Особенности быстрорежущей стали и ее обработка
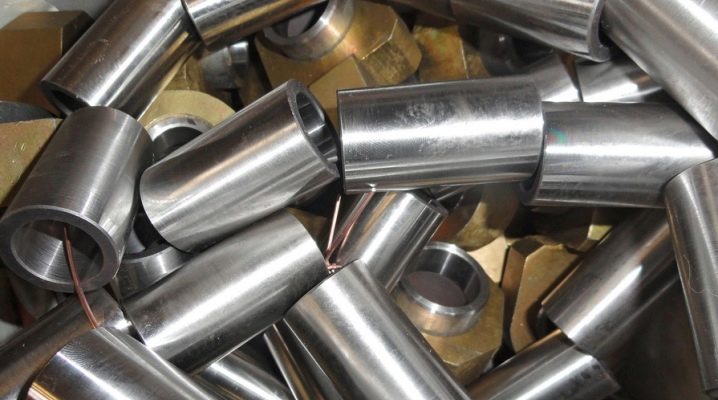
Быстрорежущая сталь относится к легированным (содержащим примеси) сплавам. Из ее названия понятна основная функция металла. В этой статье мы разберем основные характеристики, свойства, марки и принципы маркировки инструментальной стали.
Общее описание
Специальный сплав для быстрорежущей стали имеет в составе в разных процентных соотношениях в зависимости от марки углерод, хром, вольфрам, молибден, ванадий, кобальт и другие примеси. Благодаря своей структуре он (сплав) хорошо выдерживает термическое воздействие. Поэтому быстрорежущая сталь относится к инструментальным.
Необходимость в получении такого металла особенно остро стояла в середине XIX века. Предыдущие резцы из обычной стали уже не так хорошо справлялись с обработкой материалов из дерева и металлов: они быстро изнашивались, при высоких температурах теряли форму, выдерживали скорость только в 5 м/мин. В 1958 году английские мастера начали опыты и эксперименты. Долгожданный успех был достигнут в Америке спустя 40 лет. Появлению быстрорежущей стали мы обязаны инженерам Тейлору и Уатту.
Первая быстрорежущая сталь стала базой для марки P18. Ее максимальная скорость достигала 18 м/мин. Дальнейшие эксперименты уже других химиков привели к созданию сверхбыстрорежущей стали со скоростью резания 35 м/мин.
Все они привели к тому, что производительность станков по сравнению с вышеописанными английскими версиями выросла в 7 раз.
Характеристики и свойства
Быстрорежущая сталь входит в ГОСТ и имеет множество достоинств. Производители опираются на них при выборе того или иного сплава для внедрения в системы с повышенной производительностью.
К примечательным характеристикам быстрорезов можно отнести ряд факторов.
- Твердость. Ее сохранение важно, как правило, только в случаях сильного нагрева, она же именуется «горячей твердостью». Тепло возникает вследствие трения инструмента с другой поверхностью на высокой скорости. Стали другого типа в подобной ситуации подвергаются отпуску, становятся более пластичными и неработоспособными. Быстрорежущая сталь способна выдержать воздействие до 600 градусов Цельсия, тогда как обычная сталь выдерживает только 200 градусов.
- Высокая красностойкость (или теплостойкость). Это важный показатель, характеризующий тот временной промежуток, когда сплав, находящийся в нагретом состоянии, не меняет изначальных свойств.
- Сопротивление разрушительным процессам. Нагрев сплава – не единственное, о чем беспокоились химики при его создании. Материал, из которого сделан инструмент, по многу раз обрабатывающий поверхности разного характера, должен был быть особо прочным и, как следствие, иметь длительный срок эксплуатации.
Как раз быстрорежущая сталь сочетает в себе такие свойства: она прочна, не крошится и не ломается.
Виды
В зависимости от примесей, входящих в состав сплава, различают несколько основных видов быстрорежущей стали.
К ним относят: Р18, Р9, Р6М5, а также стали с более высоким содержанием ванадия и кобальта: Р12ФЗ, Р6М5ФЗ, Р18К5Ф2, Р9К5, Р6М5К5, Р9М4К8 и другие.
Последнюю группу называют высоколегированной конструкционной, сплавы из нее относят к нержавеющим и улучшенным. Из жаропрочных и высокопрочных можно выделить Р6М5, Р18К5Ф2, Р6М5К5, Р12Ф4К5, Р6М5Ф3, Р9М4К8.
Маркировка
Советские и современные марочники стали подразумевают специальные обозначения марок быстрорежущих сталей. Расшифровка их довольно проста. В обозначении каждого сплава впереди ставится буква «Р» (от английского rapid — быстрый). Последующая цифра обозначает содержание вольфрама (буква «В» не указывается) в процентном соотношении к общей массе. Затем буквами «М», «Ф» и «К» обозначается количество молибдена, ванадия и кобальта соответственно. Инструменты из быстрорежущей стали иностранного производства обычно маркируются аббревиатурой HSS (High Speed Steel), а также HSSE (кобальтовая сталь).
Однако некоторые элементы, входящие в состав металла, при маркировке могут не обозначаться. Обычно это либо углерод, содержание которого варьируется от 0,7 до 1,5%, либо хром, от 3 до 4,4%.
Сферы применения
Сплав имеет широкий спектр применения. В зависимости от марки, ее свойств, состава и назначения быстрорежущую сталь применяют в разных областях производства.
В основном это:
-
режущий и сверлящий инструмент, отрезные резцы, фрезы и метчики;
-
изготовление съемных режущих кромок;
-
детали для станков, обрабатывающих металл;
-
инструменты по отделке металлических изделий, ручная обработка которых затруднена.
Разберем несколько популярных марок и их применение.
- Р6М5. Сплав используется в изготовлении некоторых резьбонарезных и просто режущих инструментов. Он также хорошо зарекомендовал себя как довольно бюджетный вид стали с хорошей теплостойкостью.
- Р6М5К5. Более сложное соединение, включающее, помимо молибдена, как предыдущий сплав, кобальт, что делает сплав более прочным. Инструменты из такого материала легко поддаются шлифовке и рассчитаны на долгий срок эксплуатации.
- Р18. Используется как материал для обработки конструкционной стали, сохраняет свои режущие свойства при максимальных температурах. Это не бюджетный вариант, но ее аналогом выступает сплав Р9.
- Р12. Очень похожа на предыдущий вариант, однако содержит меньше карбидов, по этой причине более пластична. Инструменты из нее изготавливают посредством пластической деформации. Все они носят режущее назначение.
- Р9К5. Легированная сталь этого типа, как и Р18, необходима для обработки других, более сложных металлов. Среди них: нержавеющие, жаропрочные, сплавы повышенной прочности и другие. По сравнению с Р6М5, Р9К5 служит в 3 раза дольше.
Обработка
Дополнительные действия осуществляются с применением высоких температур. Как результат: изменяется структура материала. Делается это с целью изменения характеристик металла, его физико-механических свойств.
Отжиг
Быстрорежущая сталь, пройдя этапы прокатки и ковки, обладает внутренним напряжением и становится существенно тверже. По этой причине металл нуждается в отжиге. Процесс направлен на снятие внутреннего напряжения, делает металл более податливым в обработке и подготовленным к закалке.
Осуществляется отжиг при температурах от 850 до 900 градусов Цельсия. Более высокие температуры, наравне с неправильной выдержкой, делают сталь, наоборот, более твердой. Сплав быстрорезов характеризуется слабой способностью проводить тепло, поэтому нагрев происходит так, чтобы температура металла повышалась медленно и равномерно.
На машиностроительных заводах заготовки проходят изотермический отжиг. За небольшой промежуток времени их нагревают до 900 градусов, чтобы потом переместить в печь на 2-3 часа, где температура в 720-730 градусов Цельсия доводит материал до окончательного состояния. Появляющиеся внутренние напряжения после термообработки снимают охлаждением в печах с температурой 400-450 градусов, а затем оставляют на открытом воздухе.
Отжиг, происходящий вручную в печи, подразумевает изначальные температуры 200-300 градусов, которые постепенно повышают на 150-200 градусов каждый час. Процесс также завершается охлаждением, сначала в печи при 650 градусах, а потом при комнатных температурах. Единственный значимый минус такого метода состоит в скорости: он занимает больше времени.
А также изделия будут нуждаться в последующей механической обработке, закалке и отпуске.
Закалка
Закаливание происходит при температурах свыше 1300 градусов Цельсия. Для успешного завершения процесса металл многократно проходит отпуск при 550-560 градусах.
После охлаждения на выходе остается высоколегированный мартенсит, содержащий вольфрама, ванадия и хрома в разы больше, чем изначальный сплав. Такая структура (мартенсит) помогает создавать стали, выдерживающие крайние показатели температур (600 градусов).
Подобные показатели высокой красностойкости возможны только при закалке с очень высокими температурами. Важно следить, чтобы весь процесс происходил правильно – в худшем случае при увеличении показателей сталь начнет оплавляться.
Отпуск
Закалка всегда завершается отпуском. В зависимости от целей процесс характеризуется разными временными промежутками в этапах, темпом понижения температур. По этим показателям отпуск различают: низкий, средний и высокий.
Чем ниже отпуск, тем ниже температура охлажденного металла. «Улучшенной» сталью считают ту, что прошла правильный высокий отпуск.
Необходимые температуры: 550-560 градусов (это практически трехкратный низкий отпуск), сопровождают этапы с промежутками по 1 часу. При этом внутри сплава происходит два процесса.
-
Нагрев и отпуск способствуют выделению карбида в измельченном виде. Структура быстро доходит до мартенсита.
-
Охлаждение способствует снятию внутреннего напряжения.
Современные производства вынуждены заменить этот тип на ускоренный метод отпуска, происходящий при более высоких температурах.
Улучшение
Всех описанных выше методов по укреплению сплава часто бывает недостаточно, чтобы сталь признали пригодной. Улучшение подразумевает внешнюю обработку готовой детали. Она должна быть предварительно отшлифована, заточена и закалена по необходимости.
Способов существует довольно много, вот некоторые из них.
-
Азотирование. Деталь помещается в газообразную среду (80% азота и 20% аммиака или 100% аммиака). Длится от 10 до 40 минут при 550-6600 градусах. Метод направлен на укрепление верхних слоев.
-
Цианирование. Подразумевает насыщение углеродом и азотом. Части погружают в расплав (цианид натрия). Толщина слоя зависит от временного промежутка и температуры проведения процедуры.
-
Сульфидирование. Примерно также детали помещают в жидкий расплав (сульфид и сера). Время проведения: 45 минут – 3 часа. Температуры: 450-5600 градусов Цельсия.