Все о сварке
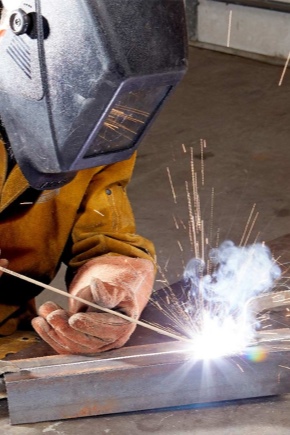
Знать все о сварке необходимо, хотя бы в общих чертах, всем руководителям, заказчикам и тем, кто оценивает результат. Существуют различные виды сваривания, включая орбитальную, электрошлаковую и диффузионную методики, но их характеристики знакомы неспециалистам недостаточно. Знать только лишь сварку автогеном, если коротко, то это совершенно несерьезно в XXI веке.
Что это такое?
История развития сварочного дела не менее увлекательна, чем иной захватывающий роман. Можно считать даже, что сварочное дело — практически ровесник цивилизации. Уже при первых кузнечных обработках были введены практики сварки металла давлением. Но, разумеется, за минувшие века и тысячелетия она существенно развилась и усовершенствовалась. Кузнечная сварка и пайка были неотъемлемой частью повседневной жизни вплоть до конца XIX века, а в отдельных местах активно использовались вплоть до середины ХХ столетия.
Но научное и технологическое развитие заложило основы множества видов сварки, о которых в прошлом можно было только мечтать. Раньше всего появилась практика сваривания электрическим током. Позже были внедрены различные газовые и модифицированные электрические, плазменные и ультразвуковые способы. На службу сварщикам поставили взрыв и мощное давление, ультразвук и напор воды, лазерные аппараты и роботизированные системы. Однако суть процесса остается той же самой, что и 5000 лет назад – имеется 2 или более фрагмента металла или сплава, которые требуется качественно соединить.
Виды
Среди способов и типов сварочного дела есть такой известный (даже непрофессионалам) вариант, как сваривание автогеном. Суть его очень проста: за счет сжигания газа возникает очень сильно нагретая струя пламени. Температура в ней превышает 3000 градусов. Ни один из используемых в быту или на транспорте металлов и сплавов не выдерживает столь сильного нагрева. Потому можно говорить, что автогенная сварка универсальна.
Наиболее сложная составная часть «автогена» – это специальный резак. Промышленное оборудование такого типа может оперировать самыми разными газами. Но в большинстве случаев используют все же проверенные ацетилен и пропан-бутан. Они на деле доказали пригодность для сварки почти любых конструкций и изделий.
Необходимо подчеркнуть, что, несмотря на доступность и сравнительную простоту, работать с автогеном можно только по строго выверенной схеме — отклонение от нее приводит к ухудшению качества.
Говоря про плюсы и минусы сваривания ацетиленом, надо указать на:
- автономность от электросетей и электрооборудования (но иногда без его употребления все же не обойтись, если решается ответственная или «очень тонкая» задача);
- изменение степени прогрева сварочной ванны только лишь за счет корректировки расположения горелки;
- легкость профилактики прожогов — за счет того же самого маневра;
- мобильность техники;
- взрывоопасность, пожароопасность и токсичность газа;
- сравнительно малую производительность процесса;
- высокую площадь нагрева (много энергии тратится зря, да и напрасный разогрев металла отрицательно сказывается на нем);
- обязательную высокую квалификацию исполнителя;
- малую пригодность для крупного серийного производства.
Значимое место в классификации сварочных методик занимает орбитальная сварка. Нет, ею занимаются не на орбитальных станциях. Речь идет о том, что электрическая дуга описывает орбиту вокруг обвариваемой трубы. Подобный вариант считается технически сложным – самые опытные сварщики уважают тех, кто владеет подобной технологией. Преимущество в том, что можно получить очень надежный шов вне зависимости от сечения и размера соединяемых частей.
Все оборудование для орбитальной сварки полностью автоматизировано. В его состав входят:
- электроды особо тугоплавкие из вольфрама;
- «голова» (с системой фиксации на трубе);
- аппарат подачи защитного газа;
- управляющая электронная система.
Один из наиболее интересных типов — это художественная сварка. Тут различение идет не по используемому аппарату (применяют тот, который удобнее в данный момент), а по эстетическому совершенству создаваемых конструкций. Сварщик-художник обязан делать максимально тонкие, но при этом исключительно прочные и стабильные швы. Методики художественной сварки подходят для формирования:
- калиток;
- заборов;
- ворот;
- декоративных фигур;
- предметов обихода;
- фасадных конструкций и ряда других вещей.
В работе с трубами сейчас все чаще применяется индукционная методика. Это электросварка, по сути, но с важной особенностью — нужна подача высокочастотных токов. Методика позволяет работать с самыми разными марками легированных сталей. Потребление электроэнергии на один и тот же объем обрабатываемого металла заметно меньше (однако растекание тока по всей поверхности обесценивает этот результат). Чаще всего применяются контактные токопроводы.
Кольцевой индуктор может находиться внутри обрабатываемых заготовок или снаружи их. Иногда применяют и стержневые индукторы. Они позволяют существенно сократить расход тока. Еще одно преимущество — за счет использования нескольких индукторов можно варьировать степень прогрева. Необходимо учесть, что выдержка равномерного зазора — одна из самых сложных проблем.
Экструзионная методика применяется главным образом при сваривании полимеров. Она пригодна лишь в том случае, если заготовки сделаны из идентичных термопластов.
Малейшее несходство состава оборачивается непреодолимыми трудностями. Обеспечивается соединение толстостенных трубчатых деталей. Темп и качество сварки будут весьма велики.
Особенности:
- свариваемые поверхности должны формировать «канавку» или «угол» между листами;
- оказание давления идет через присадку (обычно это сварочный башмак);
- в некоторых случаях внутрь экструдера встраивают термофен, эффективно прогревающий воздух.
Термические классы
Дуговая
Именно этот вид сварочных технологий чаще всего «работает» на строительных площадках и на промышленных объектах. Электрический разряд прогревается до такой степени, которая совершенно недоступна даже самым лучшим газовым горелкам. Под влиянием дуги образуется сварочная ванна, при последующем застывании которой генерируется сварной шов. Но за этой кажущейся простотой стоит очень тщательная работа, а ошибка сварщика может привести к очень неприятным последствиям
Дуговая сварка бывает:
- ручной;
- частично автоматизированной;
- полностью автоматизированной (чем выше степень автоматизации, тем больше требования к квалификации исполнителей и качеству оборудования).
Газовая
Существуют различные методы сваривания горючим газом. Но все они, какой бы газ не использовался, и какая бы задача не решалась, однозначно опережают электросварку по мобильности и гибкости. Вести работу можно практически в любом месте, где удастся поставить баллоны, протянуть шланги. При этом, однако, даже самое массовое сочетание ацетилена и кислорода дороже, чем электричество. Другие газы стоят еще больше.
Важно — газовая сварка гораздо результативнее дуговой по отношению к:
- медным;
- свинцовым;
- чугунным;
- латунным изделиям и конструкциям
Лучевая
Ее полное название — электронно-лучевая сварка. Как нетрудно догадаться, тут применяется энергия электронных лучей, вырабатываемых внутри катодной трубки. Подобный метод появился относительно недавно, но быстро совершенствуется, в ближайшие годы сфера его применения будет только расширяться. Поскольку электронные лучи очень сильно задерживаются воздухом, высокая эффективность работы достигается только в вакуумных камерах.
Разумеется, что это сильно ограничивает возможности выполнять задание вне оборудованных промышленных площадок.
Термитная
Этот метод применяют, когда надо работать вне обустроенного населенного пункта, а газовая сварка почему-либо оказывается невозможна. Нагрев обеспечивает термит (отсюда и название), то есть комбинация различных веществ в виде порошка. При его сжигании выделяется огромное количество тепла. Температура при розжиге за короткий срок поднимается до 1350 градусов. Добиться воспламенения термитной смеси можно:
- при помощи взрывающегося пиропатрона;
- коротким, но мощным электрическим разрядом;
- за счет особого инициирующего шнура.
Важно: для реакции нет необходимости получать атмосферный кислород. Необходимое количество окислителя есть непосредственно в составе смеси. Потому сварка в среде инертного газа реализуется гораздо легче, чем это можно вообразить. Основные требования к сварочному процессу закреплены в ГОСТ 2016 года.
Термитную сварку широко применяют в самых разных отраслях машиностроения.
Электрошлаковая
Несмотря на кажущееся странным и даже «мусорным» название «электрошлаковая сварка» – весьма полезная процедура. Подобная методика позволяет сваривать заготовки и конструкции практически любой толщины, на что РД (ручная дуговая) методика совершенно неспособна. Ток подается сквозь ванну из расплавленного шлака. В большинстве случаев работают «в нижнем положении», потому что так максимально удобно. Для электрошлаковой сварки применяют:
- плавкие мундштуки;
- электроды на основе проволоки;
- крупные по сечению электродные инструменты.
Электрошлаковая сварка гарантирует очень высокую производительность труда сварщика. При этом также стоит отметить:
- внушительную экономию на флюсе, которого требуется немного;
- понижение расхода тока в разы по сравнению с электродуговой флюсовой и ручной электросваркой;
- минимизацию сварочных дефектов (разумеется, при правильном выполнении процедуры);
- обязательную дальнейшую обработку шва при высокой температуре (иначе оптимальные эксплуатационные параметры не восстановятся).
Электрошлаковую сварку (ЭШС) применяют, чтобы работать с:
- отливками и поковками;
- титаном и сплавами на его основе;
- различными марками жаропрочной стали;
- металлом толщиной от 2 до 300 см;
- сплавами на основе никеля.
Завершим характеристику сварки электрической обратноступенчатым методом. Суть проста: шов сначала делят на последовательные участки. Затем их один за другим обваривают, двигаясь по направлению уменьшения длины шва. Важно: выделять следует строго одинаковые по размеру участки.
Подобная методика призвана сократить риск коробления и образования иных деформаций, которые очень портят жизнь сварщикам.
Термомеханические классы
Кузнечная
Подобная методика рекомендована для работы с низкоуглеродистыми сталями (черным металлом). Использование ее для высокоуглеродистого металла практически невозможно. Кузнечная сварка практикуется уже несколько тысяч лет, за это время, конечно, она была отточена до мелочей. Этот метод применяют, чтобы:
- изготавливать скульптуры и многие другие декоративные изделия;
- выполнять срочный ремонт частей различных машин;
- производить плуги, топоры и другие подручные сельхозинструменты;
- получать мелкие водосточные трубы.
Контактная
Поверхности, которые надо соединить, одновременно прогревают и сдавливают. Обработать единственное соединение удается за доли секунды. При любых других методах сваривания о подобном нечего и мечтать. Отпадает необходимость использовать кислород, защитный газ, вакуумные камеры, присадки и электроды. Все относительно просто и экологически чисто, однако оборудование стоит дорого и рассчитано, как минимум, на 1000 А.
Диффузионная
Знающие физическую терминологию сразу поймут, что речь идет о соединении за счет перемешивания слоев на молекулярном уровне. В большинстве случаев это обеспечивается индукционным нагревом. Сварка ведется при температуре, которая обеспечивает быстрое пластическое деформирование. Под давлением поверхностный контакт идет максимально плотно. Лучше давление поддерживать на уровне предела текучести вещества.
Часто практикуется контролируемая атмосфера на основе:
- гелия;
- аргона;
- очищенного азота;
- чистого водорода;
- комбинации 92-94% азота с 6-8% водорода.
Механические классы
Сварка трением
Этот вид сварочных работ был изобретен в нашей стране, в середине 1950-х годов. Его характеристики наилучшим образом подходят для авиастроения и строительства автомобилей. Сварка трением — примерно то же самое, что и сварка давлением. Трущиеся поверхности прогреваются, что обеспечивает необходимый тепловой импульс. Максимальное усилие всегда развивается в самом конце, когда идет проковка.
Важно: все те пленки жира, масла, которые оставались на обрабатываемых поверхностях, в итоге исчезают все равно, потому можно не опасаться проблем из-за не слишком качественной подготовки.
Холодная
Такое название имеет особо прочный тип клея. Стоит понимать, что того же качества, что и «горячий» метод обеспечить нельзя. Есть двухкомпонентные и однокомпонентные составы. Также выделяют:
- жидкие;
- пластичные;
- универсальные типы.
Специалисты рекомендуют:
- защищать посторонние поверхности малярным скотчем;
- тщательно дозировать состав;
- предварительно убирать всю пыль и грязь.
Ультразвуковая
Высокочастотные звуковые колебания провоцируют напряжение, превосходящее постепенно предел упругости. Отсутствие сильного нагрева — явный плюс. Можно спокойно сваривать металлы различного состава. Обеспечивается успешное приваривание тонких и особо тонких заготовок. Процедура легко автоматизируется.
Сварка ультразвуком:
- производится очень быстро;
- подходит для полистирола и других полимеров;
- позволяет создавать нетканые материалы;
- сильно зависит от коэффициента затухания колебаний в материале;
- дает возможность соединить пластмассу с металлом.
Сварка взрывом
Подобная технология применяется для получения биметаллических заготовок. Допускается работа с самыми разными материалами. Важно: точных расчетов и четких режимов тут быть не может. Причина проста — сам подход не разработан до конца. Контроль взрывной волны очень сложен, приходится проводить множество экспериментов, прежде чем будет накоплен необходимый опыт.
Сварка взрывом возможна и в воздушной, и в вакуумной среде. Скорость передвижения пластин достигает нескольких сотен метров за секунду. Взрыв дает возможность выполнять плакирование сталей с исключительными свойствами. Еще одно важное преимущество — возможность выработки заготовок неограниченного масштаба. Однако автоматизировать сварку взрывом на 100% нельзя.
При этом она потенциально опасна для присутствующих сотрудников.
Процесс
Сварка своими руками в квартире или гараже может быть выполнена в очень большом количестве случаев. Но прежде чем браться за работу, ее следует основательно изучить, ознакомиться с рядом тонкостей, подстерегающих в различных случаях. Распространенной ошибкой многих новичков является мысль, будто они могут выполнить соединения без чертежей, полагаясь только на свой небольшой опыт и интуицию. Что характерно, профессионалы высокого класса так никогда не поступают. Наоборот, они внимательно сверяют все чертежи и технические задания, консультируются при необходимости с другими людьми.
При сварке металла могут быть различные дефекты производства работ. Любой специалист обязан знать их все и учитывать меры профилактики, понимать, как бороться с такими проблемами. Основную опасность представляют:
- нарушения целостности металлического слоя;
- плохая форма шовного валика;
- слишком крупные или слишком мелкие зерна в области фазового перехода;
- растрескивание (из-за скверного температурного режима);
- подрезы (на фоне чрезмерно высокого напряжения дуги либо сдвига расплавных ванн).
На крупных предприятиях все чаще применяют сварочные каретки. Подобное оборудование часто применяют на судоверфях. Некоторые экземпляры оснащаются парой горелок, что существенно увеличивает эффективность использования техники. Что касается разделки кромок изделия под сварку, то такая процедура очень важна и при ручных, и при промышленных работах. Только так удается обеспечить надежный контакт. Точные требования к разделке кромок закрепляются в ГОСТ на специфический формат работ.
Часто сварщики пользуются керамическими подкладками. Подобные изделия облегчают сваривание сложных соединений в труднодоступных участках. Благодаря подкладке отпадает необходимость в сложной подготовке и последующей обработке. Но критически важно качество подложки! Также в ряде ситуаций используется универсальная сварочная плита, обеспечивающая точное позиционирование больших и мелких деталей.
В качестве присадки, в том числе при сварке коробки «автомат», наконечника рулевого, блоков ДВС можно применять сварочную проволоку «прима». Она гарантирует:
- добротное омеднение;
- стабильный химический состав;
- эффективную обработку низколегированных сплавов в углекислотном облаке.
Для подключения к кислородному баллону, при газовой сварке можно использовать только рукав, рассчитанный на подходящий уровень давления. Осмотр этих шлангов производится ежедневно до начала работы и при ее окончании. Если площадку на какое-то время оставляли без присмотра, осматривать все нужно заново. К сведению: по возможности лучше отказаться от использования карбида, а приобретать ацетилен заводского производства — так гораздо безопаснее.
При отборе сварочного преобразователя не стоит ориентироваться на надежность — все равно она меньше, чем у других устройств для электросварки. Однако в пользу этой техники свидетельствует невосприимчивость к просадкам напряжения. Подобное обстоятельство очень важно на стройплощадках. Напоследок стоит разобрать несколько тонкостей работы в конкретных случаях. В ряде случаев приходится сваривать трубы с различным количеством отводов – это реально трудная задача.
Обязательно требуется:
- контролировать величину сдвига кромок;
- центрировать изделия;
- варить первый шов на постоянном токе.
Достаточно часто нужна сварка силумина. Его обрабатывают строго под аргоновой защитой! Обработке подлежит лишь силумин литейных марок, но не иных разновидностей. Сварка потолочного шва ведется на ограниченном токе, потому важно принимать меры, чтобы непроваров не было. Электрод ведут немного вбок, чтобы ослабить растекание металла, а края заготовок зачищают максимально хорошо.
Сварка угловых швов может вестись и в горизонтальном размещении. Следует соединять конструкции строго под 90 градусами. Если толщина менее 1,4 см, скашивать кромки не требуется. А вот при толщине свыше 4 см требуется уже двусторонний скос. Создавая тавровое соединение, нужно старательно избегать появления:
- пор;
- слабо проваренных участков;
- кратеров.