Выбираем экструдер для кормов
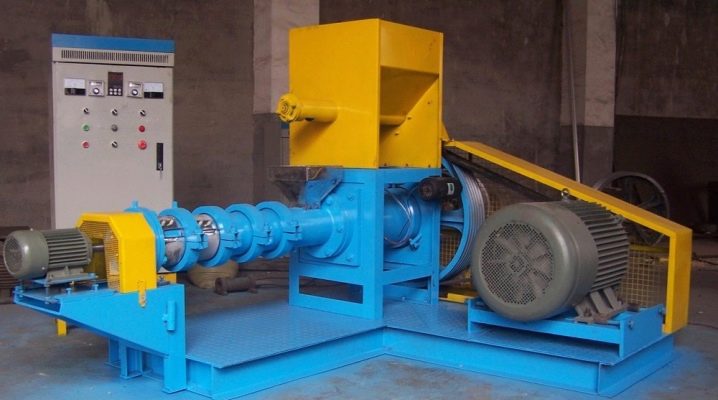
Выбирать экструдер для кормов очень часто приходится владельцам животноводческих ферм — и не только им, впрочем. В любом случае точное знание принципа работы кормового зернового гранулятора крайне актуально. А также стоит четко разделить бытовые и промышленные модели для производства комбикорма.
Что это такое?
Экструдер для кормов — отличный источник качественного питания для сельскохозяйственных животных, позволяющий заметно экономить. При выдаче свиньям сухого молотого зерна применение продуманного кормового гранулятора для производства комбикорма позволяет тратить на 30% меньше злаков. При этом привесы и показатели здоровья подопечного стада не изменятся. Устройство отлично проявляет себя и при получении кормов для других видов скота и птицы. Конкретная экономичность зависит от того, выдается ли пища в твердом виде или после варки каши.
Подобный привлекательный эффект обеспечивается наращиванием усвоения корма.
Экструзия приводит к изменению сложных молекулярных сочетаний в более простые вещества. Крахмал превращается в простые сахара, а протеины денатурируются.
При переработке бобовых культур подавляются компоненты, которые понижают питательность. Быстрое прохождение процесса гарантирует сохранность витаминов, аминокислот и иных полезных веществ.
Зерновой продукт после экструдирования позволяет обеспечить привес на 10-30% за сутки. Окупаемость достигается за 6-7 месяцев. Экструдер подходит и для производства собачьих кормов. Практически все, кто опробует такое оборудование, больше и не думают возвращаться к старым методам кормления. Производительность аппаратуры сильно отличается, варьируются также ее размеры и потребление электроэнергии.
Устройство и принцип работы
Обработка пищевого сырья в экструдере производится под давлением 50-60 атмосфер. Одновременно на зерно воздействует высокая температура. Суммарная производительность прямо коррелирует с мощностью оборудования. Ключевой составляющей экструзионного оборудования является рама, на которой и фиксируются любые детали. А также обязательно присутствуют привод, дающий энергию, и ремень.
Механический импульс транслируется при помощи этого ремня и редуктора. Отдельно располагаются емкость для загрузки и приемный накопитель, куда первоначально вываливают зерно. Дополнительными частями экструдеров являются:
-
манжеты;
-
дозирующие шнеки с обособленными приводами;
-
системы управления;
-
регулирующие ключи;
-
шайбы;
- режущие лезвия.
В случае с самодельными экструдерами важную роль играет механизм прессования. После прохождения лезвийного элемента обрабатываемый продукт будет визуально похож на удлиненные палочки. Устройство способно отлично измельчать зерно. Подготовленный корм окажется полностью продезинфицирован. Допускается также перемешивание различных составляющих в единую массу.
Нагнетающий шнек, кроме внешней и внутренней частей, содержит также шайбы для подогрева и шнековый узел выхода. Все узлы ставятся на шпильки с левыми резьбами. Корпус изготавливают из стали. Подача оборотов от главного вала на сочетанный шнек обеспечивается за счет шпонок. Ключевые составные части крепко держатся на раме.
В корпусе делается отверстие, к которому монтируется приемник. Внутренний участок оснащается пазами, идущими в продольной плоскости. За их счет любые составные части корма передвигаются соответствующим образом. Выходная система оснащается регулятором грануляции. Специальное лезвие особой пружиной придавливается к матричному блоку; тепловой режим внутри экструдера отслеживается благодаря ставящейся на раму термопаре.
Высокотемпературное воздействие идет в течение всего лишь считаных секунд. Потому полезные вещества гарантированно сохраняются. А вот гибель опасных организмов будет неизбежна; для экструдирования годится даже то, что поражено насекомыми или плесенью.
Обрабатываемое зерно словно взрывается изнутри и приобретает оптимальную воздушность, пористость. Его объем возрастает на 20% в сравнении с исходным продуктом.
Как только он подается в бункер, дальнейшие процессы не требуют дополнительного вмешательства. Вибрационное воздействие обеспечивает подачу сырья на рабочий участок. Там температура может достигать 110-160 градусов. Так как давление достигает больших значений, на выходе из основного отсека зерно и «взрывается». Если используется отсекатель, фракция сортируется до размера 1-5 см; экструдирование одной порции сырья занимает приблизительно 30 секунд.
Чертежи экструзионных аппаратов могут включать:
-
каналы охлаждения;
-
нагревательные блоки;
-
системы подачи;
-
системы выталкивания;
-
блоки пластификации;
-
дозаторы.
Обзор моделей
Бытовой
В категории мини-аппаратов выделяется ЭК-5. Несмотря на свою бытовую специфику, он вполне удобен и отвечает самым строгим требованиям. Система фактически заменяет зернодробилку. Часовая производительность составит 60-80 кг, при этом расходуется 4 кВт тока. Шнеки сделаны с расчетом на долгую службу.
Альтернативой является ЭК-40. Его суммарная производительность достигает 40 кг за 60 минут. Потребление тока также не превосходит 4 кВт. Масса устройства — 90 кг. Для него требуется подавать электропитание на 220 или 380 В.
Промышленный
Для производства комбикорма и для сопутствующей очистки зерновых от патогенных организмов хорошо подойдет система Е-500. К сведению — с ее помощью можно также приготовить к отжиму масел:
-
рапс;
-
сою;
- подсолнечник.
Основной режим обработки применяется к гороху и амаранту, кукурузе и пшенице, ржи и ячменю, люпину и сое. Так как воронка имеет магнитный узел, попадание металлических предметов и частиц в конечный корм исключается. Производитель заявляет такие свойства, как:
-
возможность производства полножирного соевого шрота;
-
сбережение до 40% зерна;
-
контроль качества выпускаемого продукта;
-
производительность по сое до 500 кг за 60 минут, по зерновым до 300 кг за 60 минут.
Производители в России предлагают и другие продвинутые модели. Среди них внимания заслуживает ES-1250. Такой аппарат найдет применение в большинстве средних и крупных агропредприятий. Уровень производительности достигает 1250 кг за 60 минут. Конструкторы продумали все, чтобы устройство могло работать круглосуточно.
Подача растительного сырья из бункера производится сбоку напрямую в рабочий участок. Такое решение обходит проблемы, типичные обычно для систем переработки с верхней подачей. Конструкция подходит для работы с биологическими отходами, просом, мукой, фаршем и тому подобными субстанциями. Устройство выполнено так, чтобы обслуживание и ремонт происходили сравнительно просто. Масса экструдера достигает 2130 кг, а потребление тока составляет 110 кВт.
Высокую производительность имеет и ПЭ-900 УШК. Он перерабатывает за 60 минут от 1300 до 1800 кг зерна. Разработчики предусмотрели кондиционирование и паровую обработку продукта, что позволяет сделать его мягче и эластичнее, уменьшить общие энергозатраты. Срок эксплуатации основных узлов экструдера больше, чем у конкурирующих моделей. Работа идет при давлении 60 атмосфер и при весьма высокой температуре.
Выбирая двухшнековый агрегат, можно присмотреться к ПЭ-110. Он способен готовить полноценные корма даже из зерносмесей и лежалого зерна. Шнековый подающий узел оборудуют частотным регулятором. Есть также и вибрационные опоры. Срок эксплуатации в 2 раза больше, чем у традиционных аналогов, часовая производительность составляет до 130 кг, а масса устройства равна 250 кг.
Критерии выбора
Ключевым показателем предсказуемо выступает мощность. Она определяется количеством поголовья животных, которых предстоит кормить. Другие критерии:
- шнековая подача зерна (единственный равномерный метод, хотя и сравнительно дорогой);
- громкость при работе;
- качество ступицы;
- рабочий ресурс основных элементов;
- удобство управления;
- качество вырабатываемого комбикорма;
- простота очистки (вручную делать ее явно менее практично, нежели реверсом мотора).
Как правильно запустить?
Обычно пошаговая инструкция, как обращаться с экструдером, дается производителями. Но получение корма своими руками ведется по более или менее традиционной устоявшейся схеме. До запуска надо проверить, все ли крепления затянуты, нормально ли подключена электрическая часть. Только при условии нормального смазывания трущихся узлов можно рассчитывать на надежную стабильную работу. Включенное устройство «разогревают», исключая нагрузку на него; соответствующая регулировка проводится фильерой.
Если запуск идет с трудом, значит, надо шлифовать аппарат изнутри. Фильеру откручивают на 100%, и засыпают понемногу мелкий песок. Комья появляться не должны.
Оборудование следует ставить на ровную площадку в идеально сухом месте. Только при соблюдении таких условий к подготовке можно гарантировать приличный уровень работы.
Полезные рекомендации
Поначалу переработка всего зерна не будет идти гладко. Это совершенно нормально. Просто продолжают эксплуатировать экструдер, пока он не даст хорошего результата. Обычно период адаптации не превышает считаных минут. Если за это время ситуация не выправилась, нужно принимать меры.
Очень важна правильная регулировка подачи. Только при верно заданном угле исключается переполнение загрузочной воронки. Все витки шнека должны быть непрерывно наполнены зерном. Категорически недопустим перегрев мотора и перегрузки установки в целом. Холостая работа экструдера также недопустима.
На выводе следует точно настраивать фракцию. Это достигается за счет подкручивания болта и сокращения отверстия пластины. Как только работа завершена, все функциональные узлы полагается вычистить от остаточного продукта. Вместо разборки аппаратов пользуются предусмотренными функциями самоочистки, или же устраивают прогон со скорлупой от семечек подсолнуха. Тормозить устройство следует постепенно; касаться неостывших частей надо в термозащитных перчатках.