Все об экструдерах
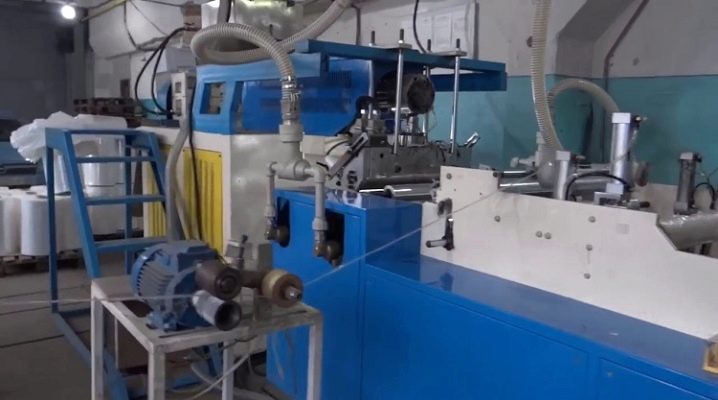
Экструдер упрощает механическую обработку в производственном цикле. Из материала данной статьи вы узнаете, что он собой представляет, как работает, каким бывает и где применяется.
Что это такое?
Экструдер – специальный агрегат, с помощью которого изготавливают длинномерные изделия из пластичного, сыпучего либо гранулированного сырья экструзионным методом. Это основной рабочий орган экструзивной линии. У него несколько ключевых функций. Он нужен для создания необходимого запаса сырья, его расплавления, дегазации, гомогенизации. Он формует и калибрует изделия. Экструзия выполняется путем непрерывного выдавливания расплавленного, пастообразного материала сквозь формовку.
При этом обеспечивается бесперебойное изготовление изделий заданного размера и формы. Для создания потока экструзивной линии техника может совмещаться с другим оборудованием. Она высокопроизводительна, отличается высокой точностью формообразования. Благодаря регулировке экструдеры допускают изменение толщины и ширины продукции. У них несложное техобслуживание. Оператор затрачивает минимум физических усилий для управления устройством.
Устройство и принцип работы
Устройство экструдера зависит от его вида, однако у всех установок есть общие принципы конструирования, а именно основные узлы. К ним относятся цилиндр, фильерная пластина, редуктор, узел загрузки сырья, рабочий орган, механический блок, ножи, блок управления и контроля. Ключевым элементом конструкции является бункер, необходимый для непрерывного функционирования оборудования. Внутри него создают нужный запас сырья. Загрузка сырья в дозатор может быть ручной либо механизированной. Подающим механизмом является плунжер или шнек. Он располагается в цилиндрическом корпусе. Вал имеет винтовую поверхность. При вращении происходит движение сырья, его проталкивание по цилиндру к формующим насадкам.
Важным узлом является формующий инструмент. Он крепится в специальной головке, где предусмотрена коррекция положения. Исходя из назначения установки, в экструдере создается выход заданных размера и формы (круглой, прямоугольной, щелевидной, иной). В оборудовании предусмотрена нагревательная система (ТЭН). Необходимая температура внутри цилиндра поддерживается нагревательными обмотками, закрепленными сверху корпуса. Сырье в цилиндре перемешивается и нагревается за счет кольцевых нагревателей или надежных и долговечных резистивных систем.
Сырье нагревается постепенно, поскольку у установки есть несколько зон с различными значениями температуры. Нужные показатели нагревателя оператор может установить самостоятельно, затем они будут автоматически поддерживаться. Еще одним ключевым узлом является привод механизма. Мощный электрический двигатель, необходимый для задания движения рабочему органу, имеет регулировку скорости вращения. У оборудования есть контролирующие приборы. Благодаря им обеспечивается качество изделий, они нужны для регистрации температуры нагревателя, скорости вращения, поступательного движения продукции.
Любой экструдер работает по принципу мясорубки. Имеющийся загрузчик помещает сырьевую массу в бункер. Для гранул предусмотрена загрузочная воронка. Затем происходит движение материала в цилиндр пластификации. По ходу пути масса перемешивается до состояния однородности расплава.
В зависимости от типа оборудования она подвергается воздействию заданной температуры, а также давлению экструдерных элементов. Благодаря растягиванию и плавлению она набухает, становится вязкой и прозрачной на выходе.
Дисковый аппарат снабжен двумя дисками, выполняющими функцию транспортировки. Один из них неподвижен, другой находится в постоянном вращении. При поступлении сырья в отверстие статичного диска происходит перемешивание и гомогенизация. Данные устройства используются в экструзионных линиях, где необходима однородность смесей. Сырье, поступающее в обработку, далеко не всегда идеально. Поэтому производственный процесс протекает с этапом дегазации. Таким образом из материала удаляются примеси, избыток влаги и воздух. Дегазационный процесс считается обязательным при использовании гранулированного материала.
Рабочее сырье для экструзии бывает разным. Например, в производстве пленочных изделий применяются такие материалы, как полипропилен, полиамид, поликарбонат, лавсан, ПВХ, экструзивный полиэтилен. Экструзия пленок происходит путем раздува рукава и плоскощелевым способом. В первом случае воздух поступает через дорн под давлением.
Материал может охлаждаться двумя способами. При вертикальном или горизонтальном направлении рукава воздух, обдувающий пленку, поступает через кольцо-охладитель по периметру рукава. Когда рукав отводится вниз, применяется водяное охлаждение. Тем самым сокращается период кристаллизации. Остывшая пленка складывается в полотно и поступает в намотку. Когда применяется способ плоскощелевой экструзии, пленка охлаждается 2-мя методами. Она подается на охлаждающий барабан либо пропускается через ванну с проточной водой. Затем поступает на натягивающие валы и наматывается.
В ручном экструдере пластик сначала нагревается до вязкого состояния, после чего выдавливается в зону сварки. Материал разогревается за счет горячего воздуха. Спустя некоторое время он подается в зону размельчения. После раздробления пластика масса отправляется в плавильную зону. Гомогенизированная масса под давлением подается в сварочную зону, выдавливается полосой на детали, которые подлежат соединению. В дальнейшем происходит остывание соединения.
Особенности и характеристики оборудования
В зависимости от вида устройств у них разнится число и тип используемых винтов. Одновинтовой экструдер прост в обслуживании в сравнении с аналогами другого типа. Им управляет 1 оператор, поскольку элементы управления располагаются в 1-м месте. Если машина является частью крупной производственной линии, не обойтись без вспомогательного работника. Число операторов зависит от технологии и целей производства. Аппараты мобильны. При необходимости их можно перемещать на новое место, перевозить с одного завода на другой. Однако мобильность определяется видом экструдера и его назначением.
У некоторых установок есть встроенная функция самоочищения, что упрощает обслуживание и продлевает срок службы. Помимо того, экструдеры оснащаются датчиками и регулировкой, необходимой для создания оптимальных условий при производстве высококачественной продукции.
Помимо надзора за работой тепловой автоматики, изменения диаметра и формы, возможна регулировка вращения винта. Так удается повысить производительность и улучшить качество.
Применение экструдеров способствует усовершенствованию существующего оборудования, автоматизации систем управления, а также использованию новых комбинаций полимеров. Современные модели экструдеров не требуют частого ремонта и больших эксплуатационных расходов. С их помощью можно изготавливать изделия той длины и ширины, которая нужна производителю. Модели, функционирующие по типу гранулятора, не особо эффективны в плане обеззараживания загружаемого материала. Они позволяют получить на выходе мелкие твердые гранулы.
Пищевые модификации способны перерабатывать не только сухие, но и влажные материалы. Принцип работы аналогичен традиционным вариантам. После загрузки происходит уплотнение и выдавливание массы. В ассортименте поставщиков предложен широкий спектр запчастей для установок, что позволяет продлить срок службы. Например, к ним относятся редукторы для шнековых моделей с односторонним, сонаправленным вращением, противотоком.
Виды
Классифицировать экструдеры можно по разным характеристикам. Например, они разнятся конструктивными особенностями, скоростью вращения. По последнему признаку их делят на устройства традиционного и быстроходного типа. Исходя из конструкционных особенностей, выделяют технику для холодного, теплого и горячего формования. В первом случае формовка осуществляется путем механического давления.
Второй способ предполагает механическое преобразование и тепловую обработку. При горячей экструзии происходит ускоренная обработка полимера, протекающая при высокой температуре и под давлением. По направлению вращения экструдеры бывают сонаправленными и противонаправленными. По назначению выделяют установки для профиля из поливинилхлорида, производства полиэтилена, модели трубного типа, технологические линии. Каждый вид имеет свои особенности.
Модификации первого вида применяются в производстве тончайших нитей, полос, листового, панельного, профильного материала со сложной геометрией. Используемое сырье – традиционный либо со взвесями полимер, благодаря чему удается изготавливать композитные продукты. Трубные экструдеры отличаются требованиями к используемым полимерным смесям. Готовый сырьевой материал не может иметь воздушных пузырьков. Иначе не избежать неоднородности и непрочности готовой продукции. В установках встроен дегазатор.
В продаже есть ручной, двойной шнековый, выдувной, полимерпесчаный, бытовой и производственный типы изделий. Кроме того, сегодня выпускают станки для 3D-принтера. Его ключевыми элементами являются подавляющий механизм и печатающая головка. Такие установки делятся на 2 типа, которые отличаются между собой удалением механизма подачи от печатающей головки и весом конструкций. Оборудование разнится видом транспортирующего устройства.
В производственных линиях используют шнековые, дисковые, поршневые, а также комбинированные виды техники.
Шнековый
В установках шнекового (червячного, одновинтового) типа сырье на формующий инструмент подается посредством винта Архимеда. Аналогичный винт применяется в классических мясорубках. Он необходим для захвата сырья, его уплотнения и продавливания сквозь формовку. Длина шнека, исходя из типа перерабатываемого материала, может разниться. При движении винта по спирали происходит прогрев материала до необходимой температуры, а также гомогенизация, удаление газов. Шнековый экструдер относится к наиболее распространенным разновидностям.
Данные модификации разнятся числом рабочих органов. Например, у них может быть разное число винтов, что отражается на характеристиках. В одношнековых устройствах переработка осуществляется одним винтом. Двухшнековый экструдер применяется при потребности в тщательной гомогенизации материала. Их используют при работе с порошковыми полуфабрикатами. У таких устройств 2 параллельных шнека, взаимно зацепленные. Они вращаются не только в одном, но и в разных направлениях. Помимо одно- и двухшнековых разновидностей, в производстве используются установки многошнекового типа. Их применяют для обеспечения максимально тщательного перемешивания сырьевого материала.
Плунжерный
В отличие от предыдущих видов у поршневых аналогов в камеру подается дозированный объем материала. Он выдавливается из агрегата из-за давления поршня или насоса. Благодаря сжатию достигается нужная форма.
Данная технология применяется в производстве штучных изделий с точной геометрией и параметрами. Классические примеры – изготовление таблетированной продукции, изделий из пластмассы и резины. Данные модификации считаются низкопроизводительными. Их применение ограничивается преимущественно производством труб.
Плоскощелевой
В установках плоскощелевого типа имеется узкая щель для выдавливания подготовленного материала. Благодаря этому удается изготавливать изделия с минимальной толщиной. Например, на данном оборудовании производят пленку, а также иную рулонную продукцию.
При этом материал может подаваться на установку посредством шнека, плунжера либо иного компонента.
Где применяются?
Экструдеры используются в разных сферах промышленности. Сегодня без них невозможны многие процессы. Они применяются в том числе и для сварки полиэтилена низкого и высокого давления (ПНД и ПВД). Например, они востребованы в химической промышленности. С их помощью производят полимерные изделия (из пластика, резины, другого сырья), получают ферриты. Экструдер не меняет химический состав.
Установки, применяемые для переработки пластмассы и резины, включают богатый перечень продукции. Например, в эту группу входит оборудование для выпуска пленок, рулонного продукта, изоляции кабельных изделий. Экструдеры нашли применение в переработке вторичного сырья. Благодаря им удалось наладить производство пластмассовых отходов (бутылок, пакетов, банок). Среди прочих видов выделяют кормовые установки. Это шнековые разновидности, используемые для переработки зерна и травы для производства комбикорма с заданной структурой для животных.
У переработанного материала повышается пищевая ценность. При этом возможно производство продукта без химических взвесей и гормональных компонентов. Подобные системы разнятся видом готового материала на выходе. В первом случае он длинный трубчатый, во втором – гранулированный. Оборудование активно используется в пищевой промышленности. Для этого применяются установки с холодной формовкой. Например, техника для производства крабовых, кукурузных палочек и макаронных изделий, где полуфабрикатом является тесто. Наряду с этим, экструдеры для пищевой промышленности востребованы в производстве чипсов, соевых продуктов, жевательной резинки. Массу уплотняют и выдавливают из фильер.
Данную технику используют в кондитерской сфере, изготавливая конфеты, батончики, иные кондитерские изделия. Экструдеры используются в фармакологии. Благодаря высокой точности дозировки на них изготавливают таблетки. Кроме того, они нужны для производства топливных брикетов, их прессовки и брикетирования. При этом в переработку может поступать разная биомасса. Чаще всего это торф, угольная пыль, подсолнечниковая шелуха, отходы сахарного производства, щепки и сухая трава. Среди прочих сфер применения установки используются при изготовлении хозяйственного мыла, труб, полиэтиленовых пакетов с ручками, для выдува рукавной пленки.
Критерии выбора
Выбирая установку, нужно учесть тип модели, ее назначение и ключевые характеристики.
- Одним из ключевых факторов является мощность устройства. Она определяет работу всех узлов, включая подачу, измельчение, нагрев, перемешивание сырьевого материала. От нее зависят скорость работы и объем выпуска.
- Важным моментом является производительность, отображающая объем продукции, выпускаемой за час работы. У профессионального оборудования данный показатель высокий. Для небольшого объема работ достаточно бытовой модели.
- Нельзя забывать о потенциальных нагрузках и условиях эксплуатации. Возможности агрегатов зависят от их мощности.
- Важно помнить о нюансах системы управления. В дешевых модификациях встроены механические устройства для регулировки температуры и скорости подачи сырья для переработки. Продвинутые приборы снабжены цифровыми системами и монитором. Кроме того, у них имеется система, отслеживающая изменение температуры окружающей среды.
- Устройства разнятся типом используемого сырья. Выбирать то или иное оборудование нужно с учетом запланированных задач.
- Также учитывается и скорость работы. Например, профессиональные кормовые варианты увеличивают цену конечного продукта без особых энерго- и трудозатрат. Процесс протекает автоматизировано и занимает несколько секунд.
При выборе ручного аппарата для сварки обращают внимание не только на мощность, диаметр прутка и тип подаваемого сырья, но также на толщину соединяемых изделий и органы управления. Чем выше показатели мощности станка, тем большая толщина соединения изделий ему под силу. Этот параметр важен не только для производства, но и для ремонта, поскольку не всегда есть потребность в сварке толстого листового материала.
Значения нижнего порога составляют 1,5 мм. Верхний предел может доходить до 4 см. Однако, чем больше толщина, тем меньше прочность сварочного шва. Это связано с нагревом и расплавом заготовки на всю глубину.