Все, что нужно знать о закалке стали
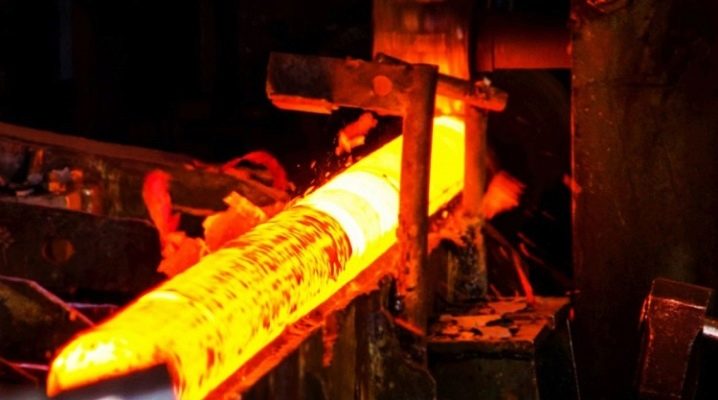
Организовывать металлообрабатывающее или машиностроительное производство, не выяснив все, что нужно знать о закалке стали, о режимах и структуре закаленной стали, весьма опрометчиво. Ряду людей будет интересно выяснить, как закалять ее в домашних условиях. Также придется разобраться с температурой и видами закалки, с закаливаемостью сталей 20, 45 и других марок.
Какие стали подлежат закалке?
Несмотря на важность этого метода обработки, он может быть применен не ко всем сплавам железа с углеродом. Возможность такой манипуляции специалисты называют закаливаемостью. Установлено, что закалить и отпустить можно только такой металл (прокат), который содержит мало углерода. Сталь 20, а также сплав 10 и 25 не подвергают закаливанию. А вот углеродистый металл вполне может быть обработан таким образом.
Речь идет про сталь:
- 40;
- 9ХС;
- 40Х;
- 13Х;
- ХВГ;
- 45;
- Х12МФ;
- М51.
Свойства закаленных материалов
Правильное закаливание обеспечивает такие характеристики металла, как:
- повышенная твердость на поверхности;
- наращивание суммарной прочности;
- минимизация пластичности до оправданных техническими требованиями показателей;
- сокращение массы металлургической продукции при поддержании исходной прочности и твердости.
В процессе обработки изменяется структура закаливаемой стали. При этом происходит ряд фазовых изменений. При критической температуре, равной 723 градусам, металл еще тверд, но в нем уже разворачивается распад цементита. Вместо него появляется постепенно аустенит. Если дальше металл охлаждать плавно, то аустенит распадается, и эффект от закаливания, по сути, пропадает.
Но вот при быстром остужении распад не происходит, и сталь приобретает те самые характеристики, которые так нужны заказчикам. Закаливаемая до мартенситного состояния сталь оказывается наиболее тверда. Это позволяет использовать готовый продукт в режущих инструментах. Закалка на троостит позволяет сбалансировать твердость и упругостные показатели, что ценно в ударном инструменте и пружинных амортизаторах. Если сталь закалена до сорбитного состояния, то она окажется:
- упругой;
- вязкой;
- стойко переносящей изнашивающие воздействия.
Виды
В одной среде
Такой способ внешне прост. Деталь прогревают строго до заданной температуры. Затем ее погружают в жидкость и держат там, пока она не достигнет полного охлаждения. Углеродистую и малолегированную сталь принято остужать в технической воде. Легированный металл традиционно закаливают в масле. Технологи стремятся к одинаковой прочности заготовки по всей поверхности. Это достигается за счет относительного движения конструкции в той среде, куда она помещена.
При механизированной закладке такое перемещение обеспечивается путем циркуляции. При ручной обработке передвигать придется заготовку. Темп перемещения и другие нюансы манипуляции подбираются таким образом, чтобы материал не подвергался короблению.
Описываемая методика ценна для легированной стали, остужаемой начиная с высокой температуры.
Ступенчатая
В этом случае металл также прогревают до закалочной температуры. Но дальше уже начинаются отличия — охлаждение ведется в относительно горячей среде, при 180-250 градусах чаще всего. Стремятся при этом, чтобы прогрев был немного сильнее, чем нужно для мартенситного превращения. В такой ситуации разогрев поверхности детали и охладительного вещества быстро выравнивается. Если охлаждение продолжается, появляется уже мартенсит.
Превращение идет по всей массе заготовок синхронно. Как результат, опасность появления напряжений сводится к минимуму. Последующее остужение можно производить уже даже просто на воздухе. Минусом ступенчатой методики оказывается ее заведомая неприменимость для крупных конструкций. Для них потребовалась бы слишком долгая выдержка, что создает опасность нежелательных структурных изменений.
Изотермическая
Методически такой подход мало отличается от ступенчатого закаливания. Цель — добиться распада аустенита и формирования нижнего бейнита. Углеродистые стали закаливают изотермически не слишком часто, потому что такой подход дает мало преимуществ в сравнении с иными вариантами. А вот для легированного металла – это возможность достичь сбалансированного уровня прочности и вязкости. Предел выносливости у стали окажется в итоге выше, чем при обработке по мартенситному сценарию.
Однако массовое использование изотермической закалки задерживается по нескольким причинам:
- необходимость использовать дорогостоящее оборудование;
- повышенная длительность и трудоемкость манипуляций (то есть рост издержек производства);
- необходимость применения высокотоксичных закаливающих сред — впрочем, эта проблема отчасти решается вертикальными элеваторными печами с интенсивным проветриванием закалочной емкости.
С самоотпуском
После прогрева при таком подходе конструкции помещают в охладительную среду. Там их надо держать до неполного охлаждения. Когда заготовка вынута, наружные слои вновь начинают повышать температуру. Необходимое тепло поступает из внутренней части детали. Такой режим и называют самоотпуском. К нему прибегают, если надо обеспечить одновременно повышенную твердость поверхностного слоя и значительную вязкость сердцевинной области.
Подобное сочетание свойств крайне ценно для молотков, зубил и иных инструментов, которые совершают ударную обработку. Закалка с самоотпуском успешно проводится даже в условиях современного поточного производства. Нередко она сочетается с местной термообработкой. Длительностью самоотпуска выступает промежуток, разделяющий остановку закалочного понижения температуры и начало повторного охлаждения.
Светлая
Техническая литература такой термин не употребляет, но знать, что это за метод, очень важно. Суть состоит в том, что закаливание обычного металла сопровождается потемнением. А вот легированные стали в вакуумной или инертной среде при этом расцветку не меняют. Очевидно, что такие методы защиты металла весьма дороги и трудоемки. К ним прибегают только при массовом выпуске однородных изделий, когда работает эффект масштаба и издержки размазываются по всем экземплярам.
Для работы используют вертикальные печи. Нагрев заготовки проходит в индукторе. Оттуда она перемещается в ванну со специальными солями или селитрой. Весь объем установки должен быть полностью герметичен. Откачка воздуха проводится после завершения каждого цикла.
Поверхностная
Поверхностная закалка, как следует уже из названия, призвана упрочнить наружные слои металла. Для этой цели используют ТВЧ (токи высокой частоты), производящие эффект индукционного нагрева. Чаще к подобной методике прибегают при обработке углеродистых сталей. Температура должна быть более высокой, чем при традиционной объемной методике закаливания. В некоторых случаях прибегают к газопламенному или даже лазерному разогреву сплава – они позволяют, соответственно, уменьшать издержки и повышать точность манипуляций.
Необходимое оборудование
О некоторых его разновидностях — вертикальных печах — речь уже заходила. Однако требуются порой и другие приспособления, технические системы. Кроме печей, обязательно понадобится специальная закалочная ванна. Она оснащается таким образом, чтобы можно было постоянно контролировать тепловые режимы и точно оценивать их соблюдение. Конструктивная схема ванн практически не отличается у разных фирм, по большей части разница касается только габаритов.
Функциональный отсек ванны преимущественно выполняется в прямоугольной форме, но также могут встретиться и цилиндрические модели. Толщина варьируется с учетом планируемой наивысшей продолжительности обработки. Важную роль играет вентиляционный контур, без которого было бы невозможно удаление токсичных веществ. Благодаря теплообменнику исключается хаотическое изменение температуры жидкости для закаливания и поддерживается стабильный ход всего процесса. Теплообменник может принудительно обдуваться вентилятором, однако иногда отвод теплоты от него ведут при помощи циркуляции, поддерживаемой компрессором.
Закалка токами высокой частоты подразумевает использование продвинутой индукционной машины. Индуктор представляет собой катушку, обвиваемую медной трубкой. Геометрия индуктора определяется только конфигурацией и габаритами детали. Предусматривается вращение заготовки в центрах, что требует наличия как зажимов, так и двигателя, и контролирующего процесс механизма.
Разумеется, независимо от способа закалки придется постоянно вести термометрию удаленными средствами наблюдения.
Температура
Выбор режимов и степени нагрева во многом индивидуален — но это не означает, что все требования можно игнорировать. Чаще всего подразумевается первоначальный прогрев стали до аустенитного состояния. Чтобы гарантированно, несмотря на вероятные примеси, произвести соответствующее превращение, нужен нагрев на 30-50 градусов выше расчетной точки. Перегрев существенно более Ac3 также нецелесообразен, потому что разрастание аустенитных зерен ведет к хрупкости материала. Инструментальные углеродистые стали доводить до аустенитной фазы не имеет смысла и даже вредно.
Легированный металл закаливают опять же учитывая критические точки. Однако большое количество улучшающих компонентов сильно затруднит отбор наилучшего рабочего режима. Если легированная сталь содержит много карбидов, ее надо прогревать существенно выше критических точек, иногда до 1000 градусов и более. Только при расплавлении карбидов и переходе заключенных в них легирующих добавок в аустенит можно получить хороший результат. Температура при неполной закалке составляет такую величину, при которой сохраняется избыточный цементит. Этот режим показан для заэвтектоидных сталей, но может использоваться и для других сплавов.
Как закалять в домашних условиях?
Технология в этом случае существенно не отличается от той, что практикуется на больших заводах. Точно так же надо разогреть металл, а затем охладить. Но ограниченное оборудование, даже в продвинутых домашних мастерских, не позволяет воспроизвести промышленные методики точь-в-точь. Процесс в любом случае должен происходить равномерно и плавно. На поверхности нельзя допускать появления черных или синих пятен. Чтобы сделать все правильно, используют термопечи. Иногда их заменяют на электропечи или даже на открытый огонь. Струйное закаливание проводится, если надо работать точечно. Время выдержки при погружении предмета в масляную ванну не превышает 3 секунд, но эту процедуру проводят многократно и быстро. Судить о температуре образца приходится по окраске поверхности или по степени побежалости.
Открытое пламя — как костра, так и горелки — позволяет прогреть лишь относительно небольшие металлические изделия. Минус открытого огня состоит еще и в опасности обезуглероживания поверхности. Наддувать кузнечный горн возможно мощным промышленным феном. Простые временные печи для такой работы создают из шамотных кирпичей. Закалочные жидкости помещают в емкости подходящей величины, изготавливаемые из несгораемых веществ. Держать заготовки помогут щипцы либо крючья подходящей величины. Охлаждение металла в домашних условиях возможно при помощи воды и воздуха, водных растворов и минерального масла. Если какое-то изделие состоит из частей с разной целевой твердостью, прибегают к последовательному остужению в двух средах.
Конкретные параметры и режимы подбирают сообразно параметрам определенного сплава. Изготовив импровизированную камеру, можно будет повысить температуру до 1200 градусов, что гарантирует обработку легированного металла.
Дефекты после закаливания
Иногда закаливаемая сталь приобретает слишком низкую твердость. Это бывает связано с чрезмерно низкой температурой или с несоблюдением временных рамок процедуры. Проблема также часто обуславливается малыми темпами охлаждения. Источником сложностей может стать и чрезмерный нагрев образца (выше допустимых температур). Из-за роста зерен в перегретой детали металл становится несообразно хрупок.
О пережоге говорят, когда сталь нагрели практически до температуры плавления. Чтобы компенсировать такую опасность, нужно использовать атмосферу, не имеющую окислительных свойств. Также вероятны:
- окисление;
- обезуглероживание;
- коробление;
- растрескивание.