Сталь 40Х
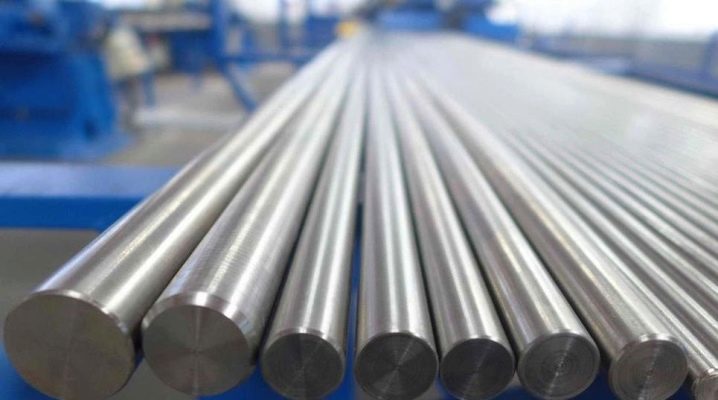
Марка стали 40Х – одна из самых актуальных в практике, и потому требованиям ГОСТа в отношении ее твердости и других характеристик надо уделить особое внимание. Заслуживают его также расшифровка сплава, порядок его термообработки и уровень плотности, предел текучести. Только разобравшись с механическими свойствами и режимами закалки, можно правильно применять этот материал.
Состав и расшифровка
Марка стали 40Х специфическим образом соответствует ее химическому составу. Число в начале названия говорит о количестве главного улучшающего железо элемента, то есть углерода, в сотых долях процента. В среднем его содержание составит 0,4%. Практически вся масса сплава образована самим железом. Буква Х говорит о повышенной (в данном случае 1,1%) хромистости.
Плюсы и минусы
Такой металл весьма прочен и надежен. Его твердость составляет до 217 МПа. Еще сталь 40Х весьма устойчива к износу. Подобное вещество способно стойко противостоять негативным воздействиям агрессивной среды.
При низких температурах и колебаниях температур проблемы практически исключены.
Однако слабостью стали 40Х является подверженность формированию структурных трещин (флокенов). Отпускная хрупкость также является серьезной проблемой. Свариваемость подобного металла ограничена. Его придется тщательно подготавливать, и дополнительно дорабатывать сплав термически после сварки. В остальном никаких сложностей не возникает.
Характеристики и свойства
Физические
Эти параметры определяются сообразно требованиям ГОСТ 4543 от 2016 года. Материал подвергают испытанию на осадку на 65%. Свариваемость у такого сплава, как уже указано, невелика. Шов очень часто растрескивается. Сложности представляет резка при помощи сварочного оборудования. Критические точки:
-
самая низкая Ar1 при 693 градусах;
-
самая высокая Ac3 при 815 градусах;
-
Ac1 при 743 градусах.
Ковочная обработка начинается при 1250 градусах, а заканчивать ее полагается при 800 градусах. Обрабатываемость твердосплавными резцами — с коэффициентом 1,2. Если используются резцы из быстрорежущей стали, то коэффициент составляет только 0,95.
Предел выносливости составляет 690 МПа. Микроструктура стали 40Х определяется после термообработки.
После полного отжига формируется полосчатая феррито-перлитная структура, а при изотермическом отжиге появляется простая феррито-перлитная структура без всякой полосчатости.
Механические
Нормативная твердость по шкале Бринелля согласно основному ГОСТу составляет не более уже упомянутых 217 МПа. Но есть и исключения:
-
для труб по стандарту 1987 года — 269 МПа;
-
для труб, получаемых методом холодной деформации, вновь 217 МПа;
-
для подвергаемых горячей прокатке прутков — всего 179 МПа.
Обычный предел текучести, измеряемый в ньютонах на квадратный миллиметр, принимается равным 785. Временное сопротивление должно достигать 980 единиц. При комнатной температуре воздуха плотность материала принимается на уровне 7750 кг на 1 куб. м.
Если температуру поднять до 200 градусов, то она вырастет до 7800 кг. При прогреве до 500˚C удельная тяжесть 1 м3 снизится до 7,65 тонны.
Кроме прочности и относительной массы, выделяются еще и другие нюансы. Так, модуль упругости достигает наивысшей величины при стандартных комнатных условиях. Ее уровень тогда составит 2,14 МПа. Когда металл разогрет до точки кипения воды, этот показатель уменьшится уже до 2,11 МПа. При более существенном прогреве он дополнительно стремительно понижается.
Например, при 300 градусах упругостный модуль все еще составит 2,03 единицы. При 500˚C он уже откатится до 1,76 единицы. А разогретая до 800˚C сталь 40Х будет иметь модуль упругости всего 1,32 МПа. Что касается твердости по Роквеллу, то она в большинстве источников не упомянута (в отличие от твердости по Бринеллю), или упоминается слабо. На этом характеристику механических свойств можно завершить.
Вид поставки
Сталь 40Х может отправляться заказчику в различном техническом состоянии. Практикуется использование поковок и фасонного проката, полосовой разновидности сплава и листов. Часто из этого металла производят:
-
трубы;
-
части для стыковки труб;
-
подвергаемые шлифовке прутки;
-
серебрянку;
-
низкоуглеродистую проволоку.
Круг или пруток из стали 40Х может производиться на основе различных стандартов — 2590, 4543, 7417, принятых соответственно в 2006, 1971 и 1975 годах. Нормативная длина составляет от 2 до 6 м. Сечения принимаются в пределах от 16 до 350 мм.
Фирменные испытания идут на термообработку и на ударную вязкость. Вес 1 метра круга при сечении 105 мм принимается равным 67,97 кг.
На основе стали 40Х вырабатываются различные плоские полотна. Допускается получение из нее полых (пустотелых) изделий разной величины. С точки зрения перевозки и хранения наиболее удобен прокат. Его полагается выравнивать на стане перед отправкой заказчику для нормализации результата. На поковки распространяется ГОСТ 8479-70.
Аналоги
В нашей стране вместо 40Х можно применять:
-
45Х;
-
38ХА;
-
40ХС;
-
40ХТГР;
-
40ХФА.
За рубежом есть альтернативные решения, употребляемые с той же целью. Так, в США заменителями являются стали 5135 и 5140. Альтернативой выступает американский же металл G51400. В ФРГ есть 3 «цифровых» заменителя — 1.7034, 1.7035 и 1.7035. А также немецкие металлурги могут предложить в качестве альтернативы 37Cr4, 41Cr4, 41CrS4.
В Японии практикуется выплавка:
-
SCr435;
-
SCr435H;
-
SCr440;
-
SCr440H.
Сплавы 41Cr4 и 38C4 поставляются французскими компаниями. В Швеции заместить такой металл можно продукцией 2245. В Чехии его аналогом является марка 14145.
Бельгийские поставщики могут предложить 37Cr4, 41Cr4, 45C4. Польские изготовители предлагают сплавы 38HA и 40H.
Металлургия КНР вместо стали 40Х поставляет заказчикам 35Cr, 40CrA, ML40Cr и некоторые другие варианты. А также в разных странах на замену этого российского металла разработали:
-
530H40;
-
42C4TS;
-
F. 1201;
-
F. 1211;
-
530A36;
-
SCr440 и ряд иных вариантов металлургической продукции.
Обработка и сварка
Присутствие целого ряда примесей очень активно влияет на технологию термообработки сплава 40Х. Процедура закалки должна проводиться очень тщательно, потому что такой сплав применяется при изготовлении ответственных изделий. Электропечь прогревают обычно до температуры 860 градусов. Чаще всего придется ждать выхода на такой режим примерно 40 минут.
Внутри камеры заготовку выдерживают от 10 до 15 минут. Требуется, чтобы образец стали приобрел равномерный желтый окрас. Термическая обработка стали марки 40Х подразумевает остужение в масле. Изредка проводится охлаждение в обычной технической воде. Установлено, что наилучшим решением является закаливание металла высокочастотным током.
Существуют различные режимы технологического отпуска. Низкотемпературный вариант подразумевает прогрев всего до 250 градусов. В дальнейшем остужение идет в воздушной среде.
Подобный подход гарантирует минимизацию внутренних напряжений, сокращение влияния на пластичность. Твердость образцов не нарушается, однако вероятно увеличение хрупкости.
При среднетемпературном отпуске прогрев идет до 500˚C. Вязкость заготовок вырастает. Пропорционально ей падает, увы, и твердость. Высокотемпературный метод подразумевает достижение температур до 600 градусов. Это приводит к тому, что во время отпуска мартенсит распадается до сорбита. В итоге пластичность и твердость будут сбалансированы.
Правильная нормализация включает доведение металла до наивысшей критической позиции. Далее сталь выдерживают и остужают в обычной среде. Нормализованная продукция приобретает мелкозернистую структуру.
Это нарастит пластичность и улучшит ударные свойства. Отжиг сплава 40Х может вестись в полном и в местном форматах, руководствуясь указаниями технических справочников.
При полном отжиге практикуется прогрев на 30-50 градусов горячее позиции Ac3. Выдерживать материал в таких условиях надо столько, чтобы он полностью прогрелся. Далее, когда закончатся фазовые преобразования для улучшения структуры, проводят медленное охлаждение. Отожженный продукт имеет малые твердость и прочность, но зато весьма пластичен. Полный отжиг подразумевает получение феррита и перлита. Дополнительно стоит указать на особенности предварительной стадии обработки.
Плавление этого сплава идет при 1420 градусах. Процесс производства включает обязательно сокращение количества фосфора. Металлическая ванна прогревается постепенно, плавно. Раскисляют металл диффузионным способом либо осаждением. Легирование проводится в последнюю очередь.
Важно рассмотреть также и сварочную обработку. Полуавтоматическое сваривание такого сплава обычно идет в защитной газовой среде.
Если вместо аргонодугового применить ацетиленовый метод, работать будет проще, но результат окажется менее надежен. Ацетиленом можно варить лишь относительно тонкие листы стали 40Х. Ручная сварка ведется с использованием специально предназначенных для этого металла электродов.
При плавлении и формировании сварочной ванны проблемы может создавать повышенная вязкость. Необходимо в дальнейшем исключать образование трещин. Лучше, если электроды будут иметь пониженное содержание водорода. Изредка применяют электрошлаковую методику. Контактно-точечное сваривание также вполне допустимо, но это уже сложнее.
Применение
Сплав 40Х достаточно прочен для выпуска ответственной продукции. Речь может идти про:
-
шестерни;
-
приспособления для клепки;
-
болты;
-
составные части машин с крутящимися барабанами;
-
оси и стержни;
-
измерительную аппаратуру;
-
кольца и втулки;
-
плунжеры и штоки;
-
трубопроводную арматуру и оправки.