Все об экструдерах для пластика
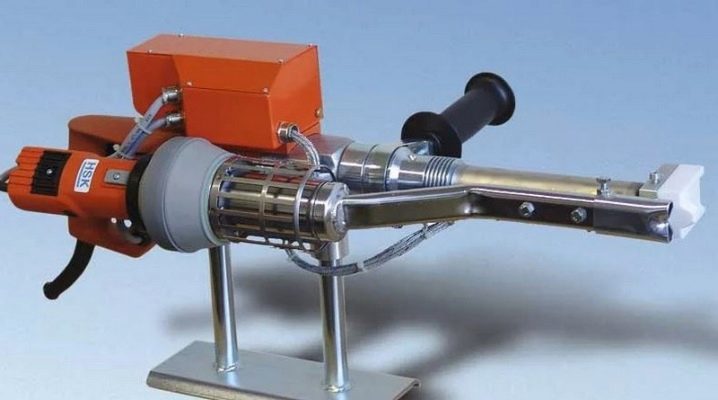
Активное развитие современных отраслей приводит к постоянному внедрению передовых производственных технологий. Это позволяет выпускать широкий ассортимент изделий самого разного назначения с максимально высокими эксплуатационными показателями. На данный момент экструзия является оной из наиболее распространенных технологий. Именно поэтому многие стремятся узнать все об экструдерах для пластика, включая нюансы выбора подобного современного оборудования.
Что это такое?
Массовое применение полимеров в промышленности и бытовых условиях сделало актуальным, в том числе, восстановление и ремонт различных изделий из пластиков. Параллельно речь идет о качественном и надежном соединении различных деталей и конструктивных элементов, выполненных из соответствующих материалов. Примечательно, что как в ситуации с металлическими изделиями работы являются сварочными. То есть технология базируется на разогревании используемого материала и его подаче к месту стыка.
Здесь важно учесть, что сравнительно невысокая температура плавления ПВХ, полиэтилена и полистирола не позволяет сильно прогревать соединяемые заготовки. Также отсутствует возможность применения напряжения, поскольку пластик сам по себе является диэлектриком. В подобных ситуациях единственным рациональным выходом и эффективным техническим решением становится ручной сварочный экструдер для обработки полимеров. По своей сути описываемое оборудование представляет собой прибор, осуществляющий непрерывную переработку пластика. В итоге формируется расплав, имеющий однородную структуру. Форма ему придается в процессе продавливания через специальную (экструзионную) насадку (головку) и калибрующее устройство.
Устройство и принцип работы
Изначально важно отметить, что речь пойдет об электромеханических приборах. Их главное предназначение – это формовка полимера, а также соответствующих полуфабрикатов. Изучив чертежи подобной техники, можно понять, что ее элементами являются следующие составляющие.
- Зона загрузки – узел, в который происходит закладка исходных композитных материалов различными способами.
- Узел нагрева исходного пластикового материала. Здесь в роли источников соответствующей энергии с учетом модели и специфики оборудования выступают системы резистивного или же индукционного типа. Во втором случае рабочая температура обеспечивается в результате наведения на сегмент переплавки токов Фуко.
- Основной рабочий узел. Именно здесь создается зона повышенного давления, за счет которого происходит смещение сырья от загрузочного блока к формовочным насадкам. Используются различные варианты рабочих механизмов. В современных моделях экструдеров для полимерных материалов устанавливаются агрегаты поршневого, шнекового и дискового типа. На практике чаще всего используется второй вариант.
- Экструзионная (формовочная) головка, которую специалисты именуют фильерой.
- Привод, представленный редукторным узлом и силовым агрегатом (электродвигателем).
- Блок контроля и управления, отвечающий за производственный процесс и соответствие параметров готовых изделий.
Анализируя, как именно работает любой экструдер, важно изначально отметить, что исходным материалом чаще всего являются гранулы или же порошок. Он помещается в отсек загрузки, после чего под действием шнеков происходит его перемещение в основную рабочую зону. На следующем этапе осуществляется плавление исходного сырья одним из следующих способов:
- высокое давление;
- интенсивное трение;
- повышение температуры.
В процессе перемещения материала в корпусе экструдера выполняется его интенсивное перемешивание. На выходе формируется однородный гомогенизированный состав. Под давлением расплав пропускается в фильтрующие элементы сетчатого типа и в формующие насадки (головки). На завершающем этапе выполняется окончательная гомогенизация, и пластику придается нужная форма. После завершения процесса изделия охлаждаются естественным путем или же с применением дополнительного воздействия с последующей полимеризацией.
Виды и модели
На сегодня компании, специализирующиеся на разработке и выпуске экструдеров для разных пластиков, предлагают в соответствующем сегменте рынка современного оборудования более чем широкий ассортимент модификаций разных видов. И речь идет как о больших профессиональных, так и о ручных мини-аппаратах. Кстати, существуют также экструдеры и грануляторы для переработки полимерных материалов. Опираясь на обзоры и отзывы, к числу популярных и хорошо зарекомендовавших себя моделей можно отнести следующие.
- StarGun R-SB 50 от Ritmo – аппарат, главными характеристиками которого являются высокая мощность и соответствующая производительность (показатели выхода полимерного материала достигают отметки 5 кг/ч).
- Leister Fusion 3C-123.866 – универсальный благодаря широкому перечню регулировок экструдер, отличающийся компактностью на фоне высокой производительности.
- MAK-18SB – представитель модельного ряда популярного бренда Munsch, относящийся к бюджетному ценовому сегменту и пользующийся заслуженным спросом. Из-за сравнительно небольшой мощности данный аппарат нельзя охарактеризовать как профессиональный, однако его более чем достаточно для выполнения небольших объемов тонких работ.
Помимо всего прочего, стоит заметить, что качественный экструдер обойдется недешево. На данный момент функциональность, надежность и, соответственно, срок эксплуатации оборудования будут пропорциональны его цене.
Одношнековый
Из всего разнообразия, существующего на сегодня экструзионного оборудования, самым распространенным видом являются шнековые модели. Эти установки в полной мере отвечают всем актуальным требованиям, предъявляемым к реализации самого процесса и качеству готовой продукции. Исходя из названия категории, можно понять, что основным конструктивным элементом таких экструдеров является шнек, который специалисты именуют «винт Архимеда». Кстати, он хорошо знаком тем, кто пользовался бытовой мясорубкой. Простота конструкции оборудования позволяет изготавливать его своими руками и достаточно успешно эксплуатировать самодельный образец.
В процессе работы шнекового аппарата лопасти основного инструмента захватывают полимерный материал в отсеке загрузки, после чего сырье перемещается вдоль всего цилиндрического корпуса. Последний включает в себя камеру нагрева, отсек гомогенизации и зону формовки. Важно учесть, что ключевыми факторами будут технологическая карта экструдера и тип самого загружаемого сырья. С их учетом шнеки делятся на быстроходные, цилиндрические, а также конические и имеющие сужение на выходе.Помимо всего перечисленного, стоит заметить, что описываемые образцы техники классифицируют также с учетом соотношения диаметра и длины главного рабочего элемента. Параллельно учитываются такие параметры, как шаг витков шнека и их глубина.
Наиболее значимый недостаток одношнековых аппаратов для работы с пластиками – это ограниченность возможности их использования. К примеру, если сырьем является порошковый полуфабрикат, то один «винт Архимеда» не справится с качественным перемешиванием исходника в рамках его плавки и процесса гомогенизации. В таких случаях потребуются модели, оснащенные двумя рабочими элементами.
Двухшнековый
Ключевая особенность таких сварочных приборов сводится к тому, что у них рабочий инструмент представлен двумя сцепленными винтами. Также важно, что шнеки способны двигаться как параллельно, так и навстречу друг другу. А сами они бывают прямой и конической формы. Главное преимущество двухшнековых аппаратов заключается в более качественных смешивании и гомогенизации исходного сырья в процессе его плавления. В итоге к формовочной насадке поступает максимально однородная и при этом полностью дегазированная смесь.
Важно, что некоторые технологии и производственные процессы предусматривают использование экструдеров, оснащенных 4 шнеками. Но и это не является приделом. Нередко применяют машины планетарного типа, в которых присутствуют до 20 винтов, вращающихся вокруг основного (центрального) рабочего элемента. Такое усовершенствованное оборудование актуально в ситуациях, когда в качестве исходников для производства используют особые виды сырья. Здесь ключевой момент заключается в том, что такие пластики при высоких температурах проявляют склонность к существенной деформации и даже разрушению. Применение планетарных экструдеров позволяет осуществлять нагрев пластмассы посредством силы трения и повышения давления.
Для ПВХ-профиля
Данная разновидность композитных профилей сейчас пользуется рекордным и вполне заслуженным спросом. Подавляющее большинство компаний-производителей при их изготовлении успешно используют описываемую технологию. Для производства листового полипропилена, включая листы ПНД, то есть изделий из полиэтилена низкого давления, применяют как одно-, так и двухшнековые аппараты. Здесь ключевым моментом является выбор формовочных головок с учетом особенностей используемого при переработке сырья.
На сегодня при помощи рассматриваемой категории экструдеров выпускается более чем широкий ассортимент продукции: от пластиковой нити с минимальным сечением до крупногабаритных листовых панелей, имеющих сложную геометрию. Кстати, исходным материалом для массово выпускаемых в наши дни оконных конструкций являются именно профили из ПВХ. Последние, в свою очередь, – это результат применения экструзионных аппаратов.
Для производства труб
В промышленном производстве данного типа пластиковых изделий один из ключевых моментов – это отсутствие в составе гомогенизированной массы пузырьков газа. Именно поэтому неотъемлемой составляющей конструкций специализированных экструдеров являются современные системы дегазации. Как правило, для производства труб из полимерных материалов используют модели шнекового типа. Не менее успешно при изготовлении полимерной трубной продукции применяются шнеки барьерного типа. Это оборудование обеспечивает качественное отделение полного расплава от твердого сырья. Именно благодаря этой особенности производственного процесса достигается максимальная однородность составов.
В итоге многократно повышаются эксплуатационные качества готовых труб.
Для производства пленки
На сегодня все виды пленок, сырьем для которых являются полимерные материалы, изготавливаются с применением экструзии. В производственных масштабах при этом используются выдувные аппараты. Так, одной из ключевых особенностей экструзионных устройств, применяемых для изготовления стрейчевых пленок, является особая форма формовочного узла в виде максимально узкой щели. Результат работы такой техники – высококачественное, однослойное полотно. При этом в процессе изготовления задаются все необходимые параметры будущей продукции (ширина рулона и толщина пленки). Некоторые образцы техники комплектуются круглыми щелевыми фильерами крупного диаметра. Компактные аппараты позволяют делать пленку, ширина и толщина которой составляет 0,3 м и 600 мкм.
Такие модели эффективно эксплуатируются в условиях ограниченного пространства.
Критерии выбора
Сфера применения рассматриваемых устройств и, соответственно, выбор конкретной модели напрямую определяются ключевыми характеристиками.
- Мощность, являющаяся одним из ключевых параметров и определяющая работу всех узлов экструдера: шнекового привода, отвечающего за подачу, измельчение и перемешивание пластика, а также нагревателя. У большинства доступных сейчас на рынке образцов описываемой техники данный показатель варьируется в диапазоне 1,6-3,6 кВт. Естественно, от мощности будет напрямую зависеть скорость и объем выполняемых работ.
- Производительность – характеристика, которая отображает количество готовой для использования пластиковой массы, вырабатываемой устройством в течение часа. Чем выше показатель, тем более подходящим для профессионального использования и выполнения больших объемов работ будет аппарат. Современные модели, представленные на рынке экструзионного оборудования, демонстрируют производительность от 0,5 до 3 кг/ч.
- Потенциальные нагрузки и условия эксплуатации. Здесь речь идет, в частности, о толщине соединяемых заготовок и конструктивных элементов пластиковых изделий. Стоит акцентировать внимание на линейной зависимости возможностей аппаратов от их мощности. Как правило, нижний порог фиксируется на отметке 1,5 мм. В принципе, возможно соединение и более тонких элементов, но стоит учесть возможность их деформации. Верхний предел у мощных моделей достигает 4 см.
- Диаметр используемого при выполнении работ прутка. Конечно же, данный критерий является актуальным для моделей с подачей исходного материала в виде стержня. Значения для профессиональных экструдеров составляют 5-6 мм. Если будут другие параметры, может значительно понизиться производительность. При эксплуатации компактных аппаратов используют пруток диаметром 3 мм.
- Система управления. Модели, относящиеся к бюджетному сегменту, оснащаются механическими устройствами, регулирующими температуру и скорость подачи материала. Более продвинутые приборы имеют цифровые системы с мониторами, а также нередко датчики температуры окружающей среды.
Помимо всего перечисленного, в перечень критериев выбора следует включить тип используемого исходного материала. В экструдерах его функции выполняет гранулят или же присадочный пруток. Стоит отметить, что второй вариант на практике оказался более востребованным, а следовательно, самым распространенным. Первая причина подобной популярности – это удобство транспортировки скрученного в бухты прутка. И даже при повреждениях упаковки материал не утрачивает своих эксплуатационных качеств. Это выгодно отличает данную форму сырья от гранулята.
Подача прутка через приемную камеру осуществляется до тех пор, пока бухта полностью не размотается. В ходе выполнения работ и эксплуатации экструдера требуется только периодически немного высвобождать по несколько витков. Гранулированный материал засыпается в специальный загрузочный бункер, который предварительно необходимо будет отсоединить. Контейнеры открытого типа существенно усложняют использование приборов, поскольку из них материал может высыпаться. Получается, что с прутком намного проще работать.
О том, как правильно выбрать экструдера для пластика, смотрите в следующем видео.