Особенности производства арболитовых блоков своими руками
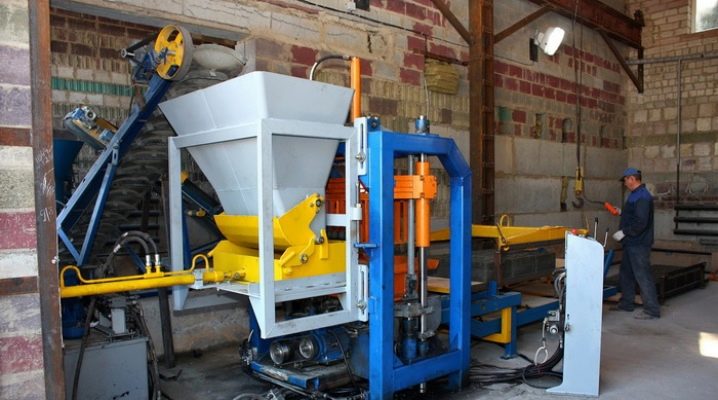
Арболит во многих публикациях описывается восторженно, сочинители рекламы не устают приписывать ему разные достоинства. Но даже если отбросить уловки маркетологов, становится ясно, что этот материал заслуживает пристального внимания. Полезно знать, как сделать его самостоятельно.
Виды и размеры блоков
Арболитовые панели делятся на несколько видов:
- блоки большого формата (предназначенные для стеновой капитальной кладки);
- пустотелые изделия различной величины;
- плиты для усиления теплоизоляции.
Также из арболита делают жидкие смеси, которыми заливают ограждающие конструкции. Но чаще всего на практике под словом «арболит» понимают именно кладочные элементы с облицовкой либо без нее. Чаще всего изготавливают блоки величиной 50х30х20 см. Однако все чаще номенклатура расширяется, а производители осваивают новые позиции. Технические характеристики выпускаемых блоков обеспечиваются только при полном отсутствии примесей.
Элементы плотностью 500 кг на 1 куб. м. и более традиционно считаются конструкционными, менее плотные — предназначенными для теплоизоляции. Их можно использовать там, где нагрузка сверху принимается другими частями сооружения. Обычно плотность измеряют только после потери блоком всей лишней влаги.
Из литого арболита удельной массой 300 кг на 1 куб. м. тоже можно возводить стены, при этом по прочности они не уступят конструкциям из более тяжелого материала.
Чтобы строить несущие стены одноэтажных домов, высота которых не превышает 3 м, надо применять блоки категории минимум В 1.0. Если сооружения будут выше, требуются изделия категории 1,5 и выше. А вот двухэтажные и трехэтажные постройки должны возводиться из арболита группы В 2,0 либо В 2,5 соответственно.
Согласно российскому ГОСТ ограждающие сооружения из арболита в умеренной климатической зоне должны иметь толщину 38 см.
На деле обычно стены жилых построек из блоков 50х30х20 см выкладывают в виде одного ряда, строго плашмя. Если нужно сформировать вспомогательную теплоизоляцию, из арболита делается так называемая теплая штукатурная система. Ее подготавливают, добавляя перлит и создавая слой от 1,5 до 2 см.
Когда помещения не отапливаются либо отапливаются время от времени, используют метод кладки на ребро. У теплозащитных арболитовых блоков коэффициент поглощения воды составляет не более 85%. Для конструктивных элементов допустимый показатель на 10% ниже.
Принято делить арболитные блоки на три категории по пожарной защищенности:
- Г1 (трудно загорающиеся);
- В1 (тяжело воспламеняющиеся);
- Д1 (образующие мало дыма элементы).
Необходимость производить арболит у себя дома связана во многом с тем, что существующие производители часто выпускают некачественный товар. Проблемы в основном могут быть связаны с недостаточной прочностью, слабым сопротивлением теплопередаче или нарушением геометрических параметров. Блоки любого вида непременно следует покрывать штукатуркой. Она надежно защищает от продувания ветрами. С арболитом комбинируются лишь способные «дышать» отделочные покрытия.
Есть 6 марок арболитовых блоков, выделяемых по уровню стойкости к морозу (от М5 до М50). Цифра после буквы М показывает, какое количество циклов перехода через ноль градусов могут перенести данные блоки.
Минимальная морозостойкость означает, что изделия должны применяться только для внутренних перегородок.
Чаще всего размер их составляет 40х20х30 см. В зависимости от устройства системы паз-гребень зависит площадь кладки и теплопроводность стен.
Говоря про размеры и характеристики арболитовых блоков по ГОСТ, нельзя не сказать, что он жестко регламентирует предельные отклонения размеров. Так, длина всех ребер может отличаться от заявленных показателей не более чем на 0,5 см. Наибольшая разность диагоналей составляет 1 см. А нарушение прямолинейности профилей каждой поверхности должно быть не более 0,3 см. Чем выше конструкции, тем меньше будет швов при укладке, и тем меньше окажется число швов.
В некоторых случаях удобнее всего оказываются блоки величиной 60х30х20 см. Они нужны там, где длина стен — кратная величина по отношению к 60 см. Это позволяет отказаться от резки блоков.
Иногда встречается так называемый «северный арболит», длина которого не превышает 41 см. В части рядов при перевязке ширина стены совпадает с длиной блока, а в другой части составляет сумму двух ширин и разделяющего их шва.
Практически все изготовители делают перегородочные блоки. В линейке каждой фирмы величина таких изделий составляет 50% стандартного типоразмера. Изредка встречаются конструкции 50х37х20 см. Это позволяет возводить стенки ровно 37 см, не прибегая к перевязке блоков или прикладыванию панелей.
В отдельных регионах могут встречаться совершенно другие размеры, это надо уточнять дополнительно. При самостоятельном производстве их надо подбирать по своему усмотрению.
Состав смеси и пропорции
Когда готовится производство арболитовых панелей, надо тщательно подбирать состав смеси и соотношение между ее частями. В качестве наполнителя неизменно выступают отбросы переработки дерева. Но так как арболит является разновидностью бетона, он содержит цемент.
Благодаря органическим компонентам материал отлично удерживает тепло и не пропускает посторонние звуки. Однако, если нарушены основные пропорции, эти качества нарушатся.
Надо понимать, что лишь некоторые виды стружки могут применяться для производства арболита. В этом его существенное отличие от опилкобетона. Согласно действующему ГОСТ, жестко регламентированы габариты и геометрические характеристики всех фракций материала.
Щепу делают, дробя нетоварную древесину. Длина щепок варьируется от 1,5 до 4 см, наибольшая ширина их составляет 1 см, а толщина должна быть не более 0,2 — 0,3 см.
В результате специальных научно-практических исследований было установлено, что самая лучшая щепа:
- по форме напоминает портняжную иглу;
- имеет длину до 2,5 см;
- имеет ширину от 0,5 до 1 и толщину от 0,3 до 0,5 см.
Причина проста: дерево при иных пропорциях поглощает влагу неодинаково. Соблюдение рекомендованных исследователям габаритов позволяет компенсировать разницу.
Кроме размеров, надо тщательно отбирать и породы дерева. Ель, бук подойдут, но лиственница не годится. Можно применять березовое и осиновое дерево.
Независимо от выбранной породы, надо непременно применять антисептические смеси.
Они позволяют избежать возникновения плесневых гнезд или поражения сырья иными патологическими грибками.
В производстве арболита иногда применяют кору и хвоинки, но их предельная доля составляет 10 и 5% соответственно.
Еще иногда берут:
- льняную и конопляную костру;
- солому риса;
- стебли хлопка.
Наибольшая длина таких компонентов составляет максимум 4 см, а ширина должна быть не более 0,2 — 0,5 см. Запрещено использовать паклю и очесы больше, чем 5% от массы употребляемого наполнителя. Если применяется костра льна, ее придется 24-48 часов вымачивать в известковом молоке. Это намного практичнее, чем 3 или 4 месяца выдерживать на открытом воздухе. Если не прибегнуть к такой обработке, содержащиеся в составе льна сахара будут разрушать цемент.
Что касается самого цемента, чаще всего для производства арболита применяют портландцемент. Именно его начали использовать для этой цели еще несколько десятилетий назад. Иногда к портландцементу добавляют вспомогательные вещества, которые увеличивают морозостойкость конструкций и улучшают другие их характеристики. Также в отдельных случаях может употребляться стойкий к сульфатам цемент. Он эффективно противостоит воздействию ряда агрессивных веществ.
ГОСТ требует, чтобы в теплоизоляционный деревобетон добавляли только цемент марки М-300 и выше. Для конструкционных блоков применяют лишь цемент категории не ниже М-400. Что касается вспомогательных добавок, их масса может составлять от 2 до 4% суммарной массы цемента. Количество вводимых компонентов определяется маркой арболитовых блоков. Хлорид кальция и сульфат алюминия употребляют в объеме не более 4%.
Таково же предельное количество смеси хлорида кальция с сульфатом натрия. Есть еще пара комбинаций, в которых хлористый алюминий объединяется с сульфатом алюминия и хлоридом кальция. Эти два состава употребляются в количестве до 2% от общей массы закладываемого цемента. В любом случае соотношение между вспомогательными добавками 1: 1. Но чтобы эффективно сработали вяжущие компоненты, требуется использовать воду.
В ГОСТ прописаны жесткие требования к чистоте используемой жидкости. Однако в реальном производстве арболита часто берут любую воду, которая пригодна для технических нужд. Нормальное схватывание цемента требует подогрева до +15 градусов. Если температура воды падает до 7-8 градусов тепла, химические реакции идут намного медленнее. Соотношение компонентов подбирают так, чтобы обеспечить необходимую крепость и плотность деревобетона.
Изделия из арболита можно армировать при помощи сеток и стержней из стали. Главное, чтобы они соответствовали нормам отраслевых ГОСТ.
Стандарт требует от производителей дважды за смену или чаще тестировать приготавливаемую смесь на соблюдение таких показателей:
- плотность;
- удобство укладки;
- склонность к расслаиванию;
- количество и размер пустот, разделяющих зерна.
Тестирование проводят в специальной лаборатории. Его проводят для каждой партии смеси на 7 и на 28 сутки после затвердевания. Стойкость к морозу определяют обязательно и для декоративных, и для несущих пластов.
Чтобы выяснить теплопроводность, мерят ее на отобранных по специальному алгоритму образцах. Определение влажности производят на пробах, отбираемых из готовых каменных блоков.
Необходимое оборудование
Лишь в том случае, когда соблюдены все требования, предъявляемые ГОСТ, можно запускать определенную марку деревобетона в производство. Но обеспечить строгое исполнение нормативов и выпустить необходимое количество смеси, а затем и блоков из нее, помогает только специальная аппаратура. Щепу разделяют на части при помощи промышленных измельчителей. Далее она вместе с другими компонентами поступает в устройство, размешивающее раствор.
Еще потребуется:
- аппарат, дозирующий и формирующий арболитовые блоки;
- вибрационный стол, который придаст им необходимые качества;
- устройства, сушащие щепки и приготовленные блоки;
- бункеры, куда закладывается песок и цемент;
- линии, подающие сырье.
Не стоит использовать самодельные аппараты, если планируется выпускать большие партии арболита. Они недостаточно производительны, потому рентабельность предприятия падает.
Полезно рассмотреть и особенности каждого вида оборудования. Устройства, режущие щепу, имеют специальный барабан с «ножами», формируемыми из качественной инструментальной стали. Дополнительно барабан оснащают молотками, которые позволяют автоматизировать подачу сырья для последующего дробления.
Чтобы сырье могло проходить внутрь, барабан делают перфорированным, его окружает несколько. Больший (внешний) барабан той же формы, который препятствует разлету осколков. Обычно устройство монтируется на рамах с трехфазными электромоторами. После расщепления щепу передают в сушилку. Именно качество этого аппарата сильнее всего влияет на совершенство готового продукта.
Сушилка тоже выполнена в форме сдвоенного барабана, ее диаметр составляет примерно 2 м. Наружный барабан перфорирован, что позволяет обеспечить поступление теплого воздуха. Его подают при помощи асбестовой трубы либо гибкого несгораемого рукава. Кручение внутреннего барабана позволяет размешать щепу и предотвратить воспламенение сырья. Качественная сушка сумеет за 8 часов довести до нужной кондиции 90 или 100 блоков. Точная величина зависит не только от ее мощности, но и от габаритов обрабатываемых конструкций.
Мешалка — это крупный цилиндрический чан. Все необходимое сырье загружается сбоку, а замешанный состав выходит снизу. Обычно электрические моторы и их редукторы располагаются сверху от растворомешалки. На эти двигатели насаживаются комплексы лопастей. Вместимость резервуара определяется тем, какова должна быть ежедневная производительность линии. Миниатюрное производство выпускает за дневную смену не более 1000 конструкций, при этом используются чаны емкостью 5 куб. м.
Технология производства
Чтобы приготовить арболитовые блоки для частного дома своими руками, надо использовать 1 часть стружек и 2 части опилок (хотя в некоторых случаях предпочитают соотношение 1: 1). Периодически все это как следует сушат. Их держат 3 или 4 месяца на свежем воздухе. Периодически измельченную древесину обрабатывают известью, переворачивают. Обычно на 1 куб. м. щепы расходуют примерно 200 л извести в концентрации 15%.
Следующий этап изготовления арболитовых блоков в домашних условиях подразумевает смешивание щепы с:
- портландцементом;
- гашеной известью;
- хлористым калием;
- жидким стеклом.
Лучше всего дома сделать блоки величиной 25х25х50 см. Именно такие размеры оптимальны и для жилого, и для промышленного строительства.
Уплотнение раствора требует использования вибрационных прессов либо ручных трамбовок. Если большое число деталей не требуется, можно использовать миниатюрный станок. Задать определить точный размер готовой продукции помогают специальные формы.
Формирование плит
Изготовить монолитный арболит можно, залив в эту форму подготовленную смесь вручную. Если добавляется жидкое стекло, готовое изделие станет более твердым, но при этом вырастет и его хрупкость. Целесообразно замешивать компоненты последовательно, а не все вместе. Тогда меньше опасность возникновения комков. Получение облегченной конструкции очень просто — надо только поставить в форму деревянный брусок.
Держать заготовку в форме надо минимум 24 часа. Потом начинается сушка на воздухе под навесом. Время высушивания определяется температурой воздуха, и если она очень низка, иногда требуется 14 дней. А последующая гидратация при 15 градусах продолжается 10 суток. На этом этапе блок держат под пленкой.
Чтобы арболитовая плита прослужила подольше, она не должна охлаждаться до отрицательной температуры. Деревобетон в летний жаркий день почти неизбежно пересыхает. Однако этого можно избежать, прибегая к периодическому опрыскиванию водой. Надежнее всего обработка в полностью контролируемых условиях в сушильной камере. Желаемые параметры — прогрев до 40 градусов при влажности воздуха от 50 до 60%.
О том, как сделать арболитовые блоки своими руками, смотрите в следующем видео.