Описание стали марки 38ХС
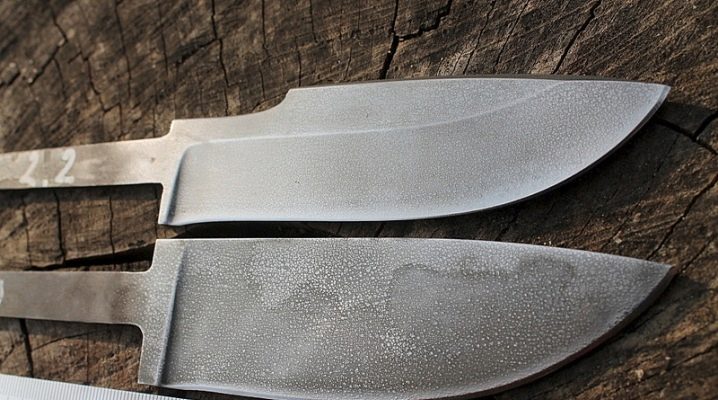
Стали, содержащие в себе некоторое количество хрома, имеют определённую устойчивость к коррозии во влажной, кислой или щелочной среде. Стальной сплав 38ХС не относится к нержавеющим, однако его качества востребованы – наряду с характеристиками похожих на него марок стали.
Состав и расшифровка
Химический состав стального сплава 38ХС подразумевает наличие углерода с массовой долей – от общего веса заготовок – порядка 0,38%. Кремний содержится в данном металле в количестве 1,2%, хром – 1,35%. Поскольку включение обеих легирующих присадок не превышает 2%, то в маркировке рассматриваемого сплава нет приписки типа 38Х2С2 (или наподобие): простое обозначение буквенных маркеров означает, что содержимое этих же примесей, полезных для данного состава, находится на уровне ниже среднего. Кроме этих двух примесей, медь представлена в сплаве 38ХС в количестве, не превышающем, чем 3 промилле, марганец – 3… 6, никель – до 3 промилле. Фосфор и сера по отдельности – не более 0,35 промилле, что, кстати, считается немалой дозой, достаточной для ломкости под околопредельными нагрузками.
Характеристики и свойства
Механика стали 38ХС при разных температурах отпускания и сечениях деталей существенно варьируется. Например, теплопроводность сплава меняется от 38 тепловых ватт на метр длины (при нагреве/охлаждении на каждый градус Цельсия) до 28 – она понижается при нагревании состава, о чём сообщают замеры на интервале от 20 до 800 градусов. Плотность остаётся на всём этом температурном отрезке практически без изменений – 7,64 г/см3. Удельная теплоёмкость, напротив, в отличие от теплопроводности, растёт устойчиво – от 463 джоулей на килограмм материала при нагревании на один кельвин, при +100 по Цельсию – до 663 Дж/кг*К.
Ковать сплав начинают при 1220 градусах, заканчивают – при 800 градусах по Цельсию. Сваривается данный состав плохо: без ручной дуги, подогрева перед самим сеансом наложения сварных швов и без постотжига соединить заготовки прочно и надёжно не удастся. При разрезах деталей до 250 мм остывание производится на воздухе, а до 350 мм – в печном отсеке, понижают температуру они вместе с самой печью. Второй метод сварки – КТС: последующее остывание с отжигом необходимо. Отпускное охрупчивание выражено значительно. Флокенообразование не так сильно. Критические температуры расположились следующим образом:
Критическая точка | °С |
Ac1 | 763 |
Ac3 | 810 |
Ar3 | 755 |
Ar1 | 680 |
Mn | 330 |
Ударная амортизация зависит от температуры. Она измеряется в джоулях на квадратный сантиметр. Показатели проверяются по ГОСТ.
Температура окружающей среды | +20 | -20 | -40 | -60 |
Закаливание при 900°С, маслосостав. Отпускание при 600°С, остывание на открытом воздухе | 87 | 64 | 56 | 54 |
Предел прочности различен для конкретного вида воздействия.
Долговременное, МПа | Момент силы, МПа | Кратковременное, непостоянное, МПа |
382 | 930 | 730 |
Прокаливание при 880°С изменяет показатель твёрдости по шкале Роквелла.
Расстояние от торца, мм / показатель твёрдости | |||||||||
1.5 | 3 | 4.5 | 6 | 9 | 12 | 15 | 18 | 24 | 36 |
48–57 | 47–57 | 46.5–57 | 45.5–56.5 | 43–55.5 | 40–54.5 | 37.5–53 | 35.5–51.5 | 33–46 | 25–46 |
Физика сплава представлена следующим образом. При нагреве изменяются модули упругости. Плотность сплава остаётся одинаковой – до его расплавления.
Нагрев,°С | 20 | 100 | 200 | 300 | 400 | 500 | 600 | 700 | 800 | 900 |
Нормированная упругость, ГПа | 211 | 203 | 194 | 184 | 174 | 166 | 157 | 139 | 127 | |
Упругость при закручивании, ГПа | 84 | 80 | 78 | 72 | 68 | 65 | 62 | 55 | 48 | |
Удельный вес, кг/см3 | 7640 | |||||||||
Проводимость тепла, Вт/ (м ·°С) | 38 | 38 | 37 | 35 | 34 | 33 | 31 | 29 | 28 | |
Удельное электрическое сопротивление, нОм · м) | 284 | 329 | 413 | 563 | 725 | 902 | 1060 | |||
Диапазон колебаний температуры,°С | 20–100 | 20–200 | 20–300 | 20–400 | 20–500 | 20–600 | 20–700 | 20–800 | 20–900 | 20–1000 |
Величина постепенного расширения | 12.3 | 13.1 | 13.6 | 13.8 | 14.2 | 14.5 | 14.7 | 12.5 |
Сплав 38ХС ржавеет в пресной и морской воде. Скорость коррозии – до 100 мкм/год в обычной влажной среде, до 1 мм/год в морской воде. Щёлочи, кислоты и некоторые соли разъедают его с катастрофичной скоростью.
Для защиты от заржавливания заготовки покрывают водоатмосферостойкими лаками и красками, хромируют, оцинковывают, наносят «серебряночное» напыление из нержавейки, подвергают анодированию (электролизному омеднению).
Применение
Из стали 38ХС изготавливают валы, зубчатки для передачи движущей силы (кинетической энергии) всевозможных механизмов. Данный сплав – превосходный исходный материал, например, для повышающих и понижающих редукторов.
Обработка
Закалка производится при температуре не выше 900 по Цельсию. Отпуск – при температуре не выше 600, но не ниже 200 в зависимости от габаритов заготовки и желаемых параметров твёрдости и упругости. Отжиг стали 38ХС используется лишь при сваривании деталей, время – не более 2 ч. Состав 38ХС неплохо режется и сверлится. Режимы резки – пильно-фрезерный и лазерно-плазменный; качество раскроя – высокое.