Все об автоклавном газобетоне
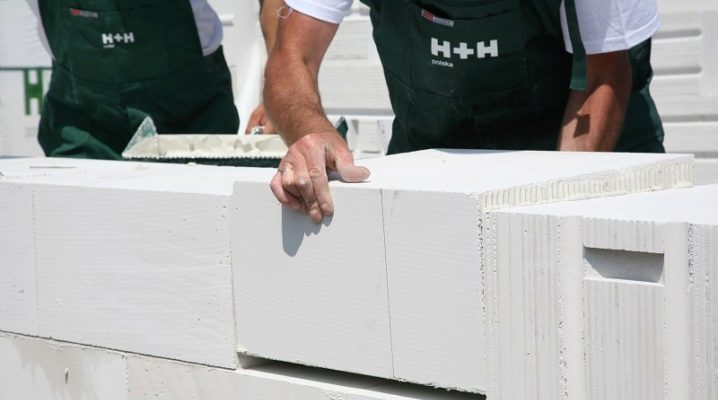
Узнав всё об автоклавном газобетоне, о его преимуществах и недостатках, можно будет грамотно и эффективно применить этот стройматериал. Стоит обратить внимание на отличие от неавтоклавного продукта. Также разумно разобраться и с особенностями технологии производства.
Характеристика
Понятие автоклавный газобетон имеет несколько синонимов:
- лёгкий автоклавный бетон;
- автоклавный ячеистый бетон;
- ячеистый или пористый бетон.
Такой стройматериал начали применять сразу после изобретения в 1920-е годы. Из него могут быть изготовлены газобетонные блоки различных размеров и разнообразного назначения: для основных конструкций, для стен, пола, кровли. По сравнению с традиционными монолитными элементами такое решение легче и удобнее. Долгое время технологические поиски были неудачными, потому что первые образцы оказывались чрезмерно рыхлыми. Однако эту проблему удалось успешно решить, и уже давно такой стройматериал доказал свою перспективность.
При изготовлении автоклавных газоблоков в нашей стране руководствуются нормами ГОСТ 31359 от 2007 года. Их популярность неуклонно возрастает. Изготавливать автоклавный газобетон могут лишь крупные предприятия, поскольку это требует сложной аппаратуры. Пористость материала повышает его стойкость к возгоранию. Производство, использование и даже утилизация не причиняют никакого ущерба природной среде. Так как газобетон очень лёгкий, перевозить его гораздо удобнее и дешевле, чем тот же кирпич
При использовании таких блоков можно избежать появления конденсата внутри помещений. На стены, сделанные из газоблока, легко навешивают тяжёлые предметы — такая нагрузка не причиняет никакого вреда. Однако снаружи фасады придётся покрыть штукатуркой или иным отделочным материалом.
Налажен выпуск автоклавных строительных блоков в форме:
- буквы U;
- буквы T;
- прямоугольника;
- дуги.
В большинстве случаев выпускают газобетонные элементы размером 600х250 мм. Их толщина варьируется от 75 до 500 мм. Если конструкция предусматривает пазы и гребни, то можно обеспечить идеальную гладкость стены.
Технология производства
Начинается всё с выкладки в отдельные бункеры основных сыпучих компонентов готовой смеси. Кроме цемента, в состав автоклавного газобетона входят:
- газообразователи (пудра или паста на основе алюминия);
- кварцевый песок (часто заменяемый золой уноса);
- известь;
- гипс.
Важно: песок и золу требуется изначально размолоть до консистенции муки. Рецептура не содержит никаких токсичных или пагубно сказывающихся на окружающей среде веществ. Она отработана уже давно, и доказано, что именно такое решение гарантирует оптимальную прочность и плотность конструкций. Когда исходные бункеры заполнены, компоненты поступают в ёмкость для перемешивания. Готовое сырьё разбавляют водой в точной пропорции.
Современное оборудование может добиться равномерности образования пор по всей массе создаваемого блока. Эту задачу решает встряхивание, но не простая вибрация, а методика, продуманная инженерами. Важную роль играет камера предварительного созревания, известная также как горячий тоннель. Внутри него цемент гидратируется, одновременно выделяется газ. Обязательное условие успеха — поддержание стабильной температуры от 35 до 40 градусов на протяжении 180–240 минут. При таком режиме бетонный массив вспучивается. Параллельно идёт процесс твердения. Или, более профессионально выражаясь, набирается распалубочная прочность.
Следующий этап производства — струнная резка. Бетонный массив по методу кантования нарезают сразу в 3-х плоскостях. Этот подход гарантирует идеальные геометрические свойства.
Продвинутая аппаратура способна не просто резать материал, но и формировать комплекс паз-гребень, и обустраивать захваты для удержания руками.
Ключевой момент, однако, наступает дальше — производится автоклавирование заготовки. Внутри камеры создаётся давление 12 атмосфер и температура 200 градусов. Применение автоклавов ускоряет набор прочности и увеличивает итоговую стойкость блоков. При условии грамотной обработки они не будут усаживаться. Разумеется, готовый продукт тщательно исследуют в специальной лаборатории, чтобы убедиться в его высоком качестве; перед отправкой заказчику товар тщательно упаковывают.
Изменение свойств при высокотемпературной обработке и повышенном давлении идёт за счёт перемены структуры на молекулярном уровне. Создаётся новый минерал — тоберморит. В обычных условиях его невозможно создать вообще.
Отличие от неавтоклавного
Сразу стоит указать, что прямое сравнение свойств уместно только в отношении химически чистого газобетона. Ряд изготовителей неавтоклавной продукции сглаживает её слабые места за счёт специализированных добавок. Без учёта их возможностей автоклавная масса имеет немало преимуществ, и только незначительно проигрывает по стойкости к воде и к разогреву.
Но всё же покупатели стремятся приобретать именно автоклавный газобетон, несмотря на его частные недостатки. Причина проста: такой стройматериал поставляют солидные фирмы, а неавтоклавный продукт делают где угодно, в том числе и на сомнительных заводах, даже в кустарных мастерских. Фальсификата уже не так много, но он есть. Если нет сомнений в профессионализме конкретного поставщика, можно смело покупать его продукцию в обоих случаях.
После полного затвердевания неавтоклавный газобетон уступает автоклавному как минимум на 50% по прочности. Он склонен также к усадке, которая составляет 3–5 мм на 1 м строительных конструкций, тогда как у автоклавной массы этот показатель не превышает 0,3–0,5 мм. Технологически сложное производство имеет куда больше шансов обеспечить приличную геометрию каждого блока. Благодаря этому свойству кладка существенно упрощается. Да, можно устранять проблему на стройке, при помощи специальной тёрки — но это слишком трудоёмкое решение.
Безусловно, неавтоклавный газобетон куда менее однороден. Технология его производства не позволяет добиться идеального распределения полостей. Уменьшение количества пузырей означает большую прочность, но и повышенную теплопроводность. Неравномерное их нахождение в толще строительного блока делает его свойства неоднородными. Вывод очевиден: это не тот случай, когда экономия при закупках оправдана. Автоклавный газобетон «дышит», то есть создаёт благоприятный микроклимат. Он не будет гнить или заражаться плесенью.
Стойкость к холоду у такого материала очень высокая. Его можно смело применять даже в районах, где регулярно случаются суровые зимы. Распилить блок и придать ему точный размер не составит особенного труда; по сроку службы неавтоклавный материал сильно проигрывает.
Лучшие производители
Существует немало заводов, поставляющих автоклавный бетон потребителям по всей территории России. Однако бесспорное лидерство среди них принадлежит большой тройке компаний, куда входят:
- «Бонолит»;
- «Аэрок»;
- «АэроСтоун».
Предприятие «Элгад-ЗСИ» является одним из крупнейших в центральном регионе. В год в Коломне могут сделать до 400 тысяч кубометров готовых блоков. «Бонолит» располагает производствами в Подмосковье и Калужской области. Эта компания поставляет не только сами конструкции, но и специальный клей для их установки.
Хорошей репутацией отличается и белгородский завод «Аэробел». На нём делают газобетон даже повышенной прочности со всеми стандартными характеристиками. Есть в ассортименте и U-образные модули, рассчитанные как несъёмная опалубка.
Также стоит упомянуть фирмы:
- «Лиски-Газосиликат»;
- «ЭкоБлок 39» (Калининград);
- «РоссБалтТорг» (Ленобласть);
- «Кировгазосиликат»;
- ПЗСП (Пермь).
В Сибири выделяются:
- тюменский завод «Поревит»;
- ООО «Байкальский газобетон»;
- ООО «Комбинат пористых материалов» (торговая марка «Вармит», Омск).
Область применения
Автоклавный газобетон подойдёт для сооружения надёжных и энергоэффективных сооружений, которые не требуется дополнительно утеплять. Он хорошо зарекомендовал себя в жилом строительстве и при возведении общественных зданий. Таким газобетоном можно пользоваться и для реконструкции, и для перепланировки объектов, а также для подготовки крыш, мансард и иных конструктивных элементов. Особая область использования блоков — сооружение подсобных помещений, которые не будут отапливать.
Неавтоклавный бетон формально дешевле, что привлекает к нему внимание частных застройщиков. Но геометрические погрешности, слабая изоляция от утечки тепла и неоднозначная прочность делают такой подход глупым. Придётся израсходовать немало денег на покупку дополнительных кладочных и выравнивающих материалов, а вся выгода сходит на нет.
Качественный автоклавный блок отлично подойдёт для строительства промышленных объектов. Можно пустить его в ход для создания однослойных, двухслойных и комбинированных стен, способных принять нагрузку от верхних этажей. Газобетон позволяет формировать перегородки и стены противопожарного характера. Он оказывается также отличным наполнителем каркаса из обычного бетона либо стали.
Так как плотность материала иногда составляет от 800 до 1000 кг на 1 куб. м, можно применять его в создании плит перекрытий. Если блок менее плотный, то он позволит обеспечить теплоизоляцию чердака или подвала. Применяемые в типовой крупнопанельной застройке упрочнённые панели полосовой разрезки образованы несколькими стандартизированными секциями.