Делаем станки из фанеры своими руками
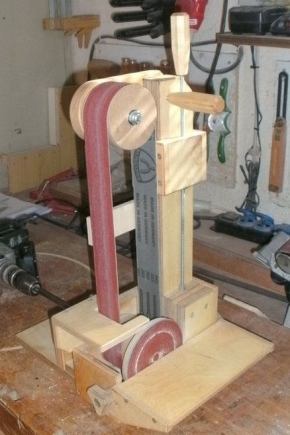
Делать станки из фанеры своими руками не так сложно, как кажется. Обязательно необходимо только изучить базовые чертежи самодельных аппаратов ЧПУ. Умелый подход позволяет делать токарные станки по дереву своими руками и другие самоделки различного профиля.
Особенности
Опытные специалисты давно знают, что самодельные ЧПУ из фанеры в ряде случаев не уступают полноценным металлическим аналогам заводского изготовления. Подобные конструкции используются, конечно, только там, где нет значительных механических напряжений, сильных вибраций, нагрева и необходимости отводить тепло водой. Технические качества фанерных аппаратов вполне могут быть на приличном уровне. При этом стоимость такой техники щадящая.
Внимание: такие системы рассчитаны лишь на частное использование. Фанерный станок не пригодится в качестве полноценного производственного рабочего места. Прежде чем его делать, нужно трезво оценить свои способности и знания в области столярного искусства. При отсутствии специальных навыков и умения работать с электроинструментами о самостоятельном изготовлении станков придется позабыть.
Кроме того, придется внимательно отбирать основной конструкционный материал.
Конструкция
На станки, даже наименее ответственные, нельзя пускать листы толщиной меньше 0,6 см. Во всяком случае, это относится к опорным и несущим частям сборки. Иногда исключение делают для кожухов и других легких частей. Однако и тогда приходится тщательно взвешивать все за и против, чтобы дать правильную оценку отобранным деталям. Ошибки при их выборе могут быть фатальными.
Некоторые эксперты полагают, что листа толщиной от 1 до 1,2 см вполне достаточно для отдельных станков, к примеру, если речь идет о раскройном столе. Другие специалисты исходят из того, что нужны всегда части большой толщины, даже для второстепенных участков конструкции. Существует также мнение, что склеенные из средней по толщине фанеры объемные детали эффективнее гасят вредные колебания при эпизодической вибрации. Но настоящие мастера всегда отдают предпочтение соображениям надежности и безопасности. Потому-то они стараются максимально использовать фанерные листы толщиной от 19 мм и более, несмотря на тяжесть и значительные цены.
Но ориентироваться только на одну толщину не следует. Обязательно надо учитывать тип исходной древесины. Хвойное дерево легче и мягче, его применяют главным образом для второстепенных узлов. Лиственный шпон дороже, и все же его используют чаще. А вот различия химического состава клеев и уровень стойкости к влаге практически не играют роли, вполне достаточно в большинстве случаев фанеры сорта ФК.
Что куда значимее, так это категория шпона. Увеличение числа сучков грозит растрескиванием и расслоением. Опытные профессионалы стараются брать листы второго сорта и выше. Не стоит пытаться покупать очень дешевый нешлифованный материал. Довести его до нужных параметров в кустарных условиях практически нереально.
Полностью шлифованные заготовки к тому же легче клеить.
В качестве оптимального кустарного образца можно рассматривать фанерный станок 4 в 1. Такая конструкция подразумевает использование коробки размером 54х32х88 см и стола величиной 65х98 см. Фанера на эти части идет толщиной 10 и 18 мм соответственно. Сечение дискового шлифовального узла в норме составит 18 см. Для работы по дереву нужен иной аппарат, типы резко отличаются, а именно:
- распиливающий на базе ручной циркулярной пилы;
- лобзиковый;
- с применением дрели;
- универсальная модель, подходящая для навешивания различных приспособлений.
Варианты самоделок
На основе фанеры вполне можно изготовить приличный токарный станок. Для работы понадобятся, кроме самого материала, следующие элементы:
- клей;
- пила циркулярная и пила торцовочная;
- карандаш или маркер, линейка (для отметок);
- фиксирующие струбцины;
- подшипники, краска, шурупы, шуруповерт;
- пластина из металла, электродвигатель и шкив;
- ряд других деталей.
Для формирования основания станка применяют клееную фанеру толщиной 1,2 см. После нарезки и склеивания заготовок края торцуют, а пазы используют для установки стоек. Переднюю бабку также делают из фанеры, в ней необходимо просверлить отверстие под подшипник. Некоторые гайки и шайбы целесообразно сажать на клей. Ширина платформы и направляющей части должна совпадать, причем качественно сделанная платформа с зажимами свободно ходит в двух плоскостях.
Изготовление задней и передней бабок не отличается. Обе они требуют специальной защиты. Крепить силовой привод нужно на доску, соединяемую с основанием при помощи петли. Чтобы сделать шпиндель, требуется приварить две гайки в шайбе, а потом проделать «зубы» в гайке. Станок обязательно окрашивают.
Из фанеры можно сделать, разумеется, еще и сверлильный аппарат. Поскольку он обычно рассчитывается на сравнительно небольшие заготовки, можно применять фанерные листы толщиной 1 см. Все детали требуется подгонять максимально плотно, чтобы не было визуально заметных разрывов. Важно: листовой материал плохо переносит грубые механические воздействия, поэтому стыковка частей на гвозди и саморезы будет плохой идеей, можно применять лишь шипы и пазы, да еще иногда клей ПВА для максимального упрочнения.
Если планируется с помощью фанерного станка сверлить другие фанерные заготовки, требуется предусмотреть место для подкладки еще одного листа. В противном случае обрабатываемые изделия могут растрескаться и даже расколоться. Окрашивание аппаратов для сверления не слишком оправдано. Они подвергаются очень интенсивным вибрационным, тепловым и механическим воздействиям. А вот нанесение грунтовки очень даже полезно, особенно в мастерских, лишенных отопления.
Возможна и сборка фрезерных или деревообрабатывающих станков с ЧПУ. Траектория обрабатывающей части (как и в других типах) рассчитывается по трем осям. Если места в мастерской не хватает, можно использовать универсальные станины, рассчитанные на широкий спектр инструментов. Обычно рабочее поле составляет 60х90 см с вертикальным ходом 25 см.
Но если сделать чуть меньше, то никаких проблем обычно не возникает.
Есть две основных схемы устройства любых фанерных самодельных станков. В одном варианте движется стол, а портал остается неподвижен, во втором – роли меняются. Первый способ позволяет упростить конструкцию, но пригоден лишь для очень малых рабочих столов. Поэтому на практике гораздо чаще используют подход с перемещением портала и неподвижностью стола. Но и во второй схеме могут быть частные варианты.
Прежде всего, они касаются использования единственного центрального или двух боковых приводов. Вариант с 2 приводами подходит для сравнительно громоздких конструкций. Он позволяет минимизировать риск перекашивания портала относительно направляющих. При этом вся сборка имеет отличную жесткость. Величина обрабатываемой области определяется теми задачами, которые предстоит решать.
Чем больше станок, тем дороже он выходит, а кроме того, на мелких моделях проще исправить ошибки.
Часто полагают, что геометрия портала, пропорции дистанции между осями и рабочими направляющими, промежутки между подшипниками могут быть рассчитаны только с учетом сопромата и точной механики. Это во многом верно, но базовые моменты доступны даже неспециалистам, а именно:
- уменьшение зазора над столом позволяет повысить жесткость конструкции;
- оси тоже следует делать жестче и не слишком большой длины;
- по возможности следует наращивать разрыв между направляющими по оси X, чтобы уменьшить ненормальное закручивание;
- центр тяжести портала должен соответствовать точке расположения фрезы и при этом оказываться между подшипниками оси Y (из-за этого часто вертикальные стойки изгибаются назад);
- требуется применять только приводные винты ШВП, дающие наименьший люфт;
- винт должен оснащаться парой независимых подшипников и присоединяться к мотору через гибкую муфту (тогда достигается баланс простоты и качества)
- сборка всех ключевых деталей может вестись на ящичных шипах (это куда эстетичнее, чем топорщащиеся во все стороны гайки).
Как сделать своими руками?
Особой необходимости искать готовые чертежи нет. Можно отталкиваться от схем металлических станков. Все равно каждое такое изделие уникально и оптимизируется под специфические задачи, под личные потребности владельцев. Однако необходимо обратить внимание на образцовые фотографии. Фанерные станки можно сделать как следует только при помощи качественного электроинструмента. Если листы до 1 см толщиной пилит лобзик, то более толстые обычно обрабатывают дисковой или циркулярной пилой. Впрочем, продвинутые электролобзики могут справиться и с распилом фанерных листов толщиной до 2 см.
Выбрать пазы и отверстия поможет ручная фреза. Двигать инструментами нужно плавно, чтобы минимизировать сколы. То же самое достигается использованием простого скотча. После окончательной сборки все поверхности и грани требуется отшлифовать. В качестве грунта можно применять смесь воды и ПВА в равных долях.
О том, как сделать ленточный шлифовальный станок из фанеры своими руками, вы можете узнать из видео ниже.