Обзор и выбор режимов сварки
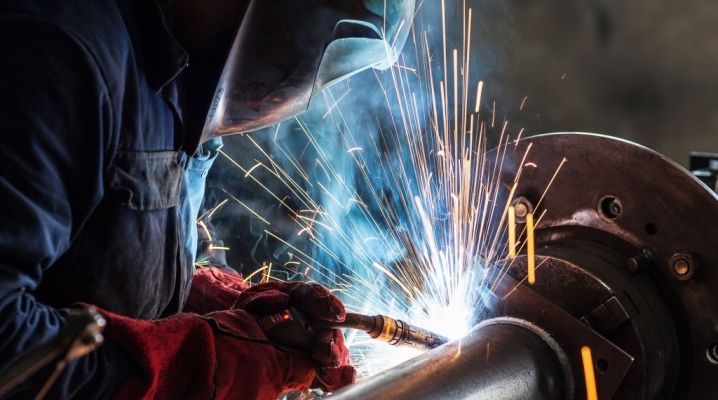
Сварка — очень сложное и многогранное понятие. Правильное выполнение работы возможно лишь при учете особенностей различных аппаратов и электродов, видов стыков и методов сваривания. Однако не менее важно произвести обзор режимов сварки и проанализировать правила выбора таких режимов.
Особенности
Прежде всего, надо разобраться, что именно включает в себя понятие режимов сварки. Профессионалы под этим словом понимают целые конгломераты отдельных свойств рабочего процесса, прямо влияющие на его результат. И профессиональный сварщик никогда не станет заявлять, что «важно только побыстрее да погорячее варить». Иногда, конечно, встречается деление на основные и второстепенные параметры. Но на деле это подразделение весьма условно: хороший результат гарантирован только при скрупулезном выполнении всех требований.
Отдельные параметры принято именовать элементами (составными частями) режима. Специалисты давно обратили внимание, что набор программ ручной и автоматической сварки довольно сильно отличается. Стоит учесть, что искать сведения о режимах в основных действующих ГОСТах, в том числе регулирующих ключевые термины и определения сварочных процессов, классификацию методов работы, запись операций и переходов по ЕСКД, бессмысленно. Там очень подробно характеризуются основные рабочие моменты, но термин «режим» нигде не употребляется.
На практике начинающие сварщики чаще всего используют синергетический режим. Именно он применяется в распространенных полуавтоматах бюджетного класса. Подобные устройства отличаются феноменальной простотой настройки (в сравнении с оборудованием предшествующих поколений). Однако сварщику обязательно надо профессионально расти.
И тут без знания специфики «режимного» вопроса не обойтись, просто подходить к нему придется иначе — не через ГОСТы.
Параметры
Рассмотрим главные и второстепенные параметры режимов сварки.
Основные
В число главных свойств режима, конечно, входят:
- электрическая полярность;
- возрастание сварочного ампеража и его локальные значения;
- рабочее напряжение;
- темп исполнения самой работы;
- сечение электродного инструмента;
- наибольший показатель колебаний электрода, допустимый в конкретном случае.
Подобные характеристики тесно взаимосвязаны с характеристиками рабочей дуги. Влияют они и на условия выполнения сварочного процесса. При совпадающем расходе энергии, меняя род используемого тока и полярность, выбирая больший или меньший электрод, можно существенно влиять на эффективность манипуляций. При идентичной силе тока сечение электродов воздействует на плотность подаваемой энергии. Воздействует оно и на подвижность дуги.
При одинаковом ампераже более крупный электрод сокращает глубину плавящегося участка. Зато он становится существенно шире. Не менее важны вид тока и его поляризация. От этих свойств зависит интенсивность прогрева, выделяемого на протяжении сварки. Уровень выброса тепла в рабочую зону сварщики определяют косвенно, ориентируясь на сокращение вольтажа.
Зависимости составляются отдельно для катода и для анода. Стоит понимать, что лишь часть энергии может выделиться в виде тепла. Разность выделения теплоты на катоде и на аноде зависит от способа, который используется для сварочных работ, он же влияет и на величину участка, который будет проплавлен. На практике установлено, что прямая полярность уменьшает площадь проплавляемой зоны по сравнению с обратной электрической поляризацией.
Поскольку пятно катода занимает меньше пространства, чем пятно анода, обрабатываемый шов оказывается шире. Но глубина расплавляемого сегмента, а также и его ширина, зависят еще и от того, как сварщик наклоняет электрод. При работе под углом ниже 90 градусов требуется отклонять его вперед. Металл, который будет плавиться, просто оттесняется в головную зону ванны. Потому шов становится мельче, что обеспечивает эффективную обработку поверхности.
Варить металл под углами свыше 90 градусов допустимо только с отклонением электрода назад. Металлический расплав будет оттесняться противоходом в заднюю зону. Подобный режим начнет заметно наращивать глубину оплавляемой зоны. На этом обзор ключевых параметров завершен.
Однако стоит рассмотреть и второстепенные моменты.
Дополнительные
Прежде всего, стоит обратить внимание на так называемый вылет электрода. Под этим термином принято понимать разрыв между контактной частью и обрабатываемым изделием. При малом вылете сокращается разогрев электрода и повышается глубина плавящейся зоны. Когда вылет проволоки растет, повышается индуктивное сопротивление. Электрод будет накаляться сильнее.
Материал этого приспособления определяет, какой окажется температура дуги, в какой среде лучше работать, и какие вещества попадут в шов. А последний момент прямо сказывается на качестве соединения. Толщину электродов подбирают сообразно толщине соединяемых частей (конструкций). Так, при работе с деталями толщиной 1-2 мм нужно применять инструмент сечением от 2 до 3 мм, а вот если нужно работать с деталями 3-6 см в толщину, необходимо использовать электрод 0,6-0,8 см в диаметре. Что касается температуры, необходимо помнить, что центр дуги прогрет сильнее всего: до 5-7 тысяч градусов.
Кроме этих свойств, важно учесть:
- пространственное расположение заготовок;
- конфигурацию кромок;
- качество проработки поверхности.
Советы по выбору
Чтобы подобрать оптимальную силу тока, учитывают не только рекомендации из универсальных таблиц. При сварке в горизонтальной плоскости ее понижают на 15-20% по сравнению с рекомендованными значениями. Подбор длины дуги ведут так, чтобы можно было поддерживать ее одинаковой на всем протяжении шва. Сделать это сложно, требуется опыт. Упростить работу начинающим помогают сварочные каретки.
Большую роль играет и скорость выполнения работы. При расчете ориентируются на равномерное наполнение рабочей ванны металлическим расплавом. Одновременно отслеживают равномерность перехода и качество покрытия кромок. Оптимальная ширина сварного шва на 50-100% больше сечения электрода.
Попытки ускорить сварку очень сильно приведут к слабому прогреву металла, и должная прочность не будет достигнута.
Грамотный контроль режима обработки подразумевает отслеживание:
- силы используемого электричества;
- схемы формирования швов;
- порядка очистки от шлака перед переходом к следующему слою.
Сварочные генераторы оснащаются в основном механическими указателями. Уровень погрешности при номинальных напряжениях ограничен 7,5% от наибольшего измеряемого значения. На самих рабочих местах в домашних условиях часто применяют элементарные технологические приемы. К примеру, сваривают пару пластин давно известной толщины, после зажимают их в тисках и ломают зубилом. Сваривание относительно толстого (свыше 2 мм) металла сопровождается проверкой сварной точки на скручиваемость: этот метод давно зарекомендовал себя с наилучшей стороны.
Но все же специалисты рекомендуют использовать автоматические системы отслеживания. Они показывают, каково реальное состояние сварочного процесса, и позволяют правильно отреагировать на возникающую проблему. Распространенной ошибкой новичков является задание очень малой силы тока. Недостаточный нагрев металла создает ничуть не меньше проблем, чем избыточно высокая температура. К тому же из-за этого дуга может гореть нестабильно, и даже вовсе гаснуть.
Чтобы правильно определить оптимальный темп сваривания, необязательно проводить расчеты по сложным формулам. Можно отталкиваться от указаний технических нормативов. Они регламентируют идеальную скорость работы по каждому типу металла или сплава в различных случаях. Если после сварки остаются слабо проваренные участки или прожоги, это повод в дальнейшем работать медленнее либо быстрее.
О том, как выбрать режим сварки, смотрите в следующем видео.