Все, что необходимо знать о гранитном щебне
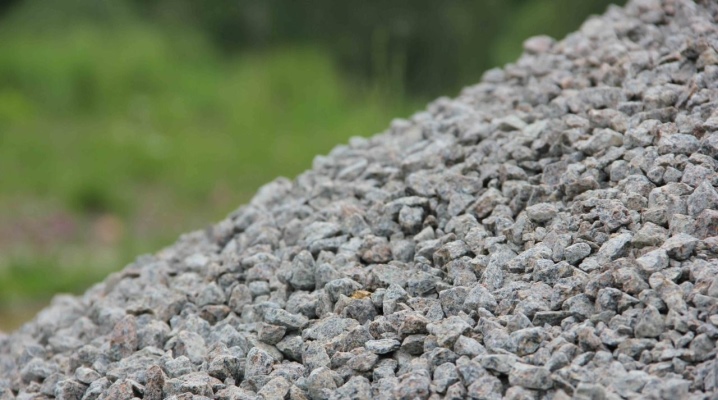
Щебень гранитный – это самый распространенный вид стройматериалов, его получают из горной вулканической породы, обладающей повышенной прочностью и имеющей зернистое строение. Оттенок может быть практически любым, все зависит от состава. Природный гранит – это особо прочная и твердая порода камня.
Плюсы и минусы
Преимущества гранита.
- Повышенная прочность и твердость — этот природный камень имеет самый высокий коэффициент.
- Легкость в обработке, так как он хорошо взаимодействует с различными сцепляющими составляющими.
- Практичность – подходит для применения в различных сферах и отраслях.
- Внешний вид – гранитный щебень выглядит как камень с множеством вкраплений черного, серого и белого цветов, такой специфичный окрас часто используется для декоративных работ.
- Низкая водопоглощаемость – это свойство играет важную роль в строительстве, так как гранит не будет деформироваться от действия влаги.
- Морозоустойчивость.
- Долговечность.
Минусы гранита.
- В отличие от доломитового щебня, коэффициент твердости и прочности которого идентичен гранитному, второй имеет цену выше. Это главный минус материала.
- Трудоемкий процесс изготовления, требуются дополнительные действия после добычи из карьера.
- Экологичность – гранитный щебень может содержать вредные составляющие, в отличие от известнякового, который имеет меньший уровень радиоактивности, несмотря на то что обе породы природного происхождения. Останавливая выбор на конкретном щебне, нужно просматривать сертификаты и выбирать 1 класс радиоактивности, гранитную разновидность лучше не использовать в строительстве жилых помещений.
Особенности добычи
В разговорной речи обычно употребляется такое выражение как «добыча щебня» – это не совсем так, на самом деле щебень получают искусственным методом. Добывается только горная порода – это начальное сырье. Сам материал изготавливается с помощью дробильно-сортировочного оборудования.
Сам процесс состоит из трех этапов – это добыча исходного материала, дробление, сортировка.
Добыча породы
Производители щебня используют разное сырье – гранит, мрамор, известняк и т. д., в зависимости от того, какой продукт нужно получить на выходе. Гранитный щебень изготавливают из многовекового вулканогенного (вулканического) материала – застывшей магмы. Перед началом работ подготавливается карьер – удаляется верхний слой дерна с травой, затем верхний слой грунта. Гранитные глыбы извлекаются из земли при помощи взрывов и техники, если необходимо их делят на части поменьше.
Производство щебня может быть целенаправленным или побочным. При изготовлении первым способом материал будет отличаться повышенным качеством и ценой. Во втором же случае щебень – это побочный материал, получаемый при добыче каких-либо полезных ископаемых или при изготовлении каких-либо изделий. Добыча породы может осуществляться четырьмя способами.
- Камнерезный – такой метод является самым затратным, но в то же время одним из эффективнейших. С помощью камнерезного оборудования блоки больших размеров отпиливаются сразу в карьере. Машины снабжены пилами канатного либо дискового типа с алмазными наконечниками. При работе данным способом глыбы получаются нужной формы и размера, на них не образуются микротрещины.
- Буроклиновой – этот метод один из старейших и сейчас его используют достаточно редко. Здесь работа начинается с того, что намечается контур глыбы, затем по этой отметке пробуриваются скважины. В них закладываются специальные колышки, при ударе по которым блок отделяется по заданной заранее линии. Этим методом обычно добываются самые твердые породы. Единственный минус технологии – она подойдет только для кусков породы маленького размера.
- Бурогидроклиновой – это усовершенствованная буроклиновая технология. Добыча проходит по идентичному плану, но клинья из стали заменяют гидроклинья. Они заполнены водой, которая находится под давлением, а в пробуренных отверстиях плавно расширяются. Таким методом можно добывать куски камней очень большого размера, в самых труднодоступных местах. Большое преимущество бурогидроклиновой технологии – это полное отсутствие шума и вибрации, так максимально сохраняется структура горной породы.
- Буровзрывной (взрывной) – этот метод является самым востребованным как при добыче каменной породы, так и при добыче руды. В камне также пробуривают отверстия, а в них закладывают взрывчатку. При взрыве откалывается множество кусков камня, самые большие собирают и увозят на переработку.
В данном методе требуется большая точность расчетов, любая ошибка приводит к увеличению затрат. Большое количество взрывчатых веществ испортит породу, при недостатке взрывчатки, наоборот, куски получатся слишком большие, их придется раскалывать снова.
Буровзрывной метод самый экономичный и одновременно самый разрушающий, так как при взрыве только 70% породы остается подходящей для дальнейшей переработки, остальные же 30% идут в отсев.
Дробление
Далее куски камней погружают в грузовые машины и отвозят на пункты переработки в бункеры. Из них материал отправляется на питатели (специальные устройства, благодаря которым подача сырья происходит равномерно). Начальные размеры камней достигают 50 – 120 сантиметров, а размер готовой продукции должен быть 0.5 – 12 сантиметров. В процессе дробления куски могут уменьшаться в сотни раз, поэтому работа проходит обычно в 2 – 4 этапа.
Дробление может быть трех видов – крупное (до 30 см), среднее (до 10 см), мелкое (до 4 см). На заводах с современным оборудованием процесс дробления проходит одновременно с сортировкой. На каждом этапе порода проходит предварительную сортировку, когда более крупные камни отделяются от маленьких.
Таким образом дальше в оборудование направляется только те камни, которые нужно измельчить.
Для работы со щебнем применяются 6 видов дробильного оборудования.
- Щековые – применяются на первом этапе дробления. Принцип их действия заключается в безударном раздавливании. Оборудование включает две плиты (щеки), между которых помещают куски гранита. Далее они начинают сближаться, таким образом кроша камни.
- Валковые – работа проходит по такой же системе, что и в щековых дробилках, только вместо плит здесь встроены специальные валы, вращающиеся в разных направлениях. Поверхность валов может быть – гладкая, зубчатая или рифленая.
- Конусные – применяются для измельчения гранита на мелкие и средние размерности. Конструкция таких дробилок сложнее – в стационарной конической емкости находится подвижный конус, вершина которого направлена вверх. Через специальную воронку камни подаются в чащу, а конус совершает возвратно-поступательные движения, сближаясь со стационарным основанием, таким образом измельчая породу.
- Роторные – принцип работы этих дробилок заключается в ударном воздействии. Устройство имеет вид камеры, по краям которой находятся отбойные плиты, а в середине располагается ротор. К нему прикреплены била (лопатки). Гранит, поступающий в дробильный автомат, врезается в отбойные плиты и друг в друга. Работа роторного оборудования отличается высоким уровнем избирательности – то есть большинство гранитных камней имеет форму куба (80 – 85%).
- Молотковые – конструкция таких дробилок идентична предыдущему виду, но вместо лопаток здесь работают молотки. Чаще всего такие дробилки применяются для мягких пород.
- Центробежные – дробилка представляет собой центрифугу, в которой порода на высокой скорости ударяется о ее стенки и друг о друга. На данном оборудовании допускается работа с гранитом до 10 сантиметров.
Сортировка
После того как порода прошла этап дробления, она поступает на сортировочные вибрационные сита – грохота. За характерный шум во время работы они получили такое название. Сортировка может быть такой.
- Предварительная – здесь отделяются камни, не требующие дробления, и некондиция, проводится она перед процессом дробления.
- Контрольная – выполняется после дробления. В процессе отделяется гранит, требующий повторной обработки.
- Товарная – этот вид сортировки, щебень проходит перед подготовкой к продаже.
Основные характеристики
- Лещадость – степень плоскости гранита, характеристика обуславливается наличием в структуре породы включений, имеющих форму игл и пластин. От формы щебенки будет зависеть сцепляемость с различными веществами. Меньший коэффициент лещадости говорит о высоком качестве гранита.
- Прочность – характеристика учитывается при возведении габаритных построек. При сжатии щебня показывается его предел прочности. По нормам действующего ГОСТа процент содержания камней с минимальной прочностью, не должен быть выше 5 единиц.
- Насыпная плотность – характеристика определяет удельный вес 1 м3 в природном состоянии, то есть учитываются пустоты и пор между кусками. От нее напрямую зависит и то, сколько весит материал. Чтобы узнать, сколько тонн в кубе щебня, нужно 1 тонну (1000 кг) разделить на коэффициент насыпной плотности. Многие производители фасуют щебень в мешки по 25, 30, 35, 40, 42, 45, 50, 55, 60 литров. Чтобы узнать, сколько мешков щебня в кубе, можно воспользоваться специальными таблицами. От этого свойства зависит как, будет храниться и транспортироваться продукция, а также сколько цементной смеси потребуется во время строительства. Чем выше коэффициент плотности, тем меньше нужно строительного раствора.
- Морозостойкость – свойство характеризует, какое количество оттаиваний и замораживаний выдерживает щебень. Маркируется буквой «F», а число рядом с ней указывает на сумму повторений заморозки/оттаивания – F15, 25, 50, 100, 150, 200, 300, 400.
- Радиоактивность – учитывается при выборе поставщика продукции. Щебень — это источник радиации, помимо этого, он может ее накапливать. Щебенка подразделяется на 3 категории: 1 – меньше 370 Бк/кг — для постройки жилых и нежилых помещений; 2 – 370 – 740 Бк/кг – для дорожных полотен и оснований заводов; 3 – больше 740 Бк/кг – допустима только для автомагистралей.
- Адгезия – это показатель того, насколько крепко щебенка сцепляется с различными веществами. Самая высокая сцепляемость у породы серых оттенков.
Виды и марки
Всего выделяется пять сортов.
- М1200 – 1400 – высокая прочность.
- М800 – 1200 – прочный щебень.
- М600 – 800 – средняя прочность.
- М300 – 600 – слабая прочность.
- М200 – очень слабая прочность.
Оттенок гранита зависит от территории, где велась добыча вулканического материала. Он может быть с белым, серым, розовым, красным тоном и т. д.
Цветовая палитра обуславливается обилием вкраплений в структуре гранитного камня.
На заводах щебенка подвергается дополнительной обработке.
- Промывка – необходима для очистки материала от пыли и глины. Потребность в промывке возникает, только если превышена допустимая норма наличия глиняных и пылевых частиц. Процесс промывки достаточно трудоемкий и дорогой, к тому же нужна дополнительная просушка продукции. Мытый щебень изготавливается редко и только для определенных целей.
- Пропитка битумом – щебень с данной обработкой применяется в строительстве дорог, его покрывают дегтем, битумом или битумным раствором. Процесс проходит в асфальтосмесительном оборудовании. Битумный или черный щебень нельзя долго хранить, так как срок его использования небольшой, обычно он сразу отправляется на место работ.
- Окрашивание – такая обработка применяется только для декоративных целей. Окрашиваться гранит может на заводах или в домашних условиях. Цветной щебень изготавливается только по предварительному заказу и маленькими партиями. В данном случае стоит помнить о том, что даже самый качественный краситель со временем потускнеет или начнет откалываться.
- Шлифовка (галтовка) – такой гранит также применяется в декоративных работах. Галтованный щебень – это материал, подвергшийся механическому воздействию, в результате которого острые края сглаживаются. Обработка происходит в галтовочном барабане, куда помещается природный камень, абразивные вещества и вода. За счет трения друг об друга и об абразивы происходит процесс шлифовки.
Галтовка – достаточно затратный процесс, поэтому шлифованный щебень изготавливается только по предварительному заказу.
Обзор фракций
Одна из важнейших характеристик щебня – это его фракционность, она присваивается еще на этапе добычи, а затем на этапе обработки гранита. Подразделяется на категории.
- От 0 до 10 мм – ЩПС (щебеночно-песчаная смесь), в составе содержатся такие компоненты, как песок и щебень. По ГОСТу продукция имеет свою гранулометрическую классификацию, соответственно, видов песчано-щебеночной смеси несколько. Отлично подходит в качестве дренажной прослойки, используется при асфальтировании дорог.
- От 5 до 10 мм – гранит мелкой размерности. Продукция отлична своей прочностью и доступной ценовой категорией. Применяется для изготовления бетонных составов, использующихся в работе с массивными и тяжелыми объектами.
- От 5 до 20 мм – это две размерные категории, смешанные вместе. Идеально подходит для закладки оснований домов.
- От 20 до 40 мм – гранит среднего размера, материал нашел свое назначение в заливке оснований жилых домов, заводских помещений, асфальтировании, прокладывании трамвайных линий.
- От 40 до 70 мм – высокопрочные крупноразмерные камни гранита. Применяются на стройках крупномасштабных объектов.
- От 70 до 120 мм, от 150 до 300 мм – гранит большого типоразмера с неправильной формой. ГОСТ для данной категории расписан в специальных таблицах, использующихся при постройке мостов и дамб. Благодаря своей повышенной прочности, его применяют при закладке бутобетонного основания.
Отсев
Фракция от 0 до 5 мм или гранитная крошка – эта категория самая мелкая, появляется она как второстепенный или побочный материал. Внешний вид отсева напоминает песок, но со свойствами гранита.
Используется в обустройстве пешеходных дорожек, тротуаров, парковых зон.
Сферы применения
- В строительстве – для создания бетона, дренажного слоя, для расклинцовки на меньшие размеры, усиления почвы под основаниями зданий, для выравнивания участков и площадок.
- В дорожных работах – для грунтовых, асфальтированных и железных дорог.
- Облагораживание участков – для тропинок и дорожек, въезда на территорию, уплотнения почвы, отсыпки парковочных территорий и спортплощадок, защиты от гололедицы и наледи.
- Для ландшафтного дизайна – оформления цветников, ручьев, искусственных водных объектов, габионов и альпийских горок.
- На производстве – для брусчатки и железобетонной продукции, минеральных сыпучих веществ.
- Инженерные работы – для мостов, плотин и дамб, путепроводов.