Лазерная резка оргстекла
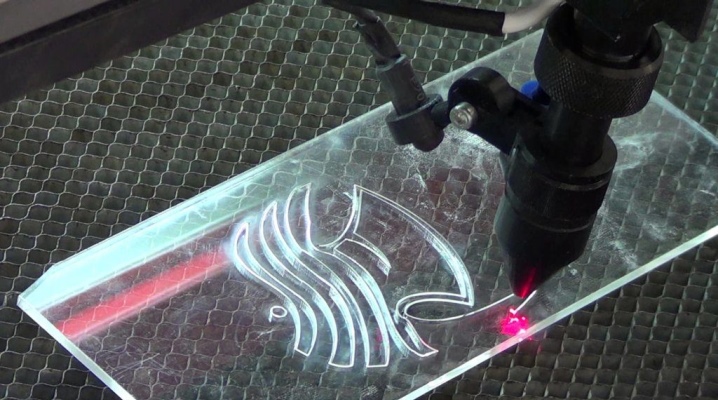
Лазерные технологии пришли на смену дисковым пилам, фрезерным станкам или ручной работе. Они упростили сам процесс и свели к минимуму возможности повреждения оргстекла. С помощью лазера стало возможным вырезание моделей со сложным абрисом даже самых маленьких размеров.
Плюсы и минусы
Работа с акрилом лазерными технологиями имеет немало преимуществ:
- аккуратные и чёткие грани;
- отсутствие деформации;
- лазерная резка оргстекла исключает риск случайных повреждений, что немаловажно при изготовлении сложных конструкций, требующих последующей сборки;
- грани вырезанных деталей не требуют дальнейшей обработки, имеют полированные края;
- работа с лазером позволяет существенно экономить на материале — при этой технологии появилась возможность более компактного расположения деталей, а значит уменьшения отходов;
- с помощью лазерного станка появилась возможность вырезать детали самых замысловатых форм, чего совершенно невозможно достичь с помощью пилы или фрезера, это позволяет решать дизайнерские проекты различной сложности;
- подобные станки дают возможность работать с большими объёмами;
- лазерная технология существенно экономит время на выполнение проекта из-за отсутствия необходимости последующей обработки срезов, при резке оргстекла механическим способом такой обработки не избежать;
- лазер используют не только для резки акрила, но и для гравировки, что позволяет расширить ассортимент услуг производителя;
- стоимость резки такого типа ниже, чем механической, особенно если это касается деталей простых форм;
- технология отличается высокой производительностью и снижением себестоимости, так как процесс резки происходит без участия человека.
Эффективность раскроя оргстекла подобным способом не вызывает никаких сомнений и пользуется всё большей популярностью.
К недостаткам можно отнести высокое внутреннее напряжение, остающееся в акриле.
Как сделать?
Раскрой плексигласа в домашних условиях делается несколькими способами. Умельцами используется электролобзик, ножовка по металлу, болгарка с трёхзубовым диском, нихромовая нить. Кроме того, производители предлагают специальные ножи для раскроя оргстекла. Несмотря на множество вариантов, резка лазером является наиболее прогрессивным методом. Такое оборудование позволяет создавать сложные и оригинальные контуры.
Качество и скорость обработки зависят от мощности луча, а подача листа влияет на глянец кромки.
Скорость подачи зависит от толщины материала — чем он толще, тем медленнее подача и наоборот. На качество кромки влияет выверенность скорости подачи. При слишком медленной скорости срез будет тусклым, при чересчур высокой кромка будет иметь выемки и эффект полосатости. Большое значение имеет точная фокусировка лазера — она должна строго соответствовать средней линии толщины листа. Органическое стекло после обработки имеет прозрачные грани с острыми углами.
Весь процесс раскроя плексигласа происходит под управлением компьютерной программы, руководящей передвижением лазерного блока. При желании можно запрограммировать декоративную отделку поверхности органического стекла, нанесение гравировки, придание ему матовости. Лист материала укладывается на рабочую поверхность, при необходимости фиксируется, хотя особой надобности в этом нет, так как он не подвергается механическому воздействию.
В компьютерную программу вносятся необходимые изменения и задачи: количество элементов, их форма и размеры.
Особым преимуществом является, что программа сама определяет оптимальное расположение деталей.
После выполнения необходимого алгоритма лазер приводят в действие. Многие умельцы самостоятельно изготавливают лазерные станки для работы в домашних условиях.
Чтобы собрать лазерный станок своими руками, понадобится набор комплектующих, позволяющих получить качественный инструмент:
- лазерная пушка — для преобразования луча;
- каретка, чьё плавное движение обеспечит необходимые результаты;
- многие изготавливают направляющие из подручных средств, но в любом случае они должны охватывать рабочую поверхность;
- двигатели, реле, зубчатые ремни, подшипники;
- программное обеспечение, с помощью которого возможен ввод требуемых данных, рисунков или узоров;
- электронный блок питания, отвечающий за выполнение команд;
- во время работы неизбежно появление вредных продуктов сгорания, чей отток необходимо обеспечить, для этого должна быть налажена система вентиляции.
Первым этапом является подготовка и сбор необходимых компонентов, в том числе под рукой должны иметься необходимые чертежи. Их можно сделать самостоятельно или воспользоваться услугами интернета, где есть масса полезной информации и готовых чертежей. Для домашнего использования зачастую выбирают микросхему Arduino.
Плату для системы управления можно приобрести в готовом виде или собрать на базе микросхем.
Каретки, как и многие другие узлы, можно напечатать на 3D-принтере. Профили используются алюминиевые, так как они лёгкие и не будут утяжелять конструкцию. При сборке рамы лучше не затягивать крепёж намертво, правильнее всего будет сделать это после завершения всех этапов работы.
После сборки всех узлов каретки проверяется плавность её хода. Затем ослабляются уголки на раме для снятия напряжения, появившегося от возможных перекосов, и вновь затягиваются. Снова проверяется плавность хода и отсутствие люфта.
Следующим этапом работы является электронная часть. Хорошо зарекомендовал себя синий лазер с длиной волны 445нМ и мощностью 2 Вт в комплекте с драйвером. Пропаиваются все проводные соединения и упаковываются в термоусадку. Установка концевых выключателей обеспечивает комфортную работу.
Корпус для лазерного станка можно сделать из ДСП, фанеры и так далее. Если нет возможности сделать его самому, можно заказать на мебельной фабрике.
Как избежать ошибок?
Чтобы избежать ошибок при раскрое органического стекла лазерной резкой, следует помнить, что этот метод сильно отличается от механического. Лазерный луч не режет пластик — там, где он соприкасается с поверхностью, молекулы материала просто испаряются.
Учитывая это свойство, детали при раскрое не должны соприкасаться друг с другом, иначе можно повредить грани.
Для создания изделия любой сложности в программу вносится макет в векторном формате. Задаются необходимые параметры для температуры и толщины луча, если модель станка не предусматривает самостоятельный выбор настроек. Автоматика распределит положение элементов на одном или нескольких листах плексигласа. Допустимая толщина равна 25 мм.
Работа с лазерным станком требует предельной точности во время программирования, иначе на выходе можно получить высокий процент брака.
Это будет заключаться в деформации, оплавлении граней или грубых срезах. В некоторых случаях для получения зеркального среза используется полировочный режим, это занимает в два раза больше времени и увеличивает стоимость изделия.
О преимуществах лазерной резки смотрите в видео.