Обзор лазерных станков для резки металла и их выбор
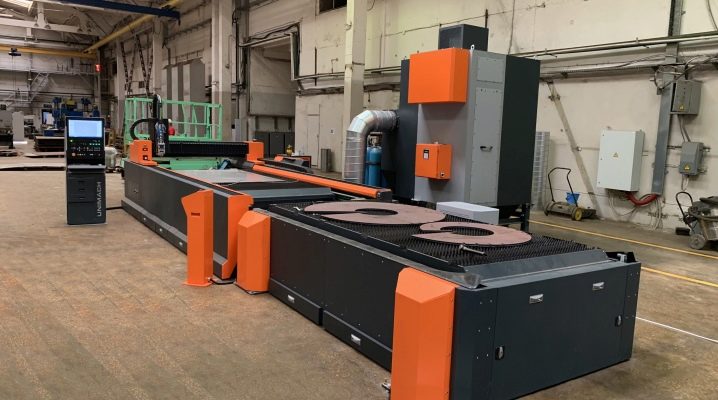
Лазерное оборудование для резки по металлу используется в самых разных сферах промышленности: в машиностроении, металлургии и изготовлении мебели. Такая популярность объясняется тем, что оно позволяет создавать детали усложненной формы с повышенным уровнем точности. О подобном оборудовании и пойдет речь в нашей статье.
Конструкция и принцип работы
Лазерные резаки для металла выполняют три основные функции:
- гравировка: нанесение картинки, текста и даже фотографии на металлическую поверхность;
- лазерная резка;
- криволинейный раскрой.
Во всех случаях формируется шаблон, по которому модуль числового программного управления задает параметры реза. В результате выходит идеально точное изделие.
Главным преимуществом работы лазерных станков является высокая производительность: за сравнительно небольшой период времени можно обработать большое количество изделий.
Конструкция любого лазерного резчика предусматривает несколько блоков:
- излучатель — отвечает за генерацию потока фотонов либо узконаправленного лазерного импульса;
- блок перемещения газа — предназначается для выдува раскаленного металла из рабочей зоны и охлаждения излучателя;
- привод — применяется для перемещения излучателя по обрабатываемой поверхности;
- рабочий раскроечный стол — именно на нем размещается заготовка, при этом стол может быть сменным;
- модуль ЧПУ/АСУ.
Принцип работы таких станков базируется на генерации лазерной трубкой узкого луча, выполняющего обработку металла. В результате контакта луча с поверхностью обрабатываемого материала возникает высокотемпературное воздействие, оно и позволяет выполнять гравировку или резку металла. При этом поток газовой смеси выдувает слой расплавленного материала, благодаря чему обеспечивается рез высокого качества. Такие станки могут использоваться для работы со всеми типами листовых сталей, а также с цветными металлами и их сплавами.
Описание видов
Суть работы любого лазерного резчика состоит в фокусировке узконаправленного луча, в результате которой энергия концентрируется на поверхности обрабатываемого материала. Диаметр такого луча не превышает десятых долей миллиметра, благодаря чему обеспечивается минимальная толщина реза. Ход расплавления и последующая трансформация структуры металла происходят как следствие доведения мощностных характеристик лазерного луча до определённых параметров. В зависимости от механизма работы выделяют четыре основные разновидности таких станков.
Газовые
Лазерная резка металла может осуществляться в кислородной или азотной среде, выбор зависит от особенностей металла, подлежащего обработке. Так, в результате кислородного воздействия запускаются экзотермические реакции, тепловая энергия которых позволяет выполнять рез довольно толстых листов из низколегированной и углеродистой стали.
Не рекомендуется резать в кислороде гальванически покрытые либо оцинкованные поверхности. В этом случае срез получается неровным, к тому же возрастает риск образования окалины. При резке нержавеющей или высоколегированной стали нежелательно допускать окисление места среза. Именно поэтому при работе с такими металлами востребованы инертные газы, чаще всего азот.
Также азот применяется в случаях, когда впоследствии срезы будут окрашиваться. Если использовать кислород, то окисление металла приведет к снижению качества колеровки.
Для резки алюминия можно использовать любую газовую среду. А вот для работы с титановыми сплавами нельзя использовать ни тот, ни другой, поскольку оба газа начинают абсорбироваться металлической поверхностью и образуют ломкий слой. Для этого материала предпочтение стоит отдавать лазерным устройствам, работающим в среде гелия или высокоочищенного аргона.
В целом же любые газовые лазерные резаки дают максимальную волну излучения, поэтому они востребованы при обработке листового проката максимальной толщины.
Оптоволоконные
Высокую эффективность и производительность оборудования обеспечивают оптоволоконные лазерные устройства, они часто реализуются в виде мини-станков. Имеют следующие преимущества.
- Высокое качество луча. Линия реза более тонкая, а пятно имеет меньший размер, что в целом повышает эффективность работы.
- Высокая скорость резки. В сравнении с газовыми она больше в два раза.
- Долговечность. Применение профессионального волоконно-оптического лазера позволяет обеспечить стабильную производительность до 100 тысяч часов работы оборудования.
- Повышенная эффективность. Результативность фотоэлектрического преобразования при оптоволоконной резке соответствует 30%, а это в 2-3 раза больше, чем при проведении лазерной резки в газовой среде.
- Низкая себестоимость использования. Потребляемая мощность оптоволоконных установок не превышает 30% от лазерной резки в газовой среде.
- Минимальные расходы на техобслуживание. Отсутствие необходимости в отражающих объективах позволяет сэкономить немало средств на обслуживании станка.
- Эксплуатация такого оборудования не составляет особой сложности. Благодаря передаче оптического волокна отсутствует необходимость в настройках параметров оптического пути.
Диодные
Основным рабочим элементом диодного лазерного резака является излучатель в виде полупроводникового кристалла, сформированного как оптический резонатор. Помимо диода, в состав такого лазера входит специализированное устройство для питания от сети переменного тока. Это позволяет варьировать параметры выходного излучения.
Также конструкция предусматривает датчик контроля температуры и оптическое приспособление, позволяющие многократно повысить монохроматичность луча.
Однако лазер диодного типа существенно проигрывает газовым и оптоволоконным по параметрам когерентности. Фокусировка даёт большую расходимость, поэтому невозможно сконцентрировать энергию в максимальном объеме. Единственное преимущество такого оборудования заключается в сравнительной дешевизне относительно всех других моделей.
Твердотельные
Принцип работы твердотельного лазера напоминает газовый. Но у него есть и свои особенности. В отличие от газовой среды, здесь используется активная среда твердых форм. Как правило, это кристаллы и различные стёкла, которые активируются при контакте с редкоземельными элементами. Такие лазеры характеризуются повышенной эффективностью, при этом ряд моделей имеет довольно компактные размеры. Эти резаки вырабатывают лучи, длина волны которых позволяет успешно работать с металлами разных видов и толщины.
Популярные производители
На сегодняшний день на рынке представлены лазерные резаки по металлу от самых разных производителей. Среди иностранных компаний на отечественном рынке большой популярностью пользуется продукция заводов, расположенных на территории европейских стран, США, а также в Японии и Тайваня:
- Trumpf (Германия);
- Schuler (Германия);
- Trotec (Австрия);
- Farley Laserlab (Австралия);
- GCC (Тайвань).
Кроме того, большую долю рынка занимает продукция китайского производства. Мнение о ней неоднозначное, многие сомневаются в ее качестве. Тем не менее, некоторые бренды, производственные мощности которых располагаются на территории Китая, работают по швейцарской технологии и под строгим контролем со стороны заказчика. Они производят лазерные станки с исключительно высокими технико-эксплуатационными характеристиками. К таким компаниям относят:
- Rabbit;
- Wattsan;
- Bodor.
В России лазерные резчики выпускают промышленные предприятия «Полупроводниковые приборы», «ЛОМО», «Плазма» и «Инверсия». Каждое из них предлагает определённые виды лазерных установок. Предприятий, занимающихся производством одновременно всех разновидностей лазерных станков, в нашей стране нет.
Как свидетельствует практика, качество российских резаков оставляет желать лучшего и не дотягивает до станков зарубежных компаний. Однако это в полной мере компенсируется их низкой ценой.
Нюансы выбора
При выборе лазерного резака по металлу необходимо обращать внимание на следующие характеристики.
- Ассортимент материалов. В первую очередь, необходимо учитывать специфику предприятия. Важно уточнить, из чего сделаны детали, подлежащие резке и какова их толщина. Эти факторы следует сопоставить с техническими данными станка, размером рабочего поля и рабочими параметрами оборудования.
- Мощность. Средняя мощность всех лазерных станков на сегодняшний день варьируется в диапазоне от 500 до 6000 Вт. Если вы планируете резать металлические листы толщиной менее 6 мм, будет достаточно лазерного резчика мощностью 500-700 Вт. Для работы с более толстым материалом нужно выбрать станки с максимальной мощностью.
- Оснастка. Если речь идет об оптоволоконных станках, необходимо обратить внимание на расходные материалы: серводвигатели, направляющие, режущие головки, химеры и прочие. Качество и функциональность этих компонентов оказывают воздействие на точность и скорость лазерной резки. Некоторые недобросовестные производители комплектуют оборудование не оригинальными компонентами, а их аналогами в целях снижения себестоимости. Это может ввести в заблуждение покупателя. Поэтому информацию о происхождении расходников нужно уточнять заранее.
- Качество оборудования. В последние годы наметилась тенденция к сокращению производственного цикла на большинстве предприятий. Многие фирмы, особенно недавно появившиеся на рынке, не уделяют достаточного внимания тестированию своих лазерных резаков перед поставкой клиенту и не производят контроль качества работы оборудования. Поэтому при выборе станка очень важно обращать внимание на наличие у производителя служб тестирования и предпродажной подготовки.
- Сервисное обслуживание. При подборе оборудования предпочтение лучше отдавать станкам тех производителей, сервисные службы которых представлены в регионе использования. В противном случае любые изъяны в ходе эксплуатации приведут к долговременному ремонту и, соответственно, производственным простоям.
Применение
Станки для лазерной резки металла являются универсальными. Причем это касается как используемых материалов, так и широты производственных возможностей. В частности, на них можно производить резку и гравировку металлов.
Наиболее частым вариантом применения лазерного оборудования считается раскрой материала. Станки, в которых основным режущим инструментом является лазер, широко распространены в металлообработке. Они позволяют изготавливать:
- отдельные элементы внутренних и наружных рекламных конструкций;
- конструкторы и пазлы из металла;
- предметы декора;
- детали для авто- и авиамоделирования;
- сувениры.
Гравировка металлических изделий при помощи лазера может превратить самую простую вещь в бесценный подарок. Наиболее четкой получается гравировка с использованием лазерного луча. Наносимые в такой технике изображения имеют безграничный срок годности, им не страшны истирания, воздействия кислотно-щелочных растворов, воды, ультрафиолета и перепадов температур.
При помощи лазера, управляемого компьютером, можно получить изображение с максимальной детализацией. Зачастую на металлических поверхностях создают затейливые узоры и даже воспроизводят фотографии.
Чаще всего лазерный резак используют для гравировки зажигалок, портсигаров, ювелирных украшений, холодного и стрелкового оружия, а также предметов декора.
При помощи лазерного луча гравировать можно не только плоские, но также и выпуклые поверхности. В этом случае к движку станка подключается специализированный механизм фиксации заготовки. Вращение двигателя передается обрабатываемому изделию, оно начинает перемещаться с заданной скоростью и лазерный луч наносит изображение со всех сторон.