в тепловую. При повышенной температуре резак изнашивается. Работа затупленным инструментом ставит под вопрос качество и долговечность вытачиваемых деталей и всего устройства в целом, где они используются. Чтобы производить подтачивание режущих кромок резака своевременно и адекватно, обратите внимание на степень износа.
Тип, вид резака |
Вытачиваемый материал |
Род, разновидность работ |
Предельный износ по задней грани, мм |
|
Для быстрорежущих резаков |
Для твердосплавных инструментов |
|||
Проходной, подрезной, растачивающий |
Углеродистая и легированная сталь |
Черновая |
1,5… 2 |
1… 1,4 |
Чистовая |
0,4… 0,6 |
|||
Жаропрочные и нержавеющие стали и сплавы |
Черновая |
1 |
1 |
|
Чистовая |
||||
Чугун |
Черновая |
Произвольный |
0,8… 1 |
|
Чистовая |
0,6… 0,8 |
|||
Отрезной, прорезывающий |
Сталь и ковкий чугун |
Общая |
0,8… 1 |
0,8… 1 |
Серый чугун |
1,5… 2 |
|||
Фасонные |
Сталь |
Общая |
0,4… 0,5 |
Произвольный |
Резьбовые |
Сталь |
Черновая |
2 |
0,8 |
Чистовая |
0,3 |
|||
Чугун |
Черновая |
Произвольный |
1 |
|
Чистовая |
Соблюдение приведённых в таблице нормативов по необходимости заточки способно продлить срок службы инструмента. В результате интенсивной работы в течение многих часов, многочисленных заточек режущие слои истончаются, и резак отправляется в утиль.
Какие инструменты и заточные станки можно использовать?
Инструментарий для затачивания резаков токарного станка представлен различными приспособлениями.
-
Мусаты – стальной стержень с рубчиком. Рукоятка позволяет управлять углом заточки, выставляя правильный его допуск.
-
Точильные бруски и круги – можно заточить без использования привода. Чаще всего количество проводок инструмента по абразивной поверхности круга – порядка 10. Мастер обладает некоторой сноровкой, позволяющей оперативно и быстро заточить резец.
-
Механизированные затачивающие приводы. Выставляется угол наклона резца, чтобы режущее ребро быстро и высококачественно подточилось.
-
Электроинструменты – например, болгарка с затачивающим кругом. В качестве такого инструмента применяется диск с алмазным напылением. Алмаз – один из наиболее твёрдых материалов, способный заточить даже победитовый резак. Он позволяет заточить на 30% больше инструментов, чем обычный пильно-шлифовальный диск. Альтернатива – наждачный круг: им не менее эффективно затачивают быстрорежущую сталь.
Наточив затупившийся резак, работу продолжают с того места, где она была прервана.
Способы заточки
Основная часть резака – режущая – рассчитана на металл или дерево. Сходство между тем и другим инструментом имеется – конструктивное. Крепление присутствует на каждом таком станке. Отслеживание стачивания лишнего материала с обрабатываемой деталью производится разными методами, определяющими вид резака. Последний, в свою очередь, отличается числом рабочих поверхностей – как правило, их не менее двух. Характеристики каждой из них зависят от ширины и формы резца.
Выбрать подходящую режущую кромку можно, опираясь на виды предстоящих работ по обточке деталей. Так, для обточки деревянных деталей и нарезки резьбы на стальных понадобятся резцы, существенно отличающиеся друг от друга. От вида резца зависит метод его затачивания.
Плоские прямые резцы обтачиваются исходя из обработки ими различных поверхностей, создания пазов и выемок в простом исполнении. С их помощью создаются прямоугольные отверстия, при этом ширина лезвий колеблется в пределах 4-40 мм. Угол заточки – 25-40 градусов. Затачиваются они по простой схеме.
-
Специалист выравнивает погнутый торец.
-
Обработка выполняется с помощью аккуратной заточки. Не рекомендуется стачивать большее количество стали, чем задумано.
-
Ручка устанавливается последней. В станке зажимают 2-3 прямых плоских резца – отдача от станка на практике окажется оптимальной.
-
Каждый резец затачивается по отдельности.
Косые прямые резцы точатся с двух сторон, но по упрощённой схеме.
На заточке выбираются нужные значения ширины – порядка 4-40 мм. Толщина также устанавливается оптимально.
-
Обтачивается один из углов, соотношение не более 75 градусов.
-
После грубой обточки производится точная, под втрое меньшим углом.
При обтачивании следите за тем, чтобы режущая кромка не отклонялась, иначе заточка окажется некачественной. Она должна сохранять симметричность.
Отрезные кромки обладают угловым резцом. Заточка производится с одной стороны, а не с обеих. Посредством обрезной кромки выполняются заготовки и вытачиваются начерно деревянные и металлические комплектующие. Методика заточки сводится к следующему:
-
вырезание угла торца в 45 градусов, превышать эту величину нельзя;
-
более точное обтачивание под углом 30-40 градусов.
Выходить за рамки угла обточки нельзя – инструмент может оказаться либо неэффективным, либо при серьёзной нагрузке затупится за считаные секунды.
Полукруглые плоские режущие кромки обтачиваются с помощью выемки в виде полукруга. Стадии затачивания этих резцов следующие:
-
обтачивание элементов посредством наждачки;
-
проверка торца на соответствие исходной (штатной) форме;
-
затачивание (точное) кромки под углом в 20-45 градусов.
Для мастеров, чья работа – форменные выемки и пазы, декорация деталей, представлены несколько вариантов заточки.
Желобчатые резаки обладают отличиями, ставящими их на особый уровень. Режущие кромки напоминают настоящий жёлоб, отчего их ширина колеблется в пределах 3-х см. Они применяются для создания рельефа-впадины и в качестве инструмента, позволяющего выполнить грубую обработку древесины. В гаражных условиях их изготовление затруднительно – к этому варианту прибегают при их невозможности быстро приобрести в ближайшем хозяйственном или строительном магазине. Изношенная конструкция резака всё ещё годится в качестве основы. Заточка делается по следующей схеме:
-
торец обрабатывается до 10 см, в результате образуется полукруг;
-
остальной слой стали снимается методом обрезания;
-
протачивается выемка – с помощью отдельного инструмента;
-
нижняя сторона, находящаяся на выпуклой поверхности, затачивается под углом в 40 градусов.
Точение резаков в состоянии выполнять начинающий мастер, не имеющий большого опыта, чего не скажешь о выделке желобчатого резака с нуля. Угол заточки может отличаться до 7 градусов – скорость, оперативность высококачественной резки деталей не пострадает.
Техника безопасности
Не стоит пренебрегать правилами ТБ – при работе с металлом и стружкой потребуются защитные очки, каска, перчатки или варежки из толстой и грубой материи. Дотрагиваться до заточенного резака и обработанных деталей можно лишь после полного их остывания.
Обточка резака конкретного вида (или определённой разновидности) осуществляется лишь оговоренным для него видом. После заточки нельзя охлаждать резцы водой – они станут хрупкими, так как сталь «отпускается». Но при обточке можно заранее подавать воду – резак при этом почти не нагреется. Кромки обтачиваются в следующем порядке: задняя – главная – боковые. Точная огранка может проводиться при смачивании в керосине, а шлифовка – при помощи мелкозернистой наждачки или такой же абразивности бруска.
Чтобы резец не затуплялся преждевременно, его во время работы непрерывно охлаждают, либо устраивают периодические перерывы – это не даст ему перегреваться.
Станок, на котором производится заточка резака своими руками, должен обладать возможностью регулировки угла заточки. В крайнем случае применяются подкладки. Уровень оси вращения точильного привода и местоположение затачиваемого резца не должны различаться более чем на полсантиметра.
Параметры затачивания резцов отслеживаются посредством вышеприведённых табличных нормативов. В расчёт берётся характер обработки (грубая или точная), материал (сорта сталей и другие сплавы, из которых сфабрикован резак), угол затачивания, показатель зернистости точильного круга.
Направление вращения точильно-кругового камня также выставляется с учётом параметров резака, его расположения относительно привода. Затачивание металла сопровождается отлетанием отстающих по ходу обточки частиц. Придавив их точильным кругом в процессе затачивания, минимизируют риск их разлёта во все стороны.
Не рекомендуется для малогабаритных резаков использовать привод с большим разбросом по мощности. Резак попросту может сломаться. Мощность привода токарного станка должна согласовываться с габаритами режущего инструмента.