Особенности прокаливаемости стали
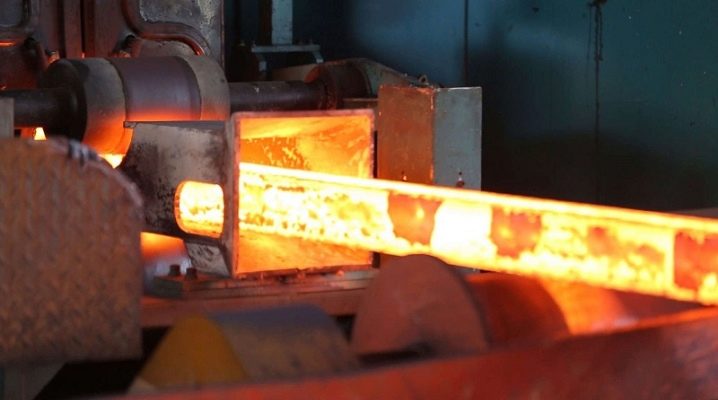
Закалка металла – особая процедура по термообработке различных сталей, подразумевающая разогрев материала до температуры выше критической с последующим выдерживанием при заданных показателях и резким остужением.
В процессе закалки сталь ведет себя по-разному. Определенная глубина, которая характеризуется данными изменениями, называется прокаливаемостью. Стоит подробнее рассмотреть особенности этого показателя.
Что это такое?
Прокаливаемость стальных материалов определяется рядом факторов и демонстрирует способность металла менять собственную структуру в пределах определенной глубины. За последнюю принимают расстояние от поверхности материала до изменившейся полумартенситной структуры, состоящей на 50% из мартенсита, на 50% – из троостита. Также стоит упомянуть критический диаметр прокаливаемой стали – это ширина от поверхности материала до полумартенситной зоны в образцах цилиндрической формы, которые изготавливают для проведения экспериментов.
Показатель прокаливаемости меняется в зависимости от ряда факторов. Один из них – критическая скорость закалки, которая формирует прямую пропорциональность изменений. Таким образом, чем устойчивее переохлажденный аустенит в составе стали, тем выше прокаливаемость материала. Регулирует норму показателя ГОСТ 5657-69, в котором подробно описана методика торцевой закалки.
Для определения степени прокаливаемости стали были проведены испытания, в результате получены графики-изображения, в которых отображается изменение твердости материала в процессе закалки.
Влияющие факторы
Прокаливаемость стали меняется в зависимости от различных факторов. Приведём основные, способные оказать сильное воздействие на показатель.
- Исходная структура. Один из важных факторов, способных оказать сильное воздействие на показатель прокаливаемости. Особое внимание стоит уделить дисперсности карбидной среды, величина которой прямо пропорционально меняет показатель.
- Химический состав. При переходе от одной марки стали к другой прокаливаемость меняется, и это можно заметить в нормативном документе при изучении графиков и таблиц. Стоит отметить, что влияние химического состава в пределах одной марки оказывает слабое воздействие на прокаливаемость, а иногда и вовсе никак не проявляется.
- Размеры зерен аустенита. Большинство конструкционных сталей обладают мелкозернистой структурой. При этом колебания в величине зерна не превышают 2–3 баллов, и прокаливаемость от этого меняется незначительно.
- Условия термической обработки. При рассмотрении данного фактора необходимо учитывать также температуру и продолжительность нагрева совместно со скоростью охлаждения. Обычно показатель увеличивается, стоит поднять температуру и продлить выдержку, однако изменения происходят неравномерно даже для одних и тех же марок. Стоит отметить, что подобные эксперименты негативно отражаются на свойствах термической обработки, поэтому необходимо соблюдать выставленный нормативом режим.
Чтобы в процессе отжига стали никаких изменений не произошло, стоит заранее установить единый оптимальный режим. Знание нормированных показателей прокаливаемости для всех марок позволит добиться эффективной технологии обработки металлических изделий и исключит риск брака.
Полосы прокаливаемости разных марок
Показатели прокаливаемости, характерные для сталей разных марок, прописаны в ГОСТ 5657-69. Определить параметр можно разными способами, но нормативный документ придерживается методики торцевой закалки. Перечислим этапы проведения испытаний.
- Из стали, показатель прокаливаемости которой нужно узнать, изготавливают образец цилиндрической формы.
- Далее заготовку нагревают в специальных печах до температуры закалки, а затем выдерживают в течение 30 минут в этих же условиях.
- По истечении установленного времени образец крепят на закалочную установку с помощью кронштейнов и охлаждают мощной струей воды.
- Далее с двух противоположных сторон с образца снимают две лыски, которые представляют собой продольные площадки. Глубина лысок не превышает 0,5 мм.
- Следующий шаг подразумевает измерение твердости от торца вдоль лыски. Замеры проводят каждые 1,5 мм.
Данные, полученные в результате замеров, используют для построения диаграммы или графика прокаливаемости. Берут стандартную систему координат, по вертикали откладывая значение твердости, а по горизонтали – расстояние от охлажденного торца. Точки впоследствии соединяют и образуют линии. Так как показатель зависит от химического состава металла и ряда других параметров, то у каждой марки – у той же стали 40 – будет не одна, а две кривые. Первая демонстрирует верхний предел прокаливаемости, вторая – нижний.
Результатом становится график из двух линий – это полоса прокаливаемости материала. Необходимо обратить внимание на то, что эти полосы не всегда будут выглядеть так же, как на графиках в ГОСТе, ввиду внешних факторов, способных повлиять на результаты процедуры.